分解槽沉降槽制作安装施工方案Word文档下载推荐.docx
《分解槽沉降槽制作安装施工方案Word文档下载推荐.docx》由会员分享,可在线阅读,更多相关《分解槽沉降槽制作安装施工方案Word文档下载推荐.docx(26页珍藏版)》请在冰豆网上搜索。
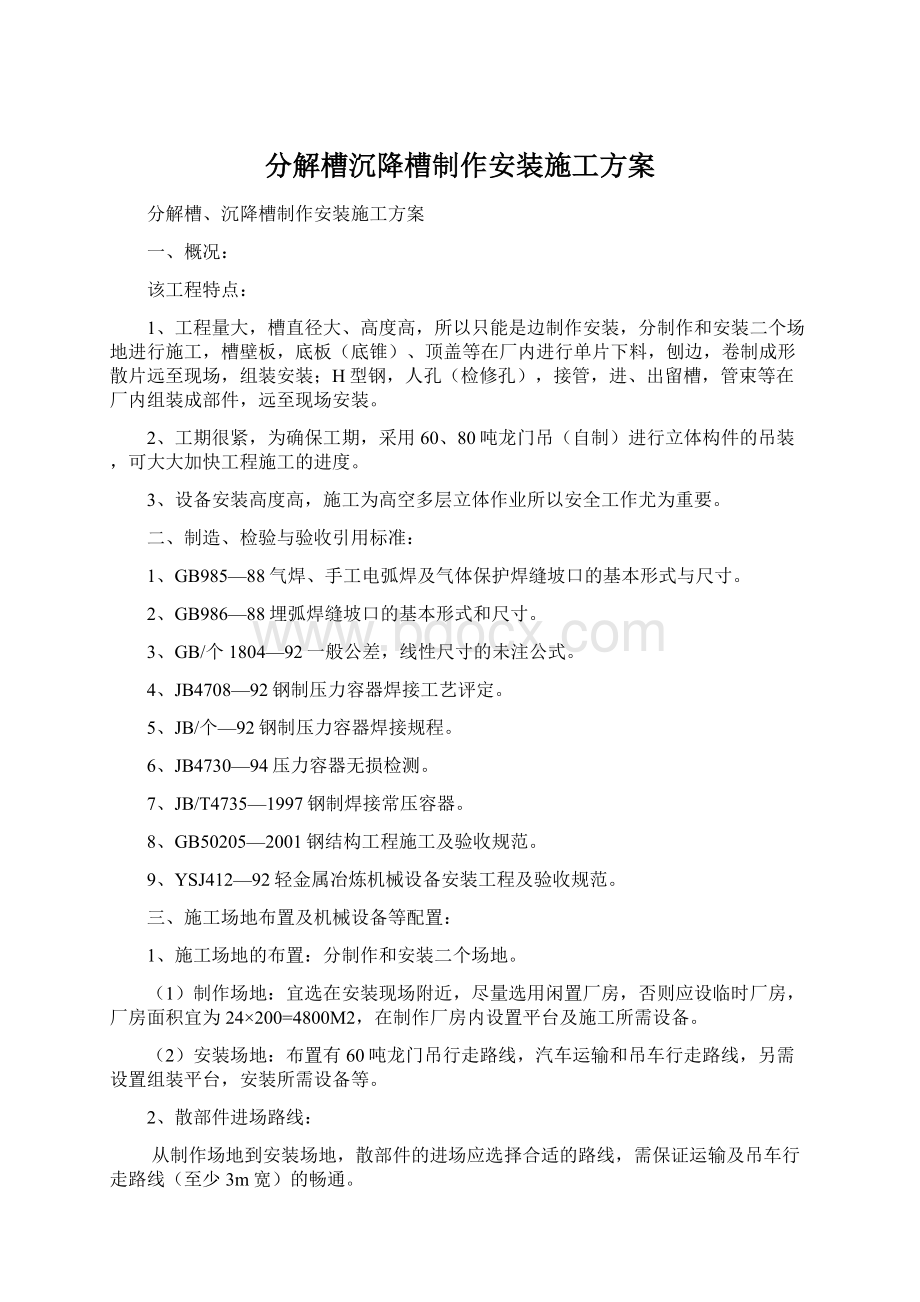
包括双梁桥吊,电焊机、卷板机、刨边机、空压机、组装平台、H型钢组装胎,船形焊接胎等。
(见表2)
安装场地应配置安装施工所需设备:
包括60吨龙门吊(图1)性能表(见表3)坦克吊、电焊机、空压机、真空泵、组装平台等。
表1、制作场地设备配置表
序号
名称
规格
数量
用途
1
双梁桥吊
30/t
2
材料、散件、部件的吊装
滚床
20×
2000
槽壁板δ20以下曲弧
3
50×
4000
槽壁板δ20以上曲弧
4
油压机
500t
槽顶拱板,锥底板的成形
5
多嘴切割机
自制
长条板的切割
6
半自动切割器
钢板的切割
7
氧乙炔切割器
12
小零件的切割及部件变形矫正
8
刨边机
12M
底板、槽壁板的坡口加工
9
交直流两用电焊机
WS—400B
焊接、碳弧气刨清根
10
埋弧自动焊
MZ—100
H型钢船形焊及其它自动焊
11
CO2焊机
YD—350KR
部件组装焊接
空压机
6m3
焊缝碳弧气刨清根
13
焊条烘烤箱
烘烤电焊条
14
超声波探伤仪
CTS—22
制作、安装焊缝检测
15
组装平台
10×
20M
部件组装
16
H型钢组装胎
H型钢组装
17
船形焊接胎
H型钢焊条
18
H型钢矫直机
H型钢矫直
19
成形胎具
拱顶,锥底形
槽顶、锥底成形
20
角向磨光机
焊缝余高及焊缝坡口等打磨
21
X射线探伤仪
300EG—S2
现场焊接焊缝检测
表2、安装场地设备配置表
龙门吊
60t
槽体立体,顶盖等大段吊装
坦克吊
80t
底板(锥底)安装,槽段节单节组装
交直流电焊机
WS-400B
焊接,碳弧气刨清根
YD-350KR
36
组装、焊接
真空泵
底板严密试验
焊条的烘烤
半自动氧乙炔切割器
槽壁板余量切割
切割与开孔
16×
16m
槽段节单节及大段组装
焊缝坡口壁板表面打磨
表3、60t龙门吊技术性能
参数
单位
数据
备注
骨架高度
m
46.2
跨距
18.840
净空高度
44.6
净宽
17.64
起重量
t
60
大车行走速度
m/min
16.6
电机
4、其他施工临时设施配置(见表4)
在安装现场还需配置空压机输气管线,遍及各槽全场;
配置内外吊兰用于高空作业时,大段槽节环缝的组装和焊接;
另外为避免槽段节吊装时的变形,需制作吊装横扁担作吊装具,在槽体内壁段节上,下端口加米字支撑。
表4、其他施工临时设施表
数量
输气管线
