全面解剖丰田汽车模具制造技术与管理模板文档格式.docx
《全面解剖丰田汽车模具制造技术与管理模板文档格式.docx》由会员分享,可在线阅读,更多相关《全面解剖丰田汽车模具制造技术与管理模板文档格式.docx(10页珍藏版)》请在冰豆网上搜索。
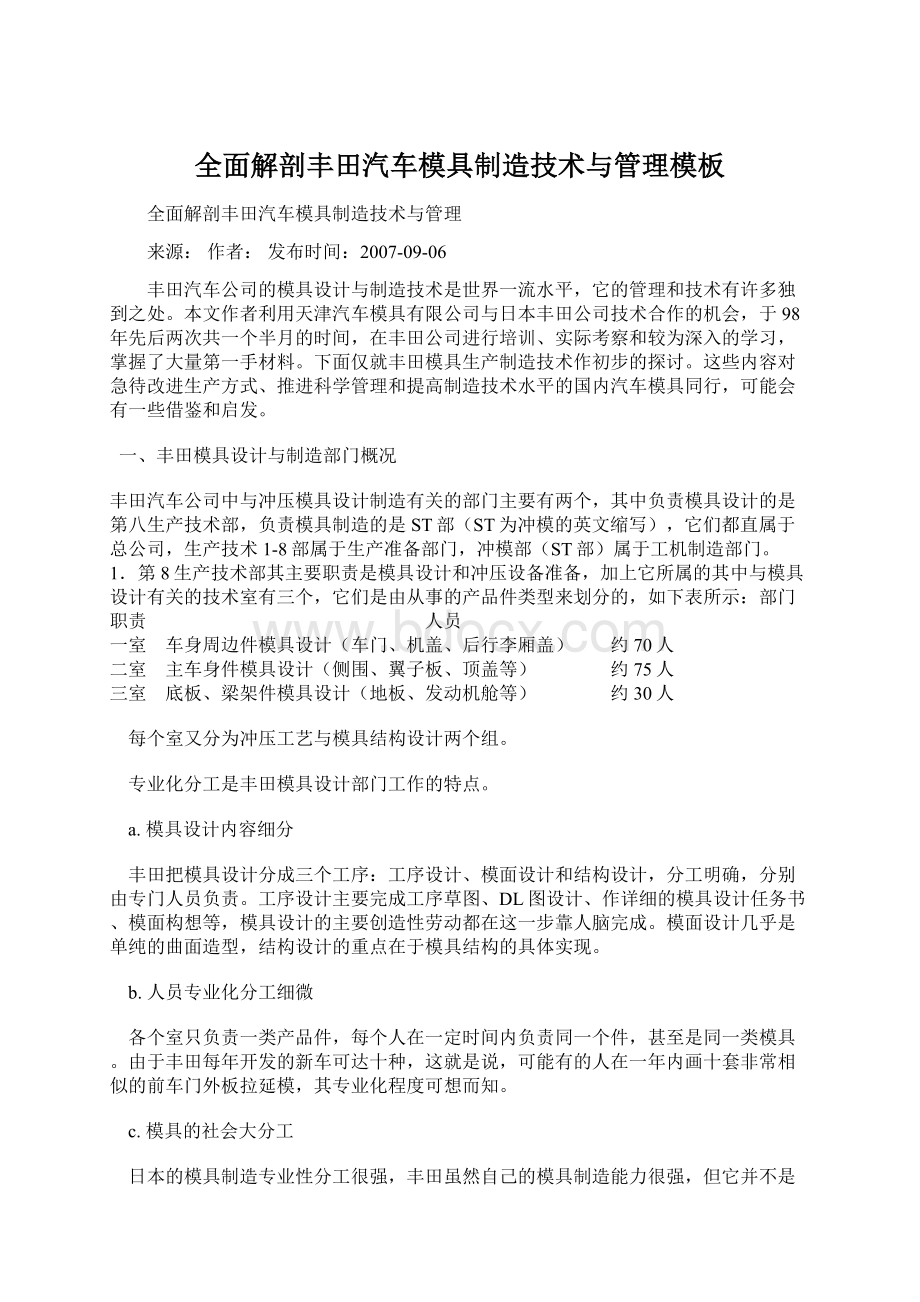
一室 车身周边件模具设计(车门、机盖、后行李厢盖) 约70人
二室 主车身件模具设计(侧围、翼子板、顶盖等) 约75人
三室 底板、梁架件模具设计(地板、发动机舱等) 约30人
每个室又分为冲压工艺与模具结构设计两个组。
专业化分工是丰田模具设计部门工作的特点。
a.
