5W2H管理方法及程序分析和产线平衡培训PPT推荐.ppt
《5W2H管理方法及程序分析和产线平衡培训PPT推荐.ppt》由会员分享,可在线阅读,更多相关《5W2H管理方法及程序分析和产线平衡培训PPT推荐.ppt(78页珍藏版)》请在冰豆网上搜索。
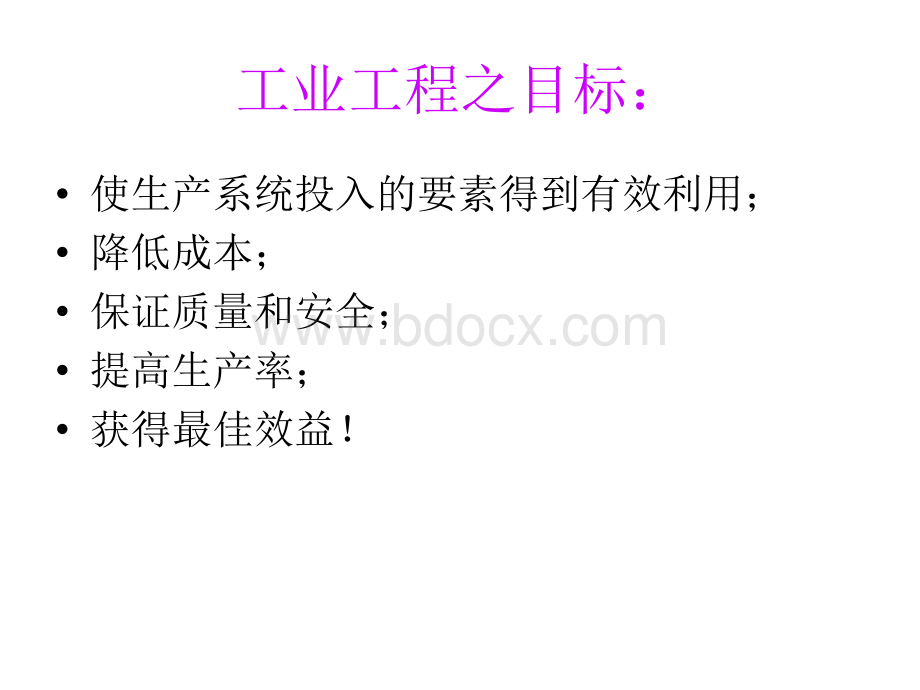
全局和整体意识;
以人为中心的意识现代IE的八大研究方向:
工作研究(基础工业工程)设施规划与物流分析生产计划与控制工程经济质量管理与可靠性技术人机工程学管理信息系统现代制造系统生产的含义:
过程转换O/I产出(O)产品服务生产率人力、设备设施、材料能源、信息等投入(I)系统生产过程中的改善点瓶颈环节或工序成本高昂的工序质量不稳定的工序劳动强度大、劳动条件恶虐的工序容易发生事故的工序主要分析技术类别分析方法内容备注程序分析工艺程序图对整个制造程序或工序的分析流程程序图产品或材料的流程的分析线图、线路图布置与经路分析作业分析人机作业分析闲余能量分析联合作业分析双手作业分析动作分析动素分析影像分析快速摄影动作分析VTR分析动作经济原则分析层次及分析技术某盒子主要工序作业单位印刷动作元素动作单位作业要素压平擦胶水包封面粘合成型入库成品组装手工作业压痕包盖封面拿围边围边过胶包围边封面包围边包底封面校正位置操作程序分析作业分析动作分析程序分析程序分析符号程序分析符号表示作业表示搬运表示检验表示暂存或等待表示受控制的贮存表示同一时间或同一工场由同一人执行作业与检验的工作程序分析程序分析技巧一程序分析技巧一(5W2H)What?
When?
Why?
Who?
Where?
Howtodo?
Howmuch?
程序分析程序分析技巧程序分析技巧二()二()取消(eliminate)合并(combine)重排(rearrange)简化(simplify)程序分析程序分析的五个方面程序分析的五个方面作业分析搬运分析检验分析贮存分析等待分析工艺程序图675帽子钢轴轮子()车身彩盒注塑去水口检查检查入盒检查注塑去水口检查注塑去水口检查装配装帽子流程程序图123145现时方法统计到仪器柜(5M)开仪器柜拿起量规带量规回工作台(5M)调整量规用量规核对工件尺寸带量规回仪器柜(5M)放回量规关仪器柜回工作台(5M)123454(20M)1用量规核对工件尺寸(人型流程程序图)作业分析动作分析方法方法目的目的分析对象分析对象优点优点缺点缺点目目视视动动作作观观察察法法动素分析法人体各部位的活动是否存在浪费和不合理之处?
