手机翻盖注射模的设计Word格式.docx
《手机翻盖注射模的设计Word格式.docx》由会员分享,可在线阅读,更多相关《手机翻盖注射模的设计Word格式.docx(27页珍藏版)》请在冰豆网上搜索。
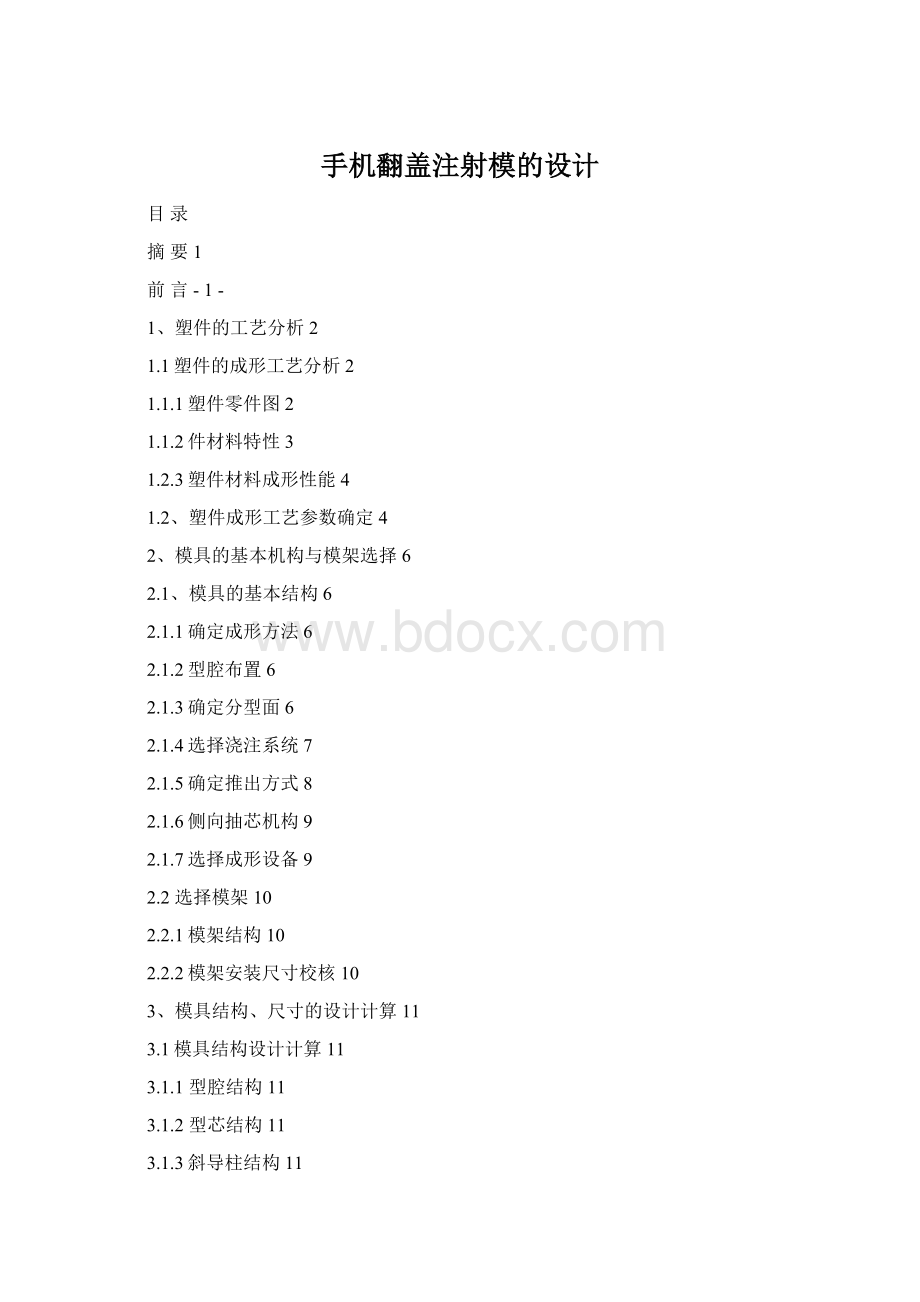
3、模具结构、尺寸的设计计算11
3.1模具结构设计计算11
3.1.1型腔结构11
3.1.2型芯结构11
3.1.3斜导柱结构11
3.1.4模具的导向结构12
3.1.5结构强度计算13
3.2模具成形尺寸设计计算13
3.2.1型腔径向尺寸13
3.2.2型腔深度尺寸14
3.2.3型芯径向尺寸15
3.2.4型芯高度尺寸15
3.3模具加热、冷却系统计算15
3.3.1模具加热15
3.3.2模具冷却16
4、模具主要零件图及加工工艺规程17
4.1模具定模板(中间板)零件图及加工工艺规程17
4.2模具侧滑块零件图及加工工艺规程18
4.3模具动模板(型芯固定板)零件图及加工工艺规程19
5、模具总装图及模具的装配、试模20
5.1模具总装图及模具的装配20
5.1.1成形零件及浇注系统20
5.1.2推出系统零件21
5.1.3滑块及活动零件21
5.1.4导向机构21
5.1.5加热与冷却系统22
5.1.6模具外观22
5.2模具的安装试模22
5.2.1试模前的准备22
5.2.2模具的安装22
5.2.3试模23
5.2.4检验24
结束语25
致谢26
参考文献26
摘要
注射成形是现在成形热塑件的主要方法,因此应用范围很广。
注射成形是把塑料原料放入料筒中经过加热熔化,使之成为高黏度的流体,用柱塞或螺杆作为加压工具,使熔体通过喷嘴以较高压力注入模具的型腔中,经过冷却、凝固阶段,而后从模具中脱出,成为塑料制品。
塑料注射成形工艺的最大特点是复制,能够复制出所需任意数量的可直接使用或稍作处理即可使用的制品,是一种适宜大批量生产的工艺。
虽然在设备上投入较大,但是可以生产制品的数量非常大,实属一种经济快捷的生产方式,因此得到广泛的应用和快速的发展
本文针对手机翻盖的结构工艺特点.分析了注射模结构的设计过程,采用热流道系统,提高了塑件表面质量及成型效率.并详细介绍了模具的工作过程。
关键词:
注射模;
手机翻盖;
热流道;
工作过程
前言
这应该算是大学阶段最后一次作业了吧——如果可以用作业来形容毕业论文的话。
一心想拼凑出一篇流光溢彩的经典之作,好为大学生涯画上一个神采飞扬的句号,写起来竟然很艰难。
