汽车悬架摆臂铝合金压铸件压铸工艺设计毕业论文.docx
《汽车悬架摆臂铝合金压铸件压铸工艺设计毕业论文.docx》由会员分享,可在线阅读,更多相关《汽车悬架摆臂铝合金压铸件压铸工艺设计毕业论文.docx(54页珍藏版)》请在冰豆网上搜索。
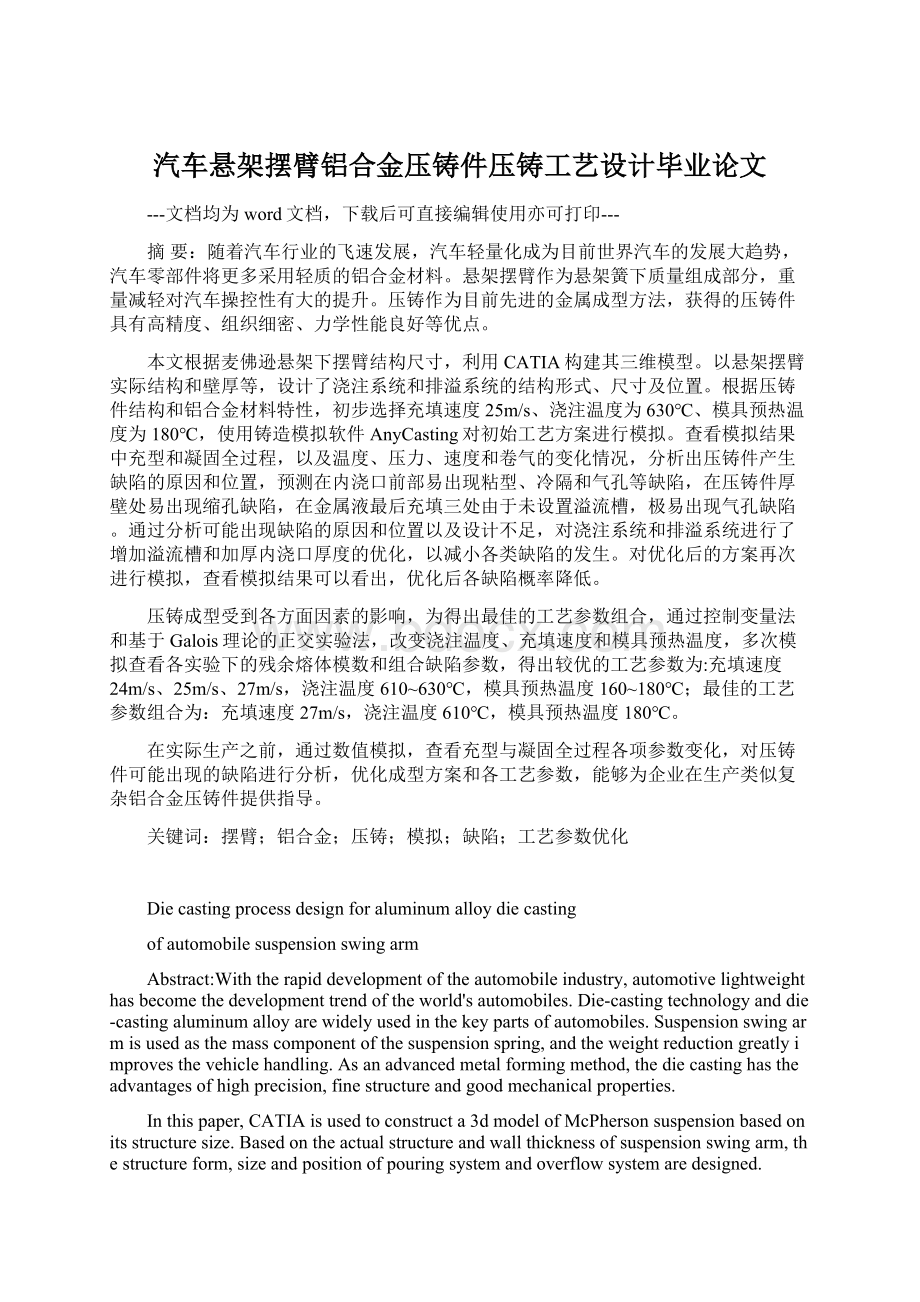
汽车悬架摆臂铝合金压铸件压铸工艺设计毕业论文
---文档均为word文档,下载后可直接编辑使用亦可打印---
摘要:
随着汽车行业的飞速发展,汽车轻量化成为目前世界汽车的发展大趋势,汽车零部件将更多采用轻质的铝合金材料。
悬架摆臂作为悬架簧下质量组成部分,重量减轻对汽车操控性有大的提升。
压铸作为目前先进的金属成型方法,获得的压铸件具有高精度、组织细密、力学性能良好等优点。
本文根据麦佛逊悬架下摆臂结构尺寸,利用CATIA构建其三维模型。
以悬架摆臂实际结构和壁厚等,设计了浇注系统和排溢系统的结构形式、尺寸及位置。
根据压铸件结构和铝合金材料特性,初步选择充填速度25m/s、浇注温度为630℃、模具预热温度为180℃,使用铸造模拟软件AnyCasting对初始工艺方案进行模拟。
查看模拟结果中充型和凝固全过程,以及温度、压力、速度和卷气的变化情况,分析出压铸件产生缺陷的原因和位置,预测在内浇口前部易出现粘型、冷隔和气孔等缺陷,在压铸件厚壁处易出现缩孔缺陷,在金属液最后充填三处由于未设置溢流槽,极易出现气孔缺陷。
通过分析可能出现缺陷的原因和位置以及设计不足,对浇注系统和排溢系统进行了增加溢流槽和加厚内浇口厚度的优化,以减小各类缺陷的发生。
对优化后的方案再次进行模拟,查看模拟结果可以看出,优化后各缺陷概率降低。
压铸成型受到各方面因素的影响,为得出最佳的工艺参数组合,通过控制变量法和基于Galois理论的正交实验法,改变浇注温度、充填速度和模具预热温度,多次模拟查看各实验下的残余熔体模数和组合缺陷参数,得出较优的工艺参数为:
充填速度24m/s、25m/s、27m/s,浇注温度610~630℃,模具预热温度160~180℃;最佳的工艺参数组合为:
充填速度27m/s,浇注温度610℃,模具预热温度180℃。
在实际生产之前,通过数值模拟,查看充型与凝固全过程各项参数变化,对压铸件可能出现的缺陷进行分析,优化成型方案和各工艺参数,能够为企业在生产类似复杂铝合金压铸件提供指导。
关键词:
摆臂;铝合金;压铸;模拟;缺陷;工艺参数优化
Die casting process design for aluminum alloy die casting
of automobile suspension swing arm
Abstract:
With the rapid development of the automobile industry, automotive lightweight has become the development trend of the world's automobiles. Die-casting technology and die-casting aluminum alloy are widely used in the key parts of automobiles. Suspension swing arm is used as the mass component of the suspension spring, and the weight reduction greatly improves the vehicle handling. As an advanced metal forming method, the die casting has the advantages of high precision, fine structure and good mechanical properties.
In this paper, CATIA is used to construct a 3d model of McPherson suspension based on its structure size. Based on the actual structure and wall thickness of suspension swing arm, the structure form, size and position of pouring system and overflow system are designed.
