铸造技术培训内容讲诉Word格式.docx
《铸造技术培训内容讲诉Word格式.docx》由会员分享,可在线阅读,更多相关《铸造技术培训内容讲诉Word格式.docx(26页珍藏版)》请在冰豆网上搜索。
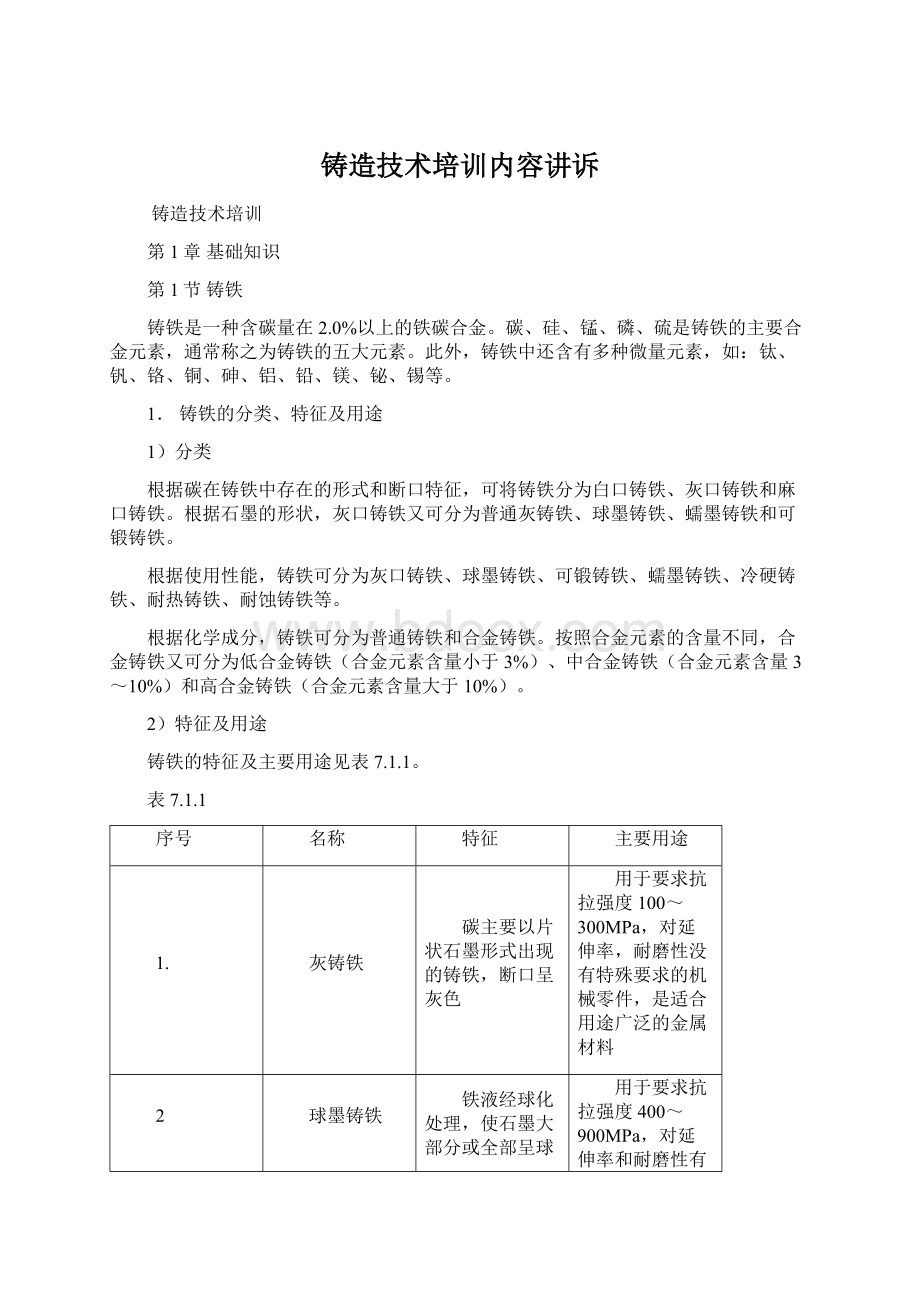
用于要求抗拉强度100~300MPa,对延伸率,耐磨性没有特殊要求的机械零件,是适合用途广泛的金属材料
2
球墨铸铁
铁液经球化处理,使石墨大部分或全部呈球状,有时少量为团絮状的铸铁
用于要求抗拉强度400~900MPa,对延伸率和耐磨性有一定要求的机械零件,如汽缸、轴承座、打桩锤等
3
蠕墨铸铁
铁液经蠕化处理,使石墨大部分呈蠕虫状的铸铁
用于要求抗拉强度350~400MPa,对导热性和耐热疲劳性有一定要求的机械零件,如大功率柴油机气缸盖、排气管等
4
可锻铸铁
(马铁)
白口铸铁通过石墨化或氧化脱碳可锻化处理,改变其金相组织和成分而获得的有较高韧性的铸铁,其石墨呈团絮状
用于要求抗拉强度300~450MPa,对塑性和韧性具有一定要求的机械零件,如铁路零件,汽车后桥等
5
白口铸铁
碳主要以游离碳形式出现的铸铁,断口呈银白色
用于高耐磨性的机械零件,如:
耐磨机内衬板和磨球等
2.铸铁的凝固
1)碳当量
碳当量表示铸铁中硅和磷对铁碳共晶综合影响的指标,用来估计某一铸铁成分在一定冷却速度时接近共晶的程度。
CE=C+1/3(Si+P)
式中CE——碳当量(%);
C——总碳含量(%);
Si——硅含量(%);
P——含磷量(%)。
2)共晶度普通铸铁中含碳量与共晶点含碳量的比值。
反映铸铁成分接近共晶的程度。
Sc=C/[4.26-1/3(Si+P)]
Sc——共晶度;
3)铸铁冷却曲线
冷却曲线反映铸铁合金的凝固结晶情况,是快速测定铸铁碳当量和碳、硅含量的依据。
典型的铸铁冷却曲线见图7.1.1。
图7.1.1铸铁的冷却曲线
4)铸铁的凝固结晶过程及其组织
根据碳当量或共晶度,铸铁可分为CE<4.26%或Sc<1为亚共晶铸铁、CE=4.26%或Sc=1为共晶铸铁、CE>4.26%或Sc>1为过共晶铸铁。
表7.1.2铸铁的组织
铸铁类别
按稳定系结晶
按介质稳定系结晶
共晶铸铁
F+G(G共晶+CⅡ+G共析)
P+Le+CⅡ+G共析
亚共晶铸铁
过共晶铸铁
F+G(GⅠ+G共晶+CⅡ+G共析)
注:
1.Le(莱氏体)=A共晶+C共晶。
2.F为铁素体,G为石墨,P为珠光体,C为渗碳体。
3.影响铸铁组织和性能的因素
灰铸铁金相组织包括石墨与金属基体两个部分。
