地下管道安装施工方案ok文档格式.doc
《地下管道安装施工方案ok文档格式.doc》由会员分享,可在线阅读,更多相关《地下管道安装施工方案ok文档格式.doc(7页珍藏版)》请在冰豆网上搜索。
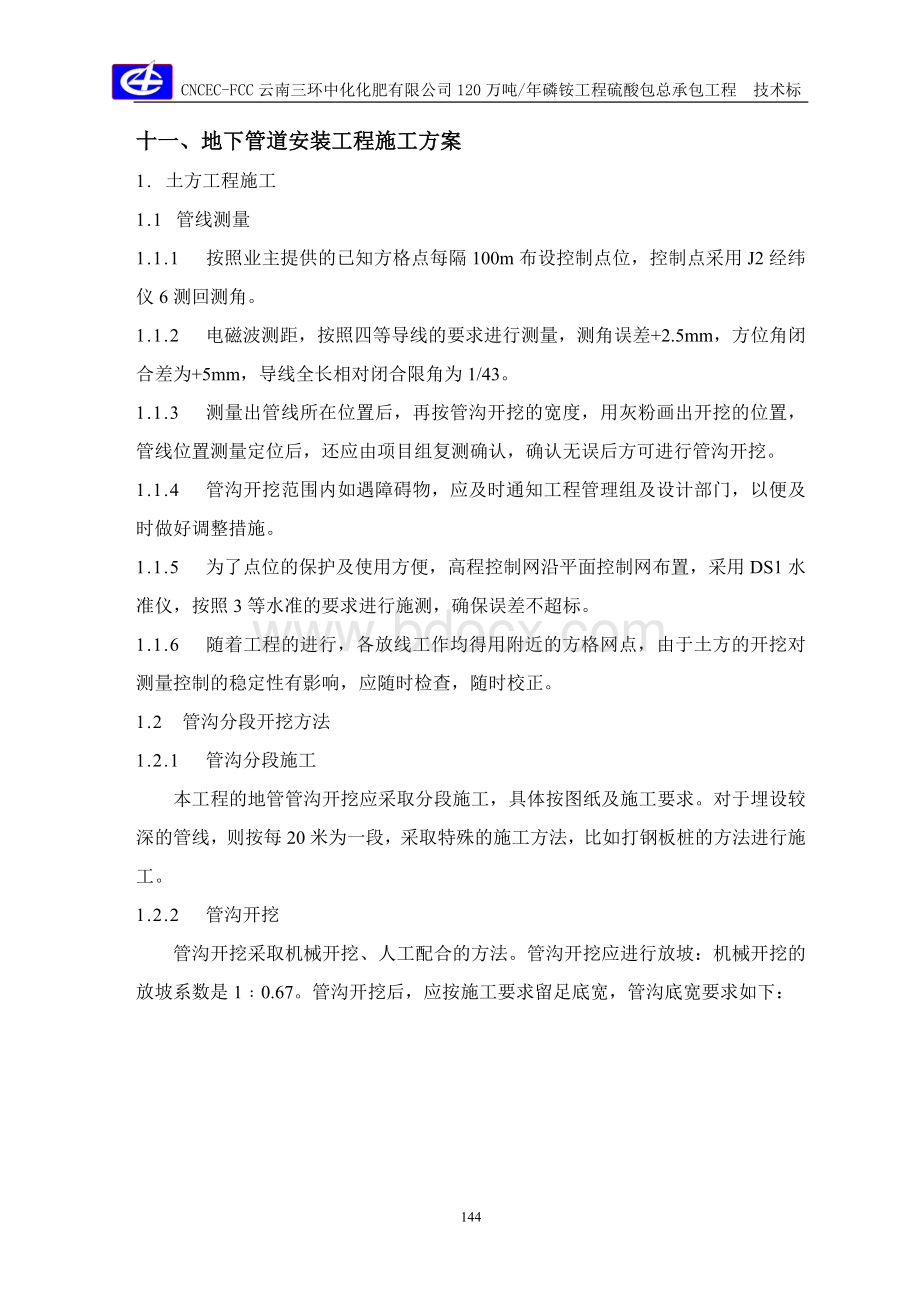
管沟开挖应进行放坡:
机械开挖的放坡系数是1﹕0.67。
管沟开挖后,应按施工要求留足底宽,管沟底宽要求如下:
管径(mm)
钢管(mm)
非金属管(mm)
100~200
700
250~350
800
1000
400~450
1300
500以上
1.2.3沟槽开挖过程中,沟底应留出0.2~0.3m原土层,待铺管或浇筑垫层前用人工挖到设计标高。
1.2.4管沟开挖时沟边堆土高度不超过1.5m,大部分须堆放在离管沟边缘1m之外的地方,土方堆放要整齐,沟底应每隔一段距离(100米)设一个集水坑。
其断面形式如下:
1.3土方运输
管沟开挖出的土方,除预留回填用土外,多余土方运往甲方指定的地方,汽车运土出现场前,车轮必须冲洗干净,沿途道路应保持清洁,拟设四名保洁工沿途清扫,送往堆土区的土方必须用推土机推平。
1.4管沟排水
在厂区内施工,土质含水多且在春季施工,要充分考虑管沟的排水,所以每挖一段管沟都要设置集水井,以便将沟内的集水及时排掉,以保持场地土体干燥,保证土方施工顺利进行。
2.井室砌筑
2.1根据设计井室采用不同结构的砖砌混凝土、混凝土井。
须采取现场支模、现场浇注的,按规范砌筑。
2.2施工中木模制作、钢筋绑扎、砼浇注一定要按规范施工,每道工序合格后方可进入下一道工序。
2.3井壁刚性防水套管在井室浇注时,注意安装位置应正确。
2.4路面上井室应与路面平齐,高度允许差为±
5mm,无路面时井盖离出地面不应超过50mm。
2.5阀门井井室施工前,应用纺织袋保护好阀门,以免损坏阀门。
3.土方回填
埋地管道安装完毕,经过监理、业主方确认后,应及时回填土,填土前排干积水,试压管道经试压合格后及时回填土。
回填土要从管道两侧填,并用蛙式打夯机夯实,不得损坏管子及防腐层。
分层夯实时,一次夯实厚度不大于0.3米,密实度不小于95%。
4.管道施工
4.1管道安装前准备
4.1.1管道应在沟底中心线、标高、基础、坡度均符合质量要求后方可进行敷设,必要时进行局部回填,严防塌方或沟两侧土层挤翻基础垫层和管道。
4.1.2防腐好的管道在运输时要用草袋衬垫,以避免防腐层受伤(管道防腐另见防腐施工方案)。
4.1.3管道吊装应在焊接吊耳后再进行吊装,以保护防腐层吊装时少受损伤。
4.2钢管的安装
4.2.1管子、管件组对时,接口应做到平整,错边量不得超过壁厚的20%,且不大于2mm;
4.2.2管道焊接采用手工电弧焊;
焊接钢管、管件的坡口:
采用“V”形坡口,单面焊,双面成型。
坡口尺寸如下图所示:
α
C
T
P
>
