油罐制安工程施工方案0405Word格式.docx
《油罐制安工程施工方案0405Word格式.docx》由会员分享,可在线阅读,更多相关《油罐制安工程施工方案0405Word格式.docx(29页珍藏版)》请在冰豆网上搜索。
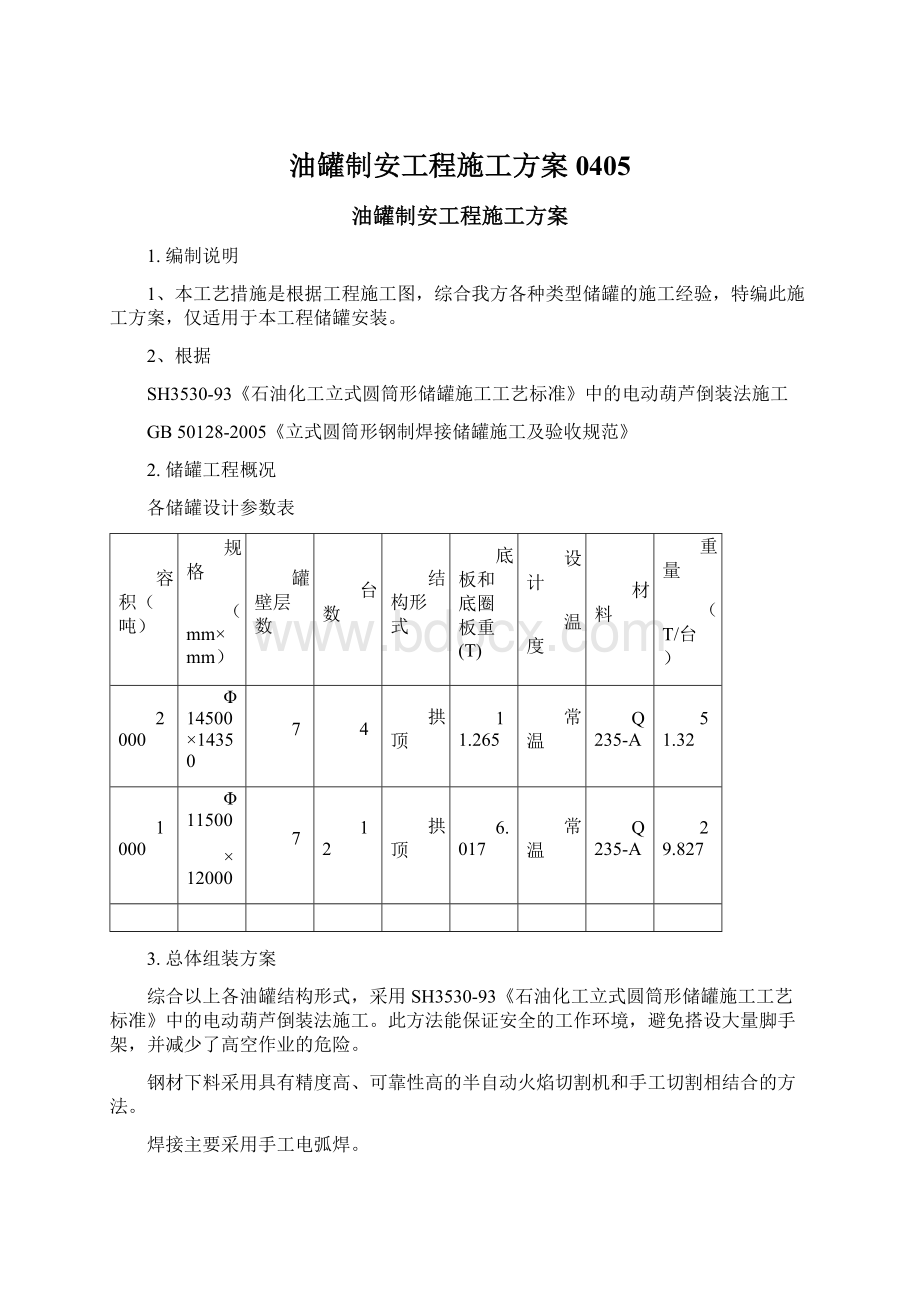
14350
7
4
拱顶
11.265
常温
Q235-A
51.32
1000
Φ11500
×
12000
12
6.017
29.827
3.总体组装方案
综合以上各油罐结构形式,采用SH3530-93《石油化工立式圆筒形储罐施工工艺标准》中的电动葫芦倒装法施工。
此方法能保证安全的工作环境,避免搭设大量脚手架,并减少了高空作业的危险。
钢材下料采用具有精度高、可靠性高的半自动火焰切割机和手工切割相结合的方法。
焊接主要采用手工电弧焊。
施工程序见下图。
4.施工方法
1、施工准备:
1)材料验收
工程所用材料的质量合格与否是决定工程质量好坏的关键,也是交工验收的主要内容之一。
所以,材料验收是施工生产不可缺少的一个重要步骤。
材料验收及管理主要包括以下几项内容:
(1)资料检查
储罐所选用的材料(钢板、钢管及其它型钢)、附件、设备等必须具有相应的合格证明书。
当无质量证明书或对质量证明书有疑问时,应进行复验,合格后方可使用。
(2)外观检查
对储罐所用的钢板,严格按照规范标准GB6654-1996《压力容器用钢板》规定的相应要求进行验收,逐张进行外观检查,其表面质量、表面锈蚀减薄量,划痕深度等应符合GB50128-2005的有关规定。
(3)焊接材料验收
焊接材料应具有质量合格证,焊条质量合格证书应包括熔敷金属的化学成分和机械性能,低氢型焊条还应包括熔敷金属的扩散氢含量。
2)技术准备:
(1)认真做好设计交底和图纸会审工作。
(2)熟悉图纸和资料,编制切实可行的施工方案。
(3)详细向施工班组进行技术交底。
3)现场准备:
(1)平整施工现场,选定材料、构件存放场地。
(2)接通水源、电源,按施工平面布置图放置焊机房及工具、休息室。
(3)在预制厂铺设预制平台。
4)工装卡具和计量器具准备:
(1)制作罐壁板放置胎具。
(2)制作工装卡具。
(3)使用的计量器具均在周检期内。
2、罐体预制:
在施工生产中,对罐体的许多构件和材料安装前必须进行预制加工,如罐底边缘板成型、罐壁板坡口及圆弧加工以及各种弧型构件(加强圈、抗风圈、包边角钢等)等。
有些构件为了成型规范、减少高空作业、提高工效、保证工程质量也需要在专用平台上进行预制加工,如劳动平台、盘梯、滚动扶梯等。
1)一般要求
