钢铁生产过程中的烧结Word格式.docx
《钢铁生产过程中的烧结Word格式.docx》由会员分享,可在线阅读,更多相关《钢铁生产过程中的烧结Word格式.docx(14页珍藏版)》请在冰豆网上搜索。
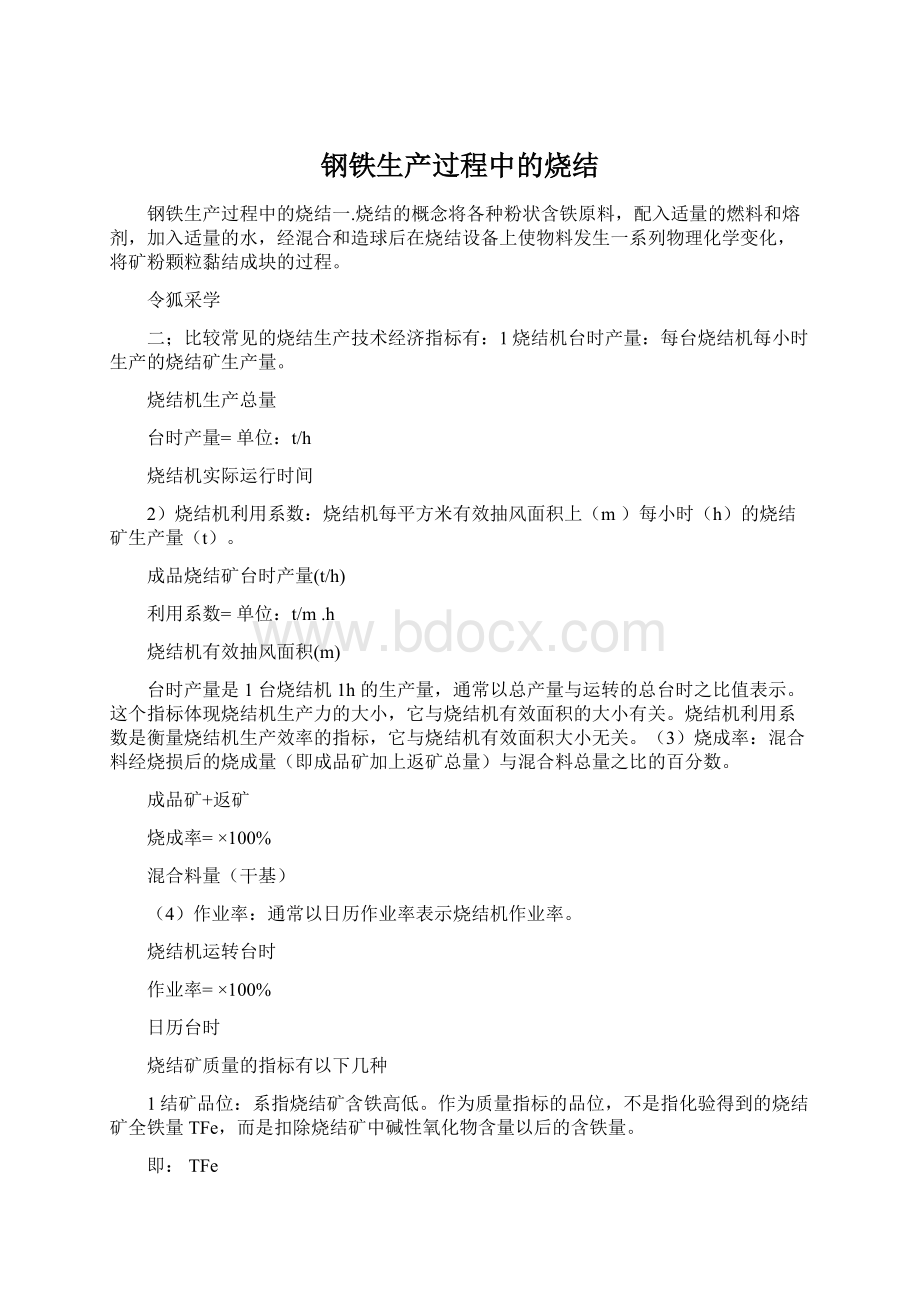
成品矿+返矿
烧成率=×
100%
混合料量(干基)
(4)作业率:
通常以日历作业率表示烧结机作业率。
烧结机运转台时
作业率=×
日历台时
烧结矿质量的指标有以下几种
1结矿品位:
系指烧结矿含铁高低。
作为质量指标的品位,不是指化验得到的烧结矿全铁量TFe,而是扣除烧结矿中碱性氧化物含量以后的含铁量。
即:
TFe
Fe=×
100-(CaO+MgO)
②烧结矿碱度:
一般用R=CaO/SiO表示。
含硫及其它有害杂质含量。
③烧结矿还原性:
生产中常用烧结矿的FeO含量来比较烧结矿的还原性。
④烧结矿转鼓指数;
⑤烧结矿落下强度;
⑥烧结矿筛分指数;
⑦烧结矿热还原粉化率:
指在高温还原条件下的机械强度。
烧结工艺对配料作业有何要求
(1)达到考核指标要求;
如TFe、MgO:
TeO碱度的稳定;
(2)达到高炉对杂质和化合物的要求,如S、P、MgO、Al2O3、SiO2、Na2O等;
(3)满足烧结的烧结性和燃料要求,如各种原料搭配合理,煤粉的用量适当;
(4)根据供料情况合理利用资源,杂矿粉、铁屑、转炉渣配用等。
三.烧结生产的工艺流程目前生产上广泛采用带式抽风烧结机生产烧结矿。
烧结生产的工艺流程如图所示。
主要包括烧结料的准备,配料与混合,烧结和产品处理等工序。
四:
烧结原料的准备
①含铁原料
含铁量较高、粒度<
5mm的矿粉,铁精矿,富矿粉,高炉炉尘,轧钢皮,钢渣等。
一般要求含铁原料品位高,成分稳定,杂质少。
②熔剂
1.溶剂的要求:
熔剂生石灰中有效CaO含量高,杂质少,成分稳定,粒度小于3mm的占85%以上。
生石灰的粒度要求小于3㎜,以利于加水消化和混匀造球。
2.溶剂的作用:
烧结矿中加入溶剂,可使烧结矿溶剂化,把炼铁过程中必须加入的部分溶剂及其在高炉内进行的化学反应移到烧结中进行,。
这也利于强化高炉冶炼,同时也强化了造杂过程,并可降低焦比.另外,能改善原料的烧结性能,强化烧结过程,提高烧结矿的产量,质量.
⑴、生石灰加水后,与水消化呈粒度极细的消石灰,呈胶体颗粒,其平均比表面积达30万㎝2∕g,比消化前的比表面积增大,有利于混合料成球,提高料层透气性,从而提高产量.
⑵、含有Ca(OH)2的烧结料小球有较高的湿容量,因此在烧结过程中热稳定性好,可抵抗干燥过程中的破坏作用,同时可抵抗过湿层的影响。
⑶、生石灰消化成消石灰后,粒度细,分布均匀,反应易于完全,有利于液相生产和提高烧结矿质量。
