塑胶件检验标准Word文档格式.docx
《塑胶件检验标准Word文档格式.docx》由会员分享,可在线阅读,更多相关《塑胶件检验标准Word文档格式.docx(28页珍藏版)》请在冰豆网上搜索。
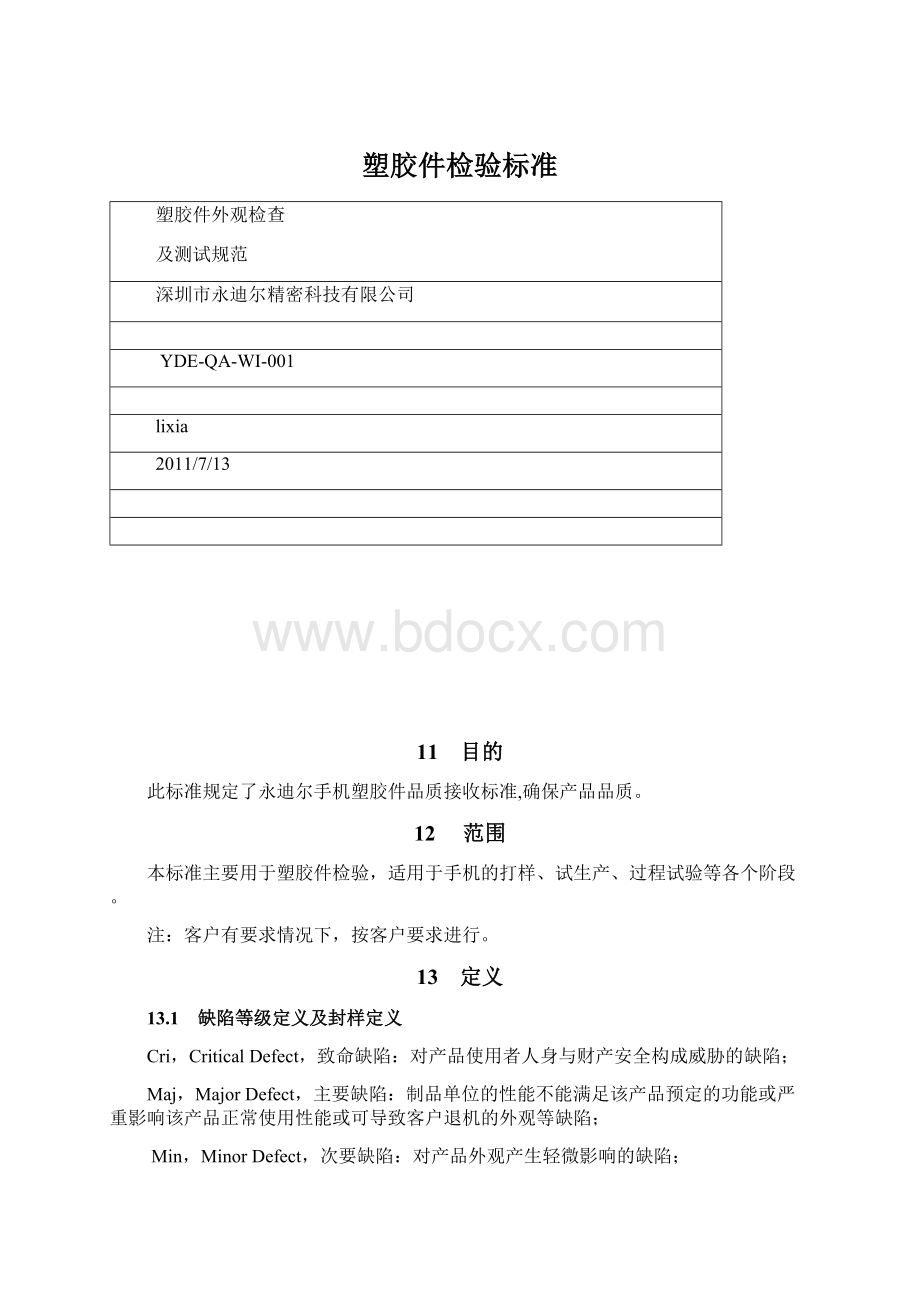
Acc,AcceptableDefect,可接受缺陷:
可以接受的缺陷,在产品制程质量评估时使
用,在产品出货抽样检验中仅供参考;
封样,GoldenSample,也称为金样板:
由设计部门或品管部门或市场部签名认可的、用于确认和鉴别各种订制结构件来料批量供货质量的样品;
一般可分为标准样板和/或
上限样板、下限样板(上/下限样板一般需征求市场部意见)、结构样板等。
13.2 不良缺陷定义
点缺陷--具有点形状的缺陷,测量尺寸时以其最大直径为准。
异色点--在产品表面出现的颜色异于周围的点,例如黑点、白点等。
Figure1
多胶--因模具方面的损伤而造成局部细小的塑胶凸起。
缩水--当塑料熔体通过一个较薄的截面后,其压力损失很大,很难继续保持很高的压力来填充在较厚截面而形成的凹坑。
最经常出现在有不同壁厚之间的分界面。
Figure2
发亮/亮斑--对于非光面的塑料件,由于壁厚不均匀,在壁厚突变处产生的局部发亮现象。
也可以由注塑时缺少足够的压力来复制模具上的纹路。
硬划痕/碰伤--由于硬物摩擦而造成产品表面有深度的划痕。
细划痕/刮花--没有深度的划痕。
顶针痕--顶针不正常的顶出产品导致突出或变形。
突出最常见在顶针顶出的对立面。
熔接线/夹水线--塑料熔体在型腔中流动时,遇到阻碍物(型芯等物体)时,熔体在绕过阻碍物后不能很好的融合,于是在塑料件的表面形成一条明显的线,叫做熔接线。
Figure3
变形/翘曲--塑料件因内应力而造成的平面变形。
顶白/顶凸--由于塑料件的包紧力大,顶杆区域受到强大的顶出力所产生的白印或凸起。
缺胶/填充不足--因注射压力不足或模腔内排气不良等原因,使融熔树脂无法到达模腔内的某一角落而造成的射料不足现象。
Figure4
流纹--产品表面以浇口为中心而呈现出的年轮状条纹。
水口位高/低--塑料成型件的浇注系统的末端部分超出/低于平面。
烧焦--在塑料件表面出现的局部的塑料焦化发黑。
由于排气不完全而导致部件表面有黑色条纹。
Figure5
玻璃纤维纹--无光泽的面和粗糙面出现玻璃纤维
Figure6
批锋--有多余的塑胶在模具分界线或分型面的位置.通常是沿着部件边长出非常薄平的胶.也常常表现为在部件的边部有非常细的线或塑胶的细丝。
Figure7