Preliminary selection pouring temperature is 630 ℃, the fill speed of 25 m/s, mould preheating temperature is 180 ℃, using AnyCasting casting simulation software for simulating the initial solution, and by looking at the filling process, solidification process changes, changes in temperature, pressure, velocity and volume air condition and so on, analyses the reasons of the casting defects and position, predict a self-adhesive is seen inside the front gate, cold insulation, porosity and other defects, causing shrinkage cavity defects in casting thick wall place, at the end of the liquid metal filling three places due to not set the overflow groove, appear easily blowhole defects. By analyzing the causes and locations of possible defects and the design deficiencies, the pouring system and overflow system are optimized by increasing the overflow groove and thickening the inner gate thickness to reduce the occurrence of various defects. The optimized scheme was simulated again, and the simulation results showed that the probability of each defect decreased after optimization.
Forming technology under the influence of the factors, obtains the best technological parameters for combination, through the control variable method and the orthogonal experiment method, based on the theory of the Galois change speed and mould preheating temperature, pouring temperature, filling simulation of the residual melt under check the experiment many times modulus and composite defect parameters, it is concluded that the optimal process parameters as follows:
the pouring temperature of 610~630 ℃, the fill speed 24 m/s, 25 m/s, 27 m/s, mould preheating temperature 160~180 ℃; The best combination of process parameters is:
pouring temperature 610℃, filling speed 27m/s, mold preheating temperature 180℃.
Before actual production, through numerical simulation, various parameter changes in the whole process of mold filling and solidification can be observed, possible defects of castings can be analyzed, and forming schemes and process parameters can be optimized, which can provide guidance for enterprises in the production of similar complex aluminum alloy die casting.
Key words:
Swing arm; Aluminum alloy; Die casting; Simulation; The defect;Processparameter optimization
第一章绪论
1.1压铸概述
压力铸造简称为压铸,是一种致密、无切屑的金属快速成型工艺[]。
实质是金属液在高压高速下充填进压铸型腔内,凝固成型后获得高精度、高致密性且力学性能优良的压铸件。
压铸的两大特点是高压和高速。
压铸生产中常用的压射比压为20~200MPa;常用充填速度为10~50m/s;由于高压高速充填,充填时间较短,一般为0.01~0.2s。
压铸与其他铸造工艺相比,有下列优点[]:
(1)质量精度高:
压铸件尺寸精度最高可达CT4级;表面粗糙度低;表层组织细密,力学性能优良;互换性好;对于复杂和薄壁类的也可以压铸。
(2)加工效率高:
国内使用最广泛的卧式冷压机每小时可压铸75~87次,机器生产效率快;压铸模可重复使用上百万次,寿命长;易实现大批量和一模多腔生产;易实现自动化和机械化。
(3)经济效益好:
由于压铸件质量精度高、表面质量优良,一般在压铸后无需再次加工或较少量加工就可使用,材料利用率高;压铸件价格与其他合金材料价格相比更便宜。
1.2压铸技术的发展及趋势
1.2.1压铸技术在国外的发展
在19世纪初期,由于印刷工业的兴起,也萌发和蕴育了压铸业的诞生。
从19世纪初期到中期的一段时间,开始出现将熔融状态的金属压入容器内制造简易零件。
到19世纪中期,陆续制造出各类用于压铸的机械设备。
1855年默根瑟勒(Mergen-thaler)以前人专利为基础,设计出印字压铸机,并在之后对该机器进行了优化改良,可用于生产简易的锌合金压铸件。
在20世纪初期,工业上开始大量使用压铸件,随后压铸机也迅速的发展。
1904年法兰克林(H.H.Franklin)公司压铸制造出汽车连杆轴承,开创了压铸件在汽车上的应用先例,压铸件应用领域由此从印刷工业逐渐转变为汽车工业;1905年多勒(H.H.Doehler)发明出多用型热室压铸机,该压铸机既能压铸锌合金也能压铸铅锡合金;随后瓦格纳(VanWagner)设计出适用于铝合金压铸的气压立式冷压机。
20世纪50年代开始出现大型压铸机,使压铸行业更快应用到更多新领域。
随着压铸工艺、压铸技术和压铸设备的发展,压铸合金的种类也在不断增多,也促进了压铸行业更加迅速的发展。
1.2.2压铸技术在国内