稀油集中润滑系统Word文件下载.docx
《稀油集中润滑系统Word文件下载.docx》由会员分享,可在线阅读,更多相关《稀油集中润滑系统Word文件下载.docx(23页珍藏版)》请在冰豆网上搜索。
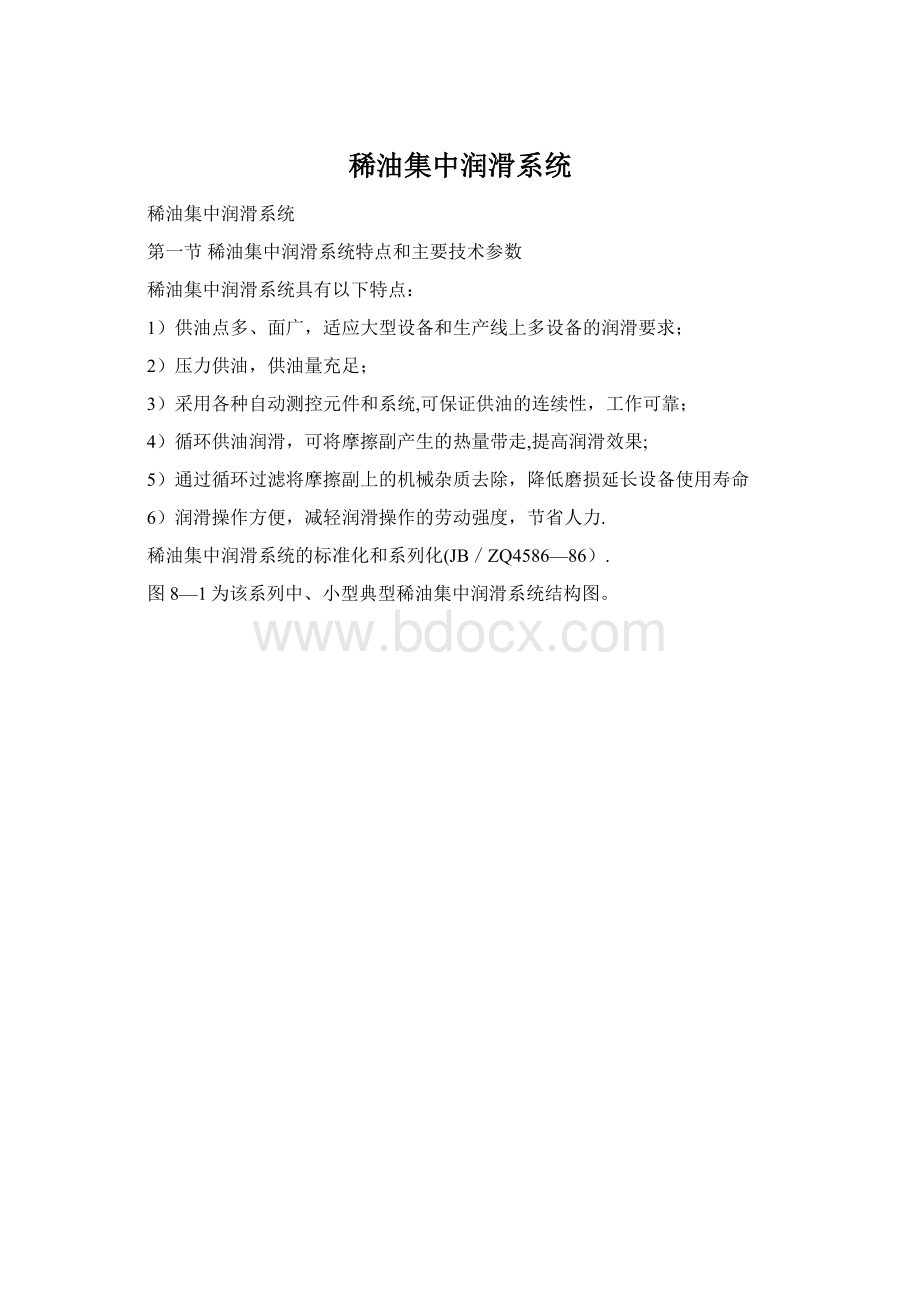
油箱,油泵,过滤系统、冷却器,给油器、各种控制阀、测量仪器仪表、控制器等元件.
一、主要元件的功能和特点
1)油箱
储存润滑油;
杂质沉淀,油水分离;
消除泡沫、冷却、加热;
油箱应具有足够的容积实现功能;
结构:
滤网;
隔板.防尘密封、人孔、泄油口.
油箱应具有足够的刚度,安装泵和一些阀类元件.
对于工作环境恶劣,污染严重的设备,为了保证润滑油中机械杂质充分地沉淀,油水充分地分离,可采用两个油箱交替使用的方法。
2)油泵
动力元件向系统提供一定压力和流量的润滑油.0。
3~0.6MPa低压范围.
动压润滑系统和静压润滑系统:
工作压力,中压或高压.
常用油泵:
有齿轮泵、回转柱塞泵、螺杆泵等.
润滑油泵选择:
现场工作条件,如压力、流量、污垫、噪音、传输介质、价格等因素讲行合理选择.