Φ42×
全场布置
碳弧气刨清根,压缩空气管线
内、外吊兰
各4付
高空作业脚手架
横扁担
2付
安装大段筒节等吊具
手动葫芦
1~3t
若干
吊装时辅助吊点
米字支撑
6付
槽筒体内支撑(防变形)
四、施工条件要求:
1、材料(重点主材)配套到位,确保及时开工;
确保制作安装工程施工进度。
2、制作按三台一组配套制作,确保现场安装工程施工进度的需要。
3、满足施工用电需求(制作:
600KW;
800KW)
4、土建设备基础,按时交付使用。
5、60吨龙门场地在安装前平整,铺设为轨道,龙门吊设备安装完毕;
运输及吊车行走路线道路需平整好;
组装平台在场地平整后铺设好。
五、制作:
1、工艺流程:
(1)分解槽底板:
下料→平整→刨边→散片出厂
(2)槽壁板:
下料→刨边→成形→散片出厂
(3)H型钢,留槽等:
下料→组装→焊接→部件出厂
(4)接管、管束、人孔、检修孔等:
下料→法兰加工→成形→组装→焊接→部件出厂
2、方法和步骤、及技术要求
(1)下料前应按钢材证明书核对并逐张(件)进行外观检查,表面不得有裂纹、拉裂、折叠、夹杂、结疤和压入氧化皮及分层等缺陷;
槽壁用钢板,当厚度δ≥22mm时,应按JB4730进行超声检测,质量等级应符合Ⅲ级要求,检查数量按钢板张数的20%进行抽查,发现有不合格者,应逐张检查。
(2)下料时要留出足够的焊接收缩余量及刨边余量,每圈槽壁板由多张组成,应在其中一张上加数50mm的余量。
槽壁数,底板中幅板的尺寸允许偏差见表5底板弓形板的尺寸允许偏差见表6,其余按GB/个1804规定的C级要求。
组装时法兰面应垂直于接管或圆筒的主轴中心线。
(4)成形:
槽壁板的成形采用卷板机卷制;
底锥、拱顶板的成形宜用专用模具在500时油压机上冷压成形。
槽壁板卷制成形应立置在平台上检查,垂直方向上用直线样板检查其间隙不得大于1mm,水平方向上用弧形样板检查其间隙不得大于4mm;
拱顶板成形后用弧形后用弧形样板检查其间隙不得大于10mm。
表5单位:
mm
测量部位
环向对接
环向搭接
板长AB
CD≥10000
CD<
10000
宽度AC、BD、EF
±
1.5
长度AB、CD
对角线|AD-BC|
≤3
≤2
直线度
AC、BD
≤1
AB、CD
表6单位:
测量部位
允许偏差
对角线之差|AD—BC|
(5)H型钢组装与焊接:
H型钢组装在组装胎上进行,翼缘板和腹板的拼接缝间缝间距应大于200mm,拼接焊接在H型钢组装前进行,拼接后应按GB11345进行100%超声波探伤Ⅱ级合格。
H型钢焊接在船形焊接胎上进行,焊接后用H型钢矫直机进行矫正。
矫正后应符合表7的规定。
(6)进、出料管与支承板,挡板分2~3段组装焊接后出厂。
(7)沉降槽的机装置、分解槽的搅拌装置一般外方供货。