1)铸铁中石墨的形状、分布、大小和数量对铸铁机械性能有着重要影响。
表7.1.3铸铁的石墨形状与其抗拉强度的关系
石墨形状
抗拉强度(MPa)
延长率(%)
片状石墨铸铁(灰铸铁)
100~300
~0.5
蠕虫状石墨铸铁
350~400
~1.0
絮状石墨铸铁(可锻铸铁)
350~450
2~10
球状石墨铸铁
400~900
2~12
在石墨均匀分布的条件下,石墨尺寸越大,铸铁的性能越差。
细小分布的石墨可有效地提高铸铁的力学性能。
此外,铸铁中石墨的数量对力学性能亦产生一定影响,通常石墨数量越多,机械性能越差。
2)灰铸铁的基体可分为铁素体基体、铁素体和珠光体混合基体、珠光体基体等三类。
以铁素体为基体的铸铁机械性能强度差、硬度和塑性亦较差。
铁素体和珠光体混合基体灰铸铁强度和硬度随着珠光体数量的增多而提高。
以珠光体为基体的灰铸铁强度和硬度均较高,并且随着珠光体的细化而明显提高。
铸铁中磷共晶若呈网状存在时,其强度大大降低,脆性增加。
因此磷共晶在铸铁中以分散孤立分布为好。
铸铁基体中如果出现碳化物和自由渗碳体,则使铸铁性能恶化,强度降低,脆性增加,硬度剧增,切削加工性能也变坏。
因此对铸铁中的自由渗碳体和碳化物要严加限制。
3)化学元素对组织与性能的影响见表7.1.4。
表7.1.4
化学元素
对金相组织的影响
对力学性能的影响
碳、硅
铸铁中碳、硅量增加,石墨粗大,数量增加,基体中铁素体增加、珠光体减少。
碳、硅量过低,铸铁中出现E型石墨,甚至出现麻口、白口组织。
铸铁的强度和硬度低组织疏松。
当碳、硅量恰当,使铸件得到均匀分布的石墨和珠光体时,力学性能提高。
碳、硅量过低,强度下降、硬度升高。
硫、锰
当铸铁中锰量较低时,硫形成共晶体以及其他富铁硫化物。
当锰量高时,则能形成高熔点MnS存在于铸铁中。
过量的锰可增加铸铁中的珠光体和化合碳。
硫在铸铁中恶化铸造性能,如降低流动性,增加铸件裂纹倾向。
铸铁中锰与硫生产MnS后剩余的锰能显著提高铸铁的强度和硬度。
磷
在铸铁中形成二元或三元磷共晶
磷共晶本身硬而脆。
铸铁的硬度随着含磷量增加而提高,而韧性则随之降低。
铜、镍
阻碍珠光体分解,可使珠光体数量增多和细化,强化铁素体
能提高铸铁强度和硬度,又能防止白口的产生
铬、钼、矾
具有细化石墨和强化基体的作用,使铸件得到细小均匀分布的珠光体基体
能有效地提高铸铁的强度和硬度。
但碳当量低而Cr、Mo、V等元素含量过高,促使铸铁产生白口
钛
在铸件中多形成特殊碳化物。
钛可促使高碳当量铸铁石墨细化
能提高铸铁的强度和耐磨性
4)铸件冷却速度对铸铁组织与性能的影响:
