外壳注塑模具设计毕业论文设计Word格式文档下载.docx
《外壳注塑模具设计毕业论文设计Word格式文档下载.docx》由会员分享,可在线阅读,更多相关《外壳注塑模具设计毕业论文设计Word格式文档下载.docx(24页珍藏版)》请在冰豆网上搜索。
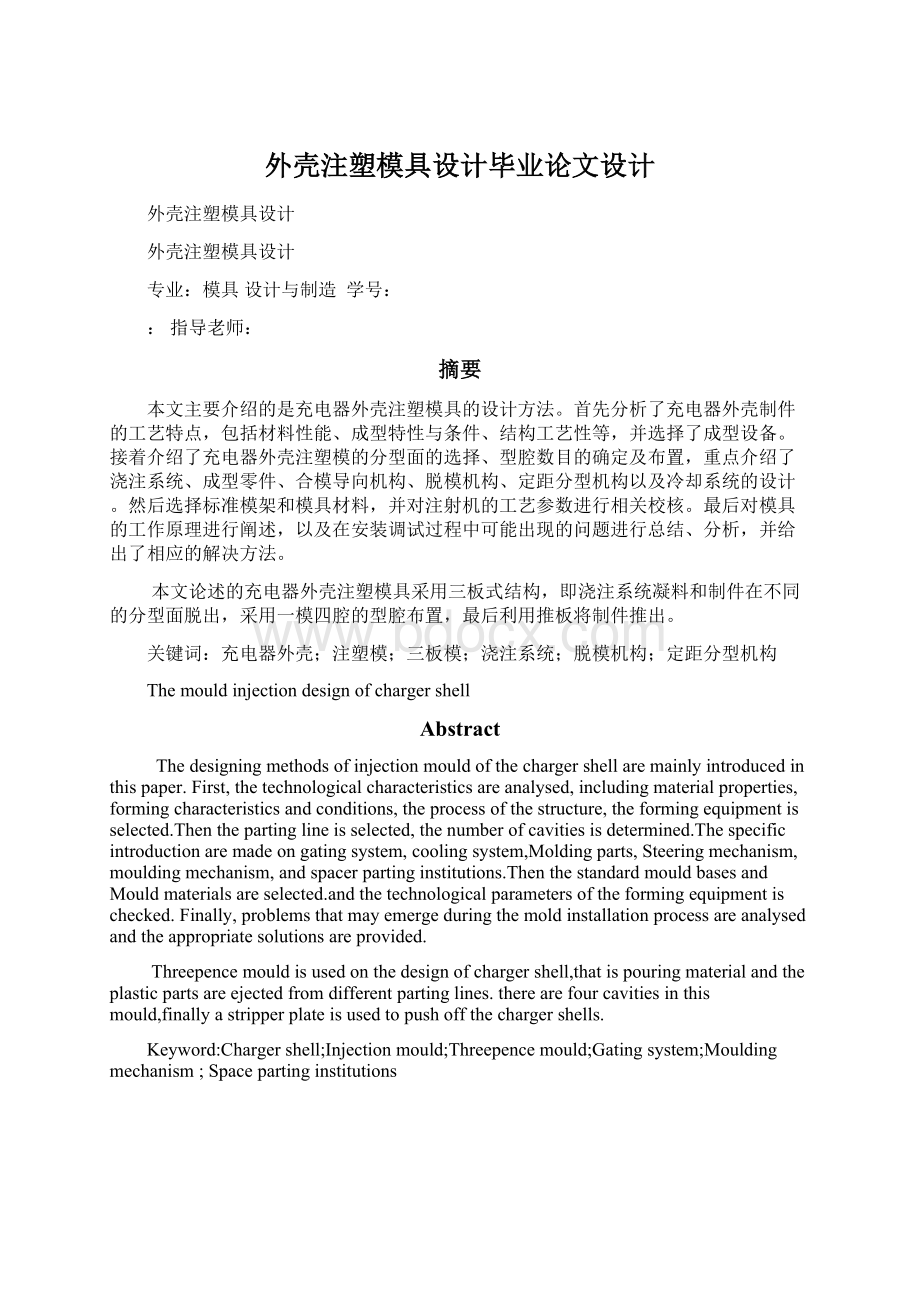
然后选择标准模架和模具材料,并对注射机的工艺参数进行相关校核。
最后对模具的工作原理进行阐述,以及在安装调试过程中可能出现的问题进行总结、分析,并给出了相应的解决方法。
本文论述的充电器外壳注塑模具采用三板式结构,即浇注系统凝料和制件在不同的分型面脱出,采用一模四腔的型腔布置,最后利用推板将制件推出。
关键词:
充电器外壳;
注塑模;
三板模;
浇注系统;
脱模机构;
定距分型机构
Themouldinjectiondesignofchargershell
Abstract
Thedesigningmethodsofinjectionmouldofthechargershellaremainlyintroducedinthispaper.First,thetechnologicalcharacteristicsareanalysed,includingmaterialproperties,formingcharacteristicsandconditions,theprocessofthestructure,theformingequipmentisselected.Thenthepartinglineisselected,thenumberofcavitiesisdetermined.Thespecificintroductionaremadeongatingsystem,coolingsystem,Moldingparts,Steeringmechanism,mouldingmechanism,andspacerpartinginstitutions.ThenthestandardmouldbasesandMouldmaterialsareselected.andthetechnologicalparametersoftheformingequipmentischecked.Finally,problemsthatmayemergeduringthemoldinstallationprocessareanalysedandtheappropriatesolutionsareprovided.
