塑料模具课程设计B1结构件Word文档格式.docx
《塑料模具课程设计B1结构件Word文档格式.docx》由会员分享,可在线阅读,更多相关《塑料模具课程设计B1结构件Word文档格式.docx(17页珍藏版)》请在冰豆网上搜索。
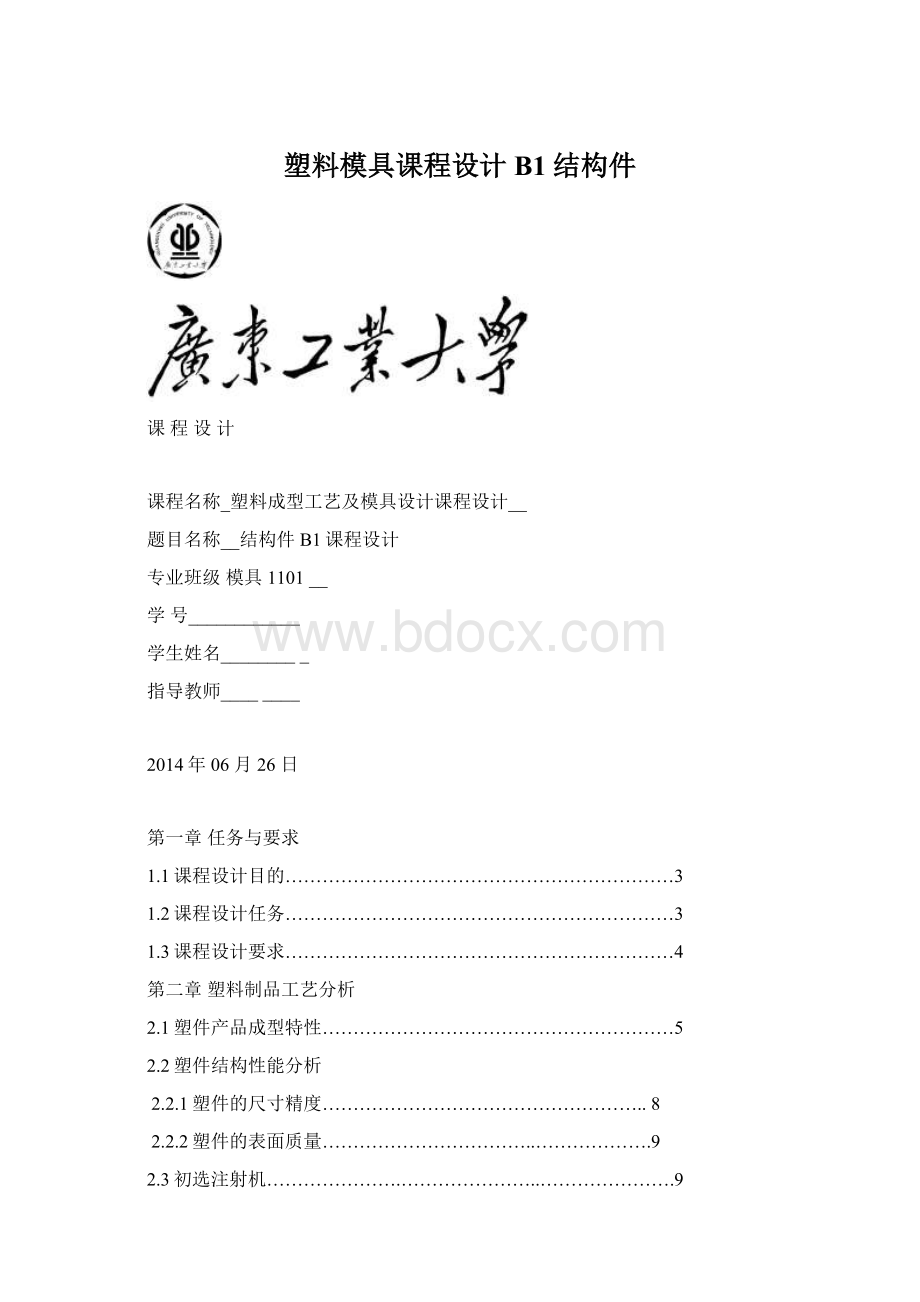
3.1选择分型面………………………………………………………10
3.2确定型腔数目……………………………………………………12
3.3设计浇注系统,安排型腔排列…………………………………12
3.4冷却系统设计……………………………………………………16
3.5脱模方式及设计…………………………………………………17
3.6确定型腔和型芯结构及固定方式………………………………18
3.7模具型腔壁厚的确…………………..………………..…………22
3.8模具与注射机有关尺寸校核…………………………………….24
1.1课程设计的目的
塑料成型模具课程设计是在修完专业课程《高分子材料科学》和《塑料成型工艺及模具设计》及其他的一些相关课程之后,进行的一个实践性教学环节。
目的在于加深对本专业主干课程《塑料成型工艺及模具设计》课程的理解,更好掌握该课程的知识要点。
要求通过本课程设计的训练,掌握以下知识和技能:
1.掌握各种常用塑料成型基本原理及工艺特点,能够分析判断成型工艺的合理性,根据塑料成型的特点进行一般塑料制品的工艺设计。
2.掌握塑料成型模具的设计程序,熟悉塑料注射成型模具的几种典型结构,掌握各种成型模具的结构特点及设计计算方法,独立完成设计一套具有一定复杂程的塑料模具。
3.了解塑料成型模具的制造、装配要求。
4.了解塑料成型模具的试模、验收方法和标准,了解塑料成型模具的使用环境和要求,了解塑料制品在成型加工过程常出现的一些缺陷,初步培养分析塑料制品在成型加工过程出现常见缺陷所产生的原因。
5.能够熟练使用有关设计手册和参考资料。
1.2课程设计的任务
1.对任务书指定的塑料零件进行工艺分析及工艺计算。
并确定模具结构。
2.根据模具的结构和尺寸选择使用的注塑机型号;
3.设计该塑件的注射成型模具,计算各成型零件尺寸,校核主要零件的强度硬度;
4.绘制所设计模具的装配图和零件图,完成1.5张零号图纸的工作量;
5.编写设计计算说明书,用本校设计说明书专用纸书写(约25页)并装订成册。
1.3设计要求
1.在规定时间内独立完成自己的设计任务;
2.及时了解有关资料,作好准备工作,充分发挥自己的创造性;
3.要求计算准确,结构合理,图面整洁,图样和标注符合国家标准;
4.设计说明书要求表达清楚,句子流畅,书写工整,插图清晰整齐。
第二章塑料制品工艺分析
2.1塑件产品成型特性
结构件材料为聚氯乙烯,简称PVC。
PVC材料分软质PVC和硬质PVC,硬质PVC(未加增塑剂)具有良好的机械强度、耐候性和耐燃性,可以单独用做结构材料。
符合塑件作为结构件的要求,故选用硬质PVC。
硬质PVC为热塑性材料,密度为1.35~1.45g/cm3。
硬PVC的抗拉强度为35~50MPa,压缩比为2.3,拉伸弹性模量为2.4~4.2*10^3。
力学性能强度高,电气性能良好,耐酸碱力极强,化学稳定性好,但软化点底。
产品的成型特性:
(1)无定形料,吸湿小,流动性差.为了提高流动性,防止发生气泡,塑料可预先干燥。
模具浇注系统宜粗短,浇口截面宜大,不得有死角,模具须冷却,表面镀铬;
