第三章耐火材料的生产过程Word文件下载.doc
《第三章耐火材料的生产过程Word文件下载.doc》由会员分享,可在线阅读,更多相关《第三章耐火材料的生产过程Word文件下载.doc(25页珍藏版)》请在冰豆网上搜索。
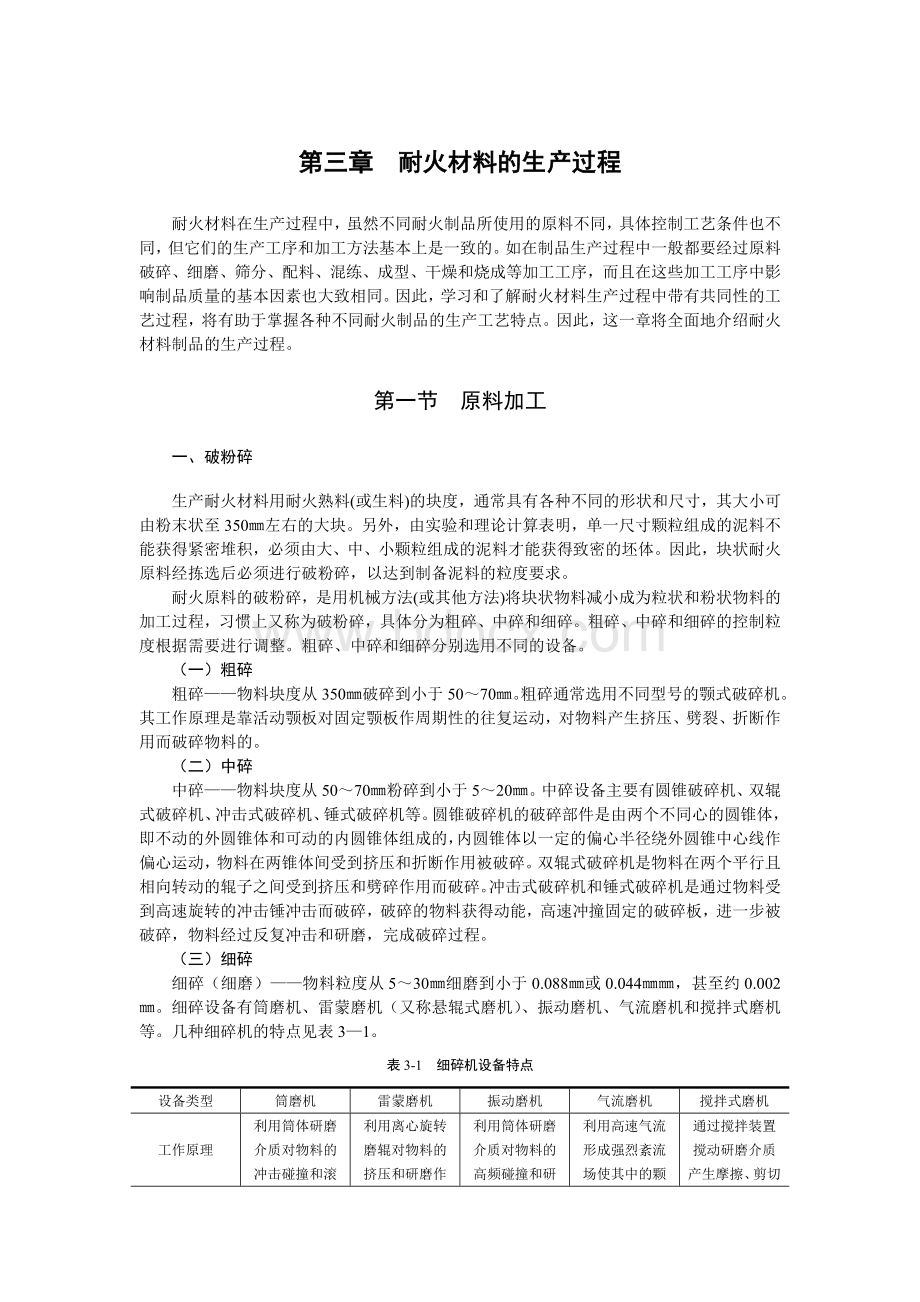
细碎设备有筒磨机、雷蒙磨机(又称悬辊式磨机)、振动磨机、气流磨机和搅拌式磨机等。
几种细碎机的特点见表3—1。
表3-1细碎机设备特点
设备类型
筒磨机
雷蒙磨机
振动磨机
气流磨机
搅拌式磨机
工作原理
利用筒体研磨介质对物料的冲击碰撞和滚动研磨作用使物料粉碎
利用离心旋转磨辊对物料的挤压和研磨作用使物料粉碎
利用筒体研磨介质对物料的高频碰撞和研磨作用使物料粉碎
利用高速气流形成强烈紊流场使其中的颗粒自撞、摩擦粉碎颗粒
通过搅拌装置搅动研磨介质产生摩擦、剪切和冲击破碎颗粒
入料尺寸/㎜
20~40
10~30
~2
~02
0.5
出料尺寸/㎜
0.074~0.088
0.044~0.088
~0.044
0.002~0.010
0.001~0.010
产量/kg/h
1000~10000
200~5000
100~1000
影响耐火原料破粉碎的因素,主要是原料本身的强度、硬度、塑性和水分等,同时也与破粉碎设备的特性有关。
在耐火材料生产过程中,将耐火原料从350㎜左右的大块破粉碎到3~0.088㎜的各粒度料,通常采用连续粉碎作业,并根据破粉碎设备的结构和性能特点,采用相应的设备进行配套,例如采用颚式破碎机、双辊式破碎机、筛分机、筒磨机,或者采用颚式破碎机、圆锥破碎机、筛分机、筒磨机等进行配套,对耐火原料进行连续破粉碎作业。
连续破粉碎作业的流程通常有两种,即开流式(单程粉碎)和闭流式(循环粉碎)。
开流式粉碎的流程简单,原料只通过破碎机一次。
但是,要使原料只经过一次粉碎后完全达到要求的粒度,其中必然会有一部分原料成为过细的粉料,这称之为过粉碎现象。
它不但降低粉碎设备的粉碎效率,而且不利于提高制品的质量。
闭流式粉碎时,原料经过破碎机后被筛分机将其中粗粒分开,使其重新返回破碎机与新加入的原料一起再进行粉碎。
显然,闭流式粉碎作业的流程较复杂,并需要较多的附属设备。
但采用闭流式粉碎时,破碎机的粉碎效率较高,并可减少原料的过粉碎程度。
在耐火材料生产中,原料破碎通常采用开流式,而粉碎系统采用闭流式循环粉碎。
原料在破粉碎过程中不可避免地带入一定量的金属铁杂质。
这些金属铁杂质对制品的高温性能和外观造成严重影响,必须采用有效方法除去。
除铁方法有物理除铁法和化学除铁法。
物理除铁法是用强磁选机除铁,对颗粒和细粉选用不同的专用设备。
化学除铁法是采用酸洗法除铁。
对于白刚玉等高纯原料,用该方法除铁才能保证原料的高纯度。
除铁设备有耐酸泵、耐酸缸、搅拌机、离心机、干燥机和打粉机等。
二、筛分
耐火原料经破碎后,一般是大中小颗粒连续混在一起。
为了获得符合规定尺寸的颗粒组分,需要进行筛分。
筛分是指破粉碎后的物料,通过一定尺寸的筛孔,使不同粒度的原料进行分离的工艺过程。
