锅炉内衬施工工艺Word文档下载推荐.docx
《锅炉内衬施工工艺Word文档下载推荐.docx》由会员分享,可在线阅读,更多相关《锅炉内衬施工工艺Word文档下载推荐.docx(16页珍藏版)》请在冰豆网上搜索。
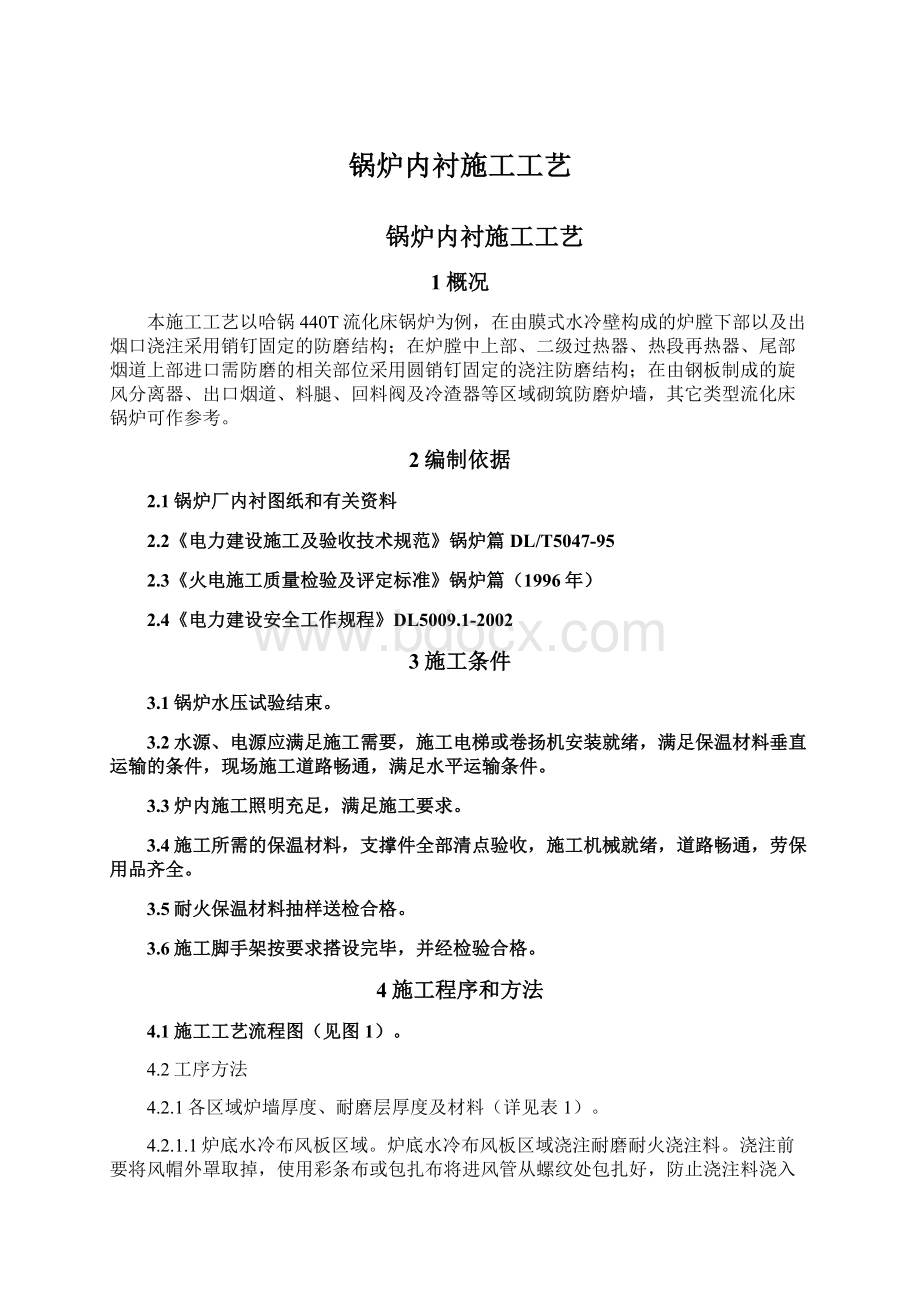
4.1施工工艺流程图(见图1)。
4.2工序方法
4.2.1各区域炉墙厚度、耐磨层厚度及材料(详见表1)。
4.2.1.1炉底水冷布风板区域。
炉底水冷布风板区域浇注耐磨耐火浇注料。
浇注前要将风帽外罩取掉,使用彩条布或包扎布将进风管从螺纹处包扎好,防止浇注料浇入风帽内管及进风管内,将布风板上所有进风管浇注料部分的外表面缠上2mm厚的陶瓷纤维纸。
为利于布风板上前墙处二个排渣口顺利排渣,布风板浇注料上表面由后墙向前倾斜,后墙处浇注料厚210mm,前墙处浇注料厚160mm,浇注料表面到风帽外罩底面的距离为30mm。
4.2.1.2下炉膛四周水冷壁。
在下炉膛四周水冷壁,为防止受热面的磨损,在受热面表面浇注80mm(从
图1:
施工工艺流程图
管子表面算起)厚的耐磨耐火浇注料。
该区域有许多开孔,包括:
出渣口及回灰口、回料口、启动燃烧器开口、二次风口、测温测压口及人孔,对于所有穿管结构,除测温管及启动燃烧器处浇注孔径与该管外径相同外,其余穿管处浇注孔径应与该处管的内径相同,且所有穿管应与浇注孔同轴。
对于直径大于159mm的管子浇注前应涂刷2mm沥青,直径小于159mm的管子浇注前应涂刷1mm沥青。
在回料阀口、启动燃烧器口周围处的膜式壁扁钢上或密封盒板上还要焊一些抓钉,用以固定这些开口周围区域的耐磨耐火浇注料。
4.2.1.3热段再热器、二级过热器及其穿越前水冷壁四周部分区域浇注90mm(由管子中心线算起)耐磨耐火浇注料;
在炉膛后水冷壁上部出烟口及尾部烟道前墙入口等区域同样浇注耐磨耐火浇注料。
表1:
炉墙厚度、耐磨层厚度及材料明细表
锅炉部位
总
厚
度
(mm)
耐磨耐火层厚度(mm)
耐火保温层厚度(mm)
耐磨
耐火砖
耐火
浇注料
耐火保温浇注料
耐火保温砖
保温浇注料
保温砖
耐火浇注料
耐火可塑料
炉
膛
水冷布风板
160~210
水冷风室
顶面及侧面
70
其余
炉膛下部水冷壁
106
二级过热器下端
90×
2
热段再热器下端
热段再热器和二过穿墙处前后墙水冷壁
90
出烟口处炉墙侧壁
出烟口内壁
旋风分离器及料腿
入口烟道
350
113
116
锥段
筒体入口段、顶棚
160
65
125
料腿
300
66
出口烟道
部分筒体入口段、底面及顶棚
130
155
侧面
回
料
阀
回料下降管入炉斜管
回料下降砖砌部分
入炉斜管部分
120
112
浇注部分
122
阀体立面
其它部分
布风板
150
100
50
冷
渣
器
顶
板
一室
200
80
55
二、三室
四周
出渣口及返气弯管
≥190
≥90
(2)
注:
(1)对受热面处总厚度从管子中心线算起,对钢板制件总厚度从钢板内表面算起。
(2)此处耐磨材料倾斜3°