(2)由于其腐蚀性和流动性特点,最好采用专用设备和模具。
所有产品须根据需要加入不同种类和数量的助剂;
(3)极易分解,在200度温度下与钢.铜接触更易分解,分解时逸出腐蚀,刺激性气体,成型温度范围小;
(4)采用螺杆式注射机喷嘴时,孔径宜大,以防死角滞料,好不带镶件,如有镶件应预热。
2.2.1塑件的尺寸精度
产品塑件的尺寸精度无特殊要求,所有尺寸都为自由尺寸,聚氯乙烯(PVC)可采取建议精度8级。
按MT8精度查取公差,塑件上主要尺寸的公差见
塑件标注尺寸
塑件尺寸公差
外形尺寸
50
0.64
89
-1.00
58
-0.74
97
30
-0.50
2.5
-0.2
内形尺寸
82.5
+0.5
45
+0.64
84
+1.00
孔尺寸
3
+0.20
6.56.5
+0.28
孔间距尺寸
1818
±
0.19
36
0.28
9
0.14
2.1.2塑件表面质量分析
塑件为结构件,在使用上只要求一般的配合精度,但是表面精度要求高,外表面粗糙度Ra:
1.6μm,故比较难实现。
由以上分析可见,该零件结构属于简单构件,结构工艺性合理,不需要对制件的结构进行修改。
塑件的尺寸精度要求不高,对应的模具零件的尺寸加工容易保证。
注射时,在工艺参数控制得较好的情况下,制件的成型要求可以得到保证。
2.3初选注射机
因为塑件是大批量生产,且生产的精度要求不高,故采用一模两腔的设计方式
(1)注射量的计算:
通过UG建模分析,塑件的体积V为7108.3732mm^3,塑件的质量:
m=
=1.38×
7108.3732=9.952g(
=1.38g/cm^3)
此时流道凝料的体积未知,可按塑件质量的0.6倍进行估算,所以注射量为:
m总=1.6×
nm=1.6×
2×
9.952=31.85g
V总=1.6×
nV=1.6×
7108.3732=22746.79mm3
(2)选择注塑机:
根据上面计算的注射量和锁模力,可选用国产XS-ZY-60
序号
主要技术参数
参参数值
11
最大注射量/cm^3
12560
22
注射压力/MPa
60122
33
锁模力/kN
500
44
动、定模版最大安装尺寸/(mm×
mm)
330×
440
55
最大模具厚度/mm
30070~250
666
最小模具最大开距/mm
200380
77
最大开模行程/mm
300180
3.1分型面及其浇注系统的设计
分型面是指分开模具取出塑件和浇注系统凝料的可分离的接触表面。
一副模具根据需要可能有一个或两个以上的分型面,分型面可以是垂直于合模方向,也可以与合模方向平行或倾斜。
分型面的形式与塑件几何形状、脱模方法、模具类型及排气条件、浇口形式等有关,我们常见的形式有五种:
水平分型面、垂直分型面、斜分型面、阶梯分型面、曲线分型面。
分型面的选择原则主要如下:
(1)符合塑件脱模:
为使塑件能从模具内取出,分型面的位置应设在塑件断面最大尺寸的部位。
(2)分型面的数目和形状:
通常只采用一个与开模运动方向相垂直的分型面。
确定分形面应以模具制造及脱模方便为原则。
(3)型腔的选择:
尽量防止形成侧孔和侧凹,以避免采用较复杂的模具结构。
(4)确保表面质量:
分型面尽量不要选择塑件光滑的外表面,避免影响塑件的外观质量;
将塑件要求同轴度的部分放在分型面的同一侧。
以确保塑件的同轴度;
要考虑减小造成塑件大、小端的尺寸差异要求等。
(5)有利于塑件脱模:
由于模具的脱模机构通常设置在动模一侧,故尽可能使开模后塑件留在动模一侧。
(6)考虑侧向轴拔距。
一般机械式分型抽芯机构的侧向轴拔距都较小,因此选择分型面的时应将抽芯或分型距离长的方向置于动、定模的开合模方向上,即将短轴拔距作为侧向分型或抽芯。
并注意将侧抽芯放在动模边,避免定模抽芯。
(7)锁紧模具的要求:
侧向合模锁紧力较小,故对于投影面积较大的大型塑件,应将投影面积大的方向放在动、定模的合模方向上,而将投影面积小较小的方向作为侧向分型面。
(8)有利于排气。
当分型面作为主要排气渠道时,应将分型面设计在塑料的流动末端,以利于排气。
(9)模具零件易于加工。
分析分型面,有以下3个方案:
方案一:
单分型面注射模:
型腔在动模模上,主流道设在定模一侧,分流道设在分型面上,利用斜滑块分型推出。
开模时塑件连同流道内的凝料一起留在动模一侧。
动模上有顶出机构,用以顶出塑件和流道内的凝料。
可能的浇口形式有:
直接浇口、侧浇口、扇形浇口。
方案二:
半边型腔在动模上,半边型腔在定模,主流道设在定模一侧,分流道设在分型面上,利用斜导柱测抽芯孔。
适合的浇口形式有:
点浇口、直接浇口、侧浇口等。
该类模具采用的侧抽芯机构一般是斜导柱在定模,滑块在动模。
该制件为结构件,要求外表光滑,无痕迹。
可选用的浇口形式有点浇口和潜伏式浇口、护耳式浇口,其中侧浇口潜伏式浇口去除浇口留下的痕迹可选在加强肋上,对塑件外观无任何影响,但浇口的制造较为复杂;
由于塑件材料流动性差,用点浇口会出现浇不满的现象,且一般采用结构复杂的三板模;
护耳式浇口需要的注射压力较高,成型后去除耳槽比较麻烦;
斜导柱的抽芯距离过长不合理。
综上,选择方案一,单分型面注射模,侧浇口,采用斜滑块抽芯推出。
3.2确定型腔数目
该塑件的精度要求不高,属小型塑件,且形状简单,又为大批量生产,初定为一模两腔的模具形式,
3.3设计浇注系统,安排型腔排列
型腔的排列方式采用平衡性较好的I型排列,其布置方式如下图所示:
为了保证塑件表面质量要求,选择侧浇口成型,浇口位置安排在塑件圆环处,模具选用单分型面注射模。
(1)浇注系统选择和设计
所谓注射模的浇注系统是指从主流道的始端到型腔之间的熔体流动通道。
其作用是使塑件熔体平稳而有序地充填到型腔中,以获得组织致密、外形轮廓清晰的塑件。
浇注系统一般由主流道、分流道、浇口、冷料穴四个部分组成。
该塑件采用中心进料,重叠式浇口浇铸
主流道的设计
主流道尺寸(如图所示)
喷嘴孔直径d0=3.5mm
喷嘴前端球面半径SR0=12mm
根据模具直流到与喷嘴的关系得到:
主流道的进口端球面半径为:
SR=SP0+(1~2)=12+(1~2)=13mm
主流道进口端球孔直径d=d0+0.5=3.5+0.5mm,取d=4mm
主流道锥角取:
为了便于将凝料从主流道中拨出,其斜度取2~4°
。
(2)分流道的设计
该塑件的体检比较小,形状比较简单,壁厚均匀,但塑料流动性差,可见采用单点进料的方式。
可采用最常用的半圆形分流道。
查教材塑料模具设计指导书与资料汇编表9-6和表9-7,选取分流道横截面形状及其相应直径尺寸,在此取半圆形分流道直径D=6mm,深度t=3mm。
分流形状如图所示。
分流道的布置:
为了让分流道要能满足良好的压力传递和保持理想的填充状态,使凝料熔体尽快地分配到各型腔,因此,采用如下图所示衡式分流道结构:
(3)浇口的设计
浇口是连接分流道与型腔之间的一段细短通