筛分过程中,通常将通过筛孔的粉料称为筛下料,残留在筛孔上粒径较大的物料称为筛上料,在闭流循环粉碎作业中,筛上料一般通过管道重返破碎机进行再粉碎。
根据生产工艺的需要,借助于筛分可以把颗粒组成连续的粉料,筛分为具有一定粒度上下限的几种颗粒组分,如3~1㎜的组分和小于1㎜的组分等。
有时仅筛出具有一定粒度上限(或下限)的粉料,如小于3㎜的全部组分或大于1㎜的全部组分等。
要达到上述要求,关键在于确定筛网的层数和选择合理的筛网孔径。
前者应采用多层筛,后者可采用单层筛。
筛分时,筛下料的粒度大小不仅取决于筛孔尺寸,同时也与筛子的倾斜角、粉料沿筛面的运动速度、筛网厚度、粉料水分和颗粒形状等因素有关。
在生产时,改变筛子的倾斜角或改变粉料沿筛面的运动速度,就可在一定程度上调整筛下料的颗粒大小。
各厂在实际生产中对筛网孔尺寸大小的表示方法不尽相同,常用的表示方法有目、孔、号和筛孔实际尺寸㎜数等,见表3-2。
表3-2编织筛网简明规格
筛号
筛孔尺寸㎜
2.5
8.00
30
0.58
325
0.044
3
6.73
35
0.50
400
0.038
3.5
5.66
40
0.42
800
0.019
4
4.76
45
0.35
1100
0.013
5
4.00
50
0.297
1300
0.011
6
3.36
60
0.250
1600
0.010
7
2.83
70
0.210
1800
0.008
8
2.38
80
0.177
2000
0.0065
10
2.00
100
0.149
2500
0.0055
12
1.68
120
0.125
3000
0.005
14
1.41
140
0.105
3500
0.0045
16
1.19
170
0.088
4000
0.0034
18
1.00
200
0.074
5000
0.0027
20
0.84
230
0.062
6000
0.0025
25
0.71
270
0.053
7000
0.00125
目前,耐火材料生产用的筛分设备主要有振动筛和固定斜筛两种,前者筛分效率高达90%以上,后者则低,一般为70%左右。
三、粉料贮存
耐火原料经粉碎、细磨、筛分后,一般存放的贮料仓内供配料使用。
粉料贮存在料仓内的最大问题是颗粒偏析。
因为在粉料颗粒中一般都不是单一粒级,而是由粗到细的连续粒级组成的,只是各种粉料之间颗粒大小和粒级之间的比例不同而已。
当粉料卸入料仓时,粗细颗粒就开始分层,细粉集中在卸料口的中央部位,粗颗粒则滚到料仓周边。
当从料仓中放料时,中间的料先从出料口流出,四周的料随料层下降,而分层流向中间,然后从出料口流出而造成颗粒偏析现象。
目前生产中解决贮料仓颗粒偏析的方法,主要有以下几种:
1)对粉料进行多级筛分,使同一料仓内的粉料粒级差值小些。
2)增加加料口,即多口上料。
3)将料仓分隔。
第二节泥料的制备
生产耐火制品的泥料(也称砖料)是按一定比例配合的各种原料的粉料,在混练机混练过程中加入水或其他结合剂而制得的混合料。
它应具有砖坯成型时所需要的性能,如塑性和结合性等。
泥料制备工序包括配料和混练两个工艺过程。
一、配料
根据耐火制品的要求和工艺特点,将不同材质和不同粒度的物料按一定比例进行配合的工艺称为配料。