Threepencemouldisusedonthedesignofchargershell,thatispouringmaterialandtheplasticpartsareejectedfromdifferentpartinglines.therearefourcavitiesinthismould,finallyastripperplateisusedtopushoffthechargershells.
Keyword:
Chargershell;
Injectionmould;
Threepencemould;
Gatingsystem;
Mouldingmechanism;
Spacepartinginstitutions
第一章绪论
1.1选题的依据及意义
随着现代制造技术的迅速发展、计算机技术的应用,在玩具产业中模具已经成为生产各种玩具不可缺少的重要工艺装备。
特别是在塑料产品的生产过程中,塑料模具的应用及其广泛,在各类模具中的地位也越来越突出,成为各类模具设计、制造与研究中最具有代表意义的模具之一。
而注塑模具已经成为制造塑料制造品的主要手段之一,且发展成为最有前景的模具之一。
注射成型是当今市场上最常用、最具前景的塑料成型方法之一,因此注塑模具作为塑料模的一种,就具有很大的市场需求量。
所以我选充电器注塑模具设计作为我毕业设计的课题。
本课题应用性强,涉及的知识面与知识点较多,如注塑成型、模具设计、三维造型、运动仿真以及二维三维软件的应用。
通过本课题的设计,将会在下述基本能力上得到培养和锻炼
(1)塑料件制品涉及及成型工艺的选择
(2)一般塑料件制品成型模具的设计能力(3)塑料制品质量分析及工艺改进、塑料模具结构改进设计的能力(4)掌握模具设计常用的商业软件(proe4.0)及同实际设计的结合的能力(5)使自己在文档组织与检索方面的能力得到提高(6)掌握写论文的一般步骤及格式方法,同时提高自己的学习、思考、解决问题的能力,因为注塑模具对我来说是一个新的领域。
1.2国外研究现状及发展趋势
近年来我国的模具技术有了很大的发展,在大型模具方面,已能生产大屏彩电注塑模具、大容量洗衣机全套塑料模具以及汽车保险杠和整体仪表板等塑料模具。
塑料模具方面,已能生产照相机塑料件模具、多型腔小模数齿轮模具及塑封模具。
在成型工艺方面,多材质塑料成行模、高效多色注塑模、镶件互换结构和抽芯脱模机构的创新业取得了较大进展。
气体辅助注射成形技术的使用更趋成熟。
热流道模具开始推广,有些单位还采用具有世界先进水平的高难度针阀式热流道模具。
当前国外用于注塑模具方面的先进技术主要有以下几种:
(1)热流道技术它是通过加热的办法来保证流道和浇口的塑料保持熔融状态。
由于在流道附近或中心设有加热棒和加热圈,从注塑机喷出口到浇口的整个流道都处于高温状态,使流道中的塑料保持熔融,停机后一般不需要打开流道取出凝料,再开机时只需加热流道到所需温度即可。
这一技术在大批量生产塑件、原材料较贵和产品质量要求较高的情况下尤为适用。
热流道注塑成型技术应用围很广,基本上,适用于冷流道模具加工的塑料材料都可以使用热流道模具加工,许多产品如手机壳、按键、面板、尺寸要求精密的机芯部件等都是采用热流道技术成型。
一个典型的热流道系统一般由如下几大部分组成:
(1)热流道板(MANIFOLD);
(2)喷嘴(NOZZLE);
(3)温度控制器;
(4)辅助零件。
(2)气体辅助注射成形技术它是向模腔中注入经准确计量的塑料熔体,在通过特殊的喷嘴向熔体中注入压缩气体,气体在熔体沿阻力最小的方向前进,推动熔体充满型腔并对熔体进行保压,当气体的压力、注射时间合适的时候,则塑料会被压力气体压在型腔壁上,形成一个中空、完整的塑件,待塑料熔体冷却凝固后排去熔体的气体,开模退出制品。
气体辅助注射成形技术的关键就是怎么合理的把握注入熔融的塑料的时间与充人气体的时间的配合。
气体辅助注射可以应用在除特别柔软的塑料以外的任何热塑性塑料和部分热固性塑料。
应用气体辅助注塑成型技术,可以提高产品强度、刚度、精度,消除缩影,提高制品表面质量;
降低注射成型压力以减小产品成型应力和翘曲,解决大尺寸和壁厚差别较大产品的变形问题;
简化浇注系统和模具设计,减少模具的重量.减少塑件产品的重量,减少成型时间以降低成本和提高成型效率等。
气体辅助成形周期可分为如下六个阶段:
塑料熔体填充阶段、切换延迟时间、气体注射阶段、保压阶段、气体释放阶段、推出阶段。
(3)共注射成形技术它是使用两个或者两个以上注射系统的注塑机,将不同品种或者不同色泽的塑料同时或者先后注射进入同一模具的成形方法。
国使用的多为双色注塑机。
采用共注射成形方法生产塑料制品时,最重要的工艺参数是注射量、注射速度和模具温度[1]。
(4)反应注射成形技术它是将两种或者两种以上既有化学反应活性的液态塑料(单体)同时以一定压力输入到混合器进行混合,在将均匀混合的液体迅速注入闭合的模具中,使其在型腔发生聚合反应而固化,成为具有一定形状和尺寸的塑料制品通常这种成形过程称之为RIM。
在制造方面,CAD/CAM/CAE技术的应用上了一个新台阶,一些企业引进CAD/CAM系统,并能支持CAE技术对成形过程进行分析。
近年来我国自主开发的塑料膜CAD/CAM系统有了很大发展,如北航华正软件工程研究所开发的CAXA系统、华中理工大学开发的注塑模HSC5.0系统及CAE软件等。
优化模具系统结构设计和型件的CAD/CAE/CAM,并使之趋于智能化,提高型件成形加工工艺和模具标准化水平,提高模具制造精度与质量,降低型件表面研磨、抛光作业量和缩短制造周期;
研究、应用针对各类模具型件所采用的高性能、易切削的专用材料,以提高模具使用性能;
为适应市场多样化和个性化,应用快速原型制造技术和快速制模技术,以快速制造成塑料注塑模,缩短新产品试制周期。
这些是未来5~20年注塑模具生产技术的总体发展趋势,具体表现在以下几个方面:
1.提高大型、精密、复杂、长寿命模具的设计水平及比例。
这是由于塑料模成型的制品日渐大型化、复杂化和高精度要求以及因高生产率要求而发展的一模多腔所致。
2.在塑料模设计制造中全面推广应用CAD/CAM/CAE技术。
CAD/CAM软件的智能化程度将逐步提高;
塑料制件及模具的3D设计与成型过程的3D分析将在我国塑料模具工业中发挥越来越重要的作用。
3.推广应用热流道技术、气辅注射成型技术和高压注射成型技术。
采用热流道技术的模具可提高制件的生产率和质量,并能大幅度节省塑料制件的原材料和节约能源,所以广泛应用这项技术是塑料模具的一大变革。
制订热流道元器件的国家标准,积极生产价廉高质量的元器件,是发展热流道模具的关键。
气体辅助注射成型可在保证产品质量的前提下,大幅度降低成本。
气体辅助注射成型比传统的普通注射工艺有更多的工艺参数需要确定和控制,而且常用于较复杂的大型制品,模具设计和控制的难度较大,因此,开发气体辅助成型流动分析软件,显得十分重要。
另一方面为了确保塑料件精度,继续研究开发高压注射成型工艺与模具也非常重要。
4.开发新的成型工艺和快速经济模具。
以适应多品种、少批量的生产方式。
5.提高塑料模标准化水平和标准件的使用率。
我国模具标准件水平和模具标准化程度仍较低,与国外差距甚大,在一定程度上制约着我国模具工业的发展,为提高模具质量和降低模具制造成本,模具标准件的应用要大力推广。
为此,首先要制订统一的国家标准,并严格按标准生产;
其次要逐步形成规模生产,提高商品化程度、提高标准件质量、降低成本;
再次是要进一步增加标准件的规格品种。
6.应用优质材料和先进的表面处理技术对于提高模具寿命和质量显得十分必要。
第二章充电器外壳工艺性分析
2.1材料性能
图2-1所示为充电器外壳立体图,材料为ABS,外观黑色,精度等级一般(4级精度),制品表面光滑美观,带有精细花纹。
ABS为热塑性塑料,密度1.05~1.07g/cm3,抗拉强度30~50MPa,抗弯强度41~79MPa,拉伸弹性模量1587~2277MPa,弯曲弹性模量1380~2690MPa,收缩率0.3%~0.8%[2]。
该材料综合性能好,冲击强度高,尺寸稳定,易于成型,耐热和耐腐蚀性也较好,并具有良好的耐寒性。
是目前产量最大、运用最广泛的一种塑料。
图2-1充电器外壳立体图
2.2成型特性和条件
其吸湿性强,塑料在成型前必须充分预热干燥(80~90℃下至少干燥2小时),使其含水量小于0.3%。
对于要求表面光泽的零件,塑料在成型前更应该进行长时间预热(80~90℃下至少干燥3小时)。
塑料加热温度对塑料的质量影响较大,温度过高易于分解(分解温度>
270℃),一般料筒温度为180~260℃,建议温度245℃
成型时宜采用较高的加热温度(对精度较高的塑件,模温宜取50-60℃,对高光泽耐热塑