如何运用IE技术提升效率PPT文件格式下载.ppt
《如何运用IE技术提升效率PPT文件格式下载.ppt》由会员分享,可在线阅读,更多相关《如何运用IE技术提升效率PPT文件格式下载.ppt(108页珍藏版)》请在冰豆网上搜索。
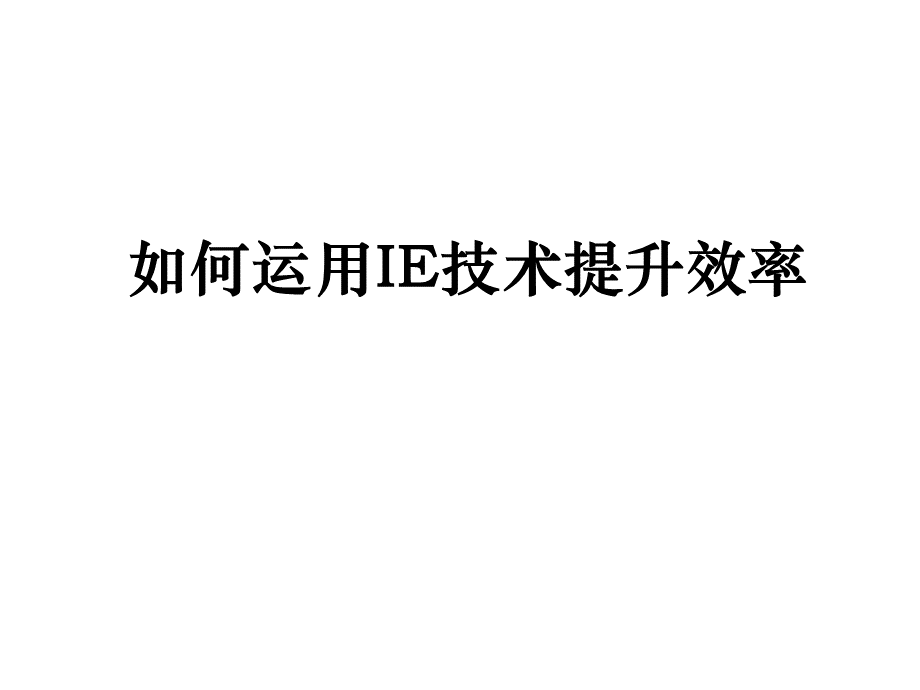
1、方法研究(改善工具):
程序分析作业分析动作分析2、时间研究(衡量标准):
作业标准和标准工时的测定,2、工业工程的原理,工作研究的实施步骤:
1、寻求最经济的工作方法(方法研究、工作改善);
2、工作方法、材料、工具及设备标准化;
3、确定标准工作时间.,3、工业工程的范畴,生物力学成本管理数据处理及系统设计工程经济设施规划与物流应用数学(运筹学、管理经济学、统计和数学应用等)组织规划与理论标准化及误差管理,9.生产规划与控制10.方法研究和作业测定价值工程ERP及物流系统厂区规划及生产线布置工业设计职业卫生与医学,4、工业工程在制造业中的应用,5、效率提升的基础与改善方向,1学会观察2深入分析3识别问题(连问5个为什么)4改善(针对根本问题),二、程序分析(ProcessAnalysis),1、程序分析定义程序分析,就是以原料、材料、零件,或者制品为对象,对工程如何的被进行,展开分析调查的方法。
是以“物的流动”为着眼点,设计或改善作业次序的分析手法。
是否有不必要的停滞搬运的次数是否太多搬运的距离是否太长搬运的方法是否有问题是否能同时实施加工及检查再检讨设备的配置工作的顺序作业的分担,2、程序分析的内容,二、程序分析(ProcessAnalysis),3、程序分析技巧,完成了什么?
(what)何处做?
(where)何时做?
(when)由谁做?
(who)如何做?
(how),为什么?
(why),要做这,是否必要?
要在此处做?
有无其他更合适之处?
要此时做?
有无更合适的时间?
由他做?
有无更合适的人去做?
要这样做?
有无更好的方法去做?