注:
(一般加水量为0.3-0.35t∕t)
⑷、生石灰消化后放出热量,可提高料温,防止或减轻过湿层。
(生石灰的活性度是指冶金石灰水化的反应速度,即生石灰水化后用4N盐酸中和的毫升数)。
③燃料
主要为焦粉和无烟煤。
对燃料的要求是固定碳含量高,灰分低,挥发分低,含硫低,成分稳定,含水小于10%,粒度小于3mm的占80%以上。
:
燃料粒度大时由于其比表面积小,使燃烧速度变慢,燃烧层厚度增加,透气性降低,垂直烧结速度下降,生产率降低。
同时,燃烧粒度大,烧结料层中燃料周围温度高,还原性气氛强,液相过多而且流动性好,容易形成难还原的薄壁粗孔结构,强度也降低。
反之,在远离燃料颗粒的周围,温度低,烧结不均匀,易出现夹生料,强度差,此外大颗粒燃料在布料时易产生自然偏析,使下层燃料多,温度过高,容易过熔和粘接炉箅;
为保护炉箅,许多工厂不敢烧透,结果返矿增多,质量变坏,抽损增加,恶化除尘及风机转子的工作条件。
由于烧结矿中含有较多的残碳,在冷却段上继续燃烧而降低冷却效果。
燃料粒度过细对烧结也不利,它使燃烧速度过快,燃烧层过窄,温度降低,高温反应来不及进行,导致烧结矿强度变坏,返矿增加,生产率降低。
五:
配料与混合
烧结配料是按烧结矿的质量指标要求和原料成分,将各种原料(含铁料、熔剂、燃料等)按一定的比例配合在一起的过程。
它是整个烧结工艺中的一个重要环节,精心配料是获得优质烧结矿的前提。
适宜的原料配比可以生产出数量足够的性能良好的液相,适宜的燃料用量可以获得强度高、还原性良好的烧结矿。
从而保证高炉顺行,使高炉生产达到高产、优质、低耗。
对配料的基本要求是准确。
即按照计算所确定的配比,连续稳定地配料,把实际下料量的波动值控制在允许的范围内。
当燃料配入量波动0.2%时,就足以引起烧结矿强度与还原性的变化;
当矿粉或熔剂配入量发生变化时,烧结矿的含铁量与碱度即随之变化,都将导致高炉炉温、炉渣碱度的变化,对炉况的稳定、顺行带来不利影响。
为保证烧结矿成分的稳定,生产中当烧结机所需的上料量发生变化时,须按配料比准确计算各种料在每米皮带或单位时间内的下料量;
当料种或原料成分发生变化时,则应按规定的要求,并准确预计烧结矿的化学成分。
六.改善烧结透气的方法加强烧结原料准备
加强原料、燃料、溶剂准备、减少烧结料层各带的气流阻力;
改进烧结设备减少漏风和提高抽风机能力等是改善烧结料层透气性的主要措施。
1)、改进原料粒度和粒度组成。
随着矿石粒度的增加,透气性显著改善,而且这种改善随抽风能力增加而加强。
因此,选用适当粗粒度矿石烧结,以增加物料间的孔隙率,是改善透气性的重要措施。
2)、加强二次混合机的制粒作用,提高烧结混合料粒度,改善烧结混合料粒度组成。