在保证析出石墨的冷却速度范围内,冷却速度慢,过冷度小,石墨粗大;
反之石墨细化。
冷却速度过快,过冷度大,则形成细小的过冷石墨。
影响铸件冷却速度的因素很多,主要有:
(1)铸件壁厚的影响
表7.1.5
铸件壁厚
冷却速度
金相组织
力学性能
减少
增加
石墨细小,基体中珠光体数量增加,铁素体量减少
强度和硬度均有所提高
过薄
加剧
局部或全部出现白口(渗碳体+珠光体)
脆性和硬度增加,而韧性下降
厚大
很低
石墨粗大,组织疏松,基体中铁素体数量增加
强度和硬度均降低
(2)浇注温度的影响
浇注温度高,冷却速度慢,铸件石墨粗大,铁素体量增加,铸件的强度和和硬度降低。
反之,浇注温度低,铸件冷却速度快,促进石墨细化,增加珠光体数量,提高铸件强度和硬度。
(3)铸型材料的影响
不同的铸型材料与冷却速度的关系见表7.1.6。
表7.1.6铸型材料与冷却速度的关系
试样直径(mm)
平均冷却速度(℃/mm)
湿砂型
干砂型
预热型
金属型
30
20.5
12.0
9.1
35
300
1.7
1.2
0.5
2.3
(4)浇注系统的影响
铁液经直浇道、横浇道和内浇道进入型腔,浇道附近的铸件被加热,降低了铸件的冷却速度,从而使该部分铸件晶粒粗大,铁素体量增加。
冒口附近亦如此。
4.普通铸铁件常见缺陷和防止方法
1)常见的缺陷:
气孔、疏松、针孔、表面气泡;
冷隔、接缝、起皮;
铁豆;
粗晶组织;
缩孔:
外缩孔、内缩孔、缩松;
热裂、冷裂;
材质硬化,如局部硬化、白口化、反白口;
浇不足、冷疤;
夹杂物;
夹渣滓、包砂、夹砂、结疤;
石墨漂浮;
化学粘砂、机械粘砂;
表面粗糙等。
2)产生原因与防止方法:
(1)气孔
气孔产生的原因:
铁水中产生气体的主要原因是熔化过程中铁水的氧化,铁水的氧化取决于所用的原材料及熔化气氛中带入的氧气,以及浇包未烘干、冷铁表面状态不适当(如有铁锈、大气中凝结的水分)等。
气孔防止方法:
获得纯净的铁水可减少气体含量;
使用无锈和无粘附杂物的干净原材料。
在熔化时还要根据熔化时设备采取适当的防止方法。
冲天炉熔化时关键在于避免过量的送风,并保证有适当的底焦高度。
电炉熔化时存在着铁水与大气接触的问题,提高熔化温度是必不可少的措施。
保持铸型内适宜的水分。
使铸型中产生的气体能够从铸型中直接排出,设计铸造工艺时提高铸型的透气性,开设透气孔。
(2)疏松
呈分散状态分布,每个空洞的尺寸较小。
疏松不一定出现在铸件的表层,铸件内部同样存在。
形成疏松的原因与气孔相同,因此其防止方法与气孔一样。
(3)针孔
