基于UG的塑料水杯模具具设计许晓涛Word格式文档下载.docx
《基于UG的塑料水杯模具具设计许晓涛Word格式文档下载.docx》由会员分享,可在线阅读,更多相关《基于UG的塑料水杯模具具设计许晓涛Word格式文档下载.docx(15页珍藏版)》请在冰豆网上搜索。
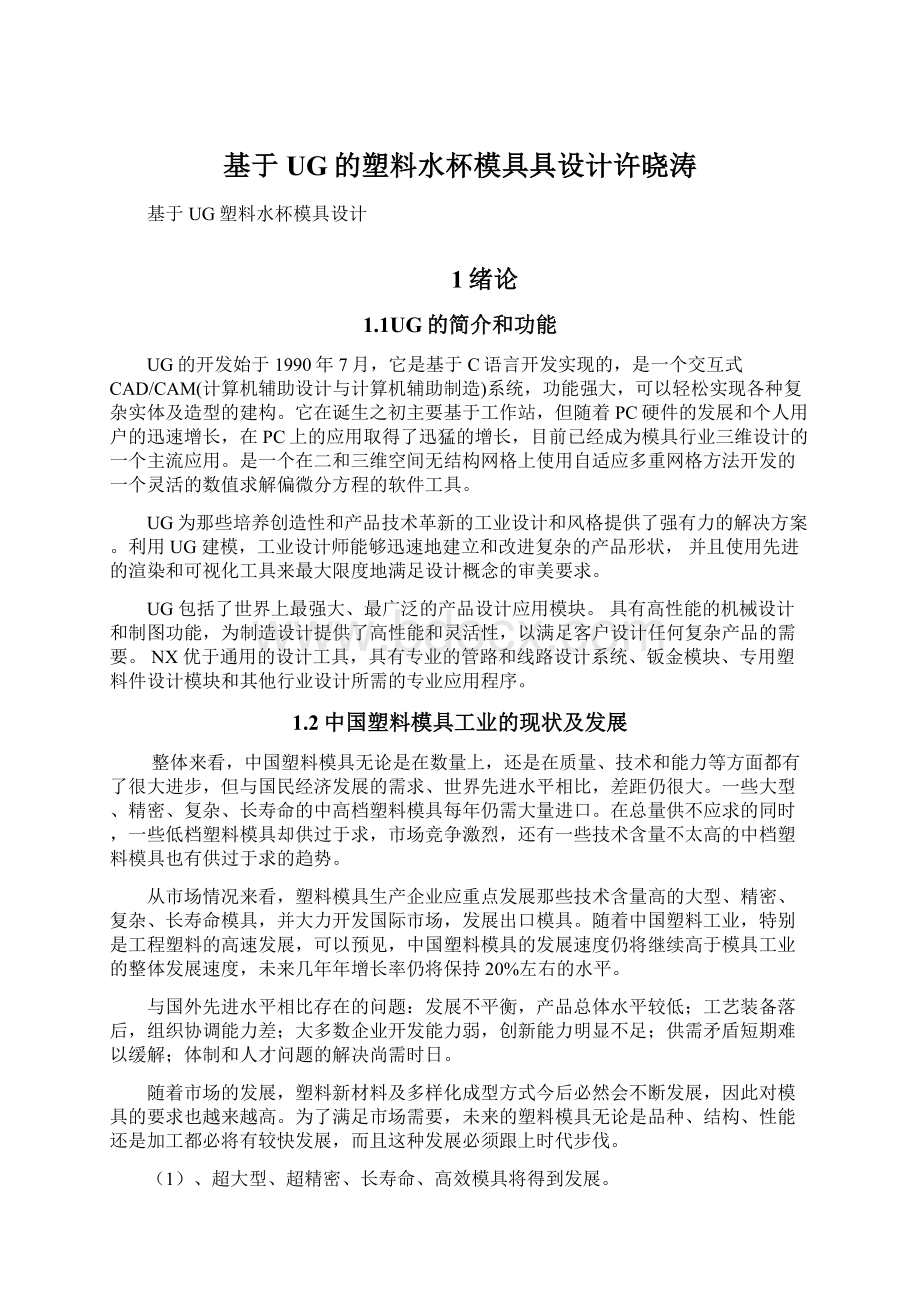
与国外先进水平相比存在的问题:
发展不平衡,产品总体水平较低;
工艺装备落后,组织协调能力差;
大多数企业开发能力弱,创新能力明显不足;
供需矛盾短期难以缓解;
体制和人才问题的解决尚需时日。
随着市场的发展,塑料新材料及多样化成型方式今后必然会不断发展,因此对模具的要求也越来越高。
为了满足市场需要,未来的塑料模具无论是品种、结构、性能还是加工都必将有较快发展,而且这种发展必须跟上时代步伐。
(1)、超大型、超精密、长寿命、高效模具将得到发展。
(2)多种材质、多种颜色、多层多腔、多种成型方法一体化的模具将得到发展。
(3)为各种快速经济模具,特别是与快速成型技术相结合的RP/RT技术将得到快速发展。
(4)模具设计、加工及各种管理将向数字化、信息化方向发展CAD/CAE/CAM/CAPP及PDM/PLM/ERP等将向智慧化、集成化和网络化方向发展
(5)更高速、更高精度、更加智慧化的各种模具加工设备将进一步得到发展和推广应用。
(6)更高性能及满足特殊用途的模具新材料将会不断发展,随之将产生一些特殊的和更为先进的加工方法。
(7)各种模具型腔表面处理技术,如涂覆、修补、研磨和抛光等新工艺也会不断得到发展。
(8)逆向工程、并行工程、复合加工乃至虚拟技术将进一步得到发展。
(9)热流道技术将会迅速发展,气辅和其它注射成型工艺及模具也将会有所发展。
(10)模具标准化程度将不断提高。
(11)在可持续发展和绿色产品被日益重视的今天,“绿色模具”的概念已逐渐被提到议事日程上来。
即,今后的模具,从结构设计、原材料选用、制造工艺及模具修复和报废,以及模具的回收利用等方面,都将越来越考虑其节约资源、重复使用、利于环保,以及可持续发展这一趋向。
2.塑料水杯的工艺分析
2.1塑件的工艺性分析
水杯是是我们日常生活所必须的用品,是装水的良好用具。
其产品主要通过注塑成型制造,本次课题为水杯,产品图如下
2.2塑件的材料选择
根据水杯的工作环境及作用,确定选用材料为聚苯乙烯树脂
聚苯乙烯树脂(ps)密度为1.05g/cm3,,成型收缩率:
0.6-0.8%,成型温度:
170-250℃
PS的性能
a、机械性能:
强度高、耐疲劳性、尺寸稳定、蠕变也小(高温条件下也极少有变化);
b、耐热老化性:
增强后的UL温度指数达120~140℃(户外长期老化性也很好);
c、耐溶剂性:
无应力开裂;
d、对水稳定性:
遇水易分解(高温、高湿环境下使用需谨慎);
e、电气性能:
1、绝缘性能:
优良(潮湿、高温也能保持电性能稳定,是制造电子、电气零件的理想材料);
2、介电系数:
3.0-3.2;
