改良A2O工艺污水处理工程实例Word格式.docx
《改良A2O工艺污水处理工程实例Word格式.docx》由会员分享,可在线阅读,更多相关《改良A2O工艺污水处理工程实例Word格式.docx(4页珍藏版)》请在冰豆网上搜索。
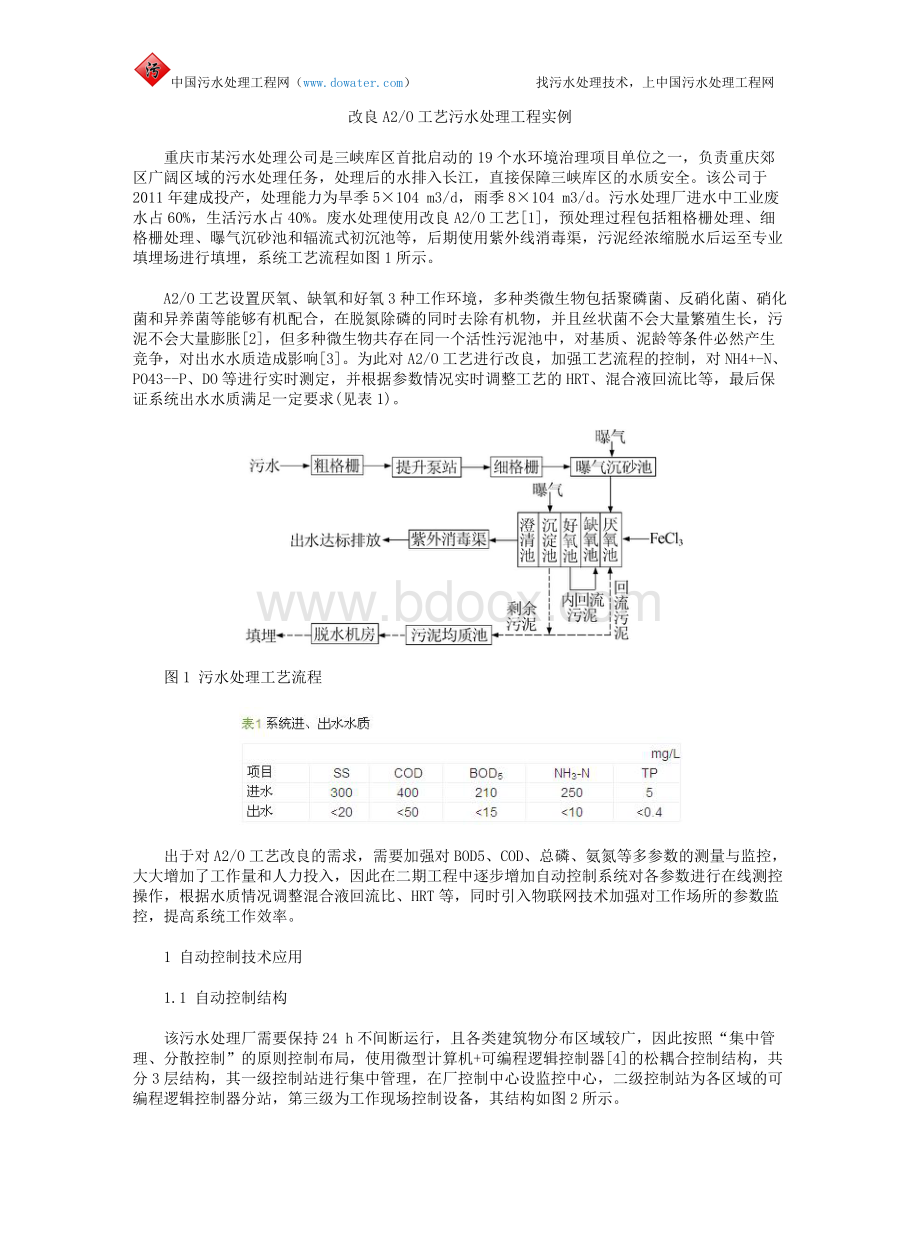
104m3/d,雨季8×
104m3/d。
污水处理厂进水中工业废水占60%,生活污水占40%。
废水处理使用改良A2/O工艺[1],预处理过程包括粗格栅处理、细格栅处理、曝气沉砂池和辐流式初沉池等,后期使用紫外线消毒渠,污泥经浓缩脱水后运至专业填埋场进行填埋,系统工艺流程如图1所示。
A2/O工艺设置厌氧、缺氧和好氧3种工作环境,多种类微生物包括聚磷菌、反硝化菌、硝化菌和异养菌等能够有机配合,在脱氮除磷的同时去除有机物,并且丝状菌不会大量繁殖生长,污泥不会大量膨胀[2],但多种微生物共存在同一个活性污泥池中,对基质、泥龄等条件必然产生竞争,对出水水质造成影响[3]。
为此对A2/O工艺进行改良,加强工艺流程的控制,对NH4+-N、PO43--P、DO等进行实时测定,并根据参数情况实时调整工艺的HRT、混合液回流比等,最后保证系统出水水质满足一定要求(见表1)。
图1污水处理工艺流程
出于对A2/O工艺改良的需求,需要加强对BOD5、COD、总磷、氨氮等多参数的测量与监控,大大增加了工作量和人力投入,因此在二期工程中逐步增加自动控制系统对各参数进行在线测控操作,根据水质情况调整混合液回流比、HRT等,同时引入物联网技术加强对工作场所的参数监控,提高系统工作效率。
1自动控制技术应用
1.1自动控制结构
该污水处理厂需要保持24h不间断运行,且各类建筑物分布区域较广,因此按照“集中管理、分散控制”的原则控制布局,使用微型计算机+可编程逻辑控制器[4]的松耦合控制结构,共分3层结构,其一级控制站进行集中管理,在厂控制中心设监控中心,二级控制站为各区域的可编程逻辑控制器分站,第三级为工作现场控制设备,其结构如图2所示。
图2自动控制结构
图2中,自动控制系统通过工业以太网和光纤冗余环网传输数据信息和控制信息,使用监控中心、二级控制站和现场控制器等设备实现自动控制功能的分级分散。
在监控中心进行工艺管理和自动控制,实时监控各设备工作状态、工艺流程参数。
下设2个二级控制站,分别位于鼓风机房和污泥脱水间内,二级控制站1控制3个现场控制设备,分别为鼓风机房、生化池和变电所,二级控制站2分别监控紫外线消毒间、1号脱水机和2号脱水机。
这种松耦合控制结构可提高系统的可靠性,即使监控中心出现故障,下级的分控站和现场控制设备也能独立延续原状态运行,降低了通信系统故障可能引起的失控风险。
1.2自动控制策略
由于季节差异、流量变化、水质特征等因素影响,处理流程的各种状态参数实时变化,需要根据状态和自动控制策略实时应对调整[5],系统中可编程逻辑控制器使用西门子S7-300系列,主要硬件配置包括PS307电源模块、CPU314中央处理器、SM321数字量输入模块、SM322数字量输出模块、SM311模块量输入模块和SM332模拟量输出模块等。
通过S7-300系列监视系统各部分工作情况并酌情采取自动控制措施。
各现场控制设备的自动控制策略如表2所示。
表2为主要控制部位及其控制策略,在工程应用中系统各环节也有监控措施。
