第11章模锻后续工序PPT课件下载推荐.ppt
《第11章模锻后续工序PPT课件下载推荐.ppt》由会员分享,可在线阅读,更多相关《第11章模锻后续工序PPT课件下载推荐.ppt(78页珍藏版)》请在冰豆网上搜索。
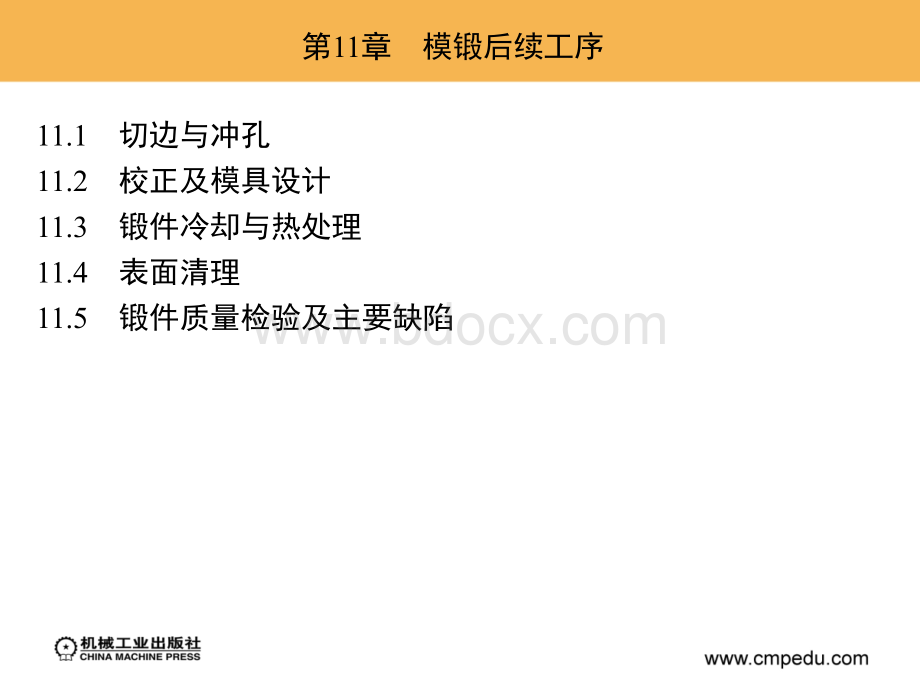
11.1.1切边和冲孔的方式及模具类型图11-1切边和冲孔示意图a)切边b)冲孔图11-2切边-冲孔连续模图11-3切边-冲孔复合模11.1.2切边模1.切边凹模的结构及尺寸2.切边凸模设计及固定方法3.模具闭合高度4.切边压力中心5.卸飞边装置1.切边凹模的结构及尺寸图11-4整体式凹模图11-5组合式凹模图11-6凹模刃口形式图11-7凹模紧固方法a)用楔铁紧固b)用螺钉紧固图11-8用压板紧固的凹模图11-9切边凹模的结构表11-1凹模尺寸(单位:
mm)图11-10切边凸模与锻件间的间隙图11-11简化凸模形状图图11-12锻件推压面的选取图11-13切边凸凹模的间隙表11-2切边凸凹模的尺寸2.切边凸模设计及固定方法
(1)楔铁紧固如图11-14a所示,用楔铁将凸模燕尾直接紧固在滑块上,前后用中心键定位,多用于大型锻件的切边。
(2)直接紧固如图11-14b所示,利用压力机上的紧固装置,直接将凸模尾柄紧固在滑块上,其特点是夹持方便,适于紧固中小型锻件的切边凸模。
(3)压板紧固如图11-14c所示,用压板、螺栓将凸模直接紧固在滑块上。
图11-14凸模直接紧固在滑块上1键2、8滑块3楔4、5、11凸模6紧固装置7定位销9压板10螺栓3.模具闭合高度1)当凸模推压面靠近飞边,需要进入凹模刃口才能将飞边切净时(图11-16a),凸模高度为2)当推压面远离飞边(图11-16b),即hn(推压面至锻件分模线距离)大于飞边桥部高度的68倍时,凸模不需进入凹模刃口便可将飞边切净,则凸模高度为图11-15压力机封闭高度与模具闭合高度的关系1曲轴2连杆3螺杆4滑块5垫板6工作台图11-16凸模高度的计算a)凸模伸入凹模b)凸模不伸入凹模4.切边压力中心图11-17用解析法求切边压力中心5.卸飞边装置图11-18卸飞边装置11.1.3冲孔模和切边冲孔复合模1.冲孔模2.切边冲孔复合模1.冲孔模图11-19冲连皮凹模尺寸图11-20锻件一面无压凹时冲连皮模结构简图表11-3凸凹模之间的间隙图11-21切边冲孔复合模1螺栓2楔3上模板4螺母5拉杆6托架7凸模8锻件9凹模10垫板11支承板12顶件器13冲头14螺栓15横梁16下模板11.1.4切边力和冲孔力的计算11.1.5切边、冲孔模材料表11-4切边、冲孔模材料及热处理硬度表11-4切边、冲孔模材料及热处理硬度11.2校正及模具设计11.2.1校正11.2.2精压11.2.1校正1.热校正与冷校正2.校正模模膛设计特点1.热校正与冷校正表11-5热校正和冷校正2.校正模模膛设计特点1)由于锻件在切边后可能留有毛刺,以及锻件在高度方向欠压,校正后锻件水平方向尺寸有所增大。
2)模膛沿分模面的边缘应做成圆角。
3)对小锻件,在锤或螺旋压力机上校正时,校正模的模膛高度应等于锻件的高度;
对大、中型锻件,因欠压量较多,校正模模膛的高度可比锻件高度小,其高度差与锻件高度尺寸的负偏差值相等。
4)校正模应有足够的承击面面积。
图11-22简化校正模模膛形状举例a)将不对称锻件制成对称模膛b)将锻件局部复杂的形状制成较简单的形状c)将形状复杂的连杆锻件大头部分制成敞开的两个平行平面d)长轴类锻件只制出杆部的校正模模膛11.2.2精压校正模模膛设计的特点如下:
1)由于锻件在切边后可能留有毛刺,以及锻件在高度方向欠压,校正后锻件水平方向尺寸有所增大。
