摩托车发动机凸轮轴外圆磨床夹具的改进通用范本文档格式.docx
《摩托车发动机凸轮轴外圆磨床夹具的改进通用范本文档格式.docx》由会员分享,可在线阅读,更多相关《摩托车发动机凸轮轴外圆磨床夹具的改进通用范本文档格式.docx(3页珍藏版)》请在冰豆网上搜索。
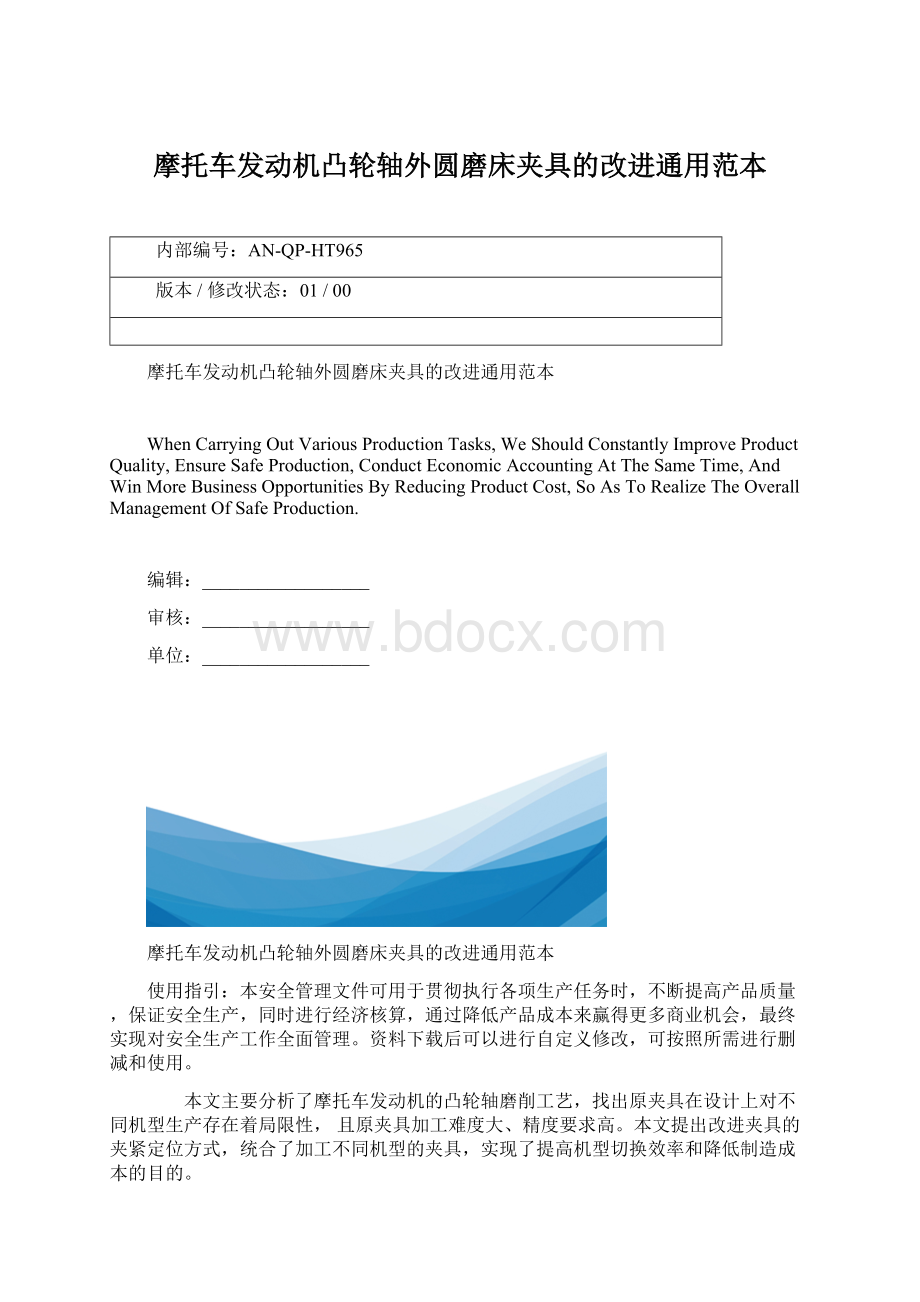
编辑:
__________________
审核:
单位:
使用指引:
本安全管理文件可用于贯彻执行各项生产任务时,不断提高产品质量,保证安全生产,同时进行经济核算,通过降低产品成本来赢得更多商业机会,最终实现对安全生产工作全面管理。
资料下载后可以进行自定义修改,可按照所需进行删减和使用。
本文主要分析了摩托车发动机的凸轮轴磨削工艺,找出原夹具在设计上对不同机型生产存在着局限性,且原夹具加工难度大、精度要求高。
本文提出改进夹具的夹紧定位方式,统合了加工不同机型的夹具,实现了提高机型切换效率和降低制造成本的目的。
社会发展日益要求环保,五羊一本田摩托(广州)有限公司始终致力于增加产品科技含量,促进摩托车行业品质的提高,使事业与世界环境共同发展。
通过技术攻关和创新、开发环保产品,生产的摩托车在20xx年满足了欧洲2号排放标准,20xx年又推出国内第一款集欧Ⅲ排放标准、电喷、水冷于一身的新产品,在20xx年该车型成为国内第一款取得国家全项许可(公告、环保以及3c)的国III车型。
20xx年更是采用领先的电喷技术、发动机上的核心二号技术及OTR技术,并采用触媒对应排放污染物控制,以符合国家新出台的国III排放环保法规要求,于7月份共推出十款达到国III排放标准的新产品。
直至20xx年,五羊—本田每年都会推出十款以上的新产品到国内以及海外市场,新产品的诞生,发动机中的凸轮轴组件也因应发生设变。
我司有两条凸轮轴生产线,通过更换工装、夹具实现全机型凸轮轴总成的加工。
新产品的导人,必须配置相适宜的工装夹具,而现代的生产是讲求效率和成本的,本文叙述的是通过改进凸轮轴的外圆磨床夹具,以最少的投入实现新产品的生产和快速的加工机型切换。
凸轮轴磨床工序工艺分析
目前,我司采用一台外圆磨床一次同时加工凸轮轴全部轴径。
该工艺特点,一次定位完成所有轴径的精加工,加工精度高,投资少,仅需要一台设备。
我们知道,实现机械加工的工装夹具关键因素是定位与夹紧。
对于轴类零件,一般以中心孔定位,相对比较简单,且容易实现。
至于夹紧,则根据零件、工艺的特点,采取适当的夹紧方式实现加工。
凸轮轴也是轴类零件,也以中心孔定位的。
夹紧机构则根据加工零件的结构不同,分有两种类型。
一类是以KZL为代表的,利用工件端面的键槽,夹具采用棘子与键槽配合,顶尖夹紧,驱动工件旋转实现磨削(以下简称:
棘子驱动顶尖夹紧)。
另一类是以KVJ为代表,利用工件端面的油孔,采用涨芯夹具夹紧油孔内壁驱动工件旋转,然后顶尖夹紧,实现磨削(以下简称:
涨芯驱动顶尖夹紧)。
两类夹紧方式如图2所示。
原夹具的分析以及问题的提出
“棘子驱动顶尖夹紧”与“涨芯驱动顶尖夹紧”,两种驱动夹紧方式完全不同。
棘子驱动夹具简单,驱动元件与夹紧部件分离,即顶尖与棘子分离,制作成本低,安装调整也方便、快捷。