表7、焊接H型钢的允许偏差(mm)
项目
允许偏差
H〈500
2.0
500≤h≤1000
3.0
H〉1000
4.0
截面宽度(b)
腹板中心偏移(e)
翼缘板垂直度(△)
b/100
弯曲矢高
/1000
5.0
扭曲
h/250
腹板局部平面度(f)
t<
t≥14
(4)补充:
角钢圈采用卷板机分段卷制成形,成形后用火焰进行矫正,矫正后的每段角钢圈应用样板检查弧度间隙≤1mm,不垂直度(△C)
3、关键控制点:
(1)下料尺寸的控制。
(2)槽壁板,角钢圆弧度成形控制。
(3)焊接H型钢外形及接质量控制。
(4)部件外形尺寸及焊接质量的控制。
六、安装:
1、安装的顺序:
设备基础的复制—→底板铺设拼焊—→弓形边缘板焊缝检测—→底板焊缝真空严密性试验—→底筒段安装—→地脚螺栓埋设—→各段节筒体(包括角钢圈)安装—→接管、人孔、检修门、进、出槽的安装—→焊缝检测—→热处理—→顶盖安装—→搅拌装置安装—→盛水试验—→总检验收。
2、方法、步骤及技术要求:
(1)安装前,必须对基础表面尺寸进行检查,合格后方可开始安装。
基础中心座标偏差不应大于20mm,标高偏差不得大于20mm。
顶面水平度要求:
a、环墙式基础,上表面任意10m弧长上不得超过±
3.5mm,在整个圆周上以平均标高计算不超过±
6.5。
b、护坡式基础,上表面任意3m弧长上不应超过±
3.0mm,在整个圆周上以平均标高计算不超过±
12mm。
(2)分解槽底板铺设前,其下表面应涂刷防腐涂料,每块底块边缘50mm范围内不刷。
(3)底板采用带垫板的对接接头时,对接接头应完全焊透,表面应平整。
垫板应与对接的两块底板贴紧,其间隙不得大于1mm。
接头间隙为7±
1mm。
(4)中幅板采用搭接接头时,搭接宽度允许偏差为±
5mm。
(5)搭接接头三层钢板重叠部分,应将上层底板切角,切角长度应为搭接长度的2倍,其宽度应为搭接长度的2/3,在上层底板铺设前,应先焊上层底板覆盖部分的角焊接接头。
(见图2)
图2底板三层钢板重叠部分的切角
A:
上层底板B:
A板覆盖的焊接接头L:
搭接宽度
(6)槽壁板组装:
1)槽壁板组装前,应对预制的壁板进行尺寸外形复验,合格后方可组装。
需要校证时,应防止出现锤痕,单节筒体及大段节筒节组装在组装平台上进行,单节筒体纵缝焊接应留出一道纵缝(留50mm余量的()板)不焊待其他焊缝焊完后,用盘尺量出周长,用半自动切割多余部分后开好坡口再进行最后一道纵缝的组装焊接,以确保筒体的直径正确。
2)对接的壁板组装应符合下列规定:
A底圈壁板:
a、相邻两壁板上口的水平允许偏差,不应大于2mm。
在整个圆周上任意两点的水平允许偏差,不应大于6mm;
b、壁板的铅垂度允许偏差,不应大于3mm;
c、组装焊接后,