3)过滤器
用于过滤润滑油中的机械杂质。
过滤器按结构形式:
网式过滤器、线隙式过滤器,纸质过滤器,磁性过滤器.烧结式过滤器、不锈钢纤维过掂器、合成树脂过滤器。
微孔塑料过滤器.
过滤器按过滤精度:
过滤器按过滤精度可分为:
粗过滤器(100m)、普通过滤器(10—100m)、
精过滤器(5—10m)、特精过滤器(1—5m)。
滤油要求:
应具有较高的过滤性能,通油性能,机械强度、耐腐蚀,价格合理等。
4)冷却器
控制润滑油温度。
冷却器有:
列管冷却器:
板式冷却器
润滑油温度低于正常工作温度时,应对润滑油进行加热.加热器主要有电加热器和蒸汽加热器等,加热器通常设在油箱内.采用电加热器应注意最高护皮温度不超过120'
C,以免润滑油过热变质.冬季油温应保持在35—45C之间。
稀油集中润滑系统种类很多,国外如日本、德国,意大利等国均有系列产品,但其基本工作原理是一致的.
二、稀油集中润滑系统工作原理
回转活塞泵供油的稀油集中润滑系统{图8-2)。
1)系统的组成
该系统组成元件有:
油箱。
回转活塞泵系统、过滤器、列管式油冷却器、空气筒、放气阀等。
系统的测量仪器有:
压力计差式压力计、电接触压力计、水银温度计、电阻温度计、电桥温度级、液位控制器、油标、给油指示器油流指示器等。
控制阀类有:
安全阀、截止阀.单向阀等。
还有用于传输油、风,蒸汽,水等的管道、接头.
2)系统工作原理
当电动机3起动时,带动油泵4从油箱内将润滑油吸出,经单向阀6送人圆盘式过滤器8中,过滤后的净油沿输油管流人冷却器15冷却,然后沿输油管道被压送到所润滑的摩擦副上。
油流经摩擦副后,流入具有一定坡度的回油管道返回油箱.
采用双油箱工作方法,以利于杂质沉淀,油水分离、清洗油箱等.
采用两台油泵供油,一台工作,一台备用.
采用—定容量的压力箱.消除囡主机惯性运行时摩擦副缺油丽造成的磨损破坏。
减少油泵供油的压力波动.
在润滑系统中装有不同形式的过滤器,保证润滑油的清静度.
敷设冷却器旁绕行管道.
与润滑点平行设有绕行管路,系统自循环清洗以及设备检修回油。
系统没有各种测控元件。
控制油冷却器的是两个差式压力计。
依靠油温使得热敏元件内的特殊介质的热涨冷缩来控制调节阀的开口度,调节冷却水的流量达到稳定油温的目的.
主机电机与与润滑系统电机采用电路联锁.
第三节稀油集中润滑系统的设计和计算
一,稀油集中润滑系统设计计算的原则
各种设备和元件的性能和规格已经由国家专业部门制订了相应的标准,并由专业厂家生产.
任务:
根据各种生产工艺和相应的机械设备的要求,设计和确定润滑系统性能、规格、数量、形式,以及对必要的组成元件的参数进行设计、计算和元件的选择.
达到:
各种润滑元件及系统能相互平衡、相互适应,以满足生产工艺及机械设备的润滑要求。
确定供油压力和流量是稀油集中润滑系统计算的主要任务.
形成润滑油膜所需要的润滑油量是很少.
用于摩擦副热平衡的润滑油液占总流量的绝大部分.
流量根据所有被润滑摩擦副的发热和散热的条件来计算。
典型摩擦副如轴承、齿轮等的循环润滑流量计算公式列出,
稀油集中润滑系统非动力源,系统压力较低,0。
3~0.6MPa.
主要用于克服润滑油流经各种元件和管路的压力损失,润滑油进入润滑点的压力只要有0。
05MPa即可。
其具体设计计算的步骤是:
1)围绕润滑系统的设计要求,了解对所要润滑机组的概况;
2)搜集润滑系统涉及和计算的必要参数和有关资料;
3)确定润滑方案;
4)根据所要润滑机组的各摩擦副的摩擦功率损耗,计算出所需要润滑油的总消耗量;
5)选定稀油集中润滑系统的形式和数量;
6)选定并计算润滑系统各项设备和元件的形式、规格、数量;
7)选定管道尺寸,画出管路布置图,验算管路的液压损失;
8)写出设计报告和计算书,绘制润滑系统原理图和管路配置图;
9)对全部设计计算进行总结.
二,稀油集中润滑系统流量的计算
1)计算设备摩擦功耗
设备的摩擦损耗:
齿轮、蜗轮等啮合摩擦损耗;
各种轴承和导轨的摩擦损耗;
飞溅搅油损耗等;
摩擦功耗为系统输入功率与系统输出功率之差,用系统的机械效率来表示.
设备的总机械效率,
设备的总机械效率可用下式表示.即:
8—1
其中,齿轮、蜗轮等的啮合传动效率;
各种轴承的传递效率;
齿轮、蜗轮传动时,在封闭式箱体内润滑油飞溅和搅动的传动效率.
