支座砂型铸造工艺设计说明书Word文件下载.docx
《支座砂型铸造工艺设计说明书Word文件下载.docx》由会员分享,可在线阅读,更多相关《支座砂型铸造工艺设计说明书Word文件下载.docx(29页珍藏版)》请在冰豆网上搜索。
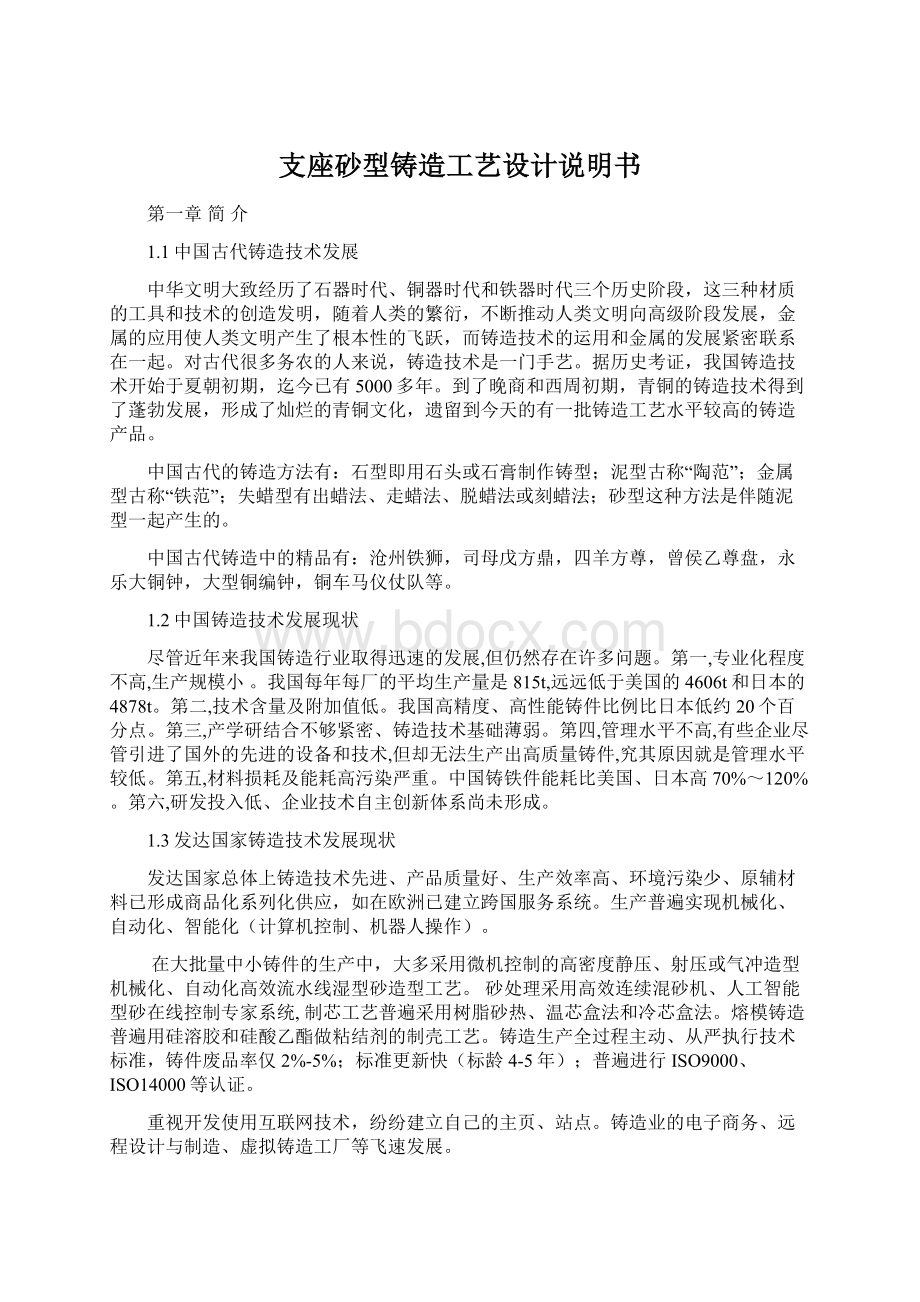
我国每年每厂的平均生产量是815t,远远低于美国的4606t和日本的4878t。
第二,技术含量及附加值低。
我国高精度、高性能铸件比例比日本低约20个百分点。
第三,产学研结合不够紧密、铸造技术基础薄弱。
第四,管理水平不高,有些企业尽管引进了国外的先进的设备和技术,但却无法生产出高质量铸件,究其原因就是管理水平较低。
第五,材料损耗及能耗高污染严重。
中国铸铁件能耗比美国、日本高70%~120%。
第六,研发投入低、企业技术自主创新体系尚未形成。
1.3发达国家铸造技术发展现状
发达国家总体上铸造技术先进、产品质量好、生产效率高、环境污染少、原辅材料已形成商品化系列化供应,如在欧洲已建立跨国服务系统。
生产普遍实现机械化、自动化、智能化(计算机控制、机器人操作)。
在大批量中小铸件的生产中,大多采用微机控制的高密度静压、射压或气冲造型机械化、自动化高效流水线湿型砂造型工艺。
砂处理采用高效连续混砂机、人工智能型砂在线控制专家系统,制芯工艺普遍采用树脂砂热、温芯盒法和冷芯盒法。
熔模铸造普遍用硅溶胶和硅酸乙酯做粘结剂的制壳工艺。
铸造生产全过程主动、从严执行技术标准,铸件废品率仅2%-5%;
标准更新快(标龄4-5年);
普遍进行ISO9000、ISO14000等认证。
重视开发使用互联网技术,纷纷建立自己的主页、站点。
铸造业的电子商务、远程设计与制造、虚拟铸造工厂等飞速发展。
1.4我国铸造未来发展趋势
自中国加入WTO以来,我国铸造行业面临机遇与挑战。
其未来发展将集中在以下几方面。
第一,鼓励企业重组发展专业化生产,包括铸件大型化和轻量化生产。
第二,加大科技投入切实推动自主创新,实现铸件的精确化生产和数字化铸造。
第三,培养专业人才加强职工技术培训。
第四,大力降低能耗抓好环境保护,实现清洁化铸造。
1.5蠕墨铸铁
蠕墨铸铁是在铸铁材料方面介于球墨铸铁与灰铸铁之间的一种材科。
蠕虫状石墨是介于球伏与片状之间的一种过渡型石墨,因而使这种铸铁的材质性能也介于球墨铸铁与灰铸铁之间。
简要地说,蠕墨铸铁具有接近于球墨铸铁的强度、刚性,一定的韧性,良好的耐磨性;
另一方面,它又具有接近于灰铸铁的铸造性能和热传导性能,因此这种铸铁材料愈来愈引起人们的注意,并且巳开始在生产上获得了应用。