(1)油罐施工用弧形样板的弦长不得小于2m,直线样板的长度不得小于1m,测量焊缝角变形的弧形样板弦长不得小于1m。
(2)罐底边缘板、罐壁板的预制切割采用半自动火焰切割机。
钢板边缘加工面应平滑,不得有夹渣、分层、裂纹及熔渣等缺陷,火焰切割坡口产生的表面硬化层应打磨清除。
(3)所有预制构件在保管、运输及现场堆放时应采取有效措施防止变形、损伤和锈蚀。
2)底板预制
根据钢板到货规格及规范要求放大罐底直径,按照设计罐底排板图,确定每张板的几何尺寸,按设计要求加工坡口,切割加工后的每张壁板都应做好标识,并复检几何尺寸、做好自检记录。
预制弓形边缘板及不规则板,钢板切割采用半自动火焰切割机和手工切割相结合的切割方法。
中幅板采用半自动火焰切割机切割。
预制好的罐底板应做好标识,然后进行防腐。
(1)罐底板的主要预制工序为:
准备工作→材料验收→划线→复验→切割→打磨→下一道工序。
(2)底板预制应符合下列规定:
a、罐底的排版直径,应按设计直径放大0.1%—0.2%。
b、排板图现场根据钢板供货状态绘制。
c、中幅板尺寸允许偏差应符合下表规定:
中幅板尺寸允许偏差表
测量部位
板长AB(CD)
宽度AC、BD、EF
±
1.5mm
长度AB、CD
2mm
对角线之差│AD-BC│
≤3mm
直线度
AC、BD
≤1mm
AB、CD
≤2mm
d、弓形边缘板的对接接头,宜采用不等间隙,外侧间隙e1宜为6-7mm,内侧间隙e2宜为8—12mm。
如图所示:
弓形边缘板的对接接头间隙
e、弓形边缘板的尺寸允许偏差应符合下表弓形边缘板的尺寸偏差规定:
弓形边缘板的尺寸偏差
弓形边缘板尺寸允许偏差
允许偏差(mm)
2
≤3
f、弓形边缘板应在坡口两侧100mm范围按《压力容器用钢板超声波探伤》有关现行规定进行超声波检查,Ⅲ级合格;
坡口表面进行磁粉或渗透检查。
3)壁板预制
(1)罐壁板的预制工序为:
准备工作→材料验收→钢板划线→复验→切割→坡口打磨→滚板成型→检查、记录→准备安装组对。
(2)罐壁板预制要严格按照图纸要求,采用半自动火焰切割机进行坡口加工,其它几何尺寸要按现场材料进行罐壁排板计算确定。
同时要做好预制检查记录。
(3)壁板预制前严格按实际排版图下料施工(排板图现场根据业主钢板供货状态绘制),并应符合下列规定:
a、底圈壁板的纵向焊缝与罐底边缘板对接焊缝之间的距离不得小于200mm。
b、罐壁开孔接管或开孔接管补强板外缘与罐壁纵向焊缝之间的距离,不得小于200mm,与环向焊缝的距离不得小于100mm。
c、包边角钢对接接头与壁板纵向焊缝之间的距离,不得小于200mm。