模具设计内容细分
丰田把模具设计分成三个工序:
工序设计、模面设计和结构设计,分工明确,分别由专门人员负责。
工序设计主要完成工序草图、DL图设计、作详细的模具设计任务书、模面构想等,模具设计的主要创造性劳动都在这一步靠人脑完成。
模面设计几乎是单纯的曲面造型,结构设计的重点在于模具结构的具体实现。
b.
人员专业化分工细微
各个室只负责一类产品件,每个人在一定时间内负责同一个件,甚至是同一类模具。
由于丰田每年开发的新车可达十种,这就是说,可能有的人在一年内画十套非常相似的前车门外板拉延模,其专业化程度可想而知。
c.
模具的社会大分工
日本的模具制造专业性分工很强,丰田虽然自己的模具制造能力很强,但它并不是什么模都干。
比如,整车所有件的冲压工艺和模具的整车协调,他自己都负责,但模具设计和制造他只干车身内外覆盖件,地板和梁架件全部到定点厂家外协。
不但丰田如此,国外的大汽车公司所属模具厂无不如此,比如日本大发公司模具厂,甚至只做侧围、翼子板、顶盖等有限的几种外覆盖件。
这可以看作是一种发展趋势,在韩国、台湾甚至是专业模具厂家也是向只做几种件的更专业方向发展。
2.模具制造部(ST部)
丰田ST部负责模具制造和新车整车模具的协调,并一直到大批量生产之前的冲压生产准备。
ST部构成:
科室 责任 人员
技术室 生产技术开发、生产计划、生产准备、设备计划 89人
NC课 NC编程、检查 175人
实型课 验具、实型制造 142人
机械课 机械加工 173人
钳工课 钳工、装配 237人
调试课 试模、调试 204人
合计 1020人
主要数控加工设备:
构造面加工数控铣床 39台
型面加工高速、五轴五面铣 15台
新型一体化加工设备 6台
其他小件加工设备 31台
总计 92台
从人员和生产能力上看,ST
部都算得上是世界上最大的汽车模具厂之一。
3.丰田的模具设计和制造能力
模具设计与制造能力 每年大约可开发10个轿车整车模具
模具产量(标准套)
约2000套/年,内制率60%(外协40%)
主要产品中 模具占80%,验具占7%,其他占13%
全年完成模具制造成本预算
近200亿日元
人均模具产量
2标准套/人.年
模具制造成本(不含设计)
约600万日元/套
工时成本(平均)
约1万日元/小时
整车模具设计制造周期
12个月
(由车身设计完成至新车批量生产)
其中包括整车全部模具设计周期
5个月
制造周期
调试周期
6个月
由此可见,丰田一年的轿车生产能力大约500万辆(日本国内部分约占50%),是中国大陆轿车产量的十倍,而模具设计制造能力也超过我们全国汽车模具生产能力的数倍。
丰田的标准单套模具制造周期为三至四个月。
4.丰田一般模具制造周期
丰田把模具的制造计划标准化,根据模具的复杂程度可分为短周期、标准周期和长周期三种。
现以单套模具的设计制造周期(拉延模,标准周期)为例:
冲压工艺
20天------------------------
模具设计 20天-------------
模面设计 8天--------
NC编程 15天 ---------
实型制作 7天 ------
铸造 12天 ------
机加工 9天 -----
钳工装配 7天 ---
单套拉延模总周期
62天
其中制造周期
52天
以上周期包括模具的设计、制造直至模具初次试模完成为止。
如果再考虑产品件各序模具的总周期,单个制件各序模具的总周期,要在拉延模的基础上再加22天(包括模具调试,但不包括整车调试),总共84天。
以上天数均为工作日(节假日除外),换算为日历日大约为20天等于一个月,也就是单套模具制造周期三至四个月。
丰田的模具制造也是按照准时化生产方式进行的,全部倒排计划,计划到每一个工作日,不提前投产,避免增加在产模具。
我们的倒排计划往往是为赶工期,人为的压缩工期。
而丰田的倒排计划,是为了在必要的时候生产出必要的产品,避免提前投产造成生产过剩的浪费。
二、丰田模具制造技术
丰田的模具技术在日本的模具厂家中也是十分突出的,无论是能力、效率及技术都不愧为世界一流水平。
通过对丰田的了解我们可以看到,世界汽车模具制造技术正在向这些方向发展:
计算机前的操作逐步代替现场操作,以高精度加工代替人的手工劳动,模具的设计、制造高度标准化,单件生产方式向流水线式生产方式发展等等。
丰田在以下一些地方值得我们很好的借鉴。
1.
冲压工艺设计
A.