详尽找出动作所存在的问题。
在固定的作业现场反复实施的持续时间较短的作业,如:
生产线装配作业能用最小的单位分析动作,详尽找出动作存在的问题。
通过观察和分析可以逐步培养出动作意识要理解和熟练掌握18个动素的记号和内容必须经过必要的专业培训。
影影像像动动作作观观察察法法慢速摄影动作分析法容易找出操作者动作和物流的瓶颈之处,大致掌握长时间作业的运行状态。
在固定的作业现场实施的不规则的持续较长时间的作业,如:
站立步行作业协同作业通过摄影,突出人的动作、物流中存在的问题可对持续时间长的作业进行摄影,通过计算摄影张数,记录作业的时间值。
由于胶卷需要冲洗显影,故分析需要时间在某种程度上必须熟悉装置的操作整套装置费用高VTR分析法反复观察作业过程,进行正确的分析,允许多人参与作业改善的讨论适合于摄像的几乎所有类型的作业通过对作业实施过程的摄像,可立即在放像机上再现作业过程,操作简单通过反复摄影可进行详细的分析整套装置的费用高动作分析的种类和特征动素分析序号名称记号代号序号名称记号代号1伸手TE10寻找SH2握取G11发现F3移物TL12选择ST4定位gP13思考PN5装配#A14预置PP6拆卸DA15拿住H7使用UU16迟延UD8放开RL17故延AD9检查()I18休息R动素性质划分有效动素:
伸手、握取、移物、定位、装配、拆卸、使用、放手和检查等9种。
辅助动素:
寻找、发现、选择、思考和预置等5种。
无效动素:
拿住、迟延、故延和休息等4种。
动作经济原则概述生产五要素:
人、机、物、法、环动作三要素:
动作方法、作业现场布置和工夹具与机器动作意识:
(1)明白合理动作与不合理动作的区别;
(2)明确动作错误的原因,判断合理动作;
(3)全身心地投入动作研究,思考合理动作方法、作业配置和工夹具。
生产线平衡分析生产线平衡分析和瓶颈改善和瓶颈改善LINEBALANCING第一节、木桶定律与生产线平衡一、何为木桶定律1.木桶定律一个木桶盛水多少,并不取决于桶壁上最高的那块木板,而恰恰取决于桶壁上最短的那块木板,这一规律我们称之为“木桶定律”。
2.木桶定律的三个推论A.只有桶壁上所有木板都足够高,木桶才能盛满水B.所有木板高出最低木板的部分是没有意义的,而且高出越多,浪费就越大C.提高木桶容量最有效的办法就是设法加高最低木板的高度二、生产线平衡与木桶定律的关系“生产线平衡”与“木桶定律”非常相似:
生产线的最大产能不是取决于作业速度最快的工位,而恰恰取决于作业速度最慢的工位,最快与最慢的差距越大,产能损失就越大。
制造现场,各个车间或小组之间,彼此的管理水平、产能等往往是不等的,企业现场管理的整体水平并不取决于最优秀的车间单位而是取决于最差的车间单位,同理,对一条生产线来言,其产量、效率高低也是如此。
三、生产线平衡的定义及意义1.何为生产线平衡:
生产线平衡是对生产的全部工序进行平均化、均衡化,调整各工序或工位的作业负荷或工作量,使各工序的作业时间尽可能相近或相等,最终消除各种等待浪费现象,达到生产效率最大化。
它是生产流程设计与作业标准化中最重要的方法。
通过平衡生产,可以加深理解“一个流”生产模式及熟悉“单元生产”的编制方法,它是一切新理论与新方法的基础。
2.提高生产线平衡效率的意义缩短每一制品装配时间,增加单位时间的生产量,降低生产成本减少工序间的在制品,减少现场场地的占用减少工程之间的预备时间,缩短生产周期消除人员等待现象,提升员工士气改变传统小批量作业模式,使其达到一个流生产。
可以稳定和提升产品品质提升整体生产线效率和降低生产现场的各种浪费第二节、生产线平衡分析与改善一、平衡分析用语1.节拍(PITCHTIME):
节拍是指在规定时间内完成预定产量,各工序完成单位成品所需的作业时间。
其计算公式:
节拍有效出勤时间生产计划量X(+不良率)例:
每月的工作天数为20天,正常工作时间每班次为480分钟,该企业实行每天2班制,如果该企业的月生产计划量为19200个,不良率为0%,请问该企业的生产节拍是多少?