4、程序分析表(改善前),4、程序分析表(改善前),4、程序分析表(改善后),4、程序分析表改善后,5、改善的着眼点全体,全体的合计时间、搬运距离、以及所需人员与每一项工程所需的时间,从搬运距离以及所需人员看来,改善的重点在那儿呢?
(如属必要,可制作草拟图,以便找出重点)。
有没有欲罢不能的工程?
有没有可以同时进行的工程能否更换工程的顺序,以便减少工程数、所需时间、搬运距离,以及所需人员呢?
6、改善的着眼点加工,有否加工时间多的工程呢?
尤其是必需检查耗时的加工工程,再利用其它的分析手法(动作分析、时间分析等),看看是否能够改善。
能否提高设备的能力能否跟其它的工程一起进行改变工程顺序的话,是否能获得改善现在的生产单位数,是否适当?
7、改善的着眼点搬运,能否减少搬运的次数?
能否一面加工,一面运输?
(例如把工作运输输送带化,或者台车化,以便在其上面加工)?
能否缩短搬运距离?
能否改变作业场所的摆设,以便取消搬运工作?
能否采取加工、检查等组合方式,以便取消搬运?
能否增大搬运单位数量,以便减少次数?
搬运前后的上、下动作,是否很耗费时间?
搬运设备是否有改良的余地?
搬运活性指数,搬运方法系数值:
散置0装箱1架起2车上3运动中4活性系数=每次搬运系数和/搬运次数活性系数大于2.3为佳,8、改善的着眼点检查,能否减少检查的次数有没有能够省略的检查能不能一面加工,一面展开必要的检查吗?
换句话说,同时实施加工与检查,凭着二项的合并即可缩短工程数及合计时间,同时也可以节省搬运?
不曾以别的工程,实施质的检查及量的检查吧?
能够同时实施吗?
检查方法适切吗?
能否缩短时间?
9、改善的着眼点停滞,尽量的减少停滞的时间能否凭组合加工、检查场所的配置、而消除停滞呢?
尤其是滞留(D)是前后工程所需时间的不平衡所引起,只要实施尽量减少它的工程组合,即可消除滞留的现象。
能否尽量的缩短停滞时间?
10、改善的四原则,取消Eliminate,对程序图上的每一项工序都加以审查,确认其保留的必要性,凡可取消者一律取消,例如:
取消一切可以取消的工作内容、工作步骤、工作环节及作业动作(包括身体、手、脚)。
取消一切不安全、不准确、不规范的动作。
取消不方便或不正常的作业取消一切不必要的闲置时间,合并Combine,对程序图上的操作和检验项目,考虑相互合并的可能性,凡能合并者,在保证质量、提高效率的前提下予以合并,例如:
把必须突然改变方向的各个小动作合成一个连续的曲线动作。
把几种工具合并为一种多功能的工具。
把几道分散的工序合并为一道工序合并可能同时进行的动作,重排Rearrange,对程序图上的作业序列进行宏观分析,考虑重新排列的必要性和可能性,有时仅仅通过重排就可显著提高效率,例如:
重新排列工艺流程,使程序优化重新布置工作现场,使物流路线缩短重排流水线工位,消除薄弱环节重新安排作业组的分工,使工作量均衡,简化Simplify,这里既包括将复杂的流程加以简化,也包括简化每道工序的内容,例如:
减少各种繁琐程序,减少各种复杂性使用最简单的动作来完成工作简化不必要的设计结构,使工艺更合理作业方法力求简化运送路线,信息传递路线力求缩短,ValueStreamMapping价值流分析,11、线路分析,线路分析:
对现场布置及物料(另件、产品、设备)和作业者的实际流通路线进行分析,以达到改进现场布置和移动路线。
工装车间,毛坯库,剪床,剪床,剪床,料场,剪料工段,拔头锻柄工段,拔头机,旋转锤,三角锉拔头锻柄平面流程分析图,55米,106米,84米,70米,5米,3米,86米,实例:
重型机器工厂,装配车间,机1,机4,机2,机3,机5,总库,铸造车间,轻型机器厂,一般机器工厂,起重机,起重机,起重机,手推车,手推车,改进:
机1,机2,机3,机4,机5,机6,铸造车间,一般机器工厂,总库,滚子台,磨床,磨床,铣床,磨床,搓丝,车床,车床,车床,来自料堆,1,1,2,3,4,5,6,磨床,7,8,去半成品库,改进:
车床1,车床1,来自料堆,铣床2,车床3,磨床4,磨床5,磨床6,磨床7,搓丝8,去半成品库,节约面积,三、设施布置FacilityLayout,使物料搬运成本最小化空间的有效利用劳动力的有效利用消除瓶颈环节便于信息沟通,1、设施布置的目的,2、布置(LAYOUT)原则,3、流程路线经济原则,路线越短越好禁止“孤岛”减少停滞消除重复停滞消除交叉路线禁止逆行,4、工艺原则布置,5、产品原则布置,TaktTime:
27Secs,TaktTime:
27Secs,6、单元布置,四、作业分析,所谓工厂的作业,并非一个作业者从事一项工作,而是由人与人,人与机械,或者是机械与机械的组合进行的场合最多。
一般有以下的组合方式一个作业者:
一部机械一个作业者:
数部机械数个作业者共同进行作业的场合数个作业者:
一部机械数个作业者:
数部机械凭分析组合作业的时间经过,以便找出“人”或“机械”所造成的“闲荡”“空等”,藉此改善作业的方法。
人机配合分析案例研讨,请分析:
如何提高生产效率?