模具是一种技术密集、资金密集型产品,在我国国民经济巾的地位也非常重要。
模具工业已被我国正式确定为基础产业,并在“十五”中列为重点扶持产业。
由于新技术、新材料、新工艺的不断发展,促使模具技术不断进步,对人才的知识、能力、素质的要求也在不断提高。
采用热流道技术的模具可提高制件的生产率和质量,并能大幅度节省塑料制件的原材料和节约能源,所以广泛应用这项技术是塑料模具的一大变革。
设计的目的及意义:
(1)培养学生综合运用所学基础课、技术基础和专业课,分析和解决工程技术问题的独立工作能力;
(2)巩固、深化和扩大学习所基本理论、基本知识和基本技能;
(3)是学生受到综合产品设计的能力的综合训练,例如,产品设计的一般程序和方法、产品系统设计以及产品的开发设计等产品设计的全过程,并以此为核心,对产品设计过程中所涉及的设计理论以及美学和工学基础、设计表达和计算机辅助设计的相关知识和内容作全面系统的训练,同时不断总结提高撰写论文和设计说明书的能力等等;
(4)参与社会生产和学校科研工作、实验室建设,为现代建设做出贡献;
(5)培养学生的创新能力和团队精神,树立良好的学术思想和工作作风。
模具市场的总体趋热是平稳向上的,在未来的模具市场中,塑料模具的发展速度将高于其它模具,在模具行业中的比例将逐步提高。
随着塑料工业的不断发展,对塑料模具提出越来越高的要求是正常的,因此,精密、大型、复杂、长寿命塑料模具的发展将高于总量发展速度。
让我们共同努力,为不断提升模具制造水平,振兴我国装备制造业,为实现把我国建设成为制造业强国的宏伟目标而奋斗。
1、塑件的工艺分析
1.1塑件的成形工艺分析
1.1.1塑件零件图
如图1所示:
图1
产品名称:
手机翻盖
产品材料:
PC+ABSPC:
ABS=30:
70
产品数量:
较大批量生产
塑件尺寸:
86mm×
43mm如图所示
塑件质量:
10g
塑件颜色:
银灰色
塑件要求:
外表面质量要求较高,要尽量减少熔接痕、气泡、银丝、缩孔或其他塑料缺陷,另外塑件尺寸精度也要求较高,以满足和其他手机零部件的配合要求。
1.1.2塑件材料特性
(1)PC塑料
PC是聚炭酸酯的简称,聚碳酸酯的英文是Polycarbonate,简称PC工程塑料,聚碳酸酯是在分子链中含有碳酸酯的一类高分子化合物的总称,透明度达90%,被誉为透明金属,密度1.02~1.05g/cm3,是一种性能优良的热塑性工程塑料.PC材料其实就是我们所说的工程塑料中的一种,作为被世界范围内广泛使用的材料.