针孔是一种在铸件表面局部区域存在,像针尖扎过的细小空洞的缺陷,往往出现于铸件的表层或皮下。
产生原因与气孔和疏松一样,主要由铁水中的氧化物与碳反应生成的一氧化碳,或铁水与型砂接触而产生的气体,以及铸型中的水分等引起的,它特别容易出现于薄壁铸件。
此外,在加入的孕育剂(硅铁合金等)未充分干燥,铝等特殊元素含量较多或浇注在强还原性气氛中熔化的铁水等情况下,也较易产生针孔。
防止方法首先必须获得纯净的铁水,适当地降低浇注温度,并尽可能地缩短浇注时间。
其次采用水分少的造型材料,以及避免在型砂中混入有机物等材料,是防止产生针孔的好方法。
(4)缩孔
铸件的缺陷中,缩孔的产生比例最高。
由于金属从开始凝固直至冷却到室温的过程中,一般都产生体积收缩,但是对凝固过程中析出石墨的铸铁来说,由于石墨的析出会引起一定的体积膨胀。
因而与其他金属相比,铸铁产生的倾向要小得多。
但也有难以避免的情况。
防止方法:
设计铸件时,尽可能减少壁厚差。
设置足够的冒口以补偿厚壁部分的凝固收缩。
但是过量的冒口不仅不经济,而且还会引起其它缺陷。
为加速厚壁部分的冷却,可使用冷铁等。
在可能的范围内提高碳硅含量,以促进石墨化。
使用不含阻碍石墨化的杂质元素的优质材料。
为更有效地发挥冒口的作用,使用发热保温剂、冒口搅拌法以及补浇高温铁水等方法。
(5)粗晶组织(缩松)
在厚壁处由于冷却缓慢,石墨得到了很好的成长,形成粗大组织,有时即使用肉眼也能看出断口颜色和光泽的差别。
稍微粗点的组织并不是一种缺陷,但在壁厚极厚的铸件中,如果化学成分调整不当,碳硅过多时,往往呈现出极端粗大组织。
如果此时再切断凝固收缩时的铁水补给,就会形成粗晶组织或缩松的缺陷。
缩松的形成机理与缩孔一样,它的特点是在局部凝固迟的部位汇集了铁水中低熔点的物质,而这些物质收宿时已无法再得到铁水的补给。
防止方法与缩孔完全相同,但特别要注意含碳量。
(6)浇不足,冷疤
浇入铸型的铁水不能完全浇到铸型的每个角落,而使边缘成圆角的情况称为浇不足。
最有效的防止方法是提高浇注温度。
此外,提高浇注速度、抑制型砂和涂料等产生气体,以及使型内的气体顺利排出型外等也很重要。
(7)热裂、冷裂
热裂和冷裂的产生条件完全相同,都是由于铁水在凝固和冷却过程中存在着不均匀的冷却,使铸件的某一部分在膨胀、收缩阶段变形,产生内应力,当铸件经受不住这个应力时,便产生热裂和冷裂。
热裂是铸件在达到室温前冷却过程中产生的裂纹,它的断口呈茶褐色或紫红色。
冷裂是冷却后形成的裂纹,其断口一般呈灰色。
防止方法
设计铸件时,尽量减少壁厚差。
设计铸造工艺时,考虑壁厚不同时如何使整个铸件均匀冷却,如在厚壁处设置