毕业论文曲轴加工工艺开题报告docWord文档格式.docx
《毕业论文曲轴加工工艺开题报告docWord文档格式.docx》由会员分享,可在线阅读,更多相关《毕业论文曲轴加工工艺开题报告docWord文档格式.docx(6页珍藏版)》请在冰豆网上搜索。
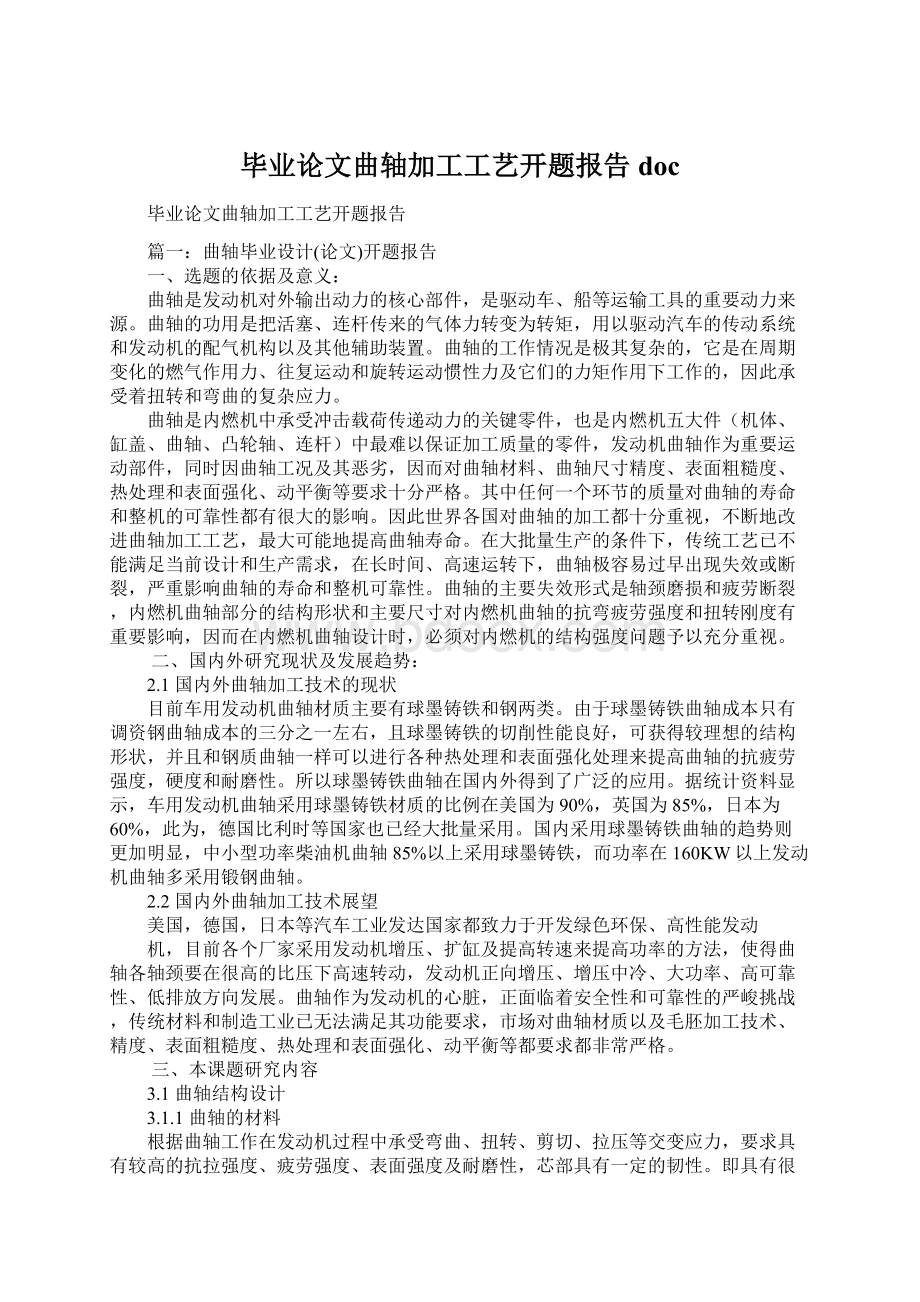
曲轴的主要失效形式是轴颈磨损和疲劳断裂,内燃机曲轴部分的结构形状和主要尺寸对内燃机曲轴的抗弯疲劳强度和扭转刚度有重要影响,因而在内燃机曲轴设计时,必须对内燃机的结构强度问题予以充分重视。
二、国内外研究现状及发展趋势:
2.1国内外曲轴加工技术的现状
目前车用发动机曲轴材质主要有球墨铸铁和钢两类。
由于球墨铸铁曲轴成本只有调资钢曲轴成本的三分之一左右,且球墨铸铁的切削性能良好,可获得较理想的结构形状,并且和钢质曲轴一样可以进行各种热处理和表面强化处理来提高曲轴的抗疲劳强度,硬度和耐磨性。
所以球墨铸铁曲轴在国内外得到了广泛的应用。
据统计资料显示,车用发动机曲轴采用球墨铸铁材质的比例在美国为90%,英国为85%,日本为60%,此为,德国比利时等国家也已经大批量采用。
国内采用球墨铸铁曲轴的趋势则更加明显,中小型功率柴油机曲轴85%以上采用球墨铸铁,而功率在160KW以上发动机曲轴多采用锻钢曲轴。
2.2国内外曲轴加工技术展望
美国,德国,日本等汽车工业发达国家都致力于开发绿色环保、高性能发动
机,目前各个厂家采用发动机增压、扩缸及提高转速来提高功率的方法,使得曲轴各轴颈要在很高的比压下高速转动,发动机正向增压、增压中冷、大功率、高可靠性、低排放方向发展。
曲轴作为发动机的心脏,正面临着安全性和可靠性的严峻挑战,传统材料和制造工业已无法满足其功能要求,市场对曲轴材质以及毛胚加工技术、精度、表面粗糙度、热处理和表面强化、动平衡等都要求都非常严格。
三、本课题研究内容
3.1曲轴结构设计
3.1.1曲轴的材料
根据曲轴工作在发动机过程中承受弯曲、扭转、剪切、拉压等交变应力,要求具有较高的抗拉强度、疲劳强度、表面强度及耐磨性,芯部具有一定的韧性。
即具有很高的疲劳强度、耐磨性和高淬透性,且进行强化处理时变形小,高温下具有高的蠕变强度。
随着发动机性能的提高,对曲轴的原材料及加工工艺提出新的要求,现代车用发动机曲轴材质主要有球墨铸铁和钢两类。
由于球墨铸铁曲轴成本只有调质钢曲轴成本1/3左右,且球墨铸铁的切削性能良好,可获得较理想的结构形状,并且和钢质曲轴一样可以进行各种热处理和表面强化处理来提高曲轴的抗疲劳强度、硬度和耐磨性。
所以球墨铸铁曲轴在国内外得到了广泛应用。