4~9mm
10~26mm
60°
~70°
+5°
1.5~3mm
2~4mm
1.1~5mm
1~2mm
4.2.3坡口加工采用氧—乙炔焰加工,并用砂轮机打磨,焊前应将坡口表面及坡口边缘内侧不少于10mm范围的油漆、污垢、锈、毛刺等清理干净,并不得有裂纹、夹层等缺陷。
4.2.4若工作环境的风力大于5级、雨天或相对湿度大于90%时,应采取保护措施后才能施焊。
4.2.5点焊时,应对称施焊,其厚度应与第一层焊接厚度一致。
4.2.6管道法兰连接时,法兰接口平行度允许偏差应为法兰外径的1.5%,且不大于2mm;
螺孔中心允许偏差应为孔径的5%。
4.2.7大管径的管道在组对时应注意对已施工完的防腐层进行保护,可采取管端末防腐处垫枕木或使用龙门架组对,以便于组对施焊,保护防腐层不受损伤。
4.3钢筋混凝土管施工
4.3.1管节安装前应检查外观是否有裂缝,保护层脱落、空鼓、接口掉角等缺陷,经检查合格的管道方可使用。
4.3.2管座分层浇筑时,管座待混凝土抗压强度应大于5N/mm2方可进行安管,管道安装前应将管内外清扫干净,安装时应使管道内节内底高程符合图纸要求,调整管道中心及高程时,必须垫稳,两侧设撑杠,不得发生滚动。
4.3.3管道中心、高程复验合格后,应及时浇筑管座混凝土。
混凝土管座的模板分两次支设,先支设一次模板浇筑管底垫层,待管道铺设好后,再支设模板浇筑管座砼;
4.3.4浇筑混凝土管座时,留混凝土抗压强度试块。
每工作班3块。
4.3.5圆形橡胶圈应符合国家现行标准的规定。
使用前必须逐个检查,不得有割裂、气泡、大飞边等缺陷。
4.3.6管道安装时,承口内工作面、插口外工作面应清洗干净。
4.3.7非金属管道基础及安装的允许偏差应符合标准GB50268-97表4.5.22的规定。
4.3.8管道采用钢丝网水泥砂浆接口,在抹带前应将管口的外壁凿毛、洗净,抹带应分两层抹层,钢丝网端头应在浇向混凝土管座时插入砼内,插入深度为150mm;
在混凝土初凝前,分层抹压钢丝网水泥砂浆抹带;
抹带完成后,应立即用平软材料覆盖,3~4h后洒水养护。
抹带水泥砂浆的厚度、宽度、钢丝网的宽度、水泥管接口的间隙见下图。
钢丝网水泥砂浆抹带接口应平整,不得有裂缝,空鼓等现象,抹带宽度、厚度的允许偏差为0~+5。
管线全部安装后做闭水实验。
4.4铸铁管安装
4.4.1铸铁管、球墨铸铁管及管件的外观质量应符合规定:
表面不得有裂纹;
橡胶圈接口的管节,承口的内工作面和插口的外工作面应光滑、轮廓清晰,不得有影响接口密封性的缺陷。
4.4.2管及管件下沟前,应清除承口内部的油污、飞刺、铸砂及铸瘤;
有裂纹的管及管件不得使用。
4.4.3铸铁管应在沟底中心线、标高、坡度均符合质量要求后方可进行安装。
4.4.4铸铁管安装配合土方开挖,分段施工,分段验收。
4.4.5铸铁管连接采用承插连接,石棉水泥接口。
接口应符合下列规定:
4.4.5.1水泥宜采用32.5级水泥;
4.4.5.2石棉选用机选取4F级温石棉;
4.4.5.3油麻采用纤维较长、无皮质、清洁、松软、富有韧性的油麻;
4.4.5.4石棉水泥应在填打前拌和,石棉水泥的重量配合比为:
石棉30%,水泥70%,水灰比宜小于或等于0.2,拌和好的石棉水泥应在初凝前用完。
填打后的接口应及时潮湿养护。
4.4.5.5铸铁、球墨铸铁管安装偏差应符合下列规定:
项目
允许偏差(mm)
无压力管道
压力管道
轴线位置
15
30
高程
±
10
20
5.管道试压
5.1管道试压的条件
5.1.1以下施工资料必须齐全:
材料质量证明书;
管道组成件,焊接材料的检验性检查或试验记录;
设计变更及材料代用文件。
5.1.2管道系统全部按设计文件安装完毕。
5.1.3管道支架的形式、材质、安装位置正确,数量齐全,牢固程度、焊接质量合格。
5.1.4焊接工作全部完成,焊缝质量检查合格。
5.1.5焊缝及其它应检查的部位不应隐藏。
5.1.6试压用的临时加固措施安全可靠,例如:
临时支架要牢固,能承受试压水重。
临时盲板加置正确,并应标识明显,同时在单线图上作出标记,记录应完整,高低排放点设置完毕且正确。
5.1.7不能参与试压的流量孔板、流量计等应拆除,用临时短管连接。
5.1.8有经过批准的施工方案,并对试压小组进行交底。
5.2液压试验:
按设计要求,压力管道做压力试验,试验压力不小于0.9MPa。
无压管道做漏水试验。
5.3试验时应利用高排点排尽系统内的空气,升压应分级缓慢,到达试验压力后停压10min,然后降至设计压力稳压30min,以无压降、无泄漏,目测无变形为合格。
试压时如有泄漏,不得带压修复,缺陷消除后应重新试压,直至合格为止。
5.4管道系统试压合格后,应缓慢降压,试验介质宜在合适地点排放,尽量将试压用水排入附近的污水沟或雨排管中。
试压完毕后的管道系统如果吹扫不用的临时盲板、短管、支架应拆除,及时复位,并填写管道系统试压记录。
6.管道冲洗
6.1冲洗前的准备工作
6.1.1压力试验完成后,方可进行管道系统的冲洗。
6.1.2应有经过审批的冲洗方案,绘制冲洗系统详图。
6.1.3准备临时冲洗管,临时过滤器,旁通管或隔离盲板,并在单线图上作出标记。
6.1.4准备好吹扫检测用工具。
6.1.5冲洗方法:
采用清洁水进行水冲洗;
6.2水冲洗
6.2.1冲洗水应是洁净水。
6.2.2水冲洗的压力不应超过管道的工作压力,采用最大的流速进行冲洗。
6.2.3支管冲洗应在主管冲洗干净后,才能进行冲洗。
6.2.4用玻璃杯取冲洗管线出口处的水,检查水质颜色和透明度是否同入口处一致为合格。
合格后的管线,应将水排尽。
6.3冲洗合格后的管线,应进行恢复,恢复程序同拆除步骤相反,同时盲板拆除后,应换上正式垫片,恢复完成后,由项目组进行现场确认,填写冲洗记录。
150