边拖花--因注射压力过大或型腔不平滑,脱模时所造成边缘的擦伤。
开裂/破裂--因内应力或机械损伤而造成产品的裂纹或细小开裂。
龟裂--橡胶件由于环境老化而造成在产品表面上有裂纹。
油渍--产品表面所残留的油污。
气泡--由于原料在成型前未充分干燥,水分在高温的树脂中气化而形成气泡。
Figure8
凹坑--由于模具的损坏等原因,造成在平面上出现的高低不平。
彩虹纹--指透明区域在反光条件下出现彩色光晕的现象。
透明度差--指透明区出现模糊、透明度不佳的现象。
Figure9
剥离--两种材料结合的部位,可以看到有间隙存在。
冷料--固体或者半固体和周围的已溶化的材料形成明显的分界和熔接线类似。
拉白--成型品脱模时,由于钩料杆的拉力大于顶料杆的顶出力,而使某部位所产生的白化。
颗粒--在喷漆件表面上附着的细小颗粒。
积油--在喷漆件表面出现局部的油漆堆积现象。
阴影--在喷漆件或塑料件表面出现的颜色较周围暗的区域。
桔纹--在喷漆件或电镀件表面出现大面积细小的像桔子皮形状的起伏不平。
透底--在喷漆件表面出现局部的油漆层过薄而露出基体颜色的现象。
鱼眼--由于溶剂挥发速度不适而造成在喷漆件表面有凹陷或小坑。
多喷--超出图纸上规定的喷涂区域。
剥落--产品表面上出现涂层或镀层脱落的现象。
毛絮--油漆内本身带有的,或油漆未干燥时落在油漆表面而形成的纤维状毛絮。
色差--产品表面呈现出与标准样品(客户承认样品)的颜色的差异,称为色差。
光泽不良--产品表面呈现出与标准样品(客户承认样品)光泽不一致的情况。
手印--产品表面或零件光亮面出现的手指印痕。
13.3 手机测量面的定义
0测量面:
手机上显示信息的重要区域,如镜片的透明区和LCD的透明区。
I测量面:
暴露在外,且正常使用时可直接看到的主要表面,如镜片的非信息显示区,键盘、前壳、后壳、电池盖的正面、翻盖(及大翻盖)的正反两面。
II测量面:
暴露在外,且正常使用时并不直接看到的次要表面及手机配件的外表面,如前壳、后壳电池盖、翻盖(及大翻盖)的侧面,天线的外表面,及其它手机配件如充电器、耳机等的外观面。
III测量面:
正常使用时看不到,只有在装卸电池或SIM卡时可看到的内表面,如后壳上被电池盖住的面或电池盖的内表面;
IV测量面:
只有在拆卸手机时才能看到的零件表面。
13.4 缺陷代码对照表
缺陷代码对照表见表1。
表1
代码
名称
N
数目
D
直径(mm)
L
长度(mm)
H
深度(mm)
W
宽度(mm)
DS
距离(mm)
S
面积(mm2)
14 抽样计划、手机检验条件及环境