据统计资料显示,车用发动机曲轴采用球墨铸铁材质的比例在美国为90%,英国为85%,日本为60%,此外,德国、比利时等国家也已经大批量采用。
国内采用球墨铸铁曲轴的趋势则更加明显,中小型功率柴油机曲轴85%以上采用球墨铸铁,而功率在160kW以上的发动机曲轴多采用锻钢曲轴。
我国球铁曲轴的生产继QT600-2、QT700-2之后,现已能稳定地生产QT800–2、QT900-2等几种牌号,目前已能大批量生产QT800-6球铁曲轴。
但从整体水平来看,存在生产效率低,工艺装备落后,毛坯机械性能不稳定、精度低、废品率高等问题。
3.1.2曲轴结构设计
曲轴结构设计在过去的几十年中得到了飞速的发展。
在曲轴的设计初期一般是按照已有的经验公式计算或者与已有的曲轴进行类比设计,在进行了初步的设
计后造出曲轴样品再进行试验,通过实验数据进行适当的改进。
曲轴设计发展到今天已经有了很大的发展。
随着内燃机向高可靠性、高紧凑性、高经济性的不断发展,传统的以经验、试凑、定性为主要设计内容的设计方法已经不能满足要求,而随着电子计算机技术的不断发展,内燃机及其零部件的设计已经发展到采用包括有限元法、优化设计、动态设计等现代先进设计技术在内的计算机分析、预测和模拟阶段。
有限元法是最有效的数值计算方法之一,它使人们对零部件关键参数的理解和设计更进了一步。
(1)在设计内燃机曲轴时,应根据内燃机的工作条件,选择不同的结构设计方案。
内燃机曲轴结构设计方法大致如下:
①选择确定结构形式:
整体锻造曲轴、整体铸造曲轴、组合曲轴。
②确定润滑油道
曲轴主轴颈和曲柄销一般采用压力润滑。
润滑油由主油道送到各主轴承,在经曲轴内润滑油道进去连杆轴承。
当主轴承为滚动轴承时,润滑可从假轴承进入曲轴内腔,再分配到各有关轴承。
在决定主轴承和曲柄销上的油孔位置时,主要考虑应保证供油压力和油孔对曲轴强度的影响程度。
③确定曲轴平衡块形式
平衡块用来平衡曲轴的不平衡惯性力和力矩,减轻主轴承载荷以及减小曲轴和曲轴箱所受的内力矩。
但曲轴配置平衡块后重量增加,将使曲轴系统的扭振效率有所降低。
因此应根据曲轴结构、转速、曲柄排列等因素来配置平衡块和平衡精度要求。
平衡块可与曲轴制成一体,也可与曲轴分开制造后再进行装配。
(2)曲轴结构形式的选择
曲轴结构形式与其制造方法有直接关系,在进行曲轴设计时必须同时进行。
曲轴有整体式和组合式曲轴两大类。
而摩托车发动机常采用组合式曲轴,这是因为其加工简单,不需要大规模锻模具设备,它由曲轴左半部、曲轴右半部及曲轴销组成。
通过液压压入的方法将其结合起来。
本设计中采用滚动轴承做主轴承。
这是因为使用它具有以下优点:
①可以采用隧道式曲轴,保证曲轴箱有较高的强度和刚度;
