过程审核控制程序Word格式文档下载.docx
《过程审核控制程序Word格式文档下载.docx》由会员分享,可在线阅读,更多相关《过程审核控制程序Word格式文档下载.docx(20页珍藏版)》请在冰豆网上搜索。
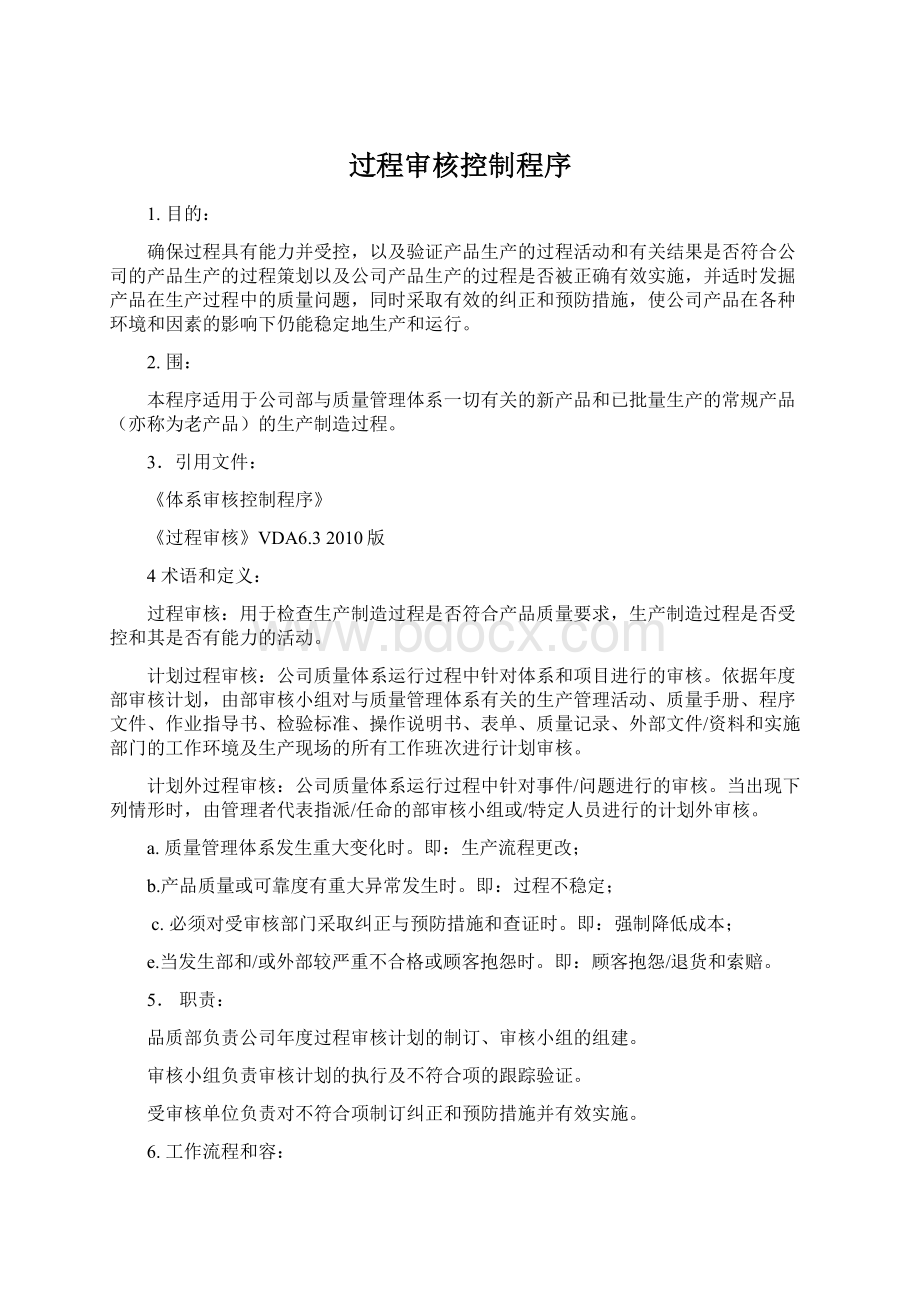
c.必须对受审核部门采取纠正与预防措施和查证时。
强制降低成本;
e.当发生部和/或外部较严重不合格或顾客抱怨时。
顾客抱怨/退货和索赔。
5.职责:
品质部负责公司年度过程审核计划的制订、审核小组的组建。
审核小组负责审核计划的执行及不符合项的跟踪验证。
受审核单位负责对不符合项制订纠正和预防措施并有效实施。
6.工作流程和容:
责任单位
工作容
记录
品质部
1.过程审核策划
1.1机构和人员
品质部负责组织实施过程审核,系统独立地行使质量审核职能。
审核员任职要求见公司的《岗位说明书》中规定的过程审核员的岗位说明书;
经最高管理者或管理者代表聘任。
为体现过程审核的客观性和公平性及公正性,审核组长在拟定审核员与被审核部门的容和围时,必须确定审核员与被审核单位无直接关系。
过程审核方法采用VDA6.3(2010),如客户有其他要求,按照客户要求执行。
1.2审核依据
a.公司编制的现行有效的质量管理体系文件:
质量手册、程序文件、作业指导书及表单/记录;
b.IATF16949:
2016质量管理体系标准;
c.有关的技术标准;
d.适用的法律、法规;
e.顾客指定的标准或特殊要求等;
f.D/PFMEA、控制计划、作业指导书等相关文件。
1.3审核围
1涉及公司质量管理体系覆盖的所有产品有关的生产制造过程(如冲压、焊接、装配等)、所有班次以及适当的交接班抽样。
1.3
1.4审核频次
本公司新产品和已批量生产的常规产品(亦称为旧产品或老产品)之过程审核每年至少实施一次(如客户有要求,按照客户要求的频次);
必须覆盖所有产品有关的生产制造过程(如冲压、焊接、装配等)、所有班次以及适当的交接班抽样;
当出现下列现象时,其实施的过程审核频率由质量、技术和生产部门根据当时产品所发生的实际状况来确定增加审核频次:
a)、顾客抱怨/退货和索赔;
b)、生产流程更改;
c)、过程不稳定;
d)、强制降低成本。
1.5审核方式
计划审核或计划外审核。
2.制定年度审核计划
品质部专职审核员根据新产品试生产过程和已批量生产的常规产品(亦称为老产品)的重要性以及以往审核的结果和管理评审的有关要求,编制《年度过程审核计划》。
2.1年度审核计划的更改
需要时,可以修改年度计划,临时增加或减少审核频次及围,修改后的计划须经管理者代表批准。
2.1.1.当外部质量问题影响到生产制造过程时,要修订《年度过程审核实施计划》,增加审核的频次。
2.1.2.已批量生产的常规产品出现下列情形时,需修订年度部质量审核计划,增加审核的频次:
生产转移;
发生重大质量问题;
新订单/合同;
材料、重要加工工艺的改变;
顾客或政府、安全法规新增加的特殊要求;
其它重要过程的改变。
3.《年度过程审核计划》由品质部部长审核、管理者代表批准,于年初以公司文件形式下发各有关单位。
年度部质量审核计划
4.品质部负责组建审核小组:
由品质部专职审核员与各有关单位的兼职审核员组成,并确定审核组长。