配料规定的配合比例也称配方。
确定泥料材质配料时,主要考虑制品的质量要求,保证制品达到规定的性能指标;
经混练后砖料具有必要的成型性能,同时还要注意合理利用原料资源,降低成本。
(一)粒度组成
泥料中颗粒组成的含意包括:
颗粒的临界尺寸、各种大小颗粒的百分含量和颗粒的形状等。
颗粒组成对坯体的致密度有很大影响。
只有符合紧密堆积的颗粒组成,才有可能得到致密坯体。
计算不同尺寸的圆球体堆积状态表明,通常向大颗粒的组分中加入一定数目尺寸较小的颗粒,使其填充于大颗粒的间隙中,则堆积物间隙可进一步降低。
假如向第一组球内引入第二组球,其尺寸比第一组球小,第二组球在空隙内也能以配位数为8的方式堆积,则混合物的空隙下降为14.4%。
依此类推,再加入体积更小的第三、第四组球,则空隙还会进一步下降,见表3—3。
当三组分球作最紧密堆积时,气孔率下降显著,当组分大于3时,则气孔率下降幅度减小。
在工艺上主要是用来满足耐火制品气孔率、热震稳定性以及透气性的要求,但实际应用时,除考虑最紧密堆积原理外,还须根据原料的物理性质、颗粒形状、制品的成型压力、烧成条件和使用要求全面考虑并加以修正。
表3—3多组分球体堆积特征
球体组分
球体体积,%
气孔率,%
气孔率下降,%
1
62
38
-
2
85.6
14.4
23.6
94.6
5.4
9.0
98.0
2.0
3.4
99.2
0.8
1.2
最紧密堆积的颗粒,可分为连续颗粒和不连续颗粒。
图3-1给出不连续三组分填充物堆积密度的计算值和实验值,由图可见,堆积密度最大的组成为:
55~65%粗颗粒,10~30%中颗粒,15~30%细颗粒。
虚线——计算结果,实线——实验结果
图3-1熟料堆积的气孔率
用不连续颗粒可以得到最大的填充密度,但其缺点是将产生严重的颗粒偏析,而且也是不实际的。
实际生产中,还是选择级配合理的连续颗粒,通过调整各粒级配合的比例量,达到尽可能高的填充密度。
在连续颗粒系列中,设D是最大颗粒粒径,d是任意大小颗粒的粒径,y是粒径d以
下的含有量,若取配合料总量为100%,则
y=l00(d/D)q
式中q值随颗粒形状等因素变化,实际上取0.3~0.5时,该颗粒系列构成紧堆积。
文献报导适应于耐火材料颗粒组成的计算公式:
y=[α+(1-α)(d1/D)n]100
式中α——系数,取决于物料的种类和细粉的数量等因素,一般情况下,0<α<0.4;
n——指数,与颗粒的分布及细粉比例有关,n=0.5~0.9;
D——临界颗粒尺寸;
d1——最小颗粒尺寸。
从式中不难看出,物料的堆积密度与物理一化学性质以及D、n和α值有关。
在一定范围内,试样显气孔率随细粉的增加而降低。
当α=0.31和α=0.32时,临界粒度为3和4㎜的物科,从其紧密堆积时的颗粒组成计算得知,<0.06㎜的颗粒应占34%和42%。
在耐火制品生产中,通常力求制得高密度砖坯,为此常要求泥料的颗粒组成应具有较高的堆积密度。
要达到这一目的,只有当泥料内颗粒堆积时形成的孔隙被细颗粒填充,后者堆积时形成的孔隙又被更细的颗粒填充,在如此逐级填充条件下,才可能达到泥料颗粒的最紧密堆