克劳斯硫磺回收技术的基本原理Word格式文档下载.docx
《克劳斯硫磺回收技术的基本原理Word格式文档下载.docx》由会员分享,可在线阅读,更多相关《克劳斯硫磺回收技术的基本原理Word格式文档下载.docx(26页珍藏版)》请在冰豆网上搜索。
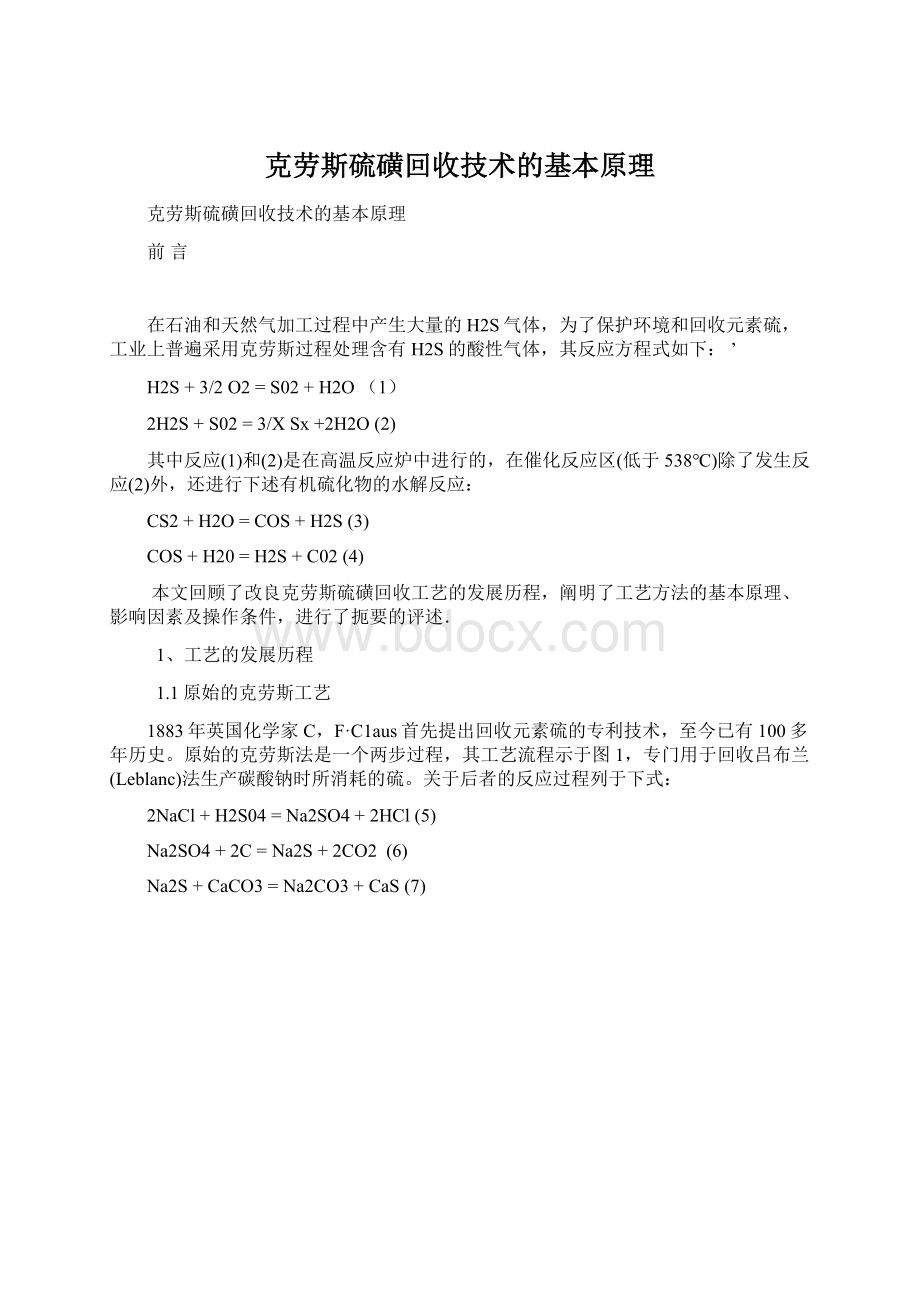
1.1原始的克劳斯工艺
1883年英国化学家C,F·
C1aus首先提出回收元素硫的专利技术,至今已有100多年历史。
原始的克劳斯法是一个两步过程,其工艺流程示于图1,专门用于回收吕布兰(Leblanc)法生产碳酸钠时所消耗的硫。
关于后者的反应过程列于下式:
2NaCl+H2S04=Na2SO4+2HCl(5)
Na2SO4+2C=Na2S+2CO2(6)
Na2S+CaCO3=Na2CO3+CaS(7)
为了回收元素硫,第一步是把CO2导入由H20和CaS(碱性废料)组成的液浆中,按上述反应式得到H2S,然后在第二步将H2S和O2混合后,导入一个装有催化剂的容器,催化剂床层则预先以某种方式预热至所需要的温度,按←CaS(固)+H2O(液)+C02(气)=CaC03(固)十H2S(气)(8)
反应式(9)进行反应。
反应开始后,用控制反应物流的方法来保持固定的床层温度.显然此工艺只能在催化剂上以很低的空速进行反应。
据报导,
H2S+1/2O2=1/XSx+H2O(9)
如果使用了水合物形式的铁或锰的氧化物,就不需要预热催化剂床层即可以开始反应,然而由于H2S和O2之间的反应是强烈的放热反应,而释放的热量又只靠辐射来发散,因此限制了克劳斯窑炉只能处理少量的H2S气体。
为了使产率达到80~90%,每小时在每体积催化剂上只能处理2~3体积的H2S气体;
为了加快热量散发从而增加处理容量,亦曾试图在窑炉中设置冷却盘管,使冷的废气循环通过窑炉,结果并不成功,此后尽管又进行了种种尝试,但在二十世纪三十年代以前,该法并没有在工业领域得到推广,其原因是如上所述的那样,将H2S和O2在反应器内直接进行氧化反应,生成的大量反应热无法移出,致使反应器内温度猛升,为了控制反应温度,只得采用相当低的空速,故因生产能力低下而阻碍了该法的工业应用.
1.2改良克劳斯工艺
克劳斯法早期的一种改型是I·
G·
Claus工艺(1932年),该法经锅炉燃烧一部分H2S,然后使生成的S02再与未反应的H2S化合.由于在燃烧生成S02时已释放出大量的反应热,因而在其后的催化反应中释放的反应热大为减少,不会因超温而造成催化剂破坏,这就是所谓的“分流法”.
1938年德国法本公司(I·
FarbenindustrieAG)对克劳斯法工艺作了重大改进,不仅显著地增加了处理量,也提出了一个回收以前浪费掉的能量的途径。
