汽车零部件传统设计与现代设计方法之比较Word文档下载推荐.doc
《汽车零部件传统设计与现代设计方法之比较Word文档下载推荐.doc》由会员分享,可在线阅读,更多相关《汽车零部件传统设计与现代设计方法之比较Word文档下载推荐.doc(12页珍藏版)》请在冰豆网上搜索。
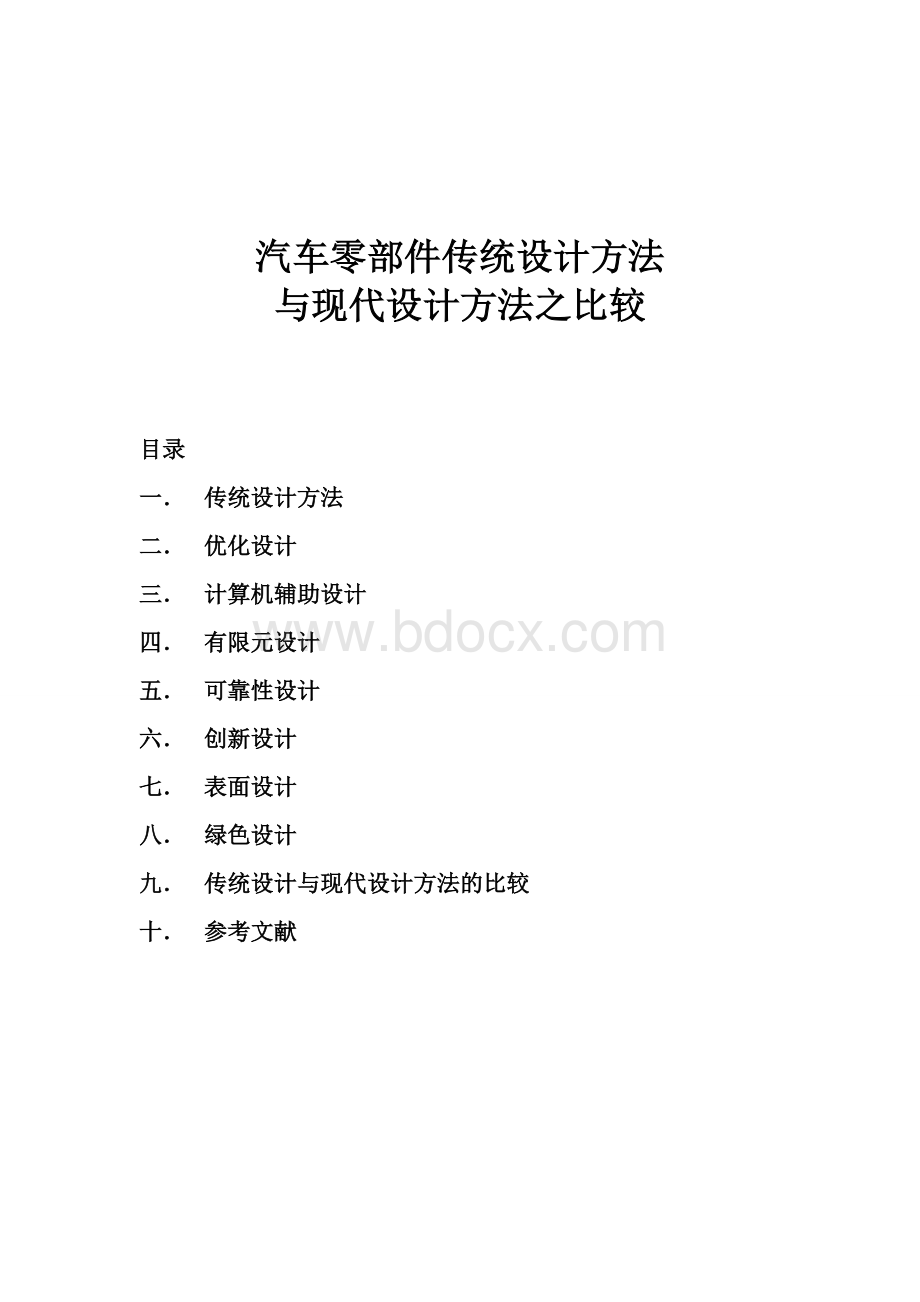
当时人们或许是从自然现象中直接得到启示,或是全凭人的直觉感官来设计制作工具。
设计方案存在于手工艺人头脑之中,无法记录表达,产品也是比较简单的。
直觉设计阶段在人类历史中经历了一个很长的时期,17世纪以前基本上都属于这一阶段。
1.2经验设计
随着生产的发展,单个手工艺人的经验或其或其头脑中自己的构思已经难以满足要求,因而促使手工艺者联合起来互相协作,逐渐出现了图纸,并开始利用图纸进行设计。
一部分经验丰富的人将自己的经验或构思用图纸表达出来,然后根据图纸组织生产。
图纸的出现,既可使具有丰富经验的手工艺人通过图纸将其经验或构思记录下来,传于他人,便于用图纸对产品进行分析、改进和提高,推动设计工作向前发展;
还可以满足更多的人同时参加统一产品的生产活动,满足社会对产品的需求及生产率额要求。
因此,利用图纸进行设计,使人类设计活动由直接设计阶段进步到经验设计阶段。
1.3半理论半经验设计
20世纪以来,由于科学和技术的发展和进步,对设计的进出理论研究和实验研究得到加强。
随着理论研究的深入和试验数据的积累,逐渐形成了一套半经验半理论的设计方法。
这种方法以理论计算和长期设计实践而形成的经验、公式、图表、设计手册等作为依据,通过经验公式、近似系数或类比等方法进行设计。
依据这套方法进行机电产品设计,称为传统设计。