3、耐电弧性:
120s
f、成型加工性:
普通设备注塑或挤塑。
由于结晶速度快,流动性好,模具温度也比其他工程塑料要求低。
在加工薄壁制件时,仅需几秒钟,对大部件也只要40-60s即可。
此外PS成本低廉,符合需求生产量大的的要求。
3.模具的设计
前述已知,该模具要应用注射模加工。
根据对塑料水杯零件图的分析,可采用中小型模架标准(GB/T.12556.1—90)中派生组合类型的模架标准,它是以点浇口和多分型面为主的结构形式,其代号取P。
派生组合中,动、定模座板的连接方式,(如采用螺钉、定距拉杆或定距拉板等)有承制单位自定。
(模具中各种零部件具体尺寸要求可见模具装配图或零件图标注)一般注射模可由以下几个部分组成:
浇注系统、导向机构、脱模机构、侧向分型机构与抽芯机构、其它零件。
对该水杯零件注射模具的基本设计:
3.1塑件的体积分析
塑件在UG中通过分析塑件的体积为:
28.33cm3
3.2塑件的质量分析
PS的密度为1.05g/cm3,即可得出该塑件制品的质量为29.7g。
3.3模具成型零部件的设计与计算
成型零件工作尺寸是指成型零件上直接用来构成塑件的尺寸,主要有型腔和型芯的径向尺寸(包括矩形和异行零件的长和宽),型腔的深度尺寸和型芯的高度尺寸,型芯和型芯之间的位置尺寸等。
任何塑件制件都有一定的几何形状和尺寸的要求,如在使用中有配合要求的尺寸,则精度要求较高。
在模具设计时,应根据塑件的尺寸及精度等级确定模具成型零件的工作尺寸及精度等级。
影响塑件尺寸精度的因素相当复杂,这些影响因素应作为确定成型零件工作尺寸的依据
3.4凸凹模的计算
凸凹凸模亦称型芯,是成型塑件内表面的零件,成型其主体部分内表面的零件称为主型芯或凸模,而成型其他小孔的型芯称为小型芯或成型杆,成型塑件上内螺纹的称为螺纹型芯。
凹模亦称型腔,是成型塑件外表面的主要零件,其中成型塑件上外螺纹的称螺纹型环。
凹、凸模按结构不同可分为整体式和组合式。
所谓成型零件的工作尺寸是指成型零件上直接构成型腔腔体的部位的尺寸,其直接对应塑件的形状与尺寸。
鉴于影响塑件尺寸精度的因素多且复杂,塑件本身精度也难以达到高精度,为了计算简便,规定塑件的工差按单向极限制,制品外轮廓尺寸公差取负值“-△”,制品叫做腔尺寸公差取正值“+△”,若制品上原有公差的标注方法与上不符,则应
按以上规定进行转换。
而制品孔中心距尺寸公差按对称分布原则计算,即取。
模具制造工差
实践证明,模具制造公差可取塑件公差的~,即δz=(,而且按成型加工过程中的增减趋向取“+”、“-”符号,型腔尺寸不断增大,则取“+δz”,型芯尺寸不断减小则取“-δz”,中心距尺寸取“”。
现取。
模具的磨损量
实践证明,对于一般的中小型塑件,
最大磨损量可取塑件公差的,对于大型塑件则取以下。
另外对于型腔底面(或型芯端面),因为脱模方向垂直,故磨损量δc=0。
(2)塑件的收缩率
塑件成型后的收缩率与多种因素有关,通常按平均收缩率计算
K==%=2%=0.02
模具在分型面上的合模间隙.
