汽车设计汽车热成型零部件设计规范模板Word格式文档下载.docx
《汽车设计汽车热成型零部件设计规范模板Word格式文档下载.docx》由会员分享,可在线阅读,更多相关《汽车设计汽车热成型零部件设计规范模板Word格式文档下载.docx(15页珍藏版)》请在冰豆网上搜索。
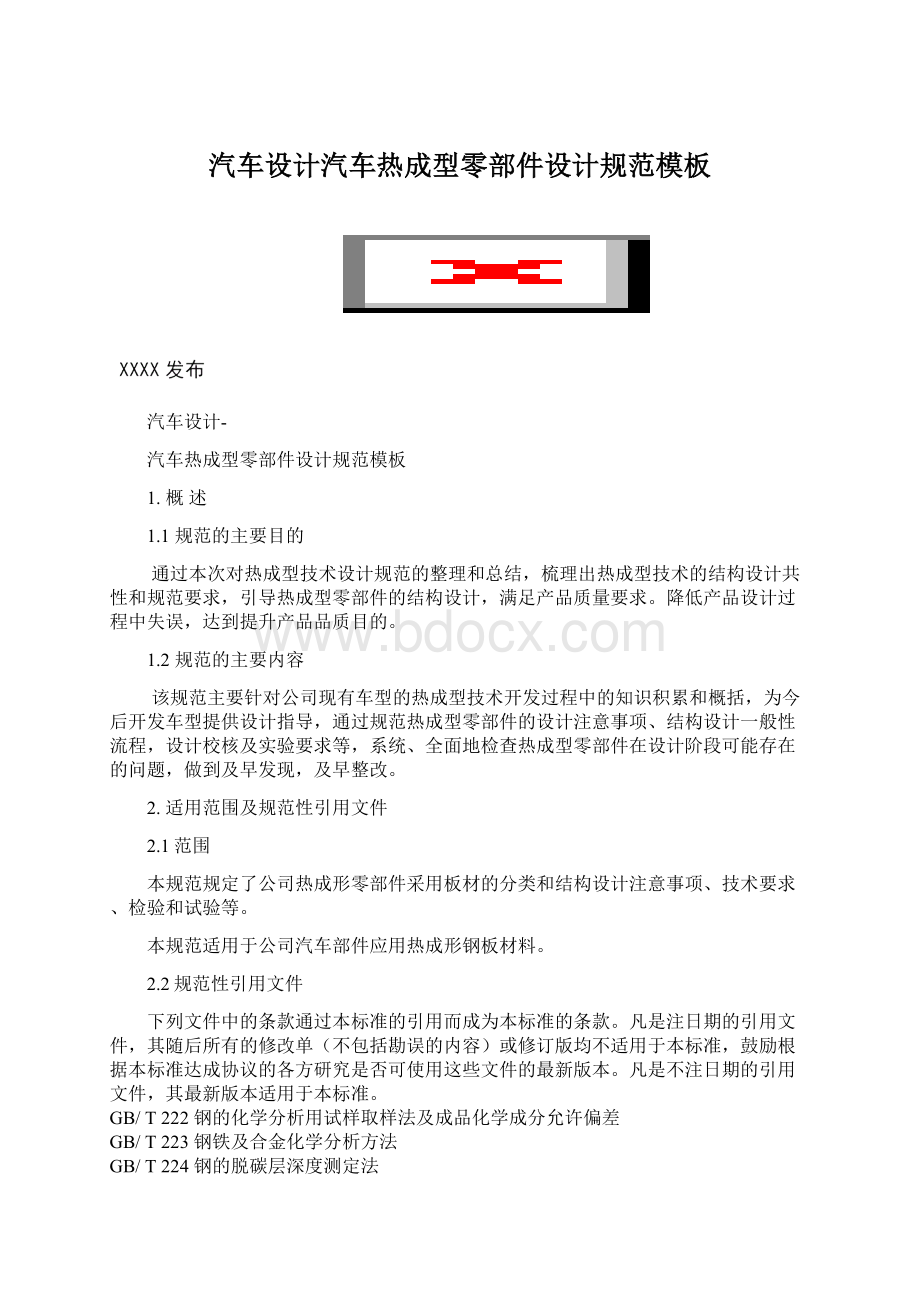
GB/T228金属材料室温拉伸试验方法
GB/T4340金属维氏硬度试验
GB/T8170数值修约规则
GB/T13298金属显微组织检验方法
GB/T13299钢的显微组织评定方法
3.术语和选材规格
3.1热成型
热成型是把钢板加热到900℃左右的奥氏体区进行冲压成形,通过制件在冲压金属模内冷却淬火强化的一种成形工艺。
3.2热成型钢
热成形钢是一种低碳合金钢,含有一定量的锰、硼为主的合金元素,具有良好的热处理性能,可以通过直接热冲压成形或先预成形再热冲压成形同时模具内淬火,从而获得高强度。
3.3热成选材规格
冷轧B1500HS/BTR165
NO.