所谓“传统”是指这套设计方法已沿用了很长时间,直到现在仍被广泛地采用这。
传统设计又被称为常规设计。
优化设计(optimaldesign)也叫最优化设计,是从多种方案中选择最佳方案的设计方法。
它以数学中的最优化理论为基础,以电子计算机为辅助工具的一种设计方法。
这种方法首先将设计问题按规定的格式建立数学模型,并选择合适的优化算法,选择或编制计算机程序,然后通过计算机自动获得最优设计方案。
对机械工程来说,优化设计方法使机械设计的改进和优选速度大大提高。
优化设计不仅应用于产品成型后的再优化设计过程中,而且已经渗透到产品的开发设计过程中。
同时,它与可靠性设计、模糊设计、有限元法等其他设计方法有机结合取得了新的效果。
1.1CAD的概念
1.1.1CAD的定义
计算机辅助设计(ComputeraidedDesign)是指工程技术人员以计算机为工具,用各自的专业知识,对产品进行总体设计、绘图、分析和编写技术文档等设计活动的总称。
1.1.2CAD系统的功能
几何建模
计算分析
仿真试验
绘图及技术文档生成
工程数据库的管理与共享
1.1.3CAD的作业过程
CAD工作的主要内容为:
①建立产品设计数据库:
产品设计数据库用来存储设计某类产品时所需的各种信息、如有关标准、线图、表格、计算公式等。
数据库可供CAD作业时检索和调用,也便于数据的管理及数据资源的共享。
②建立多功能交互式图形程序库:
这个图形程序库可以进行二维、三维图形的信息处理,能在此基础上绘制二程设计图样、多种函数曲线、可进行图形变换和投影变换、可作三维几何造型和形体的真实感处理。
③建立应用程序库:
编制及汇集解决某一类工程(或产品)设计问题的通用及专用设计程序。
如通用数学程序、常规机械设计程序、优化设计程序、有限元计算程序等。
设计模型定义
工程分析计算
满意?