由于注塑压力及模具分型面平面度的影响,会导致动模、定模注塑时存在着一定的间隙。
一般当模具分型的平面度较高、表面粗糙度较低时,塑件产生的飞边也小。
飞边厚度一般应小于是0.02~0.1mm6。
凹模有关的尺寸计算
径向尺寸:
L1=[(1+K)Ls1-(3/4)△]0+&=[1.02×
102-(3/4)×
0.46]00.46×
1/6+103.69500.08mm
L2=[(1+K)Ls2-(3/4)△]0+δ=[1.02×
81-(3/4)×
0.22]00.22×
1/6=82.45500.04mm
深度尺寸:
H1=[(1+K)Hs1-(2/3)△]0+δ=[1.02×
61-(2/3)×
1/6=62.0700.04mm
凸模有关的尺寸计算
径向尺寸:
L1=[(1+K)Ls1-(3/4)△]0+δ=[1.02×
78-(3/4)×
0.18]0-0.18×
1/6×
79.6950-0.03mm
高度尺寸:
h=[(1+K)hs-(2/3)△]0-δ=[1.02×
58.5+(2/3)×
0.28]00.22×
1/6=59.8590-0.05mm
模具型芯位置尺寸计算:
C=(1+k)Cs±
δ/2=1.02×
140±
(0.5×
1/5)/2=145.8±
0.05mm
3.5型腔侧壁厚度和底板的计算
该塑件模具型腔壁结构为组合式矩形侧壁,型腔壁厚为29.5mm,厚度为87mm
3.6型腔数目
该塑件为中批量生产,同时考虑到塑件精度要求,模具结构尺寸的大小关系,以及各种成本费用的关系,初步定位一模两腔的结构形式。
型腔排列形式的确定,由于该设计采用的是一模两腔塑件放置在中央型腔数目
3.7冷却及加热机构
冷却及加热机构主要包括冷却水嘴、水管通道、加热板等。
主要是为了调节模具的温度,以保证塑料件的质量。
加热系统主要应用于熔融粘度高,流动性差的塑料。
一般注射到模具内的塑料温度为200℃左右,而塑料固化后从模具型腔中取出时其温度在60℃以下。
热塑性塑料在注射成型后,有些需要对模具进行有效的冷却,使熔融塑料的热量尽量快地传给模具,以便使塑料可靠冷却定型并可迅速脱模,提高塑件定型质量和生产效率。
此模具不需要冷却及加热机构,虽然PC的流动性较一般,但由于塑件较小,液体充满型腔比较快,而且散热比较快,所以可以满足塑件的成型需要。
4模具结构
4.1浇注系统的设计
注系统是指注塑模中从主流道始端到型腔之间的熔体进料通道,浇注系统可分为普通流道浇注系统和无流道凝料浇注系统两类,本设计中采用普通点浇口浇注系统。
正确设计浇注系统对获得优质的塑料制品极为重要。
浇注系统组成
普通流道浇注系统的组成一般包括以下几个部分
1-主浇道2-第一分浇道3-第二分浇道4-第三分浇道5-浇口6-型腔7-冷料穴
浇注系统的设计
4.2主流道的设计
(1)所选用HTF
100XB型注塑剂喷嘴有关尺寸如下:
喷嘴前段孔径d0=3.5mm
喷嘴圆弧半径R0=12mm
为了使凝料能够顺利拔出,主流道的小段直径d应稍大于喷嘴直径
d=d0+(0.5~1)=4mm
主流道设计成圆锥形,其锥角@通常为2~4∘,过大的锥角会才产生湍流或涡流,卷入空气,过小的锥角使凝料脱模困难,还会使冲模时熔体的流动阻力过大,此处的锥角选用2∘,主流道球面半径比喷嘴球面半径大1~2mm。
这里取主流道球面半径R20mm,经测量主流道长度L取15mm。
,①主流道长度:
L=38mm
②主流道小端直径:
d=d0+(0.5~1)mm,此处取1mm,d0为注塑机喷嘴口直径2mm。
则:
d=3mm,
③主流道大端直径:
D=d+2Ltanα≈6.98mm,此处取7mm,式中α为主流道的角度,此处取3°
。
D=7mm,
④主流小端对接处设计成半球形凹坑,其半径:
SR=SR0+(1~2)mm,此处取1mm,SR0为注塑机喷嘴球半径10mm,则:
SR=11mm
⑤主流道大端圆角:
主流道大端设计成圆角过渡可以减小熔体流动阻力。
半径r一般取1~3mm,此处取1mm,则:
R=1mm