混合料粒度0-3毫米粒度增加,垂直烧结速度降低,烧结生产率降低、烧结矿强度也下降。
研究表明:
烧结料粒度组成,应是0-3毫米粒级含量小于15%,3-5毫米含量小于40%-50%,5-10毫米含量小于30%,大于10毫米的不超过10%。
总之,较好的粒度组成,应尽量减少0-3毫米粒级,及大于10毫米粒级的颗粒,增加3-10毫米粒级的含量。
3)、配加富矿粉、返矿。
在实际生产中,常采用往精矿中配加部分富矿粉和适当增多返矿加入量,以改善料层透气性。
返矿是筛分烧结矿的筛下物(粒度小于5毫米),它是由小颗粒的烧结矿和少部分未烧透的夹生料所组成。
由于返矿粒度较粗,且具有疏松多孔的结构,其颗粒成湿混合料造粒时的核心。
此外,返矿中已含有烧结的低熔点物质,有助于熔融物生成,增多了烧结液相。
所以添加返矿可提高烧结的产量和品质。
4)、适宜的混合料水份。
水分对烧结料层透气性的影响主要取决于原料的成球性、水对气流通过的润滑作用和原料对水份的储存能力。
5)、合理使用添加物。
在生产中往混合物料里加入消石灰、生石灰、等有机粘结性物质,对改善混合料的透气性有良好的作用。
这些微粒添加物是一种表面活性物质,它有提高混合料的亲水性,在许多场合下都具有胶凝性能。
因而混合料的成球性可借此类添加物的作用而大大地提高。
应该指出,向烧结料中配加生石灰和消石灰对烧结过程是有利的,但用量要适宜,如果用量过高除不经济外,还会使料层过分疏松,混合料的容积密度降低,料球强度反面变坏。
七.配料目的:
获得化学成分和物理性质稳定的烧结矿,满足高炉冶炼的要求。
常用的配料方法:
容积配料法和质量配料法。
质量配料法是按原料的质量配料。
比容积法准确,便于实现自动化
容积配料法是基于物料堆积密度不变,原料的质量与体积成比例这一条件进行的。
准确性较差。
比容积法准确,便于实现自动化。
(1)验算法:
该法首先应根据实际生产经验假定配料比,并根据各种物料的水分、烧损、化学成分等项原始数据,计算烧结矿的化学成分,看其是否满足规定的指标的要求。
1、在进行配料计算前,必须已知下列数据:
1)各种原燃料的有关物理性能与化学成分;
2)烧结矿的技术条件;
3)烧结矿的循环量;
4)原料的贮存与供应量;
5)配料设备的能力。
2、步骤为:
(1)确定配料比:
根据烧结矿技术的要求及原料供应计划、化学成分来确定各种原料的配料比。
(2)计算干料量:
干料量(%)=湿料配比X(100-水分)总干料量Σ干料=各种干料量之和
(3)计算残存量(烧成量):
残存量(%)=干料量X(100-烧损) 焦粉残存量(%)=焦粉干料配比X(100-烧损)=焦粉干料比X灰分 总残存量Σ残存量=各种原料残存量之和
