下料车间管理规定文档格式.docx
《下料车间管理规定文档格式.docx》由会员分享,可在线阅读,更多相关《下料车间管理规定文档格式.docx(4页珍藏版)》请在冰豆网上搜索。
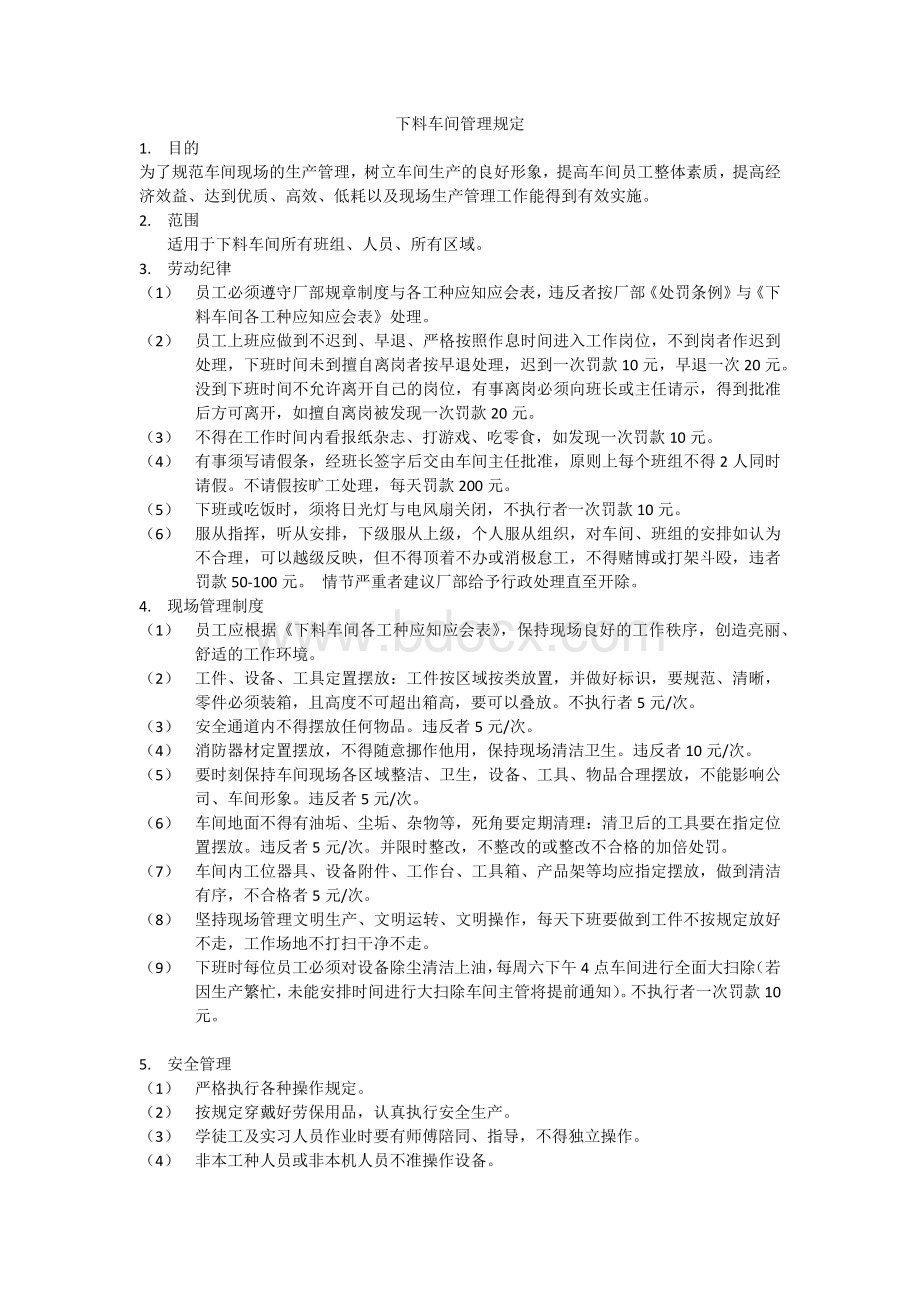
(2)员工上班应做到不迟到、早退、严格按照作息时间进入工作岗位,不到岗者作迟到处理,下班时间未到擅自离岗者按早退处理,迟到一次罚款10元,早退一次20元。
没到下班时间不允许离开自己的岗位,有事离岗必须向班长或主任请示,得到批准后方可离开,如擅自离岗被发现一次罚款20元。
(3)不得在工作时间内看报纸杂志、打游戏、吃零食,如发现一次罚款10元。
(4)有事须写请假条,经班长签字后交由车间主任批准,原则上每个班组不得2人同时请假。
不请假按旷工处理,每天罚款200元。
(5)下班或吃饭时,须将日光灯与电风扇关闭,不执行者一次罚款10元。
(6)服从指挥,听从安排,下级服从上级,个人服从组织,对车间、班组的安排如认为不合理,可以越级反映,但不得顶着不办或消极怠工,不得赌博或打架斗殴,违者罚款50-100元。
情节严重者建议厂部给予行政处理直至开除。
4.现场管理制度
(1)员工应根据《下料车间各工种应知应会表》,保持现场良好的工作秩序,创造亮丽、舒适的工作环境。
(2)工件、设备、工具定置摆放:
工件按区域按类放置,并做好标识,要规范、清晰,零件必须装箱,且高度不可超出箱高,要可以叠放。
不执行者5元/次。
(3)安全通道内不得摆放任何物品。
违反者5元/次。
(4)消防器材定置摆放,不得随意挪作他用,保持现场清洁卫生。
违反者10元/次。
(5)要时刻保持车间现场各区域整洁、卫生,设备、工具、物品合理摆放,不能影响公司、车间形象。
(6)车间地面不得有油垢、尘垢、杂物等,死角要定期清理:
清卫后的工具要在指定位置摆放。
并限时整改,不整改的或整改不合格的加倍处罚。
(7)车间内工位器具、设备附件、工作台、工具箱、产品架等均应指定摆放,做到清洁有序,不合格者5元/次。
(8)坚持现场管理文明生产、文明运转、文明操作,每天下班要做到工件不按规定放好不走,工作场地不打扫干净不走。
(9)下班时每位员工必须对设备除尘清洁上油,每周六下午4点车间进行全面大扫除(若因生产繁忙,未能安排时间进行大扫除车间主管将提前通知)。
不执行者一次罚款10元。
5.安全管理
(1)严格执行各种操作规定。
(2)按规定穿戴好劳保用品,认真执行安全生产。
(3)学徒工及实习人员作业时要有师傅陪同、指导,不得独立操作。
(4)非本工种人员或非本机人员不准操作设备。
(5)发生人身、设备安全事故按厂部规定及程序及时上报。
