玻璃钢废弃物处理方法Word格式.docx
《玻璃钢废弃物处理方法Word格式.docx》由会员分享,可在线阅读,更多相关《玻璃钢废弃物处理方法Word格式.docx(19页珍藏版)》请在冰豆网上搜索。
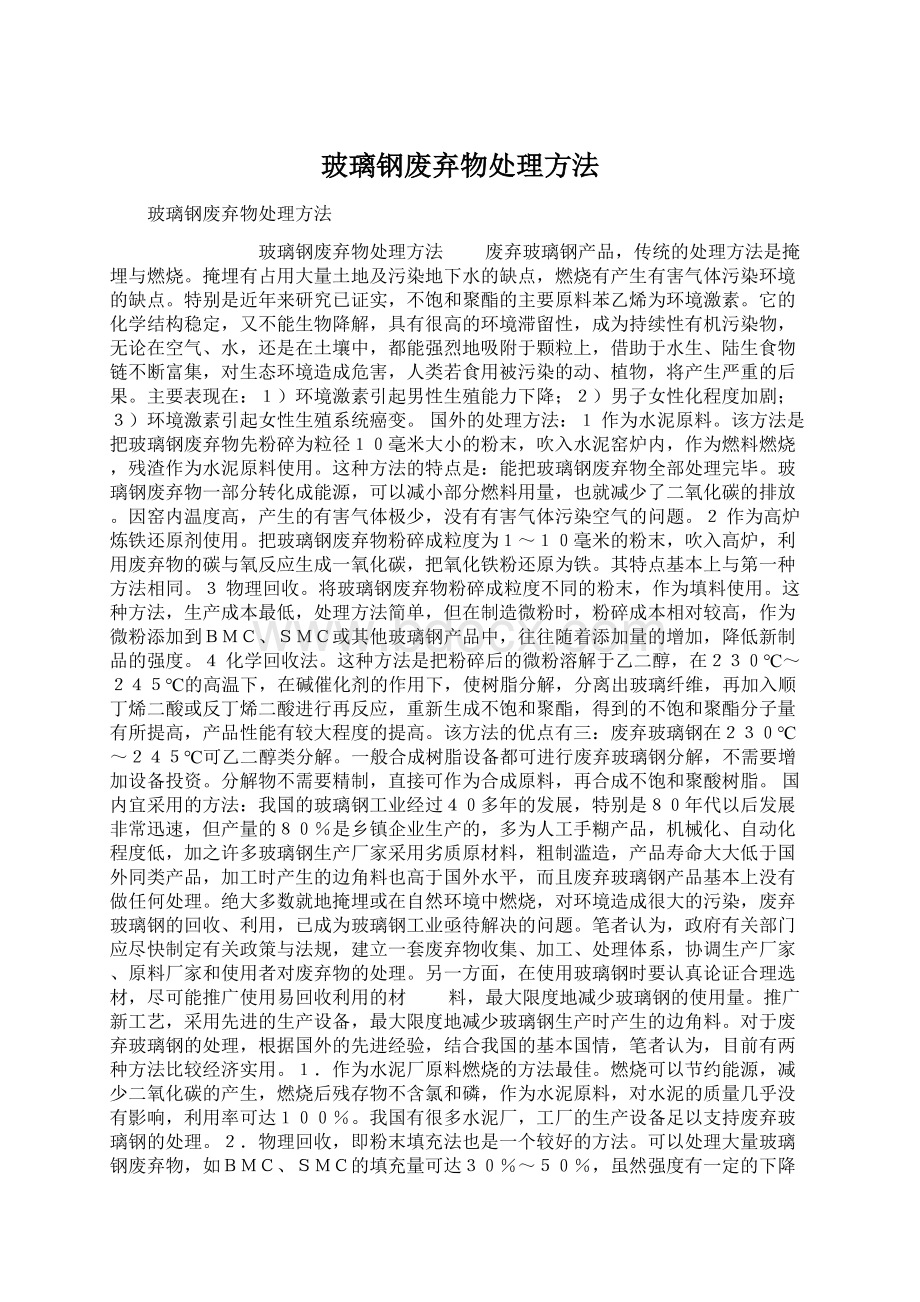
玻璃钢废弃物一部分转化成能源,可以减小部分燃料用量,也就减少了二氧化碳的排放。
因窑内温度高,产生的有害气体极少,没有有害气体污染空气的问题。
2作为高炉炼铁还原剂使用。
把玻璃钢废弃物粉碎成粒度为1~10毫米的粉末,吹入高炉,利用废弃物的碳与氧反应生成一氧化碳,把氧化铁粉还原为铁。
其特点基本上与第一种方法相同。
3物理回收。
将玻璃钢废弃物粉碎成粒度不同的粉末,作为填料使用。
这种方法,生产成本最低,处理方法简单,但在制造微粉时,粉碎成本相对较高,作为微粉添加到BMC、SMC或其他玻璃钢产品中,往往随着添加量的增加,降低新制品的强度。
4化学回收法。
这种方法是把粉碎后的微粉溶解于乙二醇,在230℃~245℃的高温下,在碱催化剂的作用下,使树脂分解,分离出玻璃纤维,再加入顺丁烯二酸或反丁烯二酸进行再反应,重新生成不饱和聚酯,得到的不饱和聚酯分子量有所提高,产品性能有较大程度的提高。
该方法的优点有三:
废弃玻璃钢在230℃~245℃可乙二醇类分解。
一般合成树脂设备都可进行废弃玻璃钢分解,不需要增加设备投资。
分解物不需要精制,直接可作为合成原料,再合成不饱和聚酸树脂。
国内宜采用的方法:
我国的玻璃钢工业经过40多年的发展,特别是80年代以后发展非常迅速,但产量的80%是乡镇企业生产的,多为人工手糊产品,机械化、自动化程度低,加之许多玻璃钢生产厂家采用劣质原材料,粗制滥造,产品寿命大大低于国外同类产品,加工时产生的边角料也高于国外水平,而且废弃玻璃钢产品基本上没有做任何处理。
绝大多数就地掩埋或在自然环境中燃烧,对环境造成很大的污染,废弃玻璃钢的回收、利用,已成为玻璃钢工业亟待解决的问题。
笔者认为,政府有关部门应尽快制定有关政策与法规,建立一套废弃物收集、加工、处理体系,协调生产厂家、原料厂家和使用者对废弃物的处理。
另一方面,在使用玻璃钢时要认真论证合理选材,尽可能推广使用易回收利用的材 料,最大限度地减少玻璃钢的使用量。
推广新工艺,采用先进的生产设备,最大限度地减少玻璃钢生产时产生的边角料。
对于废弃玻璃钢的处理,根据国外的先进经验,结合我国的基本国情,笔者认为,目前有两种方法比较经济实用。
1.作为水泥厂原料燃烧的方法最佳。
燃烧可以节约能源,减少二氧化碳的产生,燃烧后残存物不含氯和磷,作为水泥原料,对水泥的质量几乎没有影响,利用率可达100%。
我国有很多水泥厂,工厂的生产设备足以支持废弃玻璃钢的处理。
