材料成形技术基础知识点总结解读Word文件下载.docx
《材料成形技术基础知识点总结解读Word文件下载.docx》由会员分享,可在线阅读,更多相关《材料成形技术基础知识点总结解读Word文件下载.docx(23页珍藏版)》请在冰豆网上搜索。
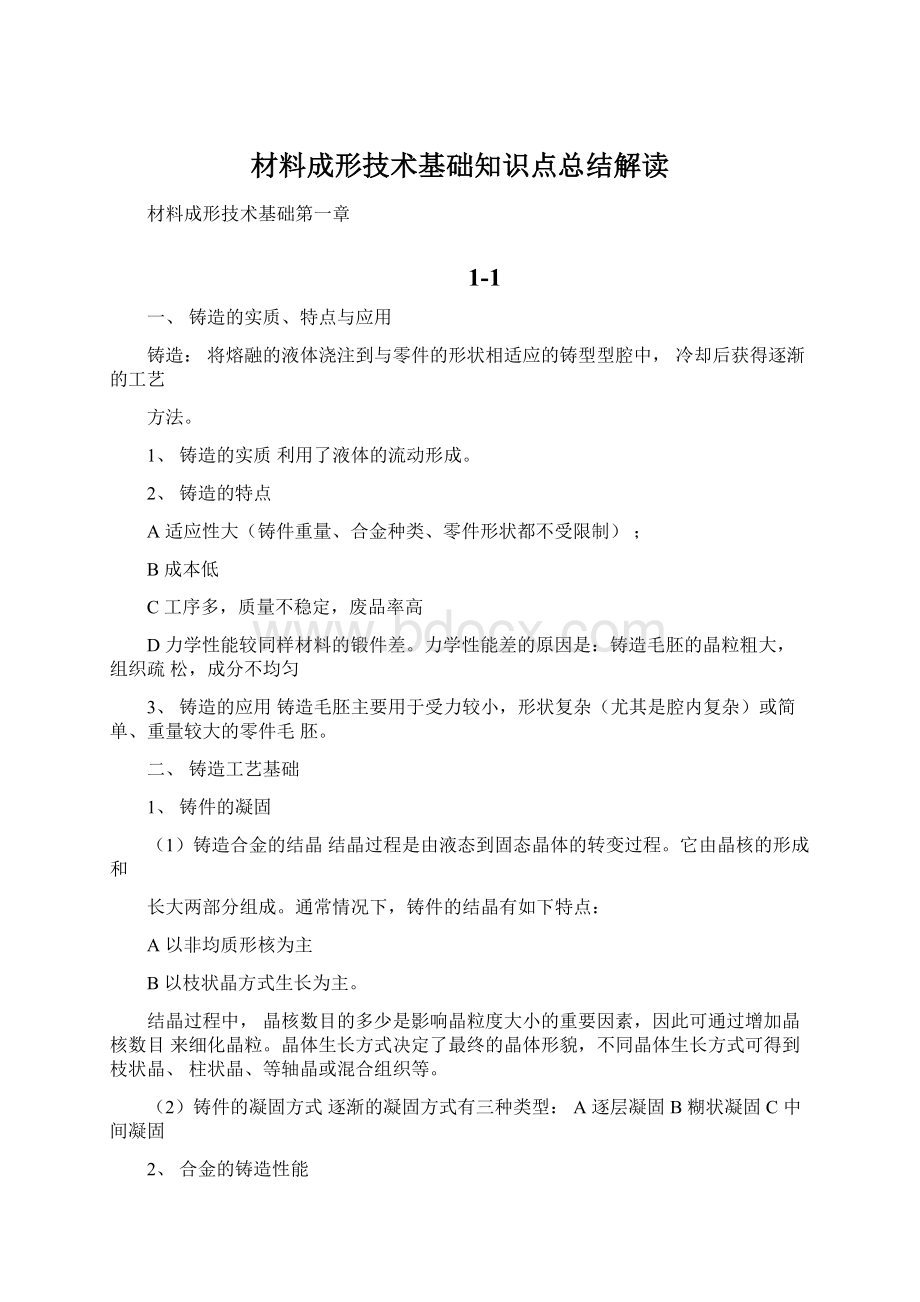
结晶过程中,晶核数目的多少是影响晶粒度大小的重要因素,因此可通过增加晶核数目来细化晶粒。
晶体生长方式决定了最终的晶体形貌,不同晶体生长方式可得到枝状晶、柱状晶、等轴晶或混合组织等。
(2)铸件的凝固方式逐渐的凝固方式有三种类型:
A逐层凝固B糊状凝固C中间凝固
2、合金的铸造性能
(1)流动性合金的流动性即为液态合金的充型能力,是合金本身的性能。
它反映了液态金属的充型能力,但液态金属的充型能力除与流动性有关,还与外界条件如铸型性质、浇注条件和铸件结构等因素有关,是各种因素的综合反映。
生产上改善合金的充型能力可以从一下各方面着手:
A选择靠近共晶成分的趋于逐层凝固的合金,它们的流动性好;
B提高浇注温度,延长金属流动时间;
C提高充填能力
D设置出气冒口,减少型内气体,降低金属液流动时阻力。
(2)收缩性
A缩孔、缩松形成与铸件的液态收缩和凝固收缩的过程中。
对于逐层凝固的合金由于固液两相共存区很小甚至没有,液固界面泾渭分明,已凝固区域的收缩就能顺利得到相邻液相的补充,如果最后凝固出的金属得不到液态金属的补充,就会在该处形成一个集中的缩孔。
适当控制凝固顺序,让铸件按远离冒口部分最先凝固,然后朝冒口方向凝固,最后才是冒口本身的凝固(即顺序凝固方式),就把缩孔转移到最后凝固的部位——冒
口中去,而去除冒口后的铸件则是所要的致密铸件
具有宽结晶温度范围,趋于糊状凝固的合金,由于液固两相共存区很宽甚至布满整个断面,发达的枝状晶彼此相互交错而把尚未结晶的金属液分割成许多小而分散的封闭区域,当该区域内的金属液凝固时,收缩得不到外来金属液的补偿,而形成了分散的小缩孔,即缩松。
这类合金即采用顺序凝固加冒口的措施也无法彻底消除缩松缺陷。
因此,
对于气密性要求不高,而要求内应力小的场合可采用同时凝固措施来满足要求。
B铸件内应力主要是由于铸件在固态下的收缩受阻而英气的。
这些阻碍包括机械阻碍
和热阻碍。
热应力与铸件结构有关。
壁厚不均铸件,冷却过程中各部分冷速不一,薄壁部分有
趣冷速快,率先从塑性变形阶段进入弹性变形阶段,此时,由于厚壁部分仍处于塑性变形收缩时,