其要点是把H2S的氧化分为两个阶段来完成。
第一阶段称为热反应阶段,有1/3体积的H2S在蒸汽锅炉内被氧化成为S02,示于反应方程式
(1),同时放出大量的反应热以水蒸汽的形式予以回收;
第二阶段称为催化反应阶段,即剩余的2/3体积的H2S在催化剂上与生成的S02继续反应而成为元素硫,示于反应方程式
(2)。
改良克劳斯法的工艺流程见于图2,对照图1和图2可以看出,由于设置了废热回收设备,炉内反应所释放的热量约有80%可以回收,而且催化转化反应器的温度也可以
凭借控制进口过程气的温度加以调节,这样就基本上排除了反应器温度控制难的问题,同时也大幅度提高了装置的处理量,从而奠定了现代硫磺回收工艺的基础。
“直流法”或“部分燃烧法”的问世是克劳斯工艺划时代的重大进展,此后克劳斯法才在工业上得到广泛应用。
随着生产发展的需要,改良克劳斯工艺本身又作了不少改进,1938年以后的主要改进是相继增加了更多的催化反应器,同时在各反应器之间除去硫磺和热量,使反应平衡向着更高的硫磺产率方向移动。
1.3现代改良克劳斯工艺
经过半个多世纪的演变,改良克劳斯法在催化剂、设备、材质和流程以及控制方法等各方面经过不断的研究改进,才发展成为今天这样简单可靠、经济有效并得到普遍应用的硫回收方法。
根据原料气中H2S的含量不同,现代改良克劳斯工艺大致可以分为三种基本型式,即部分燃烧法、分流法和直接氧化法,无论哪种型式都是由高温反应炉、冷凝器、再热炉和催化转化反应器等一系列容器所组成。
这些型式之间的区别是在一级催化转化反应器前面产生S02的方法不同。
在这三种方法的基础上,各自再辅以诸如预热、补充燃料气等不同的技术措施,又可派生出各种不同变型,其大致情况如表1所示。
应予指出,表中所示的划分范围井非十分严格,关
表1各种工艺方法及适用范围
原料气中H2S含量%(V)
工艺方法
50~100
40~50
25~40
15~25
﹤15
部分燃烧法
带有原料气和/或空气预热的部分燃烧法
分流法
带有原料气和/或空气预热的部分分流法
直接氧化法和其它处理贫酸性气的特殊方法
键是反应炉内燃烧H2S所释放的热量必须保证维持稳定的火焰,否则装置将无法正常运行。
1.3.1部分燃烧法
全部原料气都进入反应炉,而空气的供给量仅够供原料气中1/3体积的H2S燃烧生成S02,从而保证过程气中H2S:
S02为2:
l的化学计量分子比要求。
反应炉内虽不存在催化剂,但H2S仍能有效地转化为硫蒸汽,其转化率随反应炉的温度和压力不同而异,一般在炉内H2S的转化率可达到60%~75%,其余的硫化合物将继续在催化转化反应器进行如反应
(2)、(3)、(4)所示的催化反应。