为便于取放锻件,校正模模膛水平方向与锻件侧面之间要留有间隙,空隙的大小约为锻件水平方向尺寸正偏差之半。
如在曲柄压力机上校正时,在上、下模之间(即分模面上)应留有12mm间隙,防止卡死。
当用螺旋压力机校正时,校正模每千牛的承击面面积为0.100.13cm2。
精压是对已成形的锻件或粗加工的毛坯进一步改善其局部或全部表面粗糙度和尺寸精度的一种锻造方法,其优点如下:
1)精压可提高锻件的尺寸精度,减小表面粗糙度值。
2)精压可全部或部分代替零件的机械加工,节省机械加工工时,提高生产率,降低成本。
3)精压可减小或免除机械加工余量,使锻件尺寸缩小,降低了原材料消耗。
4)精压使锻件表面变形强化,提高零件的耐磨性和使用寿命。
1.精压的分类2.精压件平面的凸起3.精压余量4.精压力的计算1.精压的分类表11-6精压的分类2.精压件平面的凸起1)冷精压前先热精压一次,减小冷精压余量。
2)多次精压。
3)减小精压平板的表面粗糙度值,采用良好的平板润滑措施。
4)减小精压面的受压面积,使精压面的应力分布趋于均匀。
5)选用淬硬性高的材料做精压平板。
图11-23平面精压时工件的变形图11-24精压面上的应力分布3.精压余量
(1)平面精压余量精压余量一般与精压平面直径d与精压平面高度h的比值(d/h)有关,还与被精压件面积的大小和精压坯料的精度有关。
(2)体积精压余量体积精压余量原则上可参照平面精压余量确定。
表11-7平面精压的双面余量(单位:
mm)4.精压力的计算表11-8不同材料精压时的平均单位压力11.3锻件冷却与热处理11.3.1锻件的冷却11.3.2锻件热处理11.3.1锻件的冷却1.锻件在冷却过程中的内应力2.锻件的冷却方法3.锻件的冷却规范1.锻件在冷却过程中的内应力
(1)温度应力温度应力是由于锻件在冷却过程中内外温度不同,造成冷缩不均而产生的,如图11-25所示。
(2)组织应力锻件在冷却过程中若有相变发生,由于相变前后组织的比体积不同,而且转变是在一定温度范围内完成的,故在相与相之间产生组织应力。
(3)残余应力由于锻件在变形过程中变形不均或加工硬化所引起的应力,如未能及时经再结晶软化将其消除,锻后冷却时便成为残余应力保留下来。
图11-25锻件冷却过程温度应力(轴向)的变化和分布的示意图a)软钢锻件b)硬钢锻件1表层应力2心部应力图11-26锻件冷却过程中组织应力(切向)的变化和分布示意图2.锻件的冷却方法
(1)在空气中冷却锻件锻后单件或成堆直接放在车间地面上冷却,但不能放在潮湿地面上或金属板上,也不要放在有穿堂风的地方,以免冷却不均或局部急冷引起裂纹,冷却速度较快。
(2)在干燥的灰、砂坑(箱)内冷却一般钢件入砂温度不应低于500,周围灰、砂厚度不小于80mm,冷却速度较慢。
(3)在炉内冷却锻件锻后直接放入炉内冷却,钢件入炉温度不应低于600650,炉温与入炉锻件温度相当。
11.3.2锻件热处理锻件热处理的目的是:
1)调整锻件的硬度,以利于切削加工。
2)消除锻件内应力,以免在机械加工时变形。
3)改善锻件内部组织,细化晶粒,为最终热处理做好组织准备。
4)对于不再进行最终热处理的锻件,应保证达到规定的力学性能要求。
1.中小型锻件热处理1.中小型锻件热处理
(1)退火退火是为了细化晶粒,消除或减少残余应力,降低硬度,提高塑性和韧性,改善切削性能。
(2)正火对于碳钢锻件采用正火是为了细化晶粒、消除内应力、增加强度和韧性,或为了消除网状渗碳体。
(3)淬火、回火淬火是为了获得不平衡的组织,以提高强度和硬度。
(4)淬火、时效高温合金和能够通过热处理强化的铝合金、镁合金,在锻后常采用淬火时效处理。
