滚塑产品质量问题及解决措施Word格式.docx
《滚塑产品质量问题及解决措施Word格式.docx》由会员分享,可在线阅读,更多相关《滚塑产品质量问题及解决措施Word格式.docx(31页珍藏版)》请在冰豆网上搜索。
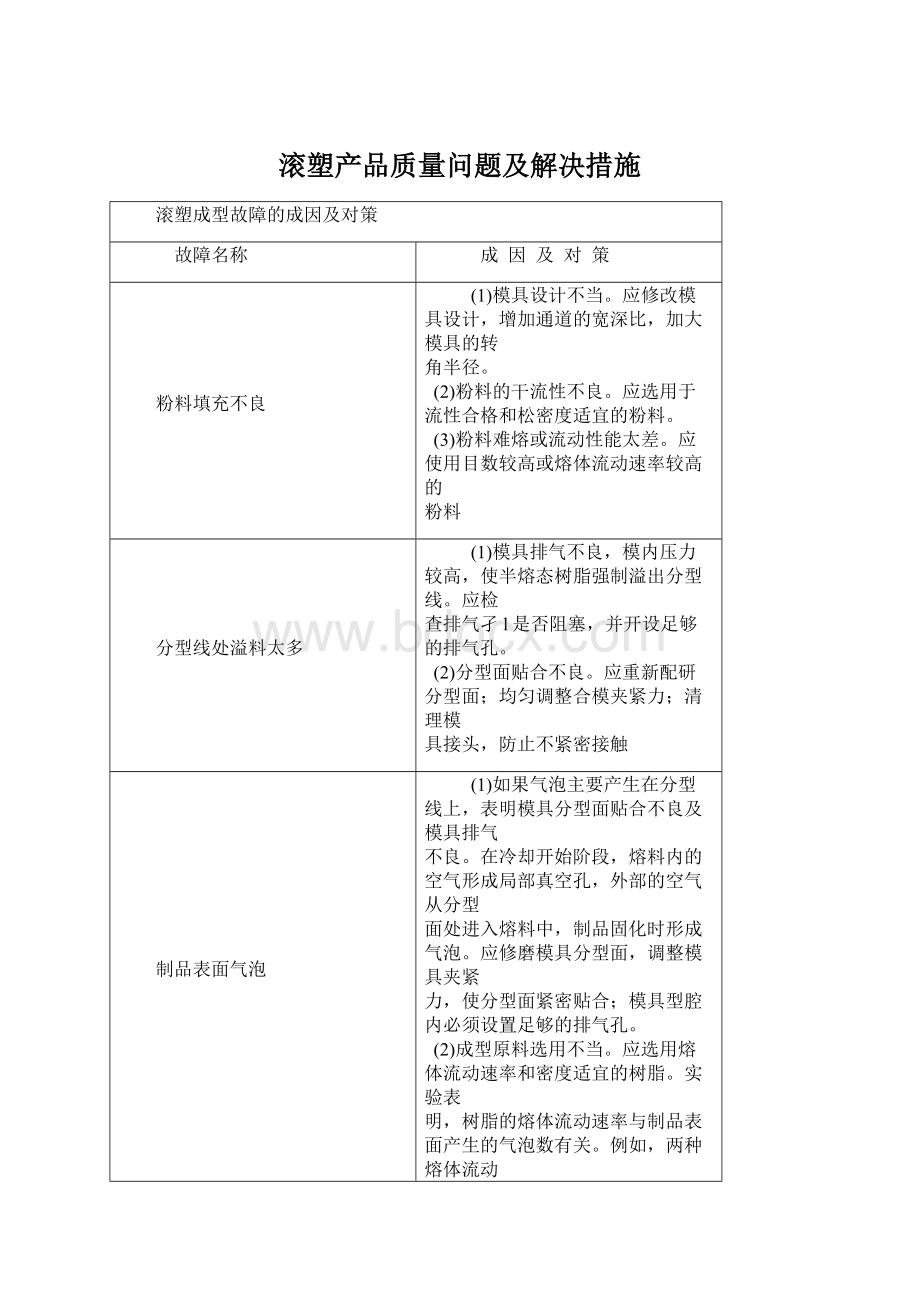
清理模
具接头,防止不紧密接触
制品表面气泡
(1)如果气泡主要产生在分型线上,表明模具分型面贴合不良及模具排气
不良。
在冷却开始阶段,熔料内的空气形成局部真空孔,外部的空气从分型
面处进入熔料中,制品固化时形成气泡。
应修磨模具分型面,调整模具夹紧
力,使分型面紧密贴合;
模具型腔内必须设置足够的排气孔。
(2)成型原料选用不当。
应选用熔体流动速率和密度适宜的树脂。
实验表
明,树脂的熔体流动速率与制品表面产生的气泡数有关。
例如,两种熔体流动
速率不同的聚乙烯树脂,虽然产生的气泡大小相同,但是熔体流动速率较大的
树脂所产生的气泡数较少。
一般应选用熔体流动速率为3—10g/10min的树脂。
此外,气泡的大小还与所用树脂及添加剂的粒度、形态和粒度分布有关。
一
般粒度越大,气泡越大,气泡数越少。
在选定树脂的粒度时,应根据制品的形
状而定,形状简单的塑件可采用颗粒较粗的树脂;
形状复杂、表面有精细花纹
的塑件,可采用颗粒较细的树脂。
通常采用200-900um粒度的粉料较为适
宜,最好为500um。
粒度的分布范围最好窄一些,但应有一定比例的小粒度
粉料以保证大粒度粉料的流动,且用量不能太多,否则会引起粉料熔融时结
块。
粉状树脂的颗粒形态以球体为佳,应尽量避免使用条状和片状颗粒。
(3)加工时间太短。
气泡的大小与加工时间有关,加工时间越长,气泡越
小。
适当延长加工时间及提高加工温度,有利于减少气泡。
(4)模具型腔表面有砂眼。
应塞焊并磨光
·
制品内表面粗糙
或有小气泡
(1)加热炉温度偏低。
应适当提高炉温或延长总加热周期。
(2)模具传热效率太差,树脂熔融不良。
应采用较薄的模壁,增加传热效
率。
也可采用导热系数较高的材料,如铝材、铜材等制作模具。
(3)树脂颗粒太粗。
应换用颗粒较细的粉状树脂。
一般,粒度在20-60目
之间为宜
制品壁厚不均匀
模具的旋转速比或速度控制不当。
应适当调整模具的旋转速比和速度,以
获得均匀的覆盖厚度和适当的粉末轨迹。
一般双轴旋转成型时,两轴的速比
不应为整数倍,这样可使每次旋转的螺旋物料流迹线互不重复。