2.物理回收,即粉末填充法也是一个较好的方法。
可以处理大量玻璃钢废弃物,如BMC、SMC的填充量可达30%~50%,虽然强度有一定的下降,但可以满足一般使用要求,同时还可以使制品的比量下降,制得轻质产品。
化学再生的方法虽然处理最为完美,能将废弃玻璃钢分解成原料再使用,但成本太高,我国的经济还不太发达,资金有限,目前还不能大规模采用这种方法,但随着经济的发展与科学技术的进步,化学处理方法将是最好的方法。
玻璃钢复合材料的刚度、层间强度、弹性模量的特点 玻璃钢/复合材料的力学性能具有明显的方向性,玻璃钢等人造的复合材料还可以人为地变化纤维方向和数量来达到某种特定的强度要求。
例如,我们采用\\玻璃布制造的玻璃钢,其经向和纬向强度几乎是相等的。
但在其它方向上强度则较低,如在45°
方向上强度比经、纬向强度1/2还要低。
值得注意的是人们常常有一种误解,认为资料中所列举的强度数据就是实际构件的强度数据。
其实这两者截然不同,差异较大。
例如手糊聚酯玻璃钢板,小试件抗伸强度可达200-250MPa,而在同样原材料的3m*9m的大型构件上取下一块试样,它的抗伸强度只有100MPa。
这是因为两者的制造操作条件不同,大块板工艺条件不如小试件那样理想。
因此,在采用各类资料、书籍所给出的强度数据时,一定要注意你所设计的构件工艺制造条件和一般小试件之间 的差异,否则将会出现问题。
此外,还要注意玻璃钢/复合材料层间强度和弹性模量低的特点。
层间是薄弱环节,因为层间没有增强纤维,所以它的层间剪切和层间抗伸强度都较低,充其量也只是树脂本身的强度。
这个特点告诫人们在设计和制造玻璃钢制品时,除工艺制造时尽量使布层间粘牢外,设计上应使层间应力降到最低,防止层间破坏情况出现。
例如,306#聚酯玻璃钢的层间剪切强度只有层间抗伸强度还要低些。
玻璃钢的弹性模量比木材大2倍,但比一般结构钢小10倍。
因此,在玻璃钢结构中,常感刚性不足,会出现较大的变形。
为了改善这一缺点,可采用夹层结构,亦可通过应用高模量纤维或中空纤维等来解决。
可以看成:
FRP刚性>优质木材≈竹材。
比强度:
即单位密度下的拉伸强度,也就是材料的抗拉强度与密度之比,用以说明其轻质高强的程度。
玻璃钢密度介于~之间,只有普通碳钢的1/4~1/5比轻金属铝还要轻1/3左右,而机械强度却很高,某些方面甚至能接近普通碳钢的水平。
例如某些环氧玻璃钢,其拉伸、弯曲和压缩强复均达到400MPa以上。
按比强度计算,玻璃钢不仅大大超过普通碳钢,而且可达到和超过某些特殊合金钢的水平。
玻璃钢接触成型工艺之--手糊成型工艺 手糊成型的工艺流程如下:
生产准备 场地手糊成型工作场地的大小,要根据产品大小和日产量决定,场地要求清洁、干燥、通风良好,空气温度应保持在15~35℃之间,后加工整修段,要设有抽风除尘和喷水装置。