d、壁板尺寸允许偏差应符合下表壁板尺寸允许偏差表规定:
壁板尺寸允许偏差表
1.5mm
≤1mm
≤2mm
e、壁板卷制后,应在平台上用样板检查,垂直方向上用直线样板检查,其间隙不得大于1mm,水平方向上用弧形样板检查,其间隙不得大于4mm。
f、壁板滚圆时,吊车配合要注意下滚床时防止外力引起不可回塑性变形。
滚制后,应立置在平台上检查,合格后,再放在准备好的成型胎具上。
壁板专用胎具如图所示:
4)罐顶预制
(1)罐顶板在预制前应绘制排板图,并应符合下列规定:
a、相邻两块顶板焊缝不得小于200mm。
b、瓜皮板本身的拼装,可采用对接接头或搭接接头(一般采用对接接头),当采用搭接接头时,搭接宽度不得小于5倍板厚。
c、排版图应根据材料规格和瓜皮板的几何尺寸精确确定,并符合排板规定。
(2)顶板预制:
按配板图放大样,制作下料样板,采用样板下料。
在地样上将各种梯形板料组焊成扇形面。
板面焊接采用手工双面焊。
为了减少材料的浪费,采用卷开平钢板,材料供货长度可根据排板确定。
(3)筋板预制:
经向长条弧筋板是用数段扁钢煨制成双曲面弧状后在地样上拼焊而成。
纬向短条双曲弧筋板用各种展开长度的扁钢煨制成双曲弧状,每种筋板用两块样板检验双曲煨弧质量。
(4)顶板和筋板组焊:
组焊前,应制作组装胎架。
组装中先将顶板吊放到组装胎架(如下图所示)上,用样板在面板上划出组装标记线,并用卡具或重物压在面板上,使顶板面胎架贴严保证弧形曲率,对板面局部凸起也可用木锤打击。
先把经向长筋板就位点焊,再将各纬向短筋板就位点焊,完成顶板面与筋板组装。
筋板和顶板焊接应在胎架上进行,采用多焊工均布同时进行施焊作业。
加强筋用弧形样板检查其间隙不得大于2mm,加强筋与顶板相焊时,应采取防变形措施。
(5)加强筋采用对接接头,应加垫板,并且应全焊透。
预制完毕的顶板应储放在刚性胎架上,运输时随同储放架装车,运至安装现场交付安装。
弧度同罐顶板
L稍长于单块顶板
胎架示意图
5)附件预制
(1)材料检查
a、材料上的标记与材料质量合格证明书上标记一致。
b、材料表面质量检查:
执行相应的材料标准中的有关规定。
(2)划线
按施工图规定的尺寸进行划线,涂清标记,并进行材料标记移植。
(3)按线切割下料(火焰切割或机械切割)。
清除熔渣或毛刺。
(4)各件加工成型
a、按施工图中各件尺寸。
b、加强圈、包边角钢等弧形构件加工成型后,用弧形样板检查,其间隙不得大于2mm。
放在平台上检查,其翘曲变形不得超过构件长度的0.1%,且不得大于4mm。
c、热煨成型的构件,不得有过烧、变质现象。
其厚度减薄量不应超过1mm。
3、罐体安装
1)基础验收