抽样计划:
按照MIL-STD-105E(或等同标准),一般檢驗水準II,;
接受标准:
AQL(Cri:
0,Maj:
0,Min:
0.25);
进料允收水准应严于或等同于客户对成品的允收水准,因此,如客户对成品的允收水准严于上述标准时,应以客户标准为依据。
手机检验条件及环境的规则如下:
a)距离:
人眼与被测物表面的距离为300mm~350mm;
b)时间:
每片检查时间不超过12s;
c)位置:
检视面与桌面成45°
;
上下左右转动15°
d)照明:
100W冷白荧光灯,光源距被测物表面500~550mm,(照度达500~550Lux)。
Figure10
30°
度
30cm
15 装配检验
手机装配的检验项目如下:
a)检查各外观件的质量符合要求;
b)前壳与后壳之间的间隙均匀,且小于(设计装饰线宽度+0.1mm),段差均匀且小于(设计段差+0.1mm/0.15mm);
c)注:
手机两侧的段差控制在0.1mm;
手机顶部和底部的段差可以控制在0.15mm;
d)后壳与电池盖之间的间隙均匀,且小于(设计装饰线宽度+0.1mm),段差均匀且小于(设计段差+0.1mm/0.15mm);
e)注:
手机顶部和底部的段差可以控制在0.15mm。
f)将翻盖合上后,翻盖与前壳之间的间隙均匀,且小于(设计间隙+0.30mm),段差均匀且小于设计段差+0.25mm);
g)电池卡扣的弹性正常,电池易于拆装;
16 喷漆件检验
16.1 喷漆件外观检验
16.1.1 手机的喷漆件外观检验见表2。
表2
序号
不良项目
I测量面
II测量面
11
点缺陷
有颜色对比的点缺陷
D≤0.3mm(S≤0.07mm2),N≤1
当D≤0.35mm(S≤0.10mm2),N≤1;
当D≤0.25mm(S≤0.05mm2),N≤2且DS≥15mm
无颜色对比的点缺陷
当D≤0.35mm(S≤0.1mm2),N≤1;
当D≤0.4mm(S≤0.13mm2),N≤1;
当D≤0.3mm(S≤0.07mm2),N≤2且DS≥15mm
当点的直径≤0.10mm且DS≥2mm时可忽略不计。
2
硬划痕(碰伤)
D≤0.35mm,(S≤0.1mm2),N≤1
D≤0.4mm(S≤0.13mm2),N≤1
L≤0.5mm,W≤0.2mm,N≤1
(S≤0.1mm2)
L≤0.8mm,W≤0.2mm,N≤1
(S≤0.16mm2)
3
细划痕
L≤3mm,W≤0.1mm,N≤1
(S≤0.3mm2)
L≤5mm,W≤0.1mm,N≤1
(S≤0.5mm2)
4
纤维状毛絮
