铸造铜及铜合金的熔炼Word文档格式.docx
《铸造铜及铜合金的熔炼Word文档格式.docx》由会员分享,可在线阅读,更多相关《铸造铜及铜合金的熔炼Word文档格式.docx(16页珍藏版)》请在冰豆网上搜索。
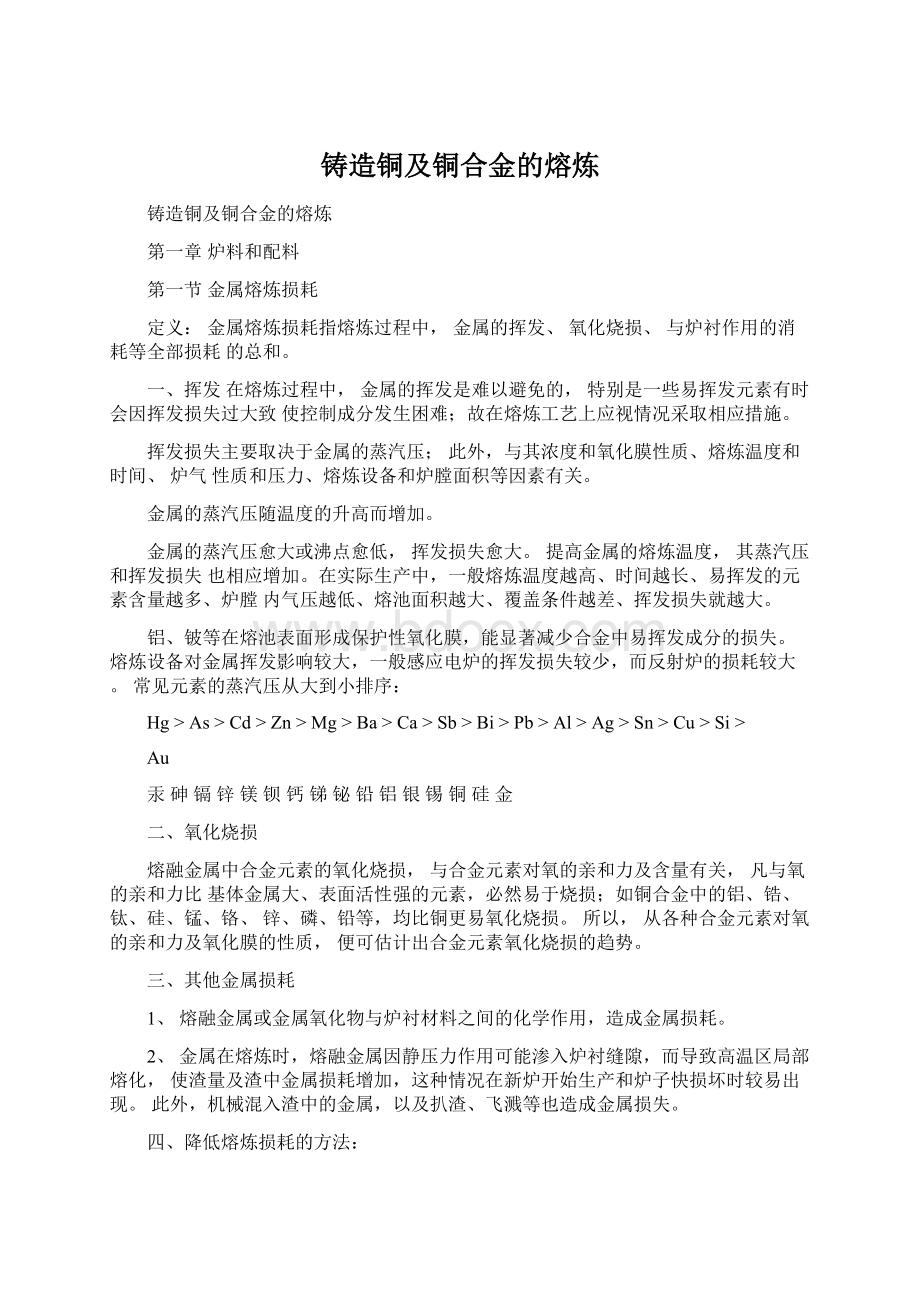
Mg>
Ba>
Ca>
Sb>
Bi>
Pb>
Al>
Ag>
Sn>
Cu>
Si>
Au
汞砷镉锌镁钡钙锑铋铅铝银锡铜硅金
二、氧化烧损
熔融金属中合金元素的氧化烧损,与合金元素对氧的亲和力及含量有关,凡与氧的亲和力比基体金属大、表面活性强的元素,必然易于烧损;
如铜合金中的铝、锆、钛、硅、锰、铬、锌、磷、铅等,均比铜更易氧化烧损。
所以,从各种合金元素对氧的亲和力及氧化膜的性质,便可估计出合金元素氧化烧损的趋势。
三、其他金属损耗
1、熔融金属或金属氧化物与炉衬材料之间的化学作用,造成金属损耗。
2、金属在熔炼时,熔融金属因静压力作用可能渗入炉衬缝隙,而导致高温区局部熔化,使渣量及渣中金属损耗增加,这种情况在新炉开始生产和炉子快损坏时较易出现。
此外,机械混入渣中的金属,以及扒渣、飞溅等也造成金属损失。
四、降低熔炼损耗的方法:
1、选用熔池面积小的炉子熔炼。
如采用工频炉代替反射炉。
2、制定合理的操作规程。
易氧化、挥发的合金元素应制成中间合金在最后加入,或在熔剂覆盖下熔化。
装料时要做到炉料合理分布,尽量采用高温快速熔化,缩短熔炼时间。
熔炼黄铜时采用低温加锌。
3、碎屑散料应制成捆或团使用。
4、正确控制炉温。
在保证熔融金属的流动性及其它工艺要求的条件下,选择适当的熔炼温度。
5、炉气一般以控制微氧化性气氛较好;
6、选用覆盖剂可防止金属氧化和减少挥发损失。
含有铝、铍等元素的合金,由于能在熔融金属表面形成致密的氧化膜,一般不再加覆盖剂;
但操作中应注意勿使氧化膜遭到破坏;
7、正确选择覆盖剂或熔剂,使具有足够的流动性和覆盖能力,同时采取高温扒渣、捞渣等措施,降低渣中金属损耗。
8、利用脱氧剂使基体金属的氧化物还原。
(*)
9、采用真空熔炼或保护性气体熔炼。
第二节杂质的控制
一、杂质的来源在熔炼过程中,大多数杂质是金属从炉衬、炉气、熔剂、炉渣、操作工具等方面吸收的。
如炉衬材料选用不当时,在熔炼温度下,金属就会与炉衬相互作用,不仅降低炉衬寿命,而且会使某些杂质进行金属。
如在酸性炉衬的工频炉中熔炼铝青铜时,会使合金增硅。
燃料不纯时也会增加杂质,如用含硫高的煤气或重油作燃料时,在加热和熔炼铜、镍的过程中,会因下列反应而增硫:
Cu+S=Cu2S