PC有着其自身的特性和优缺点,PC是一种综合性能优良的非晶型热塑性树脂,具有优异的电绝缘性、延伸性、尺寸稳定性及耐化学腐蚀性,较高的强度、耐热性和耐寒性;
良好的绝缘性及耐热性和无毒性.还具有自熄、阻燃、无毒、可着色、韧而刚、抗冲击性在热塑性塑料中名列前茅,成形零件可达到很好的尺寸精度并在很宽的温度范围内保持其尺寸的稳定性。
缺点是耐疲劳强度较差,成形后塑件的内应力较大,容易开裂。
(2)ABS塑料
ABS塑料的英文名称:
AcrylonitrileButadieneStyrene。
ABS树脂是丙烯腈(A)、丁二烯(B)和苯乙烯(S)三种单体的共聚物所组成,ABS材料是一种工程塑料。
ABS是由丙烯腈、丁二烯和苯乙烯三种化学单体合成。
每种单体都具有不同特性:
丙烯腈有高强度、热稳定性及化学稳定性;
丁二烯具有坚韧性、抗冲击特性;
苯乙烯具有易加工、高光洁度及高强度。
从形态上看,ABS是非结晶性材料。
三中单体的聚合产生了具有两相的三元共聚物,一个是苯乙烯-丙烯腈的连续相,另一个是聚丁二烯橡胶分散相。
ABS的特性主要取决于三种单体的比率以及两相中的分子结构。
这就可以在产品设计上具有很大的灵活性,并且由此产生了市场上百种不同品质的ABS材料。
这些不同品质的材料提供了不同的特性,例如从中等到高等的抗冲击性,从低到高的光洁度和高温扭曲特性等。
ABS材料具有超强的易加工性,外观特性,低蠕变性和优异的尺寸稳定性以及很高的抗冲击强度。
特点:
1、综合性能较好,冲击强度较高,化学稳定性,电性能良好。
2、与372有机玻璃的熔接性良好,制成双色塑件,且可表面镀铬,喷漆处理。
3、有高抗冲、高耐热、阻燃、增强、透明等级别。
4、流动性比HIPS差一点,比PMMA、PC等好,柔韧性好。
1.2.3塑件材料成形性能
成形收缩率很定为0.5%~0.8%。
虽然吸水性小,但高温时对水分比较敏感,会出现银丝、气泡及强度下将现象,所以加工前必须干燥处理,而且最好采用真空干燥法;
熔融温度高,熔体黏度大,流动性差,所以成形时要求有较高的温度和压力;
熔体黏度对温度十分敏感,一般用提高温度的方法来增加熔融塑料的流动性。
用途:
适于制作仪表小零件、绝缘透明件和耐冲击零件。
1、无定形料,流动性中等,吸湿大,必须充分干燥,表面要求光泽的塑件须长时间预热干燥80-90度,3小时。
2、宜取高料温,高模温,但料温过高易分解(分解温度为>
270度).对精度较高的塑件,模温宜取50-60度,对高光泽.耐热塑件,模温宜取60-80度.