结果输出
N
Y
数据库
程序库
图形库
1.1.4CAD的特点
Ø
缩短产品开发周期
提高产品设计质量
降低生产成本
便于产品标准化、系列化、通用化
CAD是CAM和CAPP的前提和基础
1.1.5CAD的发展过程
CAD数据模型的发展
我国CAD技术的应用情况
vCAD的集成化程度较低,很多企业的应用仍停在绘图、分析计算等单项技术的应用上;
vCAD系统的软、硬件均依靠进口,自主版权的软件较少;
v缺少人才和技术力量,致使有些企业尽管引进了CAD软件系统,但其功能没能充分的发挥。
CAD的发展趋势
集成化
集成化包括软件硬件的集成、不同系统之间的集成、以及通过网络多媒体数据库实现异地系统协同共享信息资源等。
标准化
标准化指研究开发符合国际标准化组织颁布的产品数据转换标准、制定网络多媒体环境下数据信息的表示和传输标准、制定统一的国家CAD技术标准体系。
网络化
网络化指充分发挥网络系统的优势,共享昂贵的设备;
借助现有的网络,用高性能的PC机代替昂贵的工作站;
在网络上方便地交换设计数据。
智能化
智能化指将领域专家的知识和经验归纳成必要的规则形成知识库,再利用知识的推理机制进行推理和判断,以获得设计专家水平的设计结果。
1.1.6CAD系统的类型
检索型CAD系统
适用基本结构已经定型,有标准零部件和结构可以借鉴的产品,即标准化、系列化产品的设计。
如电机、泵、减速器等。
建立系统时,首先把选定产品的有关设计资料如标准图形信息、加工工艺信息等存入计算机中,需要时输入设计要求,系统自动从所存储的信息中把符合要求的信息检索出来,以图形或文件的形式输出。
缺点是当不能完全满足初始参数要求时,系统将无法输出正确结果。
计算型CAD系统
也称作自动设计型CAD系统
设计人员按设计要求输入基本参数以后,无需或只需很少的人工干预,由计算机按照预先编制好的程序自动地完成全部设计任务。
适用于那些设计理论成熟、计算公式确定、设计步骤及判别标准清楚的产品。
例如齿轮减速箱设计系统等。
交互型CAD系统
交互型CAD系统是指在设计时由设计人员与计算机进行人机对话,人工干预方案决策、作出判断及修改设计等,由设计人员与计算机系统一起互相配合工作、以得到一个最优设计。
这种交互型CAD系统最适合目前工程实际中产品设计与开发的任务,是目前应用最普遍的一种CAD系统。
例如AutoCAD、Prp/Engineer、SolidWorkS。
——有限元分析在汽车工程方面的应用
1.前言
计算机辅助工程(CAE)作为一项跨学科的数值模拟分析技术,越来越受到科技界和工程界的重视,在汽车工业研究中的应用也越来越广泛。
在汽车产品的研发过程中,CAE已经成为设计链中必须的条件,没有CAE分析的设计就不能进入下一个技术流程。
新产品开涉及到的疲劳、寿命、振动、噪声等强度和刚度问题,可成熟地在设计阶段解决,这样就可以大幅度提高设计质量,缩短产品开发周期,节省大量开发费用。
本文通过对有限元分析在汽车工程方面的应用的描述和分析,阐述了以有限元分析为代表的CAE技术在汽车工程的重要作用和影响,得出了CAE在汽车工业发展更加重要,影响未来汽车的发展趋势!