由于这两部分为一整体,厚壁部分的弹性收缩必然收到薄壁部分对它的拉应力,而薄壁部分则收到相反的力一一压应力,。
因此,必须尽力那个使铸件壁厚均匀,避免金属局部积聚,以减小热应力。
铸件的内应力将导致铸件变形,甚至开裂。
1-2铸造方法
铸造按工艺方法分为砂型铸造和特种铸造砂型铸造
1、砂型铸造的特点:
(1)生产周期短,产品成本低;
(2)产品批量、大小不受限制;
(3)劳动强度大,劳动条件较差;
(4)铸件质量不稳定,易产生缺陷。
常用砂型主要特点及适用范围
铸型种类
铸型特征
主要特点
适用范围
湿砂型
以粘土做粘结剂,不经烘干可直接进行浇注的砂型
生产周期短、效率咼,易于实现机械化、自动化,设备投资和能耗低;
但铸型强度低、发气量大,易于产生铸造缺陷
单件或批量生产,尤其是大批量生产。
广泛用于铝合金、镁合金和铸铁件
干砂型
经过烘干的高粘土含量的砂型
铸型强度和透气性较咼,发气量小,故铸造缺陷较少;
但生产周期长,设备投资较大,能耗较咼,且难于实现机械化和自动化
单件、小批生产质量要求较咼,结构复杂的中、大型铸件
但铸型强度低、发气量大,易于产生
铸造缺陷
2、常用的造型方法
按使用的工具不同,分为手工造型和机器造型
(1)手工造型:
指全部用手工或手动工具完成的造型工序
1)特点:
操作灵活,适应性强,成本低,
生产准备时间短,铸件质量差,劳动强度大,生产率低。
2)应用:
单件、小批量生产,各种大、小型铸件
3)手工造型分类
按砂箱特征分
两箱造型
适用各种批量、大小铸件
三箱造型
用于有两个分型面的单件、小批量生产
脱箱造型
用于小型铸件
地坑造型
用于生产批量小的大中型铸件
(2)机器造型
指用机器完成全部或至少完成紧砂操作的造型工序。
1提高了生产率,铸件尺寸精度较高;
2节约金属,降低成本;
3改善了劳动条件;
4设备投资较大。
成批、大量生产各类铸件。
3)机械造型方法
1震压造型:
先震击紧实,再用较低的比压(0.15—0.4MPa)压实。
紧实效果好,噪音大,生产率不够高。
2微震压实造型:
对型砂压实的同时进行微震。
紧实度高、均匀,生产率高,噪音仍较大。
3高压造型:
用较高的比压(0.7—1.5MPa)紧实型砂。
紧实度高,噪音小,灰尘少,生产率高,
但设备造价高。
4抛砂造型:
利用离心力抛出型砂,完成填砂和紧实。
紧实度均匀,噪音小;
但生产率低。
特种铸造
1.特种铸造:
是指与砂型铸造有显著区别的一些铸造方法。