(4)计算进入配料中的各种组分:
进入配料中各种原料的含铁量(%):
W(TFe)=某原料含铁量X某原料干料配比。
总含铁量ΣW(TFe)=各原料含铁量之和。
进入配料中各种原料的SiO2含量(%)W(SiO2)=某原料SiO2的质量分数X某原料干料配比。
总SiO2含量ΣW(SiO2)=各原料含SiO2量之和。
进入配料中各种原料的CaO含量(%):
W(CaO)=某原料CaO的质量分数X某原料干料配比。
总CaO含量ΣW(CaO)=各原料含CaO量之和
(5)验算烧结矿R(碱度):
∑W(CaO)R=∑W(SiO2)
(6)计算烧结矿的化学成分:
W(TFe)=各种原料带入的TFe之和÷
总残存量W(SiO2矿)=各种料带入的SiO2之和÷
总残存量W(CaO矿)=各种料带入的CaO之和÷
总残存量若验算的烧结矿碱度和烧结矿成分达到要求,则预定的配料比即为实际配料比。
例题:
已知:
精粉:
配比40%SiO2=6%H2O=8%
印矿:
配比30%SiO2=3.5%H2O=7.0
返矿;
配比10%CaO=9.8SiO2=5.3
白灰:
CaO=75%SiO2=4%
高镁灰:
配比6%CaO=40%SiO2=3.5%
焦粉:
配比5.5%AC=20%H2O=5%
R中限=1.9倍
计算白灰配比?
解:
⑴、计算带入SiO2含量
精粉=40×
6%×
(1-8%)=2.6
印矿=30×
3.5%×
(1-7%)=0.98
返矿=10×
5.3%=0.53
高镁灰=6×
3.5%=0.21
焦粉=5.5×
20%×
50×
(1-5%)=0.52
∑SiO2=4.47
⑵、计算带入CaO含量
40%=2.4
9.8%=0.98
16×
(1-5%)=0.17
∑CaO=2.4+0.17+0.98=3.73
⑶、白灰有效CaO=75-4×
1.9=67.4
⑷、计算白灰配比
(4.47×
1.9-3.73)/67.4=7.07%
答:
……
2、已知60m2某班上料料层为20kg/m,精粉配比为30%,精粉水分为10%,计算当班精粉干消耗量?
(皮带速度=1.34m/s)
(60m2)精粉配料量=20×
30%×
(1-10%)×
1.34m/s×
3600s×
8h÷
1000=208.4
2.在碱度变动时方法
(1)前后照应调整法:
一般来说,从配料到成品化验出结果,
需要两个多小时,机烧冷返矿循环时间更长。
所以,配料调整就是要综合考虑前班烧结矿成分的变化情况,原料情况以及岗位工分析的结果进行调整。
特别是新配比调整后,要根据台车机速、带冷机速、皮带速度以及机返仓位估计一下新配比后的机返何时进入配料,这时,就要再调整一次配比。
量调整法:
配料调整后,当