模具准备准备工作包括清理、组装及涂脱模剂等。
树脂胶液配制配制时,要注意两个问题:
①防止胶液中混入气泡;
②配胶量不能过多,每次配量要保证在树脂凝胶前用完。
增强材料准备增强材料的种类和规格按设计要求选择。
糊制与固化 铺层糊制手工铺层糊制分湿法和干法两种:
①干法铺层用预浸布为原料,先将预学好料按样板裁剪成坏料,铺层时加热软化,然后再一层一层地紧贴在模具上,并注意排除层间气泡,使密实。
此法多用于热压罐和袋压成型。
②湿法铺层直接在模具上将增强材料浸胶,一层一层地紧贴在模具上,扣除气泡,使之密实。
一般手糊工艺多用此法铺层。
湿法铺层又分为胶衣层糊制和结构层糊制。
手糊工具手糊工具对保证产品质量影响很大。
有羊毛辊、猪鬃辊、螺旋辊及电锯、电钻、打磨抛光机等。
固化制品固化分硬化和熟化两个阶段:
从凝胶到三角化一般要24h,此时固化度达50%~70%,可以脱模,脱后在自然环境条件下固化1~2周才能使制品具有力学强度,称熟化,其固化度达85%以上。
加热可促进熟化过程,对聚酯玻璃钢,80℃加热3h,对环氧玻璃钢,后固化温度可控制在150℃以内。
加热固化方法很多,中小型制品可在固化炉内加热固化,大型制品可采用模内加热或红外线加热。
脱模和修整 脱模脱模要保证制品不受损伤。
脱模方法有如下几种:
①顶出脱模在模具上预埋顶出装置,脱模时转动螺杆,将制品顶出。
②压力脱模模具上留有压缩空气或水入口,脱模时将压缩空气或水压入模具和制品之间,同时用木锤和橡胶锤敲打,使制品和模具分离。
③大型制品脱模可借助千斤顶、吊车和硬木楔等工具。
④复杂制品可采用手工脱模方法先在模具上糊制二三层玻璃钢,待其固化后从模具上剥离,然后再放在模具上继续糊制到设计厚度,固化后很容易从模具上脱下来。
修整修整分两种:
一种是尺寸修整,另一种缺陷修补。
①尺寸修整成型后的制品,按设计尺寸切去超出多余部分;
②缺陷修补包括穿孔修补,气泡、裂缝修补,破孔补强等。
玻璃钢生产工艺--接触低压成型工艺 接触低压成型工艺的特点是以手工铺放增强材料,浸清树脂,或用简单的工具辅助铺放增强材料和树脂。
接触低压成型工艺的另一特点,是成型过程中不需要施加成型压力,或者只施加较低成型压力。
接触低压成型工艺过程,是先将材料在阴模、阳模或对模上制成设计形状,再通过加热或常温固化,脱模后再经过辅助加工而获得制品。
属于这类成型工艺的有手糊成型、喷射成型、袋压成型、树脂传递模塑成型、热压罐成型和热膨胀模塑成型等。
其中前两种为接触成型。
接触低压成型工艺中,手糊成型工艺是聚合物基复合材料生产中最先发明的,适用范围最广,其它方法都是手糊成型工艺的发展和改进。
接触成型工艺的最大优点是设备简单,适应性广,投资少,见效快。