例如:
熔模铸造、金属型铸造、压力铸造、
离心铸造、低压铸造、陶瓷型铸造、壳型铸造和连续铸造等。
2.特点:
(1)不用砂或少用砂,改善了劳动条件,
减轻了劳动强度。
(2)铸件精度较高、性能较好。
(3)生产率高,工艺简单。
(4)成本高,生产周期长,
在工艺上和应用上各有一定的局限性。
三•分类:
1、金属型铸造
(1)金属型铸造:
将金属液浇入金属铸型获得铸件的方法
(2)特点:
1)铸件力学性能比砂型铸件高。
2)铸件精度和表面质量好。
3)可节约金属,生产率较高。
4)不用砂或少用砂,改善了劳动条件。
5)铸件成本高,易产生浇不足、开裂等缺陷。
6)铸造工艺要求严格。
(3)应用:
主要用于有色金属件的大批量生产。
铝活塞、汽缸体等。
(4)金属型的结构:
1)整体型;
2)水平分型;
3)垂直分型;
4)综合分型。
(5)工艺特点:
1)金属型要预热
2)喷刷涂料
3)及时开型取件
2.压力铸造
(1)压力铸造:
指熔融金属在高压下快速压入型腔,并在压力下结晶,获得铸件的方法。
(2)应用:
主要用于大量生产非铁合金中、小型铸件。
(铝合金、锌合金等)
汽缸体、化油器、离合器等。
(3)压力铸造的特点
1)铸件尺寸精度高,表面质量好;
2)铸件力学性能好;
3)可压铸形状复杂的薄壁铸件;
4)可嵌铸其它材料,节省贵重材料;
5)生产率高,易于实现机械化和自动化;
6)铸件料质受限制;
7)设备投资大,不宜小批量生产;
8)压铸件不能进行大余量的机械加工和热处理。
(压铸件易产生小气孔)
3.低压铸造
(1)低压铸造:
将合金液在压力下由铸型底部注入型腔,并在压力(60—150kPa)下结晶,
获得铸件的方法。
(2)应用:
铝、镁合金中、小型件的成批大量生产。
例如:
汽缸体、缸盖、活塞等。
(3)低压铸造的特点
1)充型压力和速度便于控制;
2)铸件组织致密,力学性能高;
3)铸件形状可较复杂,精度较高;
4)金属利用率高,一般在90%以上;
5)但升液管寿命较短,生产率低于压力铸造。
4.离心铸造
(1)离心铸造:
将金属液浇入高速旋转的铸型中,在离心力的作用下凝固成铸件的方法。
主要用于大批量生产空心回转体铸件。
铸铁管、汽缸套、铜套等。
(3)离心铸造的特点
1)简化了套筒、管类铸件的生产过程;
2)离心铸件力学性能高,缺陷较少;
3)可生产流动性较差的薄壁及双金属铸件;
4)铸件的形状和尺寸受限制;
5)内表面粗糙,易产生偏析;