L≤3mm,W≤0.2mm,N≤1
(S≤0.6mm2)
L≤3mm,W≤0.2mm,N≤2且DS≥15mm
5
积漆
参照限度样品
6
缩水
7
多喷
8
桔纹
不允许
9
阴影
10
色差
参照上下限度样品或△E≤1时合格
11
光泽不良
参照上下限度样品或在标准光泽的±
10度公差范围内合格
12
手印(不可擦除)
13
透底
14
剥落
点缺陷包括异色点、杂质、颗粒、鱼眼等呈现点形状的缺陷。
16.2 附着力测试
用锋利刀片(刀锋角度为15°
~30°
)在测试样本表面划10×
10个1mm×
1mm小网格,每一条划线应深及油漆的底层;
用毛刷将测试区域的碎片刷干净;
用粘附力350g/cm2~400g/cm2的胶带(3M600号胶纸或等同)牢牢粘住被测试小网格,并用橡皮擦用力擦拭胶带,以加大胶带与被测区域的接触面积及力度;
用手抓住胶带一端,在垂直方向(90°
)迅速扯下胶纸,同一位置进行2次相同试验;
结果判定:
要求附着力≥4B时为合格。
5B-划线边缘光滑,在划线的边缘及交叉点处均无油漆脱落;
4B-在划线的交叉点处有小片的油漆脱落,且脱落总面积小于5%;
3B-在划线的边缘及交叉点处有小片的油漆脱落,且脱落总面积在5%~15%之间;
2B-在划线的边缘及交叉点处有成片的油漆脱落,且脱落总面积在15%~35%之间;
1B-在划线的边缘及交叉点处有成片的油漆脱落,且脱落总面积在35%~65%之间;
0B-在划线的边缘及交叉点处有成片的油漆脱落,且脱落总面积大于65%。
16.3 耐磨性测试
用专用的NORMANRCA耐磨测试仪(型号:
7-IBB-647)及专用的纸带(11/16inchwide×
6或8inchdiameter),施加175g的载荷,带动纸带在样本表面磨擦200个循环。
试验完成后以油漆不透底(露出底材)时为合格。
如果采用的是UV漆,要求耐磨性300个循环。
16.4 耐醇性测试
用纯棉布蘸满无水酒精(浓度≥99.5%),包在专用的500g砝码头上(包上棉布后测试头的面积约为1cm2),以40次/分钟~60次/分钟的速度,20mm左右的行程,在样本表面来回擦拭200个循环。
结果判定:
试验完成后以油漆不透底(露出底材)时为合格。
16.5 硬度测试
用1H铅笔(三菱或中华牌),将笔芯削成圆柱形并在400目砂纸上磨平后,装在专用的铅笔硬度测试仪上(施加在笔尖上的载荷为1Kg,铅笔与水平面的夹角为45°
),推动铅笔向前滑动约5mm长,共划5条,再用橡皮擦将铅笔痕擦拭干净。
检查产品表面有无划痕(划破面漆),当有1条以下时为合格