它具有独特的性能,在汽车发动机、排气管、玻璃模具、柴油机缸盖、制动零、件刹车盘等方面应用取得了良好的效果。
第二章铸造工艺方案的确定
2.1支座的生产条件、结构及技术要求
●产品生产性质——大批量生产
●零件材质——RuT300
●零件的外型示意图如图2.1所示,支座的零件图如图2.2所示,支座的外形轮廓尺寸为160mm*135mm*100mm,主要壁厚18mm,最大壁厚20mm,为一小型铸件;
铸件除满足几何尺寸精度及材质方面的要求外,无其他特殊技术要求。
图2.1支座外型示意图
图2.2支座零件图
2.2支座结构的铸造工艺性
零件结构的铸造工艺性是指零件的结构应符合铸造生产的要求,易于保证铸件品质,简化铸件工艺过程和降低成本。
审查、分析应考虑如下几个方面:
1.铸件应有合适的壁厚,为了避免浇不到、冷隔等缺陷,铸件不应太薄。
2.铸件结构不应造成严重的收缩阻碍,注意薄壁过渡和圆角铸件薄厚壁的相接拐弯等厚度的壁与壁的各种交接,都应采取逐渐过渡和转变的形式,并应使用较大的圆角相连接,避免因应力集中导致裂纹缺陷。
3.铸件内壁应薄于外壁铸件的内壁和肋等,散热条件较差,应薄于外壁,以使内、外壁能均匀地冷却,减轻内应力和防止裂纹。
4.壁厚力求均匀,减少肥厚部分,防止形成热节。
5.利于补缩和实现顺序凝固。
6.防止铸件翘曲变形。
7.避免浇注位置上有水平的大平面结构。
对于支座的铸造工艺性审查、分析如下:
支座的轮廓尺寸为160mm*135mm*100mm。
砂型铸造条件下该轮廓尺寸允许的最小壁厚查《铸造工艺学》表3-2-1得:
最小允许壁厚为3~4mm。
而设计支座的最小壁厚为10mm。
符合要求。
支座设计壁厚较为均匀,两壁相连初采用了加强肋,可以有效构成热节,不易产生热烈。
2.3造型,造芯方法的选择
支座的轮廓尺寸为160mm*135mm*100mm,铸件尺寸较小,属于中小型零件且要大批量生产。
采用湿型粘土砂造型灵活性大,生产率高,生产周期短,便于组织流水生产,易于实现机械化和自动化,材料成本低,节省烘干设备、燃料、电力等,还可延长砂箱使用寿命。
因此,采用湿型粘土砂机器造型,模样采用金属模是合理的。
在造芯用料及方法选择中,如用粘土砂制作砂芯原料成本较低,但是烘干后容易产生裂纹,容易变形。
在大批量生产的条件下,由于需要提高造芯效率,且常要求砂芯具有高的尺寸精度,此工艺所需的砂芯采用热芯盒法生产砂芯,以增加其强度及保证铸件质量。
选择使用射芯工艺生产砂芯。
采用热芯盒制芯工艺热芯盒法制芯,是用液态固性树脂粘结剂和催化剂制成的一种芯砂,填入加热到一定的芯盒内,贴近芯盒表面的砂芯受热,其粘结剂在很短的时间内硬化。
而且只要砂芯表层有数毫米的硬壳即可自芯取出,中心部分的砂芯利用余热可自行硬化。