施工前应组织有关施工人员按基础施工图,对基础中心的位置、标高、直径、坡度、环梁等进行检查,应符合质量验收标准。
(1)基础中心标高允许偏差为±
20mm。
(2)基础水平度不得超标,特别是基础环梁处边缘板铺设范围内的水平度要严格控制,以免影响罐底铺设和罐壁板的安装水平度。
具体要求是:
基础环梁,每10m弧长内任意两点的高差不得大于6mm,整个圆周长度内任意两点的高差不得大于12mm;
基础验收要求见下表
编号
内容
允许偏差
1
中心点坐标≤12
20
基础中心标高
3
径向平整度从中心拉线测量表面凹凸度
≤25
罐壁圆周
每隔10m周长内任意两点高差
≤6
方向的平整度
整个圆周长度内任意两点高差
≤12
沥青砂层表面应平整密实,无突出的隆起、凹陷及贯穿裂纹,沥青砂表面检查、测量如下表:
沥青砂层表面标高测量位置
同心圆直径
D/5
2D/5
3D/5
4D/5
等份测点数
8
16
24
32
同一圆周上标高差
≤12㎜
注:
D为罐体直径
(3)在0°
、90°
、180°
、270°
方位设置标记,标记定位要准确、清晰。
2)罐底组装
基础验收合格后,在基础上确定罐的具体方位,划出“十”字中心线,作为罐底铺设的基准线。
依据罐底排板图,在基础上划出各底板的位置线,然后开始罐底铺设。
罐底板从中心向四周逐张进行铺设。
罐底铺设完毕,点焊固定后,开始焊接。
焊接严格按焊接工艺的规定进行。
弓形边缘板的焊接应先焊外侧300mm,焊完经无损检测合格后磨平。
边缘板剩余焊缝以及中幅板与边缘板连接的焊缝,应在罐壁施工完毕,罐底与罐壁大角缝施焊结束后,再进行焊接。
焊接时应先焊边缘板对接缝,然后焊收缩缝,收缩缝的初层焊接应由数对焊工均布,沿同一方向跳焊或退焊,以减少应力集中。
(1)罐底组装要求:
a、根据设计要求,制定底板排版图
b、底板铺设前其下表面应涂刷防腐涂料,每块底板边缘50mm内不刷涂料。
(2)底板铺设
底板铺设采用几台吊车同时铺设。
施工时先铺设中心定位板,再向两侧铺设中幅板,底板采用铺设一张,就位固定一张的方法。
具体工序为:
施工准备→罐底放线→罐底中心定位板→中间幅板铺设→两侧幅板和异形板铺设→罐底边缘板铺设。
a、罐底放线:
以基础中心和四个方位标记为基准,画十字中心线,并确定基准线做出永久标记。
划出底板外圆周线,考虑焊接收缩量,底板外圆直径(2R1)应比设计直径放大0.1%—0.2%。
该板上画出底板中心点和中心线,打上洋冲眼做出明显标记。
铺设顺序如图所示。
铺设的大顺序为:
以中心线向四周辅设。
b、中幅板安装
铺设中心定位板(中心的一块底板),并在该板上画出底板中心点和中