,上面为100mm厚的耐磨浇注料,下面为耐火浇注料。
4.2.1.4旋风分离器。
旋风分离器是循环流化床锅炉中冲蚀、磨损最为严重的部位,防磨结构较为复杂。
每个旋风分离器由入口烟道和旋风筒组成,旋风筒从上至下又由筒体、锥体及料腿所组成。
在筒体、锥体及料腿内水平安装了8层支撑托板,焊接固定在金属壳体的内壁上,用以支撑耐磨保温材料,实现分层卸载;
入口烟道底部安装了两道止推板、入口烟道侧墙以及旋风筒入口位置分别安装5道止推板,也与金属壳体的内壁焊接,承受耐磨耐火保温材料在热膨胀后的水平推力。
在旋风分离器中,耐磨层有耐磨浇注料和耐磨砖两种,顶棚部分的耐磨浇注料中交错布置了一定数量的吊挂砖,耐磨砖又包括拉钩砖和非拉钩砖;
保温层有耐火保温浇注料、耐火保温砖、保温浇注料和保温砖等几种。
入口段顶棚及筒体顶棚。
该区域炉墙总厚度350mm,分三层:
内层为160mm厚的耐磨耐火浇注料,中间层为65mm厚的耐火保温浇注料,外层为125mm厚的保温浇注料。
浇注料的支撑件为“Y”形抓钉,同时布置了一定数量的吊挂砖。
浇注料由顶棚上部逐层浇入并捣实,然后将盖板盖上并点焊,当锅炉完成整体热养生后,再将盖板全部严密焊封。
入口段侧墙。
该区域炉墙总厚度350mm。
膨胀节周围以及形状不规则难以布置成型砖的部分内侧采用350mm厚的浇注料结构,用“Y”形抓钉固定。
其它部分为砖砌结构分三层,内层为113mm厚耐磨耐火砖,中层为116mm厚的耐火保温砖,外层为116mm厚的保温砖。
耐磨耐火砖采用拉钩楔形砖结构,在两个拉钩之间设置四块楔形砖,即两块拉钩砖,两块非拉钩砖,利用楔形拉钩砖的角度固定非拉钩砖,使其不易脱出,垂直方向每层均安装拉钩砖。
每面墙有二道止推板,耐磨耐火砖、耐火保温砖布置其中,根据所布置砖墙的长度不同,中间留有若干道膨胀缝。
两侧墙与顶部注浇料之间留有膨胀缝。
膨胀缝内应清理干净,不得有灰浆、碎砖及其它杂物并填充硅酸铝耐火纤维毡。
筒体。
筒体炉墙总厚度350mm。
筒体烟气入口上、下等形状不规则部分采用“Y”形抓钉固定,内层为160mm厚的耐磨耐火浇注料,中间层为65mm厚的耐火保温浇注料,外层为125mm厚保温浇注料;
其它部分采用砖砌炉墙结构,分三层,内层为113mm厚耐磨耐火砖,中间层116mm厚的耐火保温砖,外层为116mm厚的保温砖。
烟气入口处两侧有两道止推板,筒体烟气入口下面以及筒体与锥体交界处各布置一圈支撑托板。
筒体砖与顶部浇注料之间留有膨胀缝。
根据托板之间筒体砖的不同高度,托板下留有不同宽度的膨胀缝。
所有膨胀缝内应清理干净,不得有灰浆、碎砖及其它杂物,用硅酸铝耐火纤维毡填充。
筒体砖需用拉钩砖固定,与止推板相邻的每块砖均采用拉钩砖,支撑托板上的每层砖需采用拉钩砖,在垂直方向每层都要安装拉钩砖。
同一层砖每隔四块应在砖的一侧加一层纤维纸,沿高度方向每隔三层应在砖的上表面加一层纤维纸。
锥体。
锥体炉墙为砖砌结构厚度350mm,分三层,内层为113mm耐磨耐火砖,中间层为116mm耐火保温砖,外层为116mm厚保温砖。