6)设备投资大,不宜单件、小批量生产。
5.熔模铸造
(1)熔模铸造:
即用易熔材料制成模样,用造型材料将其包覆,制成型壳,熔出模样,经高温焙烧,浇注获得铸件的方法。
(2)熔模铸造的特点
1)铸件精度和表面质量较高。
2)可以铸造形状复杂的薄壁铸件。
3)生产批量不受限制。
4)原材料价格贵,铸件成本高。
5)工艺过程繁杂,生产周期长。
6)铸件尺寸不能太大,质量一般小于25Kg。
3)应用:
各种铸造合金,特别适于高熔点、难加工合金的小型铸件的成批、大量生产。
1-3铸造工艺设计
铸造工艺设计是根据铸件结构特点、技术要求、生产批量、生产条件等,确定铸造方案和工艺参数,绘制图样和标注符号,编制工艺卡和工艺规范等。
一、铸件浇注位置和分型面的选择
1、浇注位置的选择
1)铸件的重要加工面应朝下或位于侧面
2)铸件宽大平面应朝下
3)面积较大的薄壁部分应置于铸型下部或垂直、倾斜位置
4)易形成缩孔的铸件,应将截面较厚的部分置于上部或侧面,便于安放冒口,使铸件自下而上定向凝固
5)应尽量减少型芯的数量,且便于安放、固定和排气
2、铸型分型面的选择
1)便于起膜,使造型工艺简化
2)尽量将铸件重要加工面或大部分加工面、加工基准面放在同一个砂箱中
3)使型腔和主要芯位于下箱,便于下芯、合型和检查型腔尺寸二、铸造工艺参数确定
包括:
收缩余量、加工余量、起膜斜度、铸造圆角及芯头、芯座等。
三、铸造工艺简图绘制
1、铸造工艺符号及表示方法
2、典型零件工艺分析
1-4铸件结构工艺性
一:
合金铸造性能对铸件结构的要求铸件的结构如果不能满足合金铸造的性能要求,将可能产生浇不足、冷隔、缩孔、气孔、裂纹和变形等缺陷。
防止这些缺陷的方法包括设计合理的铸件壁厚、设计铸件加强筋、铸件结构尽量减小收缩受阻、铸件结构避免过大水平壁、注意不同铸造合金对铸件结构的要求。
设计合理壁厚:
a,铸件壁厚应合理,每种铸造合金都有其适宜的铸件壁厚要求;
b,
铸件壁厚应当均匀,防止壁厚相差过大凝固时产生缩孔、缩孔,此外冷却速度不均会产生热应力致使裂纹;
c,铸件壁的链接,①结构圆角,壁间转角处设计出结构圆角②厚壁与薄壁间的连续要逐步过渡③避免十字交叉和锐角相连接
设计铸件加强筋:
筋可以增加铸件的刚度和强度防止铸件变形,减小铸件壁厚,防止铸件产生缩孔和裂纹。
(注:
铸件结构内容比较重要,特别是P36-39的设计图,各种铸造合金的性能结构特点参照P30的表格)
二:
铸造工艺对结构的要求
1铸件外形的设计