注:
人从一个机器走到另一个机器的时间是0.04分.,线平衡,LineBalancing,线平衡是对生产线的全部工序进行负荷分析,通过调整工序间的负荷分配使之达到能力平衡,最终提高生产线的整体效率。
这种改善工序间能力平衡的方法又称为瓶颈改善。
线平衡分析及瓶颈改善的主要目的是:
提高人员及设备的生产效率减少产品的工时消耗,降低成本减少在制品,降低在库实现单元化生产,提高生产系统的弹性,五、生产线平衡分析与瓶颈改善,某生产线的线平衡分析与瓶颈改善-1,例,工序,人数,正常作业时间,正常作业时间人数,1,1,20,20,2,1,18,18,3,1,29,29,4,1,25,25,5,1,19,19,合计,5,111,111,瓶颈工序,25,20,29,损失时间,作业时间,某生产线的线平衡分析与瓶颈改善-2,例,循环时间CT=29s,线平衡率=100%=76.55%,各工序时间总和,人数循环时间,平衡损失率=1-线平衡率=23.45%,【一般来说,平衡损失率在5%以内是可以接受的,否则就要进行改善】,线不平衡造成中间在库,降低整体效率,能力需求:
100件/H,例,瓶颈改善的方法,作业方法改善,作业拆解分割,改进工具夹具,提高设备效率,提高作业技能,调整作业人员,增加作业人员,瓶颈改善,合并微小动作,取消不必要动作,重排作业工序,简化复杂动作,六、JIT之切换效率改善,月度机型切换时间,月度总出勤时间,机型切换率=100%,机型切换效率=1-机型切换率,机型切换效率与切换方式、熟练程度、计划安排合理性等密切相关。
切换管理是工序管理的重要方面。
切换率越低越好,1、四种切换形态,材料切换(材料、零部件等),生产准备(整理、条件确认等),夹具切换(模具、刀具、夹具等),标准变更(技术标准、工艺程序等),2、快速切换的4个阶段,缩短一半,个位分钟,一触即发,零切换,n*10分钟,将切换时间缩短一半,切换时间缩短到9分59秒之内,3分钟内完成切换,1分钟内完成切换,3、快速切换的改善着眼点,减少切换时生产线停顿的时间停线时间越短越好,作业分离,内,外,变作业为作业,内,外,缩短外作业,缩短内作业,4、快速切换的改善思路,内作业,外作业,将转化为,设法将内作业转化为外作业,这样就直接减少了停线时间。
例:
模具安装后的行程调整(内作业)模具安装前的标准高度设定(外作业),内作业,内作业,缩短内作业时间设法将内作业的动作简单化。
外作业,外作业,缩短外作业时间设法将外作业的动作简单化。
缩短外作业时间对缩短切换时间没有直接帮助,却能节省工时,有利于集中力量做好内切换。
5、快速切换的实施法则,平行作业,手可动脚勿动,使用道具不用工具,尽量不用螺栓,不要取下螺栓