通常,副轴
与主轴的速比为3:
10较为适宜。
不过,速比的设定主要取决于制品的形状
和结构
制品翘曲变形
(1)模具排气不良。
应设置足够的排气孔。
一般,薄壁制品每立方米模具容积应累计设置
10—13mm气孑L直径。
同时,应及时检查气孔有无堵塞。
(2)模具冷却不良。
在冷却期间继续旋转模具,并减少冷却周期初始阶段的冷却速度,适
当提高冷却介质的温度,先进行空气冷却,然后进行水冷。
冷却过程的关键是不能急剧冷却,
骤冷不但会降低模具的寿命,而且制品容易产生内应力,降低了抗冲击性能和耐环境应力开
裂性,风冷和水冷的时间关系应根据制品的形状及环境温度来确定,通常风冷时间是水冷时
间的6—8倍。
在冷却时,可通过芯轴施加气压。
(3)脱模剂用量太多。
应适当减少。
(4)制品结构设计不合理。
应在可能的情况下,尽量避免设计大而平的嵌板,制品的壁厚
也应尽量均匀。
(5)屏蔽板造成冷却不均。
应在安装模具时除去屏蔽板
制品内表面变色
(1)加热炉温度太高,树脂过热分解。
应适当降低炉温。
一般加热炉温度根据树脂的熔体
流动速率和制品的大小,应控制在250—350℃范围内。
由于提高加热温度会影响旋转部位轴
承的使用寿命,物料易分解,所以加热温度不宜太高。
(2)加热周期太长。
应适当缩短。
如果制品由于树脂过热分解产生变色,可采用氮气等惰
性气体吹洗制品
制品韧性不良
(1)制品壁太薄。
应适当增加投料量。
(2)树脂选用不当。
应使用密度较高的树脂。
(3)树脂熔融不良。
应适当提高成型温度或延长加热周期,提高模具的传热速度,使树脂
充分熔融。
一般对于低熔体流动速率的树脂,为了防止其分解,稍微欠熔融是可行的,但过分
欠熔融是不可取的。
应在可能的情况下修改设计
制品抗冲击强度
(1)树脂选用不当。
应使用密度较低或熔体流动速率较低的树脂。
树脂的密度对制品的
性能影响较大,密度高,制品的刚性大,但抗冲击性能差;
密度低,制品的抗冲击强度高,但刚
性差,耐化学药品性和耐环境应力开裂性也差,而且成型脱模困难。
因此,树脂的密度应适
中,一般滚塑成型时,树脂的密度为0,92—0.舛旷cm3为宜,熔体流动速率以3—lOg/lOmin
为宜。
(2)冷却速度太慢,使树脂密度增加。
应适当加快冷却速度,但也不能太快。
(3)模具设计不当。
应修改模具设计,消除小半径转角和狭窄通道。
(4)加热温度太高或加热周期太长,使树脂过热分解。