②可以减少摩擦损失,提高机械效率,因而使燃料消耗下降;
③发动机启动较为容易,尤其在气温较低的时候;
④采用滚动轴承后,对主轴的润滑较易实现。
3.2曲轴工艺分析
3.2.1曲轴的机械加工技术
曲轴主轴颈的粗加工、半精加工工艺和精加工工艺,大体分为以下几种:
(1)传统的曲轴主轴颈的多刀车削工艺。
生产效率和自动化程度相对较低。
粗加工设备多采用多刀车床车削曲轴主轴颈,工序的质量稳定性差,容易产生较大的内应力,难以达到合理的加工余量。
一般精加工采用曲轴磨床,通常靠手工操作,加工质量不稳定,尺寸的一致性差。
(2)数控车削工艺。
数控车削设备价格相对便宜,不需要复杂的刀具,但只适合小批量生产。
(3)数控内铣铣削工艺。
内铣设备价格较高,刀具费用也很高,但适合大批量生产。
(4)数控车—拉、数控车—车拉工艺。
其突出优点是可对宽轴径进行分层加工,切削效率高,加工质量好,但车拉刀具结构复杂,技术含量高,并且长期依靠进口,好处是可集车—车拉工艺加工连杆轴颈要两道工序于一起。
(5)CNC高速外铣工艺。
数控高速外铣是20世纪90年代新兴起来的一种新型加工工艺,其应用范围广,特别双刀盘数控高速外铣以其加工效率高、加工质量稳定、自动化水平高,已成为当前是曲轴主轴颈粗加工的发展方向。
就比较而言,CNC车—车拉工艺加工连杆轴颈要二道工序,CNC高速外铣只要一道工序就能完成,切削速度高(目前最高可达350m/min)、切削时间较短、工序循环时间较短、切削力较小、工件温升较低、刀具寿命高、换刀次数少、加工精度更高、柔性更好。
如德国BOEHRINGER公司专为汽车发动机曲轴设计制造的柔性的高速随动数控外铣床VDF315OM-4型,该设备应用工件回转和铣刀进给伺服连动控制技术,可以一次装夹不改变曲轴回转中心随动跟踪铣削曲轴的轴颈。
其采用一体化复合材料结构床身,工件两端电子同步旋转驱动,具有干式切削、加工精度高、切削效率高等特点;
使用SIEMENS840DCNC控制系统,设备操作说明书在人机界面上,通过输入零件的基本参数即可自动生成加工程序,可以加工长度450~700mm、回转直径380mm以内的各种曲轴轴颈直径误差仅为±
0.02mm。
(6)数控曲轴磨削工艺。
精加工使用数控磨床,采用静压主轴、静压导轨、静压进给丝杠(砂轮头架)和线性光栅闭环控(本文来自:
wwW.xIAocAofaNwE小草范文网:
毕业论文曲轴加工工艺开题报告)制等控制装置,使各尺寸公差及形位公差得到可靠的保证,精加工还广泛使用数控砂带抛光机进行超精加工,经超精加工后的曲轴轴颈表面粗糙度至少提高一级精度。