thickness(mm)
width(mm)
1
0.70~0.90
900~1200mm(max1250mm)
2
0.91~1.20
900~1300mm(max1350mm)
3
900~1400mm(max1450mm)
4
1.51~1.80
900~1450mm(max1500mm)
注:
选材必须符合公司车身材料选材库
4.热成型技术的优势及应用范围
4.1.热成型技术的优势:
1)提高车型的碰撞性能;
2)实现更大程度的车身轻量化,降低油耗;
3)零件成形性相对较好,不易回弹;
4)采用激光切割,零件精度容易保证;
5)车身结构设计简单,减少加强板数量;
6)降低压机吨位要求,减少固定投资;
7)有效提高零件的表面硬度及耐磨性;
8)通过车身结构优化设计,可以有效控制车身综合制造成本。
4.2热成型的应用范围:
1)前、后门左右防撞杆(梁);
2)前后防撞梁;
3)下车身前后梁;
4)A柱加强板;
5)B柱加强板;
6)C柱加强板;
7)地板中通道;
8)车顶加强梁;
9)其它车身、底盘结构件、加强件等。
5.热成型技术工艺介绍
5.1热成型工艺分为两种:
1)直接成型工艺:
直接热成型中,板材不经过预成型,直接将平板加热奥氏体化,然后放入模具中高速成型,冲压深度到达预定值,直接成型工艺流程如下图;
2)间接成型工艺:
间接成型工艺也称为多步热冲压,材料首先在常规冷成型模具中成型到最终形状的90%~95%,然后将预成型的零件加热奥氏体化并热成型和淬火硬化。
在间接热成型工艺中,零件的预成型可以减材料与模具之间的相对位移,从而减小模具表面在高温下的磨损。
对于一些形状复杂或拉深较大的工件使用这种工艺,但间接工艺增加了设备成本,国内主机厂大多采用直接成型工艺。
5.2热成型板料:
热成型板料采用带镀层和不带镀层两种超高强钢板材,这两种不同类型超高强钢板的冲压工艺也有所区别。
1)带镀层钢板:
在热冲压过程中不会产生氧化皮,但加热时镀层容易与加热炉的套磁辊发生粘结,且价格较贵,其基本流程可概括为:
下料→加热、保温→冲压成形、淬火→保压定型→激光切边、冲孔→喷丸→涂油。
2)不带镀层的超高强钢板:
其加热时会产生氧化皮,其冲压工艺基本流程可概括为:
下料→喷涂防氧化涂料→加热、保温→冲压成形、淬火→保压定型"
激光切边、冲孔"
去涂层→涂油。
考虑到成本因素,除了工作环境相对恶劣的零件,目前主机厂倾向于使用非镀层钢板。
6.热成型零部件结构设计注意事项
6.1热成型零部件为一次性成型,后进行激光切割,杜绝热成型零部件有冲压负角。
6.2热成形结构的设计中,应该避免圆孔翻边(如下图1)。
目前的热冲压工艺中进行圆孔热翻边是比较困难的很难达到必要的精度,且很难将胚料优化到可以翻孔的位置,且翻边后难以做激光切割。
图1
6.3热成形零部件设计成型结构时应注意拉延-法兰边区域,这些区域有更高的起皱、开裂风险。
外凸翻边的最终线长度比初始长度短(如下图2)产生压缩法兰边,容易导致起皱和折叠,且起皱的趋势随翻边高度的增加而增大,建议翻边控制在5mm以内。
内凹翻边属于伸长类翻边,产生拉伸法兰边(如下图3),竖边的长度在成形过程中会被拉长,当变形程度过大时,竖边边缘的切向伸长和厚度减薄就比较大,容易发生拉裂。
法兰边越高,拉伸失稳越明显。
无论是外凸翻边,还是内凹翻边,都应降低翻边高度和曲率。
总体上说,热成形零部件不宜有翻边,尤其是90度的翻边特征。
图2图3
6.4热成形零部件结构设计中,翻边特征是外凸翻边且转角很急的情况下做以下缺口改进(如下图4)。
避免局部堆料起皱(保证焊接边15mm,缺口处到圆角保证3mm以上).