审核组长
5.审核组长召集审核小组成员根据产品过程审核的实际状况确定每种产品的过程审核围,其过程审核围的容包括:
a.新产品的生产制造过程;
b.已批量生产的常规产品的生产制造过程。
审核员
6.1审核员根据《过程审核实施计划》中相关的过程文件/资料把自己所负责的过程划分为工序,并对过程加以足够的描述,同时确定影响过程的各种参数。
6.2审核员在现场进行过程审核时直接用“质量审核查检表”或“审核提问表”有目的地进行提问。
7.在每次审核实施前,由审核员根据年度审核计划,编制部质量过程审核分计划(过程审核计划时程表),明确审核目的、围、依据、被审核单位、审核日程安排以及审核组组长,确定审核组成员,进行必要分工。
过程审核计划时程表
8.审核分计划由审核组长核准,提前5—7天通知审核组成员和被审核单位。
审核分计划一式两份,被审核单位与品质部各保存一份。
9.审核组成员收集并审阅《质量手册》、《程序文件》、《作业指导书》等有关文件资料。
研究本次审核容、目的、依据及方法,进行审核准备,编制“过程审核检查表”,。
检查表中所需检查的容,依据《过程审核》中的P2-P7容和项目编制。
质量审核检查表
10.审核员根据“过程审核实施计划”上的时间规定按已填写好的“质量审核检查表”上的相关容,对被审核部门进行过程抽样审核。
审核员对于审核的结果必须作好评分说明,评分方法详见本程序12-13流程容。
10.1审核员对于审核的结果必须加以适当的说明,如:
符合、不符合、
不适用或列入观察项等。
10.2现场审核方法:
提问、查看、收集证据、查文件、验证、确认,系统地记录审核实施情况。
11.按《年度过程审核计划》的过程审核采取定量评价,对审核结果以及审核报告的分析具有可比性,并按持续改进过程(KVP)的观点可以看出与以往审核的差异。
11.1对潜力分析结果的评价
针对每个问题,应根据相关的要求以及存在的风险一贯的落实情况,开展具体的评价。
作为参考基础,应对另一种使用类似的过程加工制造的类似的产品,开展在同等规模的量产条件下的评审。
对于没有评价的问题,必须说明原因(最多3个没有评价的问题)。
在这里需要注意的是,在这种情况下,评审结果可能将不再具备任何可比性。
针对潜力分析的每一个问题,应根据相关的要求以及存在的风险的一贯落实情况,开展具体的评价。
评价应采用信号灯系统,具体评价结果为“红灯”,“黄灯”或者“绿灯”。
对各个问题的评价
问题所涉及的要求没有被满足
问题所涉及的要求有条件的被满足(在对产品不构成风险的情况下)
问题所涉及的要求得到了满足
对于评价结果为“红灯”或者“黄灯”的问题,应说明具体的不符合项。
将各个问题的评价结果相加,就可以得到最终的评级。
最终评级采用的也是信号灯系统。
红灯:
被禁止的供应商(申请方)
评级
根据问卷目录做出的评价
黄灯
红灯
被禁止的供应商
超过14盏
一旦有任何一个问题被判定为红灯
需要加以控制的供应商
最多14盏
没有
放行的供应商
最多7盏
对于询价的项目,所涉及的零部件或者产品组,将不得发包(任命为合格供应商)。
黄灯:
需要加以控制的供应商(申请方)
可以发包(任命为合格供应商),但需要绑定一定的条件:
-由供应商开发团队负责专门的管理,对项目进展开展连续监控
提示:
上述条件应在相关负责的质量和综合部门之间协商确定。
绿灯:
放行的供应商(申请方)
对于询价的项目,所涉及的零部件或者产品组,客户将无条件的发包(任命为合格供应商)。
针对在生产基地审核基础上的质量能力验证,必须在具体的客户要求和过程,或者客户提供的具体产品的基础上,通过在研发或者量产过程中开展一次过程评审来加以实现。
11.2对物质类产品过程评审结果的评价:
11.2.1对各单独问题的评价
每个问题的评价得分可以分别是0分,4分,6分,8分或者10分。
在这里,验证要求的落实情况将被作为打分的评判依据。
分数
对符合要求程度的评定
10
要求完全得到落实
8
要求基本上得到落实;
只有极轻微的不符合情况*
6
要求部分得到落实;
存在一定程度的不符合情况
4
要求落实不够;
存在严重的不符合情况
要求没有得到落实
备注(*)
所谓“基本上”,指的是所有相关的要求在超过大约四分之三的实际应用情况中都被证
明得到了有效的落实,并且不存在任何特定的风险。
如果有任何问题没有被评价,则必须对不评价的理由进行说明。
对于每一个被评价的过程要素,必须有至少三分之二的问题得到评价。
为了确保评价结果可比性,应对问卷目录中的所有问题进行评价。
对于在过去的评审中已经反复出现过的不符合项,可以在打分时对具体的问题进行降级。
涉及特殊产品和过程风险的问题(*-问题):
在过程要素中,应将涉及特殊产品和过程风险的问题标记为星号问题(*-问题)。
对于此类问题,一旦出现不符合项,则应将其评定为非常严重的不符合项。
因为在这里,存在过程不可靠或者产品可能发生失效的风险。
某个具体的过程要素的落实程度EE的计算方法如下:
各相关问题实际得分的总和
Ee(%)=---------------------------------------×
100%
各相关问题可能的最高分的总和
12.3总体评价:
a.
针对物质产品的过程
项目管理P2
EPM
产品和过程开发的策划P3
EPP
产品和过程开发的实现P4
EPR
供应商管理P5
ELM
过程分析/生产P6
EPG
客户支持/客户满意度/服务P7
EK
b.SOP前ED的落实程度(参见第1版A部分)的计算方法如下:
(EPM+EPP+EPR)
ED(%)=--------------------------------×
3
c.SOP或者SOP以后的落实程度EP(参见第1版B部分)的计算方法如下:
(ELM+EPG+EK)
Ep(%)=--------------------------------×
d.过程评审的总体落实程度EG的计算方法如下:
(EPM+EPP+EPR+ELM+EPG+EK)
Eg(%)=----------------------------------×
e.总体落实程度
落实程度EG[%]
评级说明
A
EG≥90
具备质量能力
B
80≤EG<
90
有条件的具备质量能力
C
EG<
80
不具备质量能力
降级规则
应应用以下的分级规则,并且在评审报告中加以记录。
在落实程度EG≥90%的情况下,仍然将级别从A降至B的理由:
●P2-P7中至少有一个过程要素或者过程步骤E1-En被评价为落实程度<
80%
●P6的子要素,例如过程输入,工作容,过程支持,物质资源,效率,过程成果,零部件搬运的落