关于各种摩擦副的传动效率计算公式和方法,可参阅有关的工程手册.
2)计算摩擦副的总发热量
用热功转换公式计算总的发热量.其表达式为:
千卡/时8—2
式中,总传递效率;
输入功率,单位为千瓦.
当输入功率单位为马力时,热功当量系数为.
3)计算自然散发的热量
摩擦副产生的热量一部分由传动副的壳体散发到空气中,其计算公式为:
千卡时
式中,T0—由传动副的壳体散发到空气中的热量;
k—热传导系数,一般取值为7.5~15(千卡/米2小时C)。
当通风良好,油池中油的循环条件良好,箱体内壁没有妨碍油液循环的筋条,油液循环快,粘度较小时,可取较大值,即取12~15(千卡/米2小时C)。
反之取小值7.5~9(千卡/米2小时C)。
t1—润滑油的温度C,对齿轮传动允许到55C;
对蜗轮传动副允许到60C。
对灌注式齿轮传动允许到70C;
对蜗轮传动副允许到95C。
t2—周围空气的温度C,一般取20~30C。
S-传动系统散热的计算面积(米2),其计算方法为:
S1-为内壁面被油浸着,外面被自然循环空气所冷却的箱壳表面积;
S2—为计算表面的加强筋和凸出表面,以及装在金属底座或机械框架上的箱壳体低面积。
4)计算润滑油的流量
摩擦副产生的热量自然散发外,循环润滑油冷却将热量带走,其流量为:
升/分8—4
式中,Q—润滑油的比热,取0。
4~0.5千卡/公斤C;
润滑油的比重,取公斤米;
-润滑油的温升,一般为8~10C,不超过15C。
t1—循环润滑油吸收了热量后的回油温度C;
t2—循环润滑油进入润滑部位时的温度C;
K1-循环润滑油在啮合处不能全部利用的系数,一般取0。
5~0.8。
多个摩擦副组件:
分别计算每个组件冷却润滑油的需用量,再求其总和确定稀油润滑系统的润滑油的总流量.
三,稀油集中润滑系统压力的计算
进行稀油集中润滑系统压力的计算首先应确定润滑系统的原理图.根据原理图明确元件的组成,压力损失的组成部分.
保证润滑点处的输油管具有0.05~0.06MPa,
1、流体力学原理计算润滑系统中的各项压力损失:
MPa
式中:
P-油泵的实际工作压力,MPa;
P1—在润滑点处,输油管的压力,MPa;
P—润滑系统中的总压力损失,MPa,包括:
8-5
-输油管中各段沿程压力损失之和,MPa;
—输油管中各局部压力损失之和,包括各种阀门、过滤器、冷却器、弯头、三通等元件的局部压力损失,MPa。
2、压力水头来计算各种压力损失
润滑系统的管路分布较复杂,且管路静压力在全部压力损失中占很大的比重,
为了计算方便,常用压力水头来计算各种压力损失,其计算公式为:
8—6
H总—总的扬程,米油柱;
H静—从油泵中心到该系统最高点的垂直高度称为静压高度,米油柱;
H直—直段管路的沿程损失,米油柱;
H吸—油泵吸油管路的扬程,米油柱;
—过滤器、冷却器等的压差,换算成扬程损失,米油柱。
根据上述的扬程可换算成总压力损失:
MPa
其中:
润滑油的比重。
四、稀油集中润滑系统元件的选择
(1)油泵
根据式8-4计算系统所需最大流量Q,并取油泵额定流量Q泵:
油泵的有效功率Ne:
千瓦8—7
电动机功率:
8—8
式中:
油泵总效率,;
m油泵机械效率;
v油泵容积效率。
由上述计算参数,根据油泵标准可选择相应型号的油泵和电动机。
(2)油箱
油箱在实际使用时不应装满,其容量应控制在油箱容积的;
油箱容量根据油泵的流量(升/分)的20~25倍来考虑。
(3)过滤器
选择过滤器应考虑:
根据润滑系统的要求,确定相应过滤器的形式、规格.在满足过滤精度的条件下,使过滤器的通油能力与系统流量相当。
过滤器的通油量与过滤器前后的压力差、油的粘度、油的温度、滤油速度、过滤面积等因素有关。
滤芯的有效过滤面积A为:
,米28-9
油的动力粘度;
—过滤器前后的压力差,Pa;
滤芯材料的单位过滤能力,L/cm2,由实验测定,参见有关资料.
(4)冷却器
冷却器的计算主要是有效冷却面积F的计算,其公式为:
,米28—10
T—热负荷,为了降温必须排出的热量,千卡/时;
c-润滑油比热,一般取0.45~0。
5千卡/公斤C;
润滑油的容重,取公斤米3
t1和t2-润滑油出入冷却器的温度,出口42~47C,入口50~55C;
t3和t4—冷却水出入冷却器的温度,入口20~25C,出口一般大于入口温度4C;
k—总传热系数,千卡/米2时C,当冷却器内油的平均流速为0.2~0.3米/秒,取