根据近年来的统计,接触低压成型工艺在世界各国复合材料工业生产中,仍占有很大比例,如美国占35%,西欧占25%,日本占42%,中国占75%。
这说明了接触低压成型工艺在复合材料工业生产中的重要性和不可替代性,它是一种永不衰落的工艺方法。
但其最大缺点是生产效率低、劳动强度大、产品重复性差等。
1、原材料 接触低压成型的原材料有增强材料、树脂和辅助材料等。
增强材料 接触成型对增强材料的要求:
①增强材料易于被树脂浸透;
②有足够的形变性,能满足制品复杂形状的成型要求;
③气泡容易扣除;
④能够满足制品使用条件的物理和化学性能要求;
⑤价格合理,来源丰富。
用于接触成型的增强材料有玻璃纤维及其织物,碳纤维及其织物,芳纶纤维及其织物等。
基体材料 接触低压成型工艺对基体材料的要求:
①在手糊条件下易浸透纤维增强材料,易排除气泡,与纤维粘接力强;
②在室温条件下能凝胶,固化,而且要求收缩小,挥发物少;
③粘度适宜:
一般为~·
s,不能产生流胶现象;
④无毒或低毒;
⑤价格合理,来源有保证。
生产中常用的树脂有:
不饱和聚酯树脂,环氧树脂,有进也用酚醛树脂,双马来酰亚胺树脂,聚酰亚胺树脂等。
几种接触成型工艺对树脂的性能要求:
成型方法对树脂性能要求
胶衣制作1、成型时不流淌,易消泡2、色调均匀,不浮色 3、固化快,不产生皱纹,与铺层树脂粘接性好手糊成型1、浸渍性好,易浸透纤维,易排除气泡2、铺敷后固化快,放热少、收缩小3、易挥发物少,制品表面不发粘4、层间粘接性好 喷射成型1、保证手糊成型的各项要求2、触变性恢复更早3、温度对树脂粘度影响小 4、树脂适用期要长,加入促进剂后,粘度不应增大袋压成型1、浸润性好,易浸透纤维,易排出气泡2、固化快,固化放热量要小3、不易流胶,层间粘接力强 辅助材料 接触成型工艺中的辅助材料,主要是指填料和色料两类,而固化剂、稀释剂、增韧剂等,归属于树脂基体体系。
2、模具及脱模剂模具 模具是各种接触成型工艺中的主要设备。
模具的好坏,直接影响产品的质量和成本,必须精心设计制造。
设计模具时,必须综合考虑以下要求:
①满足产品设计的精度要求,模具尺寸精确、表面光滑;
②要有足够的强度和刚度;
③脱模方便;
④有足够的热稳定性;
⑤重量轻、材料来源充分及造价低。
模具构造接触成型模具分为:
阴模、阳模和对模三种,不论是哪种模具,都可以根据尺寸大小,成型要求,设计成整体或拼装模。
模具材料造反模具材料时,应满足以下要求:
①能够满足制品的尺寸精度,外观质量及使用寿命要求;
②模具材料要有足够的强度和刚度,保证模具在使用过程中不易变形和损坏;
③不受树脂侵蚀,不影响树脂固化;
④耐热性好,制品固化和加热固化时,模具不变形;
⑤容易制造,容易脱模;
⑥昼减轻模具重量,