图4
翻边成形的改进设计
6.5降低拉延深度,且成形深度尽可能相同,应能够采用一次拉延成形,避免多次拉伸。
冷拉深成形中,零件易在凸模圆角处开裂。
而热拉深成形时,板料与模具在凸凹模圆角处先接触(如下图5),导致这些部位首先冷却硬化,变形抗力增大。
变形将转向温度较高、具有良好塑性流动性的拉延侧壁,导致应变集中。
由于侧壁处于平面应变状态,拉延深度的增加依靠材料厚度的减薄,因而易产生拉裂,且拉裂的倾向随着拉深深度的增加而加剧。
(a)(b)
板料与模具接触时对成形的影响:
(a)接触时序不同导致温度分布不均匀;
(b)局部塑性变形
图5
6.6热成型零部件截面形状上应避免直壁和阶梯形零件的拉深成形。
直壁和阶梯型截面形状在成形过程中,材料流动阻力增大,且热板料与模具的接触状况差,接触压力低,甚至出现不与模具接触的非接触区域,影响板料快速淬火。
应采用锥形(α≥93°
)或是抛物线形拉深成形(如下图6)。
拉深成形:
(a)锥形拉深;
(b)抛物线形拉深
图6
6.7热成型零部件结构分尺寸比例要恰当,尽量避免设计宽凸缘和深拉延(D>3d,h≥2d,d为工件直径,D为凸缘直径,h为拉深深度);
拉深成形的圆角半径要合适,圆角半径尽量取大,一般应满足关系:
R≥5t(t为板料厚度,R为圆角半径);
6.8热成型零部件特征避免高落差急剧变化,以减少堆料问题,在中间需有过渡特征,可减缓特征变化,以便多余材料能及时消除(如下图7)。
优化前优化后
图7
6.9避免剧烈的几何形状过渡(如下图8)
板料与模具间存在接触时序上的差异,急剧的几何形状过渡将会造成接触,时序相差更大,更易产生高的温度梯度,加剧应变集中。
B柱的形状设计必须平缓过度,增加过渡圆角半径,尽可能的减少变形过程中不与模具接触的板料面积。
减小零件沿长度方向的弯曲角度。
过大的弯曲角度会使得冲压方向的选择变得困难,影响零件的成形。
图8
6.10由于模具在制作过程中,冲压方向选择产品各方面比较均衡的方向,因此相关的锁位凸包,需以出模方向进行设计,冲压方向确定的一个原则是:
以产品能够在4个角能尽量保证上模同时接触胚料为原则(如下图9)。
图9
6.11圆角要求:
拐角处尽可能的以球R接顺,且尽可能的大(如下图10)
图10
6.12锁扣为和门铰链位的凸包在满足功能要求的情况下,尽可能降低凸包高度,且凸包面的角度要尽可能的大,然后倒R15以上圆角。
孔位凸包不能做得太深,且周边R角和斜度都必须是做大,以防止局部缺料而拉薄拉裂(如下图11).
图11
6.13热成型零部件应尽量采用规则的形状设计,降低不对称度,截面形状应该尽量简单对称。
对称度较差的零件设计,会导致坯料难以定位(如下图12)。
在成形过程中,坯料可能会产生转动,模具与坯料接触状态差,甚至会影响材料的流动和淬火冷却。
图12
6.14B柱结构应尽量避免封闭式设计,而采用开放式设计。
尽可能采取弯曲成形,减少法兰边产生起皱、减薄以及拉裂的危险。
封闭式的“杯状”结构会导致成形过程中材料在凸凹模拐角处产生压缩变形和起皱,在满足使用要求的情况下,增大零件圆角半径或侧壁的倾斜度有利于成形(如下图13)。
图13
6.15板件(侧壁)弯曲时,若弯曲处的圆角过小,则外表面容易产生裂纹。
如使用涂层板时,还会引起涂层的剥离,为此规定最小弯曲半径R≥2t(t为板料厚度,R为弯曲半径);
防止圆角在弯曲时受压产生挤料后起皱,应设计预留切口(如下图14)。
图14
6.16热成形零部件的应尽量在零件上设置吸皱筋(余料仓),防止零件的起皱。
尤其是B柱零件的端部和中间梁的设计中,应该设置吸皱筋(如下图15)。
同时有利于焊接工艺。
图15
6.17热成型零部件红色R角需要尽可能的大,方便在成型过程中材料的流动,避免产品表面的拉伤和刮痕(如下图16)。
图16
7.技术要求
7.1一般技术要求
7.1.1表面质量
热冲压件加工表面不允许有裂纹、夹杂、起皱、氧化皮、切边拉伤等缺陷,对于不带涂层的热冲压成形制件,表面应经过喷丸或其他处理方式去除氧化皮。
7.2材料特性要求
7.2.1化学成分
7.2.1.1热成形钢板的化学成分(熔炼分析)应符合下表的规定,且不含禁限用物质,满足公司汽车禁用和限用物质规范Q/ZTB07.25。
牌号
化
学
成
分
%
C
Si
Mn
P
S
Alt
B
Cr
MO
TI
B1500HS/BTR165
0.18~0.28
≤0.7
2.0~4.0
≤0.025
≤0.01
≥0.020
≤0.004
≤0.4
≤0.06
0.22~0.27
0.15~0.5
1.1~1.4
≤0.011
0.02~0.06
0.0015~0.0035
≤0.35
0.03~0.05
7.2.1.2热成形钢及钢管的成品化学成分允许偏差应符合GB/T222的规定。
7.2.2力学性能
7.2.2.1热成形钢管的力学性能应符合下表的规定。
状态
牌号
屈服强度MPa
抗拉强度MPa
延伸率A50(%)
热成形后
≥1000
≥1300
≥6
7.2.2.1热成形钢板的力学性能应符合下表的规定。
延伸率A80(%)
推荐料厚(mm)
热轧