对于违反上列安全管理规定的,按厂部《安全处罚条例》处理。
6.备注
(1)对于限期整改而未整改的,加倍从重处罚。
(2)本制度如有与公司制度、规定相违背的,以公司制度规定为准。
四维源创下料管理系统是从生产实践中诞生,是一套实用性非常强,经济实惠型的管理软件,该下料管理系统有如下十五大亮点:
1、下料工艺数据标准化:
实现以零件为中心的标准化数据库,技术人员将设计和工艺数据直接分解到系统标准下料工艺作业指导书,并保存至系统数据库,客户项目下料生产BOM的设计和工艺数据直接从系统读取,实现无图化生产。
2、下料程序图数据标准化:
对零件下料程序图基础数据进行批量导入或单个新建,相同零件只需导入或新建一次。
下料生产计划下达后系统直接读取下料程序基础数据并自动附加生产信息并自动分包进行排料,大大提高排料前数据准备效率。
3、计划零件属性优化:
计划下达时系统对零件进行自动编号,各环节查找零件只需查找零件编号即可,大大提高标识书写,收料码放分类,零件成套清点等工作效率。
4、计划无限整合:
系统内下料计划可任意合并或调取,大大提升套料利用率。
5、钢板编号管理:
系统对入库钢板或套料切割后的余料进行自动编号管理,结合现场钢板码放技巧,无论边料或整板切割可快速找到所需钢板,大大提高现场管理和余料利用效率。
6、钢板余料管理:
对排料利用率较低钢板可多次生成精确余料并自动编号入库(附简图),确保下次套料切割时余料优先利用,减少余料库存,大大提高材料利用率。
7、档案文件管理:
系统集成档案文件管理的附属功能,对纸质文件进行扫描存档,分类管理,实现快速查找。
8、支持零件多种拼接方式:
为了充分利用材料,减少余料产生,零件的拼接数量在满足技术工艺要求时,还可充分利用板材尺寸进行套料。
即板材尺寸如果不一样,那么零件的拼接数量就可能会发生改变。
本系统支持零件多种拼接方式,可根据现有钢板尺寸选择最为适合的拼接方式,以充分提高材料利用率。
9、支持各类套料软件:
可与各类套料软件实现系统集成。
10、利库管理:
系统计划导入时,后台自动比对库存并按计划自动提取库存零件,规划企业标准件库存的下料数量,保证下料零件库存数据的合理性。
11、预算钢板需求:
计划导入后所需材料自动与板材库进行比对,可快速提出材料差缺需求清单。
12、ERP数据反馈:
下料完毕后系统向ERP提供所需的反馈数据,包括排料清单、板材利用清单、下料零件清单等。
13、切割优先级别:
计划下达时根据生产任务计划要求,确定切割零件的优先级别,按项目零件优先级别自动生产切割优先顺序,确保产品及时成套。
14、临时计划一键下达:
零件补废、补失任务一键下达。
15、可视化管理:
下料生产的技术工艺准备和下料零件生产状态用颜色进行分类分序可视化管理