2.4浇注位置的确定
铸件的浇注位置是指浇注时铸件在型内所处的状态和位置。
确定浇注位置是铸造工艺设计中重要的环节,关系到铸件的内在质量,铸件的尺寸精度及造型工艺过程的难易程度。
初步对支座对浇注位置的确定有:
方案一如图2.3、方案二图2.4
图2.3浇注位置确定方案一
图2.4浇注位置确定方案二
确定浇注位置应注意以下原则:
1.铸件的重要部分应尽量置于下部
2.重要加工面应朝下或直立状态
3.使铸件的答平面朝下,避免夹砂结疤内缺陷
4.应保证铸件能充满
5.应有利于铸件的补缩
6.避免用吊砂,吊芯或悬臂式砂芯,便于下芯,合箱及检验
对于方案一如图2.3进行综合分析如下:
1.铸件的A面(如图2.3所示)为重要加工面,朝上放置容易产生气孔、非金属夹杂物等缺陷。
2.铸件的重要部分也没能全部置于下部。
对于方案二如图2.4进行综合分析如下:
1.铸件的重要部分全部置于下部,这样置于下部的重要部分可以得到上部金属的静压力作用下凝固并得到补缩,组织致密。
2.铸件的重要加工面A面、B面(如图2.4所示)位于侧立面,比较光洁,产生气孔、非金属夹杂物等缺陷的可能性小。
综合比较,方案二更加科学可行。
2.5分型面的确定
分型面是指两半铸型相互接触的表面。
分型面的优劣在很大程度上影响铸件的尺寸精度、成本和生产率。
初步对支座进行分型有:
方案一如图2.5、方案二图2.6、方案三图2.7
图2.5分型面确定方案一
图2.6分型面确定方案二
图2.7分型面确定方案三
而选择分型面时应注意一下原则:
1.应使铸件全部或大部分置于同一半型内
2.应尽量减少分型面的数目
3.分型面应尽量选用平面
4.便于下芯、合箱和检测
5.不使砂箱过高
6.受力件的分型面的选择不应削弱铸件结构强度
7.注意减轻铸件清理和机械加工量
对方案一如图2.5进行综合分析如下:
1.铸件没有能尽可能的位于同一半型内,这样会因为合箱对准误差使铸件产生偏错。
也有可能因为合箱不严在垂直面上增加铸件尺寸。
2.砂芯不能全部位于下半型内。
3.上箱难于取出模样。
对方案二如图2.6进行综合分析如下:
铸件没有能尽可能的位于同一半型内,这样会因为合箱对准误差使铸件产生偏错。
对方案三如图2.7进行综合分析如下:
此方案较之方案一与方案二更加科学可行。
2.6砂箱中铸件数量及排列方式确定
支座轮廓尺寸为160mm*135mm*100mm,单件质量约为4kg,因此看铸件为小型简单件。
如果一箱一件生产则工艺出品率会较低,如此生产成本较高。
所以采用一箱四件生产。
这样工艺出品率大幅提高,生产成本也大大降低。
初步选取砂箱尺寸由《铸造实用手册》查表1.5-45得:
上箱为450*350*200mm下箱为450*350*200mm
由《铸造实用手册》查表1.5-44得:
a>
20e>
30f>
30
铸件在砂箱中排列最好均匀对称,这样金属液作用于上砂型的抬芯力均匀,也有利于浇注系统安排,在结合已经确定分型面及浇注位置以及砂箱尺寸,基本确定铸件在砂箱内的排列如图2.8所示,其中模样的吃砂量基本确定为:
a1=30a2=40e1=70e2=70f=35
图2.8砂箱中铸件排列示意图
第三章铸造工艺参数及砂芯设计
3.1工艺设计参数确定
铸造工艺设计参数通常是指铸型工艺设计时需要确定的某些数据,这些工艺数据一般都与模样及芯盒尺寸有关,及与铸件的精度有密切关系,同时也与造型、制芯、下芯及合箱的工艺过程有关。
这些工艺数据主要是指加工余量、起模斜度、铸造收缩率、最小铸出孔、型芯头尺寸、铸造圆角等。
工艺参数选取的准确、合适,才能保证铸件尺寸精确,使造型、制芯、下芯及合箱方便,提高生产率,降低成本。
3.1.1铸件尺寸公差
铸件尺寸公差是指铸件公称尺寸的两个允许的极限尺寸之差。
在两个允许极限尺寸之内,铸件可满足机械加工,装配,和使用要求。
支座为砂型铸造机器造型大批量生产,由《铸造工艺设计》查表1-10得:
支座的尺寸公差为CT8~12级,取CT9级。
支座的轮廓尺寸为160mm*135mm*100mm,由《铸造工艺设计》查表1-9得:
支座尺寸公差数值为2.5mm。
3.1.2机械加工余量
机械加工余量是铸件为了保证其加工面尺寸和零件精度,应有加工余量,即在铸件工艺设计时预先增加的,而后在机械加工时又被切去的金属层厚度。
支座为砂型铸造机器造型大批量生产,由《铸造工艺设计》查表1-13得:
支座的加工余量为E~G级,取G级。
支座的轮廓尺寸为160mm*135mm*100mm,由《铸造工艺设计》查表1-12得:
支座加工余量数值为2.2mm,取2mm。
但在分型面及浇注系统设置中,不得已将重要加工面底面朝上放置,这样使其容易产生气孔、非金属夹杂物等缺陷,所以将采取适当加大加工余量的方法使其在加工后不出现缺陷。
将底面的加工余量调整为3mm。
3.1.3铸造收缩率
铸造收缩率又称铸件线收缩率,用模样与铸件的长度差除以模样长度的百分比表示:
ε=[(L1-L2)/L1]*100%
ε—铸造收缩率
L1—模样长度
L2—铸件长度
支座受阻收缩率由《铸造工艺设计》查表1-14得:
受阻收缩率为0.9%
3.1.4起模斜度
为了方便起模,在模样、芯盒的出模方向留有一定斜度,以免损坏砂型或砂芯。
这个斜度,称为起模斜度。
起模斜度应在铸件上没有结构斜度的,垂直于分型面的表面上应用。
初步设计的起模斜度如下:
外型模的A面