在汽车发展历史上,至今还没有什么技术能与CAE技术相比,为汽车企业带来巨大的回报。
统计结果表明,应用CAE技术后,新车开发期的费用占开发成本的比例从80%~90%下降到8%~12%。
例如:
美国福特汽车公司2000年应用CAE后,其新车型开发周期从36个月降低到12~18个月;
开发后期设计修改率减少50%;
原型车制造和试验成本减少50%;
投资收益提高50%。
汽车行业是一个高速发展的行业,其竞争也日趋激烈,在这种情况下,新产品推出的速度也越来越快,这也对行业的CAE应用提出了越来越高的要求。
CAE技术为汽车行业的高速发展提供具有中心价值地位的技术保障,可以为企业带来巨大的技术经济效益。
[2]
2.正文
汽车工业代表着一个国家制造业发展的水平,它不仅是带动面最广泛的工业,而且是高新技术的最大载体,一般航空、航天领域的高精尖技术只有通过汽车工业才能转化为规模产业,所以汽车工业是或曾是几乎所有发达国家的支柱产业。
作为制造业的中坚,汽车工业一直是CAE应用的先锋。
CAE技术的应用,有效地推动了汽车制造业的前进;
汽车业的需求也极大地带动了CAE。
多年来,汽车业的选型趋向一直是CAE技术发展的晴雨表,也是业内人士关注的焦点。
CAE分析贯穿了汽车开发的全过程,小到螺栓预紧力分析,大到整车碰撞模拟和整车NVH(噪声、振动和声振粗糙度)分析,CAE分析都发挥了无可替代的优势和作用。
CAE分析范围覆盖了结构、流体力学、多体动力学、被动安全、工艺、整机合整车性能等方方面面。
概括起来,目前汽车开发过程中的CAE分析主要包括以下几个方面。
[3]
2.1结构强度、刚度和模态分析及结构优化设计
车身是轿车的关键总成,车身结构必须有足够的强度以保证气疲劳寿命,足够的静刚度以保证其装配和使用要求,同时应有合理的动态特性达到控制振动与噪声的目的。
有限元分析的方法能够有效地满足上述车身设计的要求。
汽车结构有限元分析的应用体现于:
一是在汽车设计中对所有的结构件、主要机械零部件的刚度、强度和稳定性进行分析;
二是在汽车的计算机辅助设计和优化设计中,用有限元法作为结构分析的工具;
三是在汽车结构分析中普遍采用有限元法来进行各构件的模态分析,同时在计算机屏幕上直观形象地再现各构件的振动模态,进一步计算出各构件的动态响应,较真实地描绘出动态过程,为结构的动态设计了提供方便。
有限元分析在汽车结构上的应用实践证明可以从根本上提到车身设计水平,并降低研制周期和成本。
[4]
2.2噪声、振动与不平顺性(NVH)的有限元分析
NVH是评价车辆舒适性的重要指标,直接关系到产品的市场形象。
NVH分析有助于匹配产品结构重各子系统的振动频率特性,以消除振动过程中耦合现象,从而改善产品的振动特性。
噪音、振动分析包括动力总成的缸体模态、点的传递函数、静负荷强度及动态响应、BIW动态稳定性、整车各子系统的刚度频率匹配等。
虽然NVH的CAE技术起步较晚,NVH的建模方法以及计算还处在摸索阶段。
但随着计算机的能力及容量的越来越强大,计算结果的精度越来越准确,计算方法越来越科学性,CAE在汽车的NVH开发设计当中所发挥的作用也越来越大。
在汽车开发设计的初期,就以及开始了NVH的各项规划,甚至在样车完成之前或设计图纸完成之前,通过对现有车型的对比,就可以预先得到新开发车型的NVH性能指标,并在此基础上,对设计及制造的各个环节加以优化及完善。
无论是从设计成本上,还是从开发周期上考虑,都为车厂更快、更好地开发出新一代车型来提供了强有力的保障。
可以预测,NVH的CAE技术,在汽车设计开发及改进领域内的应用会越来越广泛,而其本身也会越来越成熟,成为人们进行汽车设计开发所不可或缺的工具。
[5]
2.3碰撞与安全性分析
私家汽车给人们带来了便利,让人们更充分的享受生活。
随着全世界汽车数量的迅速增加,汽车质量、驾驶技术问题及道路状况等多种因素合力作用结果,汽车交通事故已成为严重问题。
联合国世界卫生组织(WHO)提交的最新报告显示:
近几年全球每年因交通事故造成死亡的人数多达约120万,另外还有数百万人在汽车事故中受伤致残。
面对这个严重的问题,各国的工程技术人员都在不遗余力的提高汽车的安全性能。
早期的被动安全性研究主要是通过大量的试验来进行,采用同样的碰撞过程反复进行,收集数据。
这样的试验方法需要相当长的时间。
发达国家每次汽车安全性能的试验都需要手工打造几十辆新车,人力、物力、财力都需要很大的消耗。
伴随着计算机技术的发展,原来不可能完成的大量参数有限元计算成为可能。
有限元计算分析方法运用到汽车的碰撞模拟仿真中,极大地降低了汽车的设计成本和研发周期,并且获得更为精确的数据对汽车结构进行下一步优