催化转化反应器的操作温度大致控制在比过程气中气态硫的露点温度高20~30℃,二级以后催化转化反应器的H2S转化率约为20~30%,因此部分燃烧法装置其H2S转化率可以达到90~98%水平。
目前在工业上有几种常用的部分燃烧法工艺流程。
图3为外掺合式部分燃烧法的原则工艺流程图。
此流程主要特点是从废热锅炉出口处引出一股高温过程气掺合到一级和二级转化反应器的入口气流中,以达到使过程气再热的目的。
外掺合式流程的优点是设备简单、平面布局紧凑、温度调节
灵活;
缺点是高温掺合管制作用难,掺合阀腐蚀严重,对总硫转化率有所影响。
图4为内掺合—换热式部分燃烧法的原则工艺流程图。
此流程的主要特点是把掺合管(又称内旁通管)和废热锅炉的炉管组合在一起,掺合过程在废气锅炉的尾部进行,利用掺合管出口阀开度不同来调节一级催化转化反应器的过程气温度,而二级催化转化反应器的入口温度则用自热式换热器来调节。
内掺合的原理与外掺合相同,故它们的优、缺点也类似,只是内掺合式更节省占地面积。
但是,由于掺合管设置在废热锅炉内部,一旦发生意外故障,检修比较困难。
图5为酸性气再热炉式部分燃烧法。
此流程的特点是设置一系列再热炉作为过程气的调温手段。
再热
炉以酸性气为燃料,所需空气量仍以进炉酸气中l/3体积的H2S转化为SO2的计算量为准,炉内温度则以进酸气量的多少来控制。
至于再热炉,其本身也有多种形式,除酸气再热炉外,常见的还有燃料气再热炉和管式再热炉,前者是以天然气或燃料气为再热炉燃料,把燃烧后的烟气掺入过程气以调节其温度,后者是以管式炉间接加热的方式来调节过程气的温度。
1.3.2分流法
原料气中H2S含量在25~40%(V)范围内推荐使用分流法。
该法先将
原料气中1/3体积的H2S送入高温反应炉,配以适量的空气燃烧而全部生成SO2,其过程如反应
(1)所示,生成的S02气体与其余2/3的H2S混合后在催化转化反应器内进行低温催化反应。
分流法一般都采用两级催化转化,其总硫转化率大致为88~92%,适宜规模较小的硫磺回收装置。
图6为掺合—换热式分流法的原则工艺流程图。
此流程的特点是把上面所述的掺合与换热两种再热手段分别应用于分流法。
1.3.3直接氧化法
直接氧化法就其实质而言是原始克劳斯法的一种形式。
原料气中H2S含量在2~15%(V)范围内推荐使用此法。
直接氧化法的特点是不设置高温反应炉,而是将原料气预热至适当的温度,再与空气加以混合后直接送入催化转化反应器,按反应式
(1)和
(2)进行低温催化反应,所需配入的空气量仍为l/3体积H2S完成燃烧生成SO2所需的量。
图7为直接氧化法的原则工艺流程图。
另外,根据酸性气中是否含有NH3,还可分为不烧NH3流程和烧NH3流程。
若NH3体积浓度<
2%,推荐采用不烧NH3流程,此时两种酸性气所需全部空气量都进入酸气高温反应炉第一段,操作中可调节进入第一段和第二段的酸性气的流量,以确保尾气中H2S与S02的比率为2:
1。
目前国内已有处理NH3体积浓度为17%的操作经验,而且可处理NH3体积浓度高达30%的酸性气。
2、工艺的基本原理
改良克劳斯法硫磺回收工艺的基本原理可简略地用上文中化学反应方程式
(1)、
(2)、(3)和(4)来表示。
现以图8所示部分燃烧法工艺为例予以说明,在图8中,酸性气中的H2S转化为元素硫是酸性气在反应炉内的高温反应和在反应器内的低温催化反应中共同完成的。
在反应炉内H2S氧
化为元素硫的高温热反应分两部进行,其中1/3的H2S参与反应方程式
(1)所示的第一步反应,与化学计量的空气在900~1300℃之间进行燃烧,经
过自由火焰部分氧化后,H2S被转化成S02和H20;
剩余的2/3的H2S再与S02进行反应方程式所示的第二步反应生成硫和水。
在高温热反应条件下,硫元素基本上以Sl和S2形态存在,燃烧后的含硫混合物进入废热锅炉冷却到350℃左右,同时产生中压饱和水蒸汽送入蒸汽管线;
从废热锅炉出来的混合气进入一级冷凝器,冷却到150~160℃,产生的液硫以S8和S6形态从一级捕集器底部进入液硫储罐,同时产生水蒸汽进入低压管网,再热后的工艺过程气则进入二至三个绝热反应器进行低温催化反应。
鉴于CS2和COS的水解反应受动力学过程所控制,高温有利于有机硫化物水解反应的进行,而H2S与SO2的克劳斯反应受热力学平衡所控制,低温有利于生成元素硫和水的反应进行,因此第一反应器床层的操作温度一般控制在320℃左右,第二和第三反应器床层的操作温度大致控制在260℃和220℃,比过程气中的气态的露点温度高20~30℃,采用逐级降低温度的措施强制反应向右进行,同时在反应器间采用冷凝的方法连续不断地回收液态硫。
工业实践表明,在反应炉能达到的高温下,—般炉内H2S转化率可以达到60~75%,若采用二级克劳斯工艺装置总硫转化率约为92~95%,三级克劳斯工艺最高可以达到98%水平。
3、工艺的化学反应
克劳斯硫磺回收工艺过程尤其是高温反应炉内的化学反应非常复杂,如果用纯的H2S气体作为原料气,又配入纯O2一起在高温反应炉内燃烧,则化学反应基本上可以用图9来形象表示,反应后的过程气中仅含有H2S、SO2、H2O及不同形态的硫分子。
然而在工业酸性气中除了H2S外,通常还含有CO2、H2O、烃类、NH3等,因此如图10所示的那样,实际的化学反应十分
复杂,使反应后过程气中的组分也相应的变复杂了。
表2为克劳斯反应炉内可能出现的基本化学反应,表3、表4和表5则分别为可能发生或消耗CO、H2的反应和COS的副反应及CS2的副反应,可以看出工业克劳斯过程尤其是反应炉内的化学反应相当的错综复杂.
表2高温反应炉内的主要反应*
反应
(摩尔)
△F①,kJ