3、如需解决夹水纹,需提高材料的流动性,采取高料温、高模温,或者改变入水位等方法。
4、如成形耐热级或阻燃级材料,生产3-7天后模具表面会残存塑料分解物,导致模具表面发亮,需对模具及时进行清理,同时模具表面需增加排气位置。
适于制作一般机械零件,减磨耐磨零件,传动零件和电讯零件
综上所述,6W&
E
{"
J#r_KiCAx开PC+ABS的强度方面又兼具了一些PC的特性是因为这种材料既具有PC树脂的优良耐热耐候性、尺寸稳定性和耐冲击性能,又具有ABS树脂优良的加工流动性。
所以应用在薄壁及复杂形状制品,能保持其优异的性能,以及保持塑料与一种酯组成的材料的成型性。
该PC/ABS塑料合金材料的综合性能较好,特别具有优良的耐热性能、冲击性能、低温冲击性能和阻燃性。
主要应用于通讯器材、家用电器、汽车、电脑及外设部件。
1.2、塑件成形工艺参数确定
查(塑料模具设计与制造)手册得到PC+ABS塑料的成形工艺参数:
密度:
1.02~1.05g/cm3;
收缩率:
0.4%~0.8%;
预热温度:
80℃~85℃预热时间:
2~3h
模具温度:
50℃~100℃
喷嘴温度:
250℃~300℃
料筒温度:
前段温度:
200℃~220℃
中段温度:
220℃~240℃
后段温度:
190℃~200℃
注射压力:
130~180MPa
注射机类型:
螺杆式
螺杆转速:
40~80次/min
保压压力:
50~60MPa
喷嘴形式:
直接接触式
注射时间:
0—5S
保压时间:
20—60S
冷却时间:
15—50S
成形时间:
40—120S
2、模具的基本结构与模架选择
2.1、模具的基本结构
2.1.1、确定成形方法
塑件采用注射成形法生产。
此塑件外形尺寸小,结构复杂,需多个抽芯结构。
另外塑件对外观质量要求较高,而所用的材料流动性较差,注射压力应保证充分,因此采用1模1腔的模具结构,且使用热流道浇注系统。
2.1.2、型腔布置
为了节省成本和减小加工难度,成型零件的型腔和型芯均采用整体嵌入式的结构。
对于产品周边的内凹搭扣和转轴孔,需要设计斜导柱抽芯机构来满足成型要求。
对于转轴下面的由内向外凹的结构,可以采用斜滑块内抽芯机构来解决。
所以模具采用一模一腔。
2.1.3确定分型面
选择分型面时的考虑方向:
〈1〉塑件开模后留在动模上
〈2〉分型面的痕迹不影响塑件的外观
〈3〉浇注系统和浇口的合理安排
〈4〉推杆的痕迹不露在塑件的外观上
〈5〉使塑件易于脱模
根据以上的分型面选择的原则:
塑件分型面的选择应保证塑件的质量要求,由于零件上有侧孔和侧凹,塑件外形尺寸小,结构复杂所以零件从塑件上的侧向分开,为此模具增加抽芯机构,需多个抽芯结构。
a图的分型面选择在下端面,这样的选择使塑件的外表面可以在整体凹模型腔内成形,塑件大部分外表面光滑,仅在侧向抽芯处留有分型面痕迹,同时抽芯简单,而且塑件脱模方便。
b图的分型面选择在轴线上,这种选择会使塑件表面留下痕迹,影响塑件表面质量,同时分型面也使侧向抽芯困难。
因此塑件选择图a所示的分型面。
图2
2.1.4选择浇注系统
(1)浇注系统的作用就是将熔融状态的塑料均匀,迅速地输入型腔,使型腔内气体及时排出,并且将注射压力传递到型腔的各个部分,从而得到组织紧密的制品。
模具浇注系统应尽量粗短。
热流道浇注系统在整个生产过程中浇注系统内的塑料始终处于熔融状态,具有如下优点:
1)由于热流道内的溶体温度与注射机喷嘴的温度基本相同,因而流道内的压力损耗小。
2)浇