Ni+S=Ni3S当铜和铜合金用米糠作覆盖剂,镍和镍合金用稻草灰作覆盖剂时,都会使金属增磷。
从炉衬、炉气、覆盖剂或熔剂中吸收的杂质,虽然每次熔炼所吸收的量很小,但由于部分炉料经反复使用,杂质含量也有可能逐步积累增多,甚至造成报废。
许多杂质在熔炼中的烧损比合金的组成元素少,反复回炉熔炼会使杂质相对含量增加。
因此,生产中新金属与旧料的使用量一般保持一定比例,使杂质不超过一定含量。
此外,变料时洗炉不彻底,炉料管理不善,原料的混料等都会使金属中杂质增多。
二、控制杂质的途径
1、加强炉料管理,杜绝混料
2、在可能条件下,新金属和旧料搭配使用,旧料的使用量不超过炉料的50%;
3、变料时,必须按金属的杂质要求,准确计算洗炉次数;
4、选用化学稳定性高的耐火材料。
如镍合金用镁砂炉衬,铝青铜用中性炉衬等;
5、与熔融金属接触的工具,尽可能采用不易带入杂质的材料,或用涂层保护。
第三节炉料炉料包括:
新金属、厂内旧料、外来废料、二次重熔料、中间合金等。
1、新金属:
电解铜、电解镍、电解锌、电解锡
2、厂内旧料:
包括熔铸车间的残料、洗炉料和废品,铸锭加工的锯屑和切削屑,加工车间返回的残屑、残料及边角料等。
(废梗、刨花、铜渣)
3、外来废料:
如紫铜、白铜角料、火烧铜
4、二次重熔料:
铜块
装料顺序及原则:
1、炉料入炉前应检验化学成分及杂质含量;
2、炉料应该清洁干燥、无尘土、油污、腐蚀物
3、为装炉方便,锭块要堆垛整齐,边角料要打包制团,散料应装入料斗等,以减少装炉时间。
原则:
1)炉料中总质量最多的金属应最先入炉,即基体金属首先入炉。
如熔炼铜合金时,先熔铜。
2)易氧化,易挥发的合金元素,应留到最后装炉和熔化。
3)合金熔化放出大量热的金属,不应单独加入,而应与预先留下的基体冷却料同时加入。
如将铝加入到铜液中,所放出的热量,可使局部温度升高200度以上。
4)一般两种熔点相差较大的金属,应先装入易熔金属,然后再加入难熔金属,利用难熔金属的熔解作用,使其逐渐溶解于低熔点金属中。
如熔炼白铜时,由于铜(1083)的熔点比镍(1451)低出较多,故先熔铜后加入镍,只需在1250-1270时镍可全部熔化。
如硅青铜熔炼时,将硅和锰先熔化在感应炉起熔体中,合金熔体含气量大为减少。
第四节中间合金一、使用目的与要求
1)便于加入某些熔点高、易氧化燃烧或挥发的元素到合金中去;
2)有利准确控制合金的化学成分;
3)避免金属液过热,减少熔炼损耗;
4)缩短熔化时间。
第二章熔炼与铸造
第一节除气和脱氧
一、气体的来源能溶解于金属中的气体,主要是氢和氧。
在熔炼过程中,气体的主要来源有:
1、炉气:
非真空熔炼时,炉气是金属中气体的主要来源。
在炉气中除含有氧、氮外,还含有水汽、氢、一氧化碳、二氧化碳、二氧化硫和碳氢化合物等。
炉气的成分随使用的燃料和燃烧的情况的不同而变化;
如以重油或煤气做燃料的反射炉或坩埚炉中,常含有5-10%的水汽和较多的氢、一氧化碳等。
2、炉料:
电解金属表面大都有残留电解液,加工车间返回料大都含有油、水、乳液等。
外来废料大都有水腐蚀物、锈蚀等。
特别是露天堆放和潮湿季节,炉料表面吸附有水分。
这些都会使金属在熔炼过程中吸收较多的氢。
3、耐火材料:
耐火材料中所含水分也能促使金属吸气,新炉开始生产时尤为严重。
4、熔剂:
许多熔剂都带有水分,其中一些(如木炭、米糠等)含有吸附的水分,有些熔剂(如硼砂)本身带有结晶水。
为减少熔炼过程中气体的来源,熔剂应进行干燥或脱水处理。
5、操作工具:
操作工具预热不彻底,也会增加金属的含气量。
二、气体的溶解过程及溶解度
气体在金属中溶解度:
金属在固体时,气体的溶解度很小,随着温度的上升溶解度缓慢增加,到熔点温度时溶解度急剧增加,继续提高熔融金属的温度,气体溶解度继续增加,到某一最大点后开始下降,到金属的沸点温度时,气体溶解度几乎等于零。
不同的合金元素对气体在合金中的溶解度的影响也不同,某些元素如镍等与气体有较大的结合力,使合金中的气体的溶解度增加。
另上些元素如铝、锡等能使气体在合金中的溶解度降低。
铜合金中合金元素对氢气溶解度的影响如下:
Cu+Ni>
Cu+Pb>
Cu+Ag>
Cu+Au>
Cu+Sn>
Cu+Al
三、除气方法:
1、气体除气法:
一种为惰性气体(如N2等),另一种是活泼气体(如Cl2等)气泡越小,数量越多,对除气是有益的。
但由于气泡上浮的速度大,通过熔体的时间短,且气泡不可能均匀分布于整个熔体中,故用此法除气不容易彻底;
随着熔体中含氢量的减少,去气效果显著降低。
2、熔剂除气法:
熔剂除气是利用熔盐的热分解或与金属进行置换反应,产生不溶于熔体的挥发性气泡而将氢除去。
如铝青铜常用冰晶石熔剂除气,白铜和镍合金常用萤石、硼砂、碳酸钙等熔剂除气。
熔剂精炼时,一般将干燥的熔剂用带孔罩压入熔池中。
为了提高除去效果,也可采用干燥氮气将粉状熔剂吹入熔池中。
熔剂在除气的同时,还可去渣。
3、沸腾除气:
在工频炉熔炼高锌黄铜时常用的一种方法。
但需具备两个条件:
一是高锌黄铜的沸腾温度较低,二是熔沟部分熔体温度较高。
铜锌合金的沸腾温度随锌含量的增加而降低。
由于工频炉中熔沟部分熔体温度最高,首先形成锌的蒸汽泡随即上浮。
伴着熔池温度的升高,炉膛内的蒸汽压也随逐渐提高;