如GF70M-T曲轴磨床是日本TOYADA公工机开发生产的专用曲轴磨床,是为了满足多品种、低成本、高精度、大批量生产需要而设计的数控曲轴磨床。
该磨床应用工件回转和砂轮进给伺服联动控制技术,可以一次装夹而不改变曲轴回转中心即可完成所有轴颈的磨削;
采用静压主轴、静压导轨、静压进给丝杠(砂轮头架)和线性光栅闭环控制,使用TOYADA工机生产的GC50CNC控制系统,磨削轴颈圆度精度可达到0.002mm;
采用CBN砂轮,磨削线速度高达120m/s,配双砂轮头架,磨削效率极高。
3.2.2曲轴的强化工艺技术
目前国内外曲轴常见的强化工艺大致有如下几种:
(1)氮化处理。
氮化能提高曲轴疲劳强度的20%~60%。
(2)喷丸处理。
曲轴经喷丸处理后能提高疲劳强度20%~40%。
(3)圆角与轴颈同时感应淬火处理。
该强化方式应用于球铁曲轴时,能提高疲劳强度20%,而应用于钢轴时,则能提高l00%以上。
(4)圆角滚压处理。
球铁曲轴经圆角该压后寿命可提高120%~300%,钢轴经圆角液压后寿命可提高70%~150%。
曲轴圆角滚压强化工艺主要包括曲轴圆角滚压和曲轴滚压校正两部分。
(5)复合强化处理。
它是指应用多种强化工艺对曲轴进行强化处理,球墨铸铁曲轴采用圆角该滚压工艺与离子氮化工艺结合使用,可使整个曲轴的抗疲劳强度提高130%以上。
四、本课题研究方案
(1)查阅原始资料,熟悉曲轴结构设计的方法及曲轴工艺技术。
(2)根据曲轴的工作条件和柴油机工作参数对曲轴进行结构设计及强度校核。
(3)利用曲轴材料和工况分析曲轴的加工工艺。
五、研究目标、主要特色及工作进度:
篇二:
发动机曲轴的加工工艺及夹具设计-开题报告
毕业设计(论文)开题报告
1.选题背景及意义
柴油机自十九世纪后期出现以来,经过一百多年的不断研究和改进,已经发展到比较完善的程度,它以热效率高、功率和转速范围宽广、比重景较小的优点,在动力机械中占有极其重要的地位,广泛应用于国民经济和军事装备的各领域中[1].随着发动机技术的不断发展,发动机的设计向着高效率,高可靠性,轻质量,低燃油消耗率以及低排放等方向发展,其强化指标不断提高,机械负荷不断增加。
作为发动机中最重要、载荷最大、价格较贵的零件之一的曲轴在周期性变化的气体力、往复和旋转运动引起的惯性力以及他们的扭矩、弯矩的共同作用下,产生弯曲和扭转变形,工作条件愈加苛刻。
因此,对曲轴的刚度和强度提出了很高的要求,也是发动机设计的重点和难点之一.曲轴是发动机的关键零件,其尺寸大小在很大程度上影响着发动机的外形尺寸和重量,以及工作可靠性和寿命。
曲轴的破坏事故可能引起其它零件的严重损坏。
随着内燃机的发展与强化,曲轴的工作条件愈加严酷了,必须在设计上正