应适当降低炉温或缩短加热周期。
(5)树脂熔融不良。
应适当提高炉温或延长加热周期;
最好采用较薄的模壁,提高传热效
率,使树脂充分熔融。
(6)着色剂选用不当。
应选用不影响冲击强度的着色剂或着色填充物,也可使用着色性能
好的染色树脂或配人其他树脂
制品粘附模具
(1)脱模剂用量不足或选用不当。
应适当增加脱模剂的用量或换用热稳定性能较好的脱
模剂。
(2)分型面设置不当,制品取出时有阻碍。
应将模具的分型面设置在模壁的凹槽处或锥度
的端部。
(3)模具排气不良,模内压力使半熔态树脂强行通过分型面,导致粘模。
应设置足够的气
孔。
一般薄壁制品每立方米模具型腔容积应累计设置气孔直径lo—13mm。
(4)模具型腔表面太粗糙或有砂眼。
应抛光型腔表面或塞焊砂眼并修磨光滑。
(5)模具型腔内积留了一层树脂的分解焦化物。
应定期清理模具
加热周期太长
(1)模壁太厚,传热效率太差。
应采用较薄的模壁,提高传热速度,或采用导热系数较高的
材料制作模具。
(2)加热效率太低。
应在加热时适当增加模具周围空气的流动。
(3)加热炉温度太低。
应适当提高。
并注意控温仪表是否校准。
(4)粉料粒径太粗。
应使用目数较高的粉料
滚塑(rotationalmolding)生产过程中常见的产品质量问题及应对措施
(一)
在滚塑生产过程中,常常会出现一些大大小小的产品质量问题,这些都可以通过一些必要的措施来避免。
本文集中描述了一些滚塑成型工艺中
本文集中描述了一些滚塑成型工艺中的常见问题及解决方案,以期与大家共同探讨。
1.
插入嵌件不牢固或边缘周围有吹孔。
影响因素:
1.1插入嵌件尺寸不符合要求,周围空间太小,嵌件彼此太接近或太靠近模壁,局部受到屏蔽导致受热不均匀。
1.2安装嵌件时,未注意清洁,嵌件受到污染
1.3嵌件预热过度,插入后粘附粉料。
1.4嵌件固定不良,旋转模塑时松动。
1.5嵌件的材质影响。
有些导热性不强或过度导热。
可能的解决方法:
嵌件做良好固定,且保证其不要松动;
嵌件周围不要留有空隙,以免空气吸入造成湿气膨胀而侵入产品内部;
附着在嵌件上的污染物如牛油、机油会在成型时气化,从而产生气泡而让粉料无法粘附,使用前要对嵌件作适当的清洗、干燥处理;
使用大型的嵌件时要涂布兼容材料以保障其粘附效果;
如果嵌件材料具良好的导热性,可对嵌件进行轻微的屏蔽,避免嵌件过热而在产品截面产生气泡;
如嵌件导热性差,可提前预热至合适的温度。
2.