如预处理系统中有2台螺旋输送压榨机和3台粗格栅,通过液位差值智能监控粗格栅运行状态,栅格初始状态按设定的周期运转,在粗栅格前后各安装1个超声液位差计,测定液位差后输入到自动控制系统中,根据液位差是否大于阈值判定粗格栅是否存在堵塞,如大于阈值则判定堵塞,系统自动控制除污机增大运转量,直至液位差小于阈值的80%后除污机恢复常态工作量。
细格栅、沉砂池等部位也有相应的监控部位执行功能,通过智能监控和自动控制策略减少人力操作,提高系统的工作效率和可靠性。
2物联网测试应用
为实现自动控制必须实时、准确地监控各部位工作状态,而物联网技术可实现传感器与网络的多方互联,是解决自动监视问题的较优策略。
在自动控制系统中采用物联网[6]进行从下到上感知层、网络层、应用层的架构,对应结构如图3所示。
感知层使用传感器进行专业监测,要求具备数字化、高精度和实时性;
网络层使用工业以太网和光纤冗余环网将感知层的传感器数据传入到应用层,实现物理链路的互联互通[6],使用TCP/IP协议,保证数据交互的安全性和高速率;
应用层对传感器数据进行汇总分析、图文展示,并配置相关的应用程序进行动态处理。
感知层状态监控是实现自动化控制的关键依据,其主要监控数据如表3所示。
控制中心汇总各种传感器数据,经整理分析可得整个生产流程的关键数据如耗电量、进出口水量等,并算出出口水质指标如BOD5、COD、NH3-N等。
3效果分析
该污水处理厂进口的污水量虽然在重庆市污水处理厂所占比例相对较小,但由于地处郊区,服务区域较大,要接收3条沟渠的污水,监控难度较大,同时污水直接排入长江,必须严格控制水质,为此引进物联网技术进行自动控制管理。
系统实时测试各环节、各系统状态并传输到控制中心,控制中心经分析计算后确定各系统工作状态,并使用可编程逻辑控制器自动控制各系统采取应对措施,减少了人工操作工作量,提高了操作的精确性和及时性。
系统可提供图形化示意图,测试周期为60min,可选择SS、COD、BOD5、NH3-N、TP、水量、平均耗电量等参数,最多能显示4种参数,当刷新的参数值连续超出阈值时表明系统故障,状态框将会标示异常并告警,否则显示状态正常,移动光标将显示参数测量时间和数值。
使用自动控制系统之后,系统运行稳定性得到提升,数据采集测试频率可稳定维持在15min/次(实际中一般设定为30min测试1次,甚至更长时间),出水达标率>
90%,耗电量<
0.35kW·
h/m3。
4结论
可行性分析和试运行结果表明,使用融合物联网技术的自动控制系统对污水处理厂进行智能化监控,通过关键参数和关键部分的状态参数测试明确各部位工作情况,并根据预定原则进行自动化、智能化处理是可行的,且在效率和效益上都得到一定提升,控制系统建设较为完善,具有较优越的性能,借鉴国外的先进经验,可在重庆地区进一步推广。
但该系统复杂度较高,同时因污泥浓度计、pH计等感知层传感器使用维护要求较高,接触探头需要定期维护清洗并标校,而且国内技术基础较为薄弱,一般使用进口器件,价格较为昂贵,一定程度上增加了污水处理系统的投资建设费用和维护成本,这是进一步推广面临的主要问题之一,但这种自动化智能控制策略是国内外污水处理系统发展的必然趋势,在后续工作中将研究更为稳定可靠、维护更为简便、效费比更高的自动化控制系统,使自动化系统得到推广普及。
(文章来源:
中国污水处理工程网)