锥体炉墙分三段,每段之间布置一层支撑托板,托板上下各采用不同的尺寸的耐磨耐火砖,其它部分只采用二种耐磨耐火砖,一种为楔形砖,另一种为矩形砖。
锥体部分没有拉钩砖,锥体环向无膨胀缝,高度方向膨胀缝留在支撑托板下面。
料腿。
料腿部分采用砖砌炉墙结构,厚度300mm,内层为113mm厚耐磨耐火砖,中间为116mm厚耐火保温砖,外层为66mm厚保温砖。
料腿分三段,每段布置一层支撑托板,托板上、下各采用不同尺寸的耐磨耐火砖,其它部分只采用二种耐磨耐火砖,一种为楔形砖,另一种为矩形砖。
在料腿下部与回料阀筒体相接处采用浇注料结构,分三层,内层为100mm厚的耐磨耐火浇注料,中间层为65mm厚的耐火保温浇注料,外层为135mm厚的保温浇注料,采用“Y”形抓钉固定。
入口烟道底板。
该区域炉墙总厚度350mm,不规则部分采用浇注料,分三层,内层为160mm厚的耐磨耐火浇注料,中间层为65mm厚的耐火保温浇注料,外层为125mm厚保温浇注料;
规则部分采用砖砌,分三层,内层为113mm厚的耐磨耐火砖,中间层为116mm的耐火保温砖,外层为116mm厚保温砖;
砖与浇注料之间有两道止推板。
4.2.1.5出口烟道。
出口烟道炉墙总厚度350mm。
出口烟道顶棚、底板及部分筒体。
顶棚及部分筒体采用浇注炉墙结构。
分三层,内层为130mm厚耐磨耐火浇注料,中间层为65mm厚的耐火保温浇注料,外层为155mm厚保温浇注料。
浇注料的支撑件为“Y”形抓钉,同时布置了一定数量的吊挂砖,施工顺序同4.2.1.4。
出口烟道两侧及部分筒体炉墙区域在膨胀节周围以及形状不规则难以布置成型砖的部分采用浇注料炉墙,分三层,内侧采用130mm厚的耐磨耐火浇注料,中间层为65mm厚的耐火保温浇注料,外层为155mm厚的保温浇注料,由“Y”形抓钉固定;
其它部分采用砖砌炉墙结构,分三层,内层为113mm厚的耐磨耐火砖,中间层为116mm厚的耐火保温砖,外层为116mm厚的保温砖,同入口烟道一样采用拉钩楔形砖结构。
两侧墙均有四道止推板,筒体砖与止推板之间有1mm间隙,留作止推板缠绕陶瓷纤维毡用;
根据所布置砖墙的长度不同还留有若干道11mm膨胀缝。
两侧墙与顶部浇注料之间留有膨胀缝,所有膨胀缝用硅酸铝耐火纤维毡填充。
以上介绍的绝热式旋风分离器的耐磨层结构形式,有些流化床锅炉旋风分离器采用受热面形式,在受热面内表面采用一定厚度的耐磨可塑料作为耐磨层,受热面外保温。
4.2.1.6回料阀区域。
回料阀布风板采用耐磨耐火浇注料,共二层,上面一层为耐磨耐火浇注料,厚100mm,下面一层为耐火保温浇注料,厚50mm。
布风板浇注料上表面水平,施工详细要求同4.2.1.1。
回料阀外壳。
回料阀炉墙分砖砌和浇注两类,总厚度300mm。
浇注料部分内侧为122mm厚的耐磨耐火浇注料,中间层为65mm厚的耐火保温砖,外层为112mm厚的保温砖;
砖砌部分下降管炉墙内层为113mm厚耐磨耐火砖,中间为116mm厚的耐火保温砖,外层为66mm厚的保温砖;
斜腿部分内层为120mm厚的耐磨耐火砖,中层为65mm的耐火保温砖,外层为112mm厚的保温砖。
入炉斜管进炉膛部分为浇注结构