而涨芯驱动夹具复杂,驱动元件与夹紧部件合为一体,结构复杂,制作精度要求高,目前均从日本进口,每套涨芯夹具约3万元,使用成本相当昂贵。
涨芯夹具安装调整也较复杂,特别是,两种夹具切换时,耗时长达60分钟以上。
而目前我司两条凸轮轴生产线的节拍35秒/件,要求机型切换时间30分钟。
凸轮轴磨多级外圆工序的机型切换时间长达60分钟以上,是整条生产线耗时最长的,其中,切换砂轮25分钟,切换工装夹具35分钟,严重影响生产线的效率。
目前,摩托车市场竞争越加激烈,生产机型越来越多,导致生产机型切换更加频繁。
虽然我司历经多年的FOG(生产能力提升活动)推进,本工序机型切换时间长的问题依然没解决,已成为抑制整条生产线生产能力的瓶颈。
新夹具的构思
我们知道,磨削外圆时,作用于工件和砂轮上的磨削力可以分解为相互垂直的三个分力,即沿砂轮切向的切向磨削力Ft,沿砂轮径向的法向磨削力Fn,以及沿砂轮轴向的轴向磨削力Fa。
在外圆磨削过程中,工装夹具的驱动夹紧力主要克服切向磨削力,驱使工件旋转实现磨削。
当切向磨削力大于驱动夹紧力时,工件会出现打滑甚至脱离夹具的情况。
因此,我们有个大胆的假设:
能否通过头架顶尖上“磨削法向磨削力”和“尾座顶尖推力”,使头架顶尖与工件产生的摩擦力克服切向磨削力,驱动工件旋转的,实现磨削。
统合两种夹具为两顶尖驱动夹紧(其中一顶尖为活动顶尖),实现机型切换时间中的工装夹具切换时间为零。
根据工艺夹具设计要求,精加工过程中,一般夹具安全系数为1.5~2.0,即尾座顶尖总推力应大于72.6N,磨削夹紧力才是充足的、安全的。
我司使用进口日本丰田工机GL5PⅡ-32型外圆磨床磨削凸轮轴各级轴径,其尾座顶尖工作推力由弹簧控制,且其弹簧力可调。
丰田工机GL5PⅡ-32型外圆磨床尾座顶尖弹簧力:
MIN245N,MAX1076N。
因此,设备的尾座顶尖推力永大于假设所需安全值。
所以,假设是可以实现的。
新工艺验证:
根据以上分析论证,将设备尾座固定顶尖变更为回转顶尖,尾座顶尖推力设定为设备最小值245N。
对以下两组磨削参数进行试验。
实际验证结果也证明:
我们的假设是可行的。
新夹具投入使用的效果
新驱动夹具全面实施后,检测产品加工精度CP值均与原工艺一致,均达1.33以上。
项目实施后,跟踪回转顶尖使用寿命均长达14个月以上,满足我们预定寿命1年(或加工35万件)以上。
新驱动夹具:
取消了专用的夹紧驱动装置,两类不同结构的凸轮轴统一由两顶尖定位兼驱动夹紧,各机种工装简单、统一,机型切换方便快捷,由于统合了两种夹具,机型切换时间中的工装夹具切换时间变为零,总的时间由原来60分钟以上缩短至30分钟以内,大大的提升了生产线的生产效率。
现在社会发展日新月异,产品更新换代越来越快。
企业的生产制造模式越来越多是以小批量多品种,以适应市场的需求。
多品种小批量的生产模式,换型效率越来越受到关注。
利用项目成果,可以进一步简化传统外圆磨削工艺的工装,统一由两顶尖定位兼驱动夹紧,大大缩短了新产品的生产准备周期,提高产品的生产切换效率。
可在此位置输入公司或组织名字
YouCanEnterTheNameOfTheOrganizationHere