精细模面设计
我们常说的模具设计实际上分为三个部分:
冲压工艺设计、模面设计和结构设计。
这三种设计的内容和侧重点是完全不同的,丰田的工作流程为先有冲压工艺设计然后指导模面设计和模具结构设计,分别由不同的人来做,专业分工很明确。
传统的冲压工艺设计采用工序图或是DL图,它的模面设计是非常粗略的,以这样的图纸指导下的工艺造型,必须在后序靠人工修整、制造工艺祢补,造成模具制造的人工钳修量很大、周期延长。
丰田在设计阶段通过计算机的曲面造型,完成模面的精细设计。
比如:
针对进料量不同设计各种拉延筋,同一套模不同部位的拉延筋截面不同,防回弹、过拉延处理,最小压料面设计,凸凹模不等间隙设计等等。
精细模面设计的结果,可以极大的减少型面加工,减少钳修,减少试模工时,它的作用非同小可。
对比之下,国内的模具设计还停留在结构设计阶段,模面设计没有受到很好的重视,模面实际上是靠后天完成,模具设计的落后造成了制造的落后,也就毫不奇怪了。
B.板料成型分析技术应用情况
丰田公司从5-6年前,开始应用有限元法做计算机模拟板料成型分析,主要应用的解算软件为美国的DYNA3D,他们经过了近三年的努力才达到实用水平。
目前,丰田建立了一个整车身各种典型件的分析结果库。
对一个新车型的件,如果成型性没有太大的变化,只是参考原工艺不做分析,只有特殊的新造型才做板料成型分析。
丰田的新车要做样车,对造型特殊的件除了做板料成型分析外一般还要做简易模进行验证。
因此,丰田人认为目前板料成型分析还不是一件必需的、简单的事,无论是周期还是成本都有很大代价。
本人认为,丰田的车型开发量很大,车型之间变化不大、类似件很多,又积累了丰富的人的经验,板料成型分析确实用武之地不多,建立一个分析结果库是一个好方法(日本富士模具公司也是这么做的)。
反观国内现状,一方面模具厂专业分工很低,各种件都会遇到,难有现成经验,似乎更需要板料成型技术。
另一方面,技术水平低支持环境差(如:
板料参数、摩擦系数等难掌握),模具厂应用起来,要达到实用(不讲效果、不计代价的研究不算)也是非常困难的。
即使是成立专业分析公司,考虑用户数量、周期、价格等因素,恐怕也曲高和寡。
目前,这项技术在国内的实际应用效果还难有定论。
C.
模面设计经验积累机制
丰田的设计部门除手工勾画草图以外,设计已全部计算机化,一般设计人员除一台工作站外还有一台笔记本电脑。
但真正创造性的设计还是靠人脑,特别是靠人的经验积累。
丰田特别强调经验积累机制:
只有集体的经验不能有只属于个人的经验,比如:
资料的统一管理,草图设计的小组讨论,图纸的多部门集体审核,设计标准、规范的经常性增改等等。
经验积累机制是丰田能够不断提高模面精细设计的主要手段。
模具加工完成之后,一般模具型面不用研合,刃口不必对间隙,钳工只负责安装,在初次试模时也不能随便修调模具,调试模具有模面设计人员在场,初次试模缺陷需要记录下来。
最后的休整结果,象拉延筋、拉延圆角变动、对称件的不对称现象等,还要进行现场测量。
这些资料的积累、整理、分析、存档,都是模面设计的经验积累,并随时加入到下一次的设计中去。
丰田的模具设计和调试过程,真正做到了是一个闭环制造系统,借助于这种自我完善的经验积累机制,模具的设计越来越精细,越来越准确。
D.间隙图设计
在丰田,模面设计实际上是由曲面造型和NC编程两部分共同完成的,为了传达和描述模面设计思想,就产生了除DL图、模具图之外的第三种图――间隙图,也叫质量保证图。
间隙图可能是丰田的一种创造。
模具设计不是单纯为了设计出一种能够完成一定动作的机器,设计的最终目的是为了保证它所压出的产品件是合格的,间隙图就是这样一种专为保证产品质量的图。
质量保证图中,主要包括这样几项内容:
模具实际符型面区域、各个符型区域的间隙值、工艺要求的模面变化情况、拉延圆角的变化、各种模面的挖空等等。
凡是无法通过曲面造型实现的模面设计,都通过间隙图的传达,依靠NC编程的设计来实现,在这里NC编程也不再是单纯的实现模具结构的加工,它实际上也参与到模面设计中来了。
因此,间隙图的应用也是精细模面设计的一种必然。
E.大规模生产对模具的影响
材料利用率:
对于大批量汽车生产来说,提高板