合模线处出现吹孔。
主要原因:
2.1合模线不干净
2.2通气管阻塞
2.3合模线错位
2.4成型时模内气压过大
2.5合模线变成热沉体。
解决方案:
确保合模线的干净是前提条件,合模线处残留的积塑会致合模线密封不良,模具外的空气会乘虚而入或积塑劣化而产生吹孔。
用适当的工具清理合模线处的残渣或用脱模剂涂布降低残渣的附着机会不失为一个好的方法。
在滚塑模具添加粉料时,尽量让粉料远离合模线,一旦不慎漏洒上粉料要及时清理干净。
通气管阻塞会让空气流无法进入滚塑模具,许多人认识不到这点的严重性。
在滚塑成型第三期及冷却期,模具内的聚合物仍然呈熔融状态,如果空气不能自由出入而保持模具内外的气压平衡,要么形成负压而至产品收缩,要么气体从合模线处不严密的地方穿过而留下吹孔。
正确制定模具的通气管的长度也是必要的,且每个模塑周期都必须检查通气管内的填充物是否还具透气功能。
模具错位或配合不良必然引起合模线处的开口现象,这样的模具所生产的滚塑产品显然会有裂口。
适当地旋紧该处的螺丝或增大夹具压力是常用办法,以达到合模线的准确配合。
如果在加热成型或冷却过程中采用了模具内增压,如果压力过大会造成熔融聚合物的挤出。
你需要对模具内的压力做适当的调整。
合模线处一般比模具其它地方厚重结实,自然,在加热过程中会变成热沉体而降低此处模具的温度,如果采用的材料为成型周期较长才能消除气泡,那么整条合模线处都可能看到气泡。
你可以用预热合模线的方式来消除气泡。
3.
其它地方的吹孔。
有时吹孔不一定会是在合模线处,细心的滚塑工人可能要问,这是什么原因:
3.1铸铝模与生俱来的气孔
3.2钢板模焊接不良也会留下气孔。
3.3模具的材质问题——有不纯物夹杂其中
解决方法:
如果是陷在滚塑模具表面的气孔,滚塑成型时模内的热空气会迅速膨胀而致吹孔的产生。
改变这种现象首先是要提高模具铸造的技术水平。
如果是较少的气孔,且滚塑成型产品的表面痕迹可以为客户所接受,可以采用敲打或抛光冷焊接的方法来解决,当然这是事后弥补之计,无奈之举,治标不能治本,不足取。
不锈钢模具或钢板模在焊接的地方会有气孔产生,要反复加以修补直到无气孔砂眼为止。
确保模具表面的清洁也是一个重要环节。
任何的不纯物在脱落后都会形成成型产品的吹孔。
4.
滚塑产品表面或截面出现气泡,其原因:
4.1滚塑成型过程中加热或循环方式不当
4.2滚塑原料——树脂聚合物的熔融指数太低
4.3脱模剂的使用不当——过多使用致脱模剂塑化
4.4原料粉体内有水分存在或混入其它加热挥发性物质
4.5粉料的颗粒粒径不符要求——过大
4.6滚塑模具内残留水分
所有的滚塑产品在成型初期都会形成泡,不过可以利用持续加热的方式来排除气泡的产生,再有一点就是变更原料的粘度来达到消除气泡的目的。
如果滚塑产品出现大量的气泡,则表示塑化不完全以及加热时间过短,适当地调整加热时间或提高加热温度可以得到改善。
树脂聚合物的熔融指数会影响气泡的生成和消失。
增加树脂原料的熔融指数会让原料颗粒更容易融合在一起。
不适合或劣质的脱模剂会在大部分材料的表面形成细微的针孔;
脱模剂的过量使用也会产生针孔。
采用适当的温和方式擦掉脱模剂会收到好的效果。
树脂原料内的湿气和挥发性物质会导致滚塑产品表面的气泡。
如尼龙和聚碳酸酯材料在使用之前必须做干燥处理。
交联聚乙烯含有大量的触媒残渣,或聚碳酸酯内的残余挥发性溶剂都是气泡产生的推手。
交联类材料如加热太快会导致提前交联而致气泡残留在材料的截面。
尺寸过大的粉料或颗粒会导致产品表面气泡,需检查粉体的流动性和粉料颗粒的粒径及颗粒大小的分配比例。
(详见拙文滚塑工艺对聚