答:
节拍时间=有效出勤时间/生产计划量X(1+不良率)=480X2X20/19200X(1+0%)=60秒/个2.传送带速度CV:
传送带速度是指流水线的皮带传递速度,一般情况下,采用一定的距离作好标记,然后测定其时间,进而得出流水线传送带的实际速度,计算公式:
CV=间隔标记距离/所耗时间。
采用流水线作业的企业,传送带的速度与作业效率、疲劳程度以及能否完成产量有密切的关系。
理想的传送带速度是恰好能完成预定产量的同时又能减少作业员的身心疲劳。
理想的传送带速度的计算公式:
CV=间隔标记距离/节拍时间,因此在现场生产管理过程中,只要把流水线的皮带速度调成理想的传送带速度即可。
3.瓶颈工时:
指生产线所有工序中所用人均工时最长的工序,通常指一道工序,有时也指几道工序。
3.总瓶颈站工时:
指瓶颈站工时乘以生产线作业人数的总和。
4.周程时间:
是指单个产品从前到后所有工序所费时间的总和。
5.平衡率:
其计算公式=生产线各工序时间总和/(瓶颈工时X人员数)6.平衡损失:
其计算公式=1-平衡率7.平衡损失时间:
其计算公式=(瓶颈工时-工位工时)8.稼动损失时间:
其计算公式=(节拍-瓶颈时间)X总人数9.稼动损失率:
其计算公式=稼动损失时间/(节拍X总人数)X100%,平衡损失时间与稼动损失时间是两个不同的概念,平衡损失时间是瓶颈工时与各工位工时时间差的总和,而稼动损失时间是工序生产节拍与瓶颈工时时间差的总和,它们之间的关系如下图所示:
节拍=33瓶颈时间=29.2此部分是稼动损失时间此部分是平衡损失时间稼动损失时间与平衡损失时间的区别10.瓶颈的(BottleNeck)定义:
阻碍企业流程更大程度增加有效产出或减少库存和费用的环节谓之瓶颈,瓶颈可能是有形的,也可能是无形的。
生产系统的目标是平衡物流,而不是平衡生产能力;
“非瓶颈”资源的充分利用不仅不能提高有效产出,而且还会使库存和搬运增加;
瓶颈环节损失1小时,相当于整个系统损失1小时,而且是无法补救的;
非瓶颈环节上节约1小时,毫无实际意义;
瓶颈制约了生产系统的有效产出和库存;
11.瓶颈的常见表现:
整体进度缓慢,生产效率下降;
出现产品零部件不能配套的现象;
一些工序加班赶货,而另一些则很轻松;
一些工序的半成品堆积过多,而另一些则很少;
个别工序在等材料、设备,其他工序进展正常;
个别生产线流动停止,出现在制品滞留时间过长情况。
12.瓶颈效应:
是指瓶子颈部流量的大小限制了倒水时的水13.瓶颈的不良影响:
A.工序的先后关系,会影响后续工序进度:
B.工序间的平行关系,则会影响产品配套二、平衡改善法则及注意事项1.平衡改善法则-ECRS法则符号名称说明E取消Eliminate对于不合理、多余的动作或工序给予取消C合并Comebine对于无法取消又是必要的,看是否可以合并以达到省时、简化的目的R重排Rearrange经过取消、合并后,可再根据“何人”“何时”“何处”三个提问后进行重排S简化Simplify经过取消、合并、重排后的必要工序,应考虑能否采用最简单的方法或设备替代,以节省人力和时间以上ECRS法则,具体可通过下列图片来说明生产中如何运用改善:
作业时间作業改善工序12345作业时间工序23作业改善压缩分割转移并行作业,增加人员拆解去除作业时间1人作业2人作业工序12345作业时间工序12345作业时间工序12345作业时间工序12345作业改善后合并重排2-1.平衡改善的基本原则和方法:
通过调整作业工序的作业内容来使作业时间相近或减少这一偏差。
A.首先考虑对瓶颈工序进行改善,作业改善方法可参照程序分析、动作分析、工装自动化等工程方法和手段B.将瓶颈工序的作业内容分割给其它工序。
C.合并相关工序,重新排布生产线。
D.分解作业时间较短的工序,把它安排到其它工序中去。
E.增加作业员,只要平衡率提高了,人均产量就提高了,单位成本也随之下降。
2-2.平衡改善的基本原则和方法:
改善耗时长的工程,缩短作业时间A.分割作业,把一部分作业分配到耗时较短的工程B.改善作业,缩短作业时间(如:
活用工具等)C.使作业机械化;
提高机械的效能D.并行作业,增加作业人数E.更换技术水准更高、动作更快的作业人员改善耗时较短的工程A.分割作业,将其分配到其他耗时也短的工程,从而省略原工程B.从耗时长的工程,接过一部分作业内容C.把耗时较短的工程结合起来D.把需要两个人工程,改成一个人就能应付的工程.3.平衡改善过程中应注意事项:
A.需要同样工具和机器的作业要素可分配在同一专用设备工序内B.作业要素相同或前后相近的应尽量分配在同一工序C.不相容的作业尽量不分在同一工序D.必要时可对关键作业,增加操作人数或改用更有效的工具/设备以缩短其作业时间,提高平衡率E.生产线补进新手时,因新手对工作不熟悉,在配置上需特别注意,否则会造成严重的不平衡致使产量大幅下降。
F.采用ECRS法则进行改善时的优先顺序为:
“取消”不必要的动作或工序(第一选择);
“合并”微小动作(次选);
“重排”作业工序或动作(第三选择);
“简化”复杂动作或工序(最后选择)三、平衡改善的实施步骤:
第一步:
明确改善目的和对象:
是否因为生产量变动(增产或减产)而进行的改善是否为了提高生产率、减少作业人员改善对象是一条生产线、某段工序还是整个流程第二步:
了解、分析生产现状及相关人员的工作状况:
如各工位或工序的良品率