图11-27各种锻件热处理加热温度范围示意图2.大型锻件热处理
(1)防止白点处理主要是把锻件中的氢扩散出去和减少组织应力。
(2)正火回火处理对于基本不会产生白点和对白点不敏感的锻件,后可采取正火回火处理,使锻件晶粒细化、组织均匀。
图11-28大型锻件防止白点的锻后冷却与热处理曲线a)等温冷却b)起伏等温冷却c)起伏等温退火图11-29锻件正火回火曲线(热装炉)11.4表面清理1.表面清理的目的2.滚筒清理3.喷砂(丸)清理4.抛丸清理5.光饰6.酸洗7.局部表面缺陷的清理11.5锻件质量检验及主要缺陷11.5.1锻件质量检验11.5.2锻件的主要缺陷11.5.1锻件质量检验1.锻件几何形状与尺寸的检验2.锻件表面质量的检验3.锻件内部缺陷和组织检验4.锻件力学性能检验5.化学成分检验表11-9批生产锻件等级及其检验项目1.锻件几何形状与尺寸的检验
(1)锻件长、宽、高尺寸和直径的检查主要用卡钳、卡尺进行检查。
(2)锻件内孔的检查无斜度用卡尺、卡钳,有斜度用塞尺。
(3)锻件特殊面的检查例如,叶片型面尺寸可用型面样板、电感量仪(电感量仪一次可以准确地检测2034个测量点的尺寸公差)、光学投影仪检查。
(4)锻件错移量的检查对形状复杂锻件,可用划线方法分别划出锻件上、下模的中心线,若两个中心线重合说明锻件无错移;
若不重合,两中心线错开的间距就是锻件的错移量。
(5)锻件弯曲度的检查通常把锻件放在平台上或用两个支点把锻件支起而旋转锻件,用千分表或划针盘测量其弯曲的数值。
(6)锻件翘曲度的检查检查锻件两平面是否在同一平面上或保持平行。
2.锻件表面质量的检验
(1)磁粉检验(磁力探伤)用于检测由铁磁材料制成的零件或锻件的表层缺陷。
(2)荧光检验对于非铁磁性材料,其表面缺陷可用荧光检验来显示。
(3)着色检验其工作原理与荧光检验相似,只是渗透溶液和显示剂不同,无需紫外线照射,依靠有颜色的渗透液来显示缺陷的形状与位置。
图11-30磁力线在有缺陷条件中图11-31磁力线方向与裂纹方向的关系3.锻件内部缺陷和组织检验
(1)超声波检验超声波具有很强的穿透能力,可以穿透几米甚至十几米厚的金属。
(2)低倍检验低倍检验是指用肉眼或借助于1030倍的放大镜,检验锻件断面上的组织状态,故又称为宏观组织检验。
(3)显微组织检验显微组织检验(高倍检验)是在光学显微镜下检验锻件内部(或断口)组织状态与微观缺陷,因此,检验用试样必须具有代表性。
图11-32超声波探伤示意图11.5.2锻件的主要缺陷1.自由锻件2.模锻件1.自由锻件
(1)横向裂纹横向裂纹如果为较深的表面横向裂纹,主要是因为原材料品质不佳,钢锭冶金缺陷较多。
(2)纵向裂纹在镦粗或每一火拔长时出现的表面纵向裂纹,除了由于冶金品质外,也可能是倒棱时压下量过大引起的。
(3)表面龟裂当钢中铜、锡、砷、硫含量较多及始锻温度过高时,在锻件表面会现龟甲状较浅的裂纹。
(4)内部微裂由于中心疏松组织未能锻合而引起,常与非金属夹杂并存,也有人称其为夹杂性裂纹。
(5)局部粗晶锻件的表面或内部局部区域晶粒粗大,其原因是加热温度高,变形不均匀,并且局部变形程度(锻造比)太小。
(6)表面折叠这是由于拔长时型砧圆角过小,送进量小于压下量而造成的。
(7)中心偏移坯料加热时温度不均,或锻造操作时压下不均,均会导致钢锭中心与锻件中心不重合,影响锻件品质。
(8)力学性能不能满足要求锻件强度指标不合格与炼钢、热处理有关,而横向力学性能(塑性、韧性)不合格,则是由于冶炼杂质太多或锻造比不够所引起的。
2.模锻件表11-10模锻件缺陷及其产生的原因模锻件缺陷及其产生的原因见表11-10。
表11-10模锻件缺陷及其产生的原因表11-10模锻件缺陷及其产生的原因