当温度升高到整个熔池接近锌的沸点时,甚至使整个熔池表面出现冒泡。
当熔池上面的蒸汽压升高到超过大气压时,锌蒸汽便向炉口喷出,被氧化燃烧,形成沸腾的喷火现象。
次数越多,除气效果越好,一般2-3次即可。
含锌量小于20%的黄铜,不能利用沸腾除气。
缺点在于低沸点金属元素(如锌等)损耗较大。
4、其他除气法:
1)冷凝除气;
2)振荡除气;
3)直流电解除气
四、脱氧过程
使金属熔体中的氧化物还原而除去氧的过程称为脱氧。
熔融金属及合金中的脱氧过程属于置换反应,凡在操作条件下,能从熔融金属中取得氧的任何物质,即氧化物的分解压比被脱氧金属氧化物的分解压为低的元素,一般都可作为脱氧剂。
五、脱氧剂
分为表面脱氧剂和溶解于金属的脱氧剂两种。
表面脱氧剂基本上不溶于金属,脱氧作用仅在与金属接触的表面进行,脱氧速度较慢。
它的优点不溶于金属,脱氧剂不会影响金属的质量。
常用的表面脱氧剂有:
碳化钙、硼化镁、木炭、硼(B2O3)等。
溶于金属的脱氧剂,能在整个熔池中与熔融金属中的氧化物相互作用,脱氧效果好得多。
缺点是剩余的脱氧剂将留于金属中而影响金属的性能。
常用的脱氧剂有:
磷、硅、锰、铝、镁、钙、钛、锂等。
这些元素可以中间合金的形式加入。
脱氧反应所产生的细小固体氧化物,使金属的粘度增大,或成为金属中分布不均匀的夹杂物,故应控制加入量。
对脱氧剂的要求:
1.对金属或合金的性能无害。
2.脱氧产物最好不溶于熔融金属,且容易除去。
3.脱氧剂应足够活泼,即脱氧产物应与熔融金属在比重和熔点上有较大的差别。
铜磷中间合金除能脱氧外,并能改善合金的流动性,在铜合金生产中应用较广。
第二节精炼
1、氧化精炼
2、除渣精炼
3、熔剂:
使用熔剂的作用是:
防止吸气、氧化;
除气、除渣;
细化晶粒;
通过熔剂加入某些元素。
熔剂按用途分覆盖剂、精炼剂、氧化剂、还原剂、变质剂。
按化学性质又分为酸性、碱性、中性三大类。
酸性熔剂如硼砂、硅砂等,用来除去碱性和中性如氧化物;
而碱性熔剂如苏打、
碳酸钙,则用以除去酸性及中性氧化物;
中性熔剂有碱金属、碱土金属的氯盐和氟盐,如KCL、NaCl、CaCl2、CaF2等以及木炭、米糠、玻璃等。
铜和铜合金常用木炭、米糠等作覆盖剂,既可保温和防氧化,又可结渣和改善流动性。
第三节变质处理
变质处理是金属或合金在熔铸过程中,广泛应用于改善材料性能、提高产品质量的重要手段。
变质处理的方法很多,如加变质剂、机械振动、超声波振动、快速冷却等。
变质剂的作用有:
1)细化晶粒
2)使合金中高熔点化合物的粗大晶粒改变形状,并均匀分;
3)使晶