铝热焊接作业流程Word文档下载推荐.doc
《铝热焊接作业流程Word文档下载推荐.doc》由会员分享,可在线阅读,更多相关《铝热焊接作业流程Word文档下载推荐.doc(15页珍藏版)》请在冰豆网上搜索。
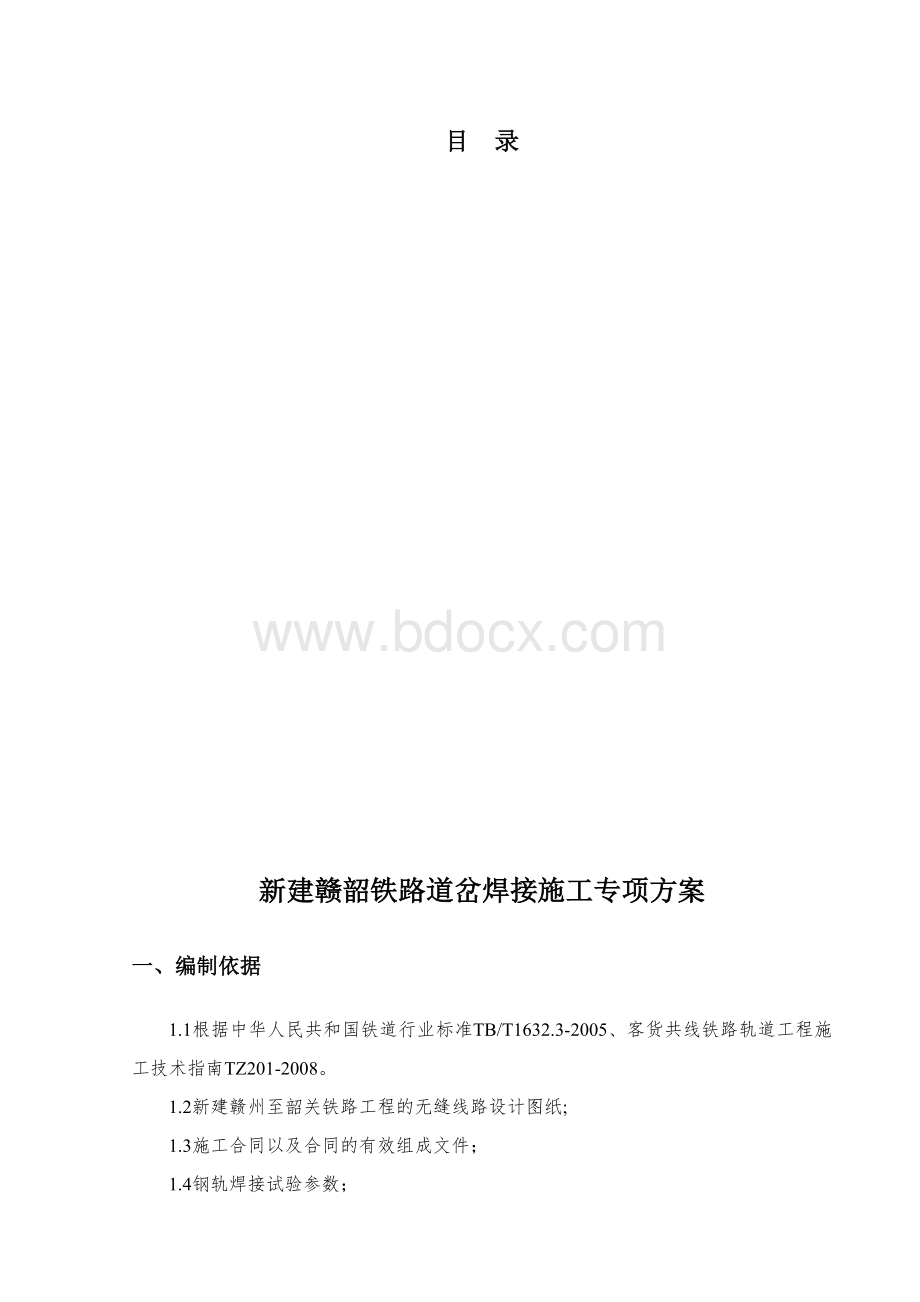
根据腊石坝车站焊接数量及施工进度计划,配制专业机具设备进行钢轨铝热焊施工,主要工具见附表:
五、铝热焊接工艺流程图和焊接顺序图
5.1铝热焊接工艺流程图
根据设计道岔焊接采用“道岔铺设好后进行焊接施工”。
道岔内焊接采取铝热焊接方式,采用法国拉伊台克公司的焊接材料及技术。
铝热焊工艺流程图
钢轨预热
施工准备
轨端干燥
坩埚安装
轨端除锈去污
点火浇铸
调整轨缝、轨端对正
砂模安装
拆模、推瘤
打磨
封箱
探伤、记录
5.2焊接顺序图
道岔焊接顺序图
5
2
4
1
3
6
按上图所示焊接顺序,顺序为1、2、3、4、5、6、详述如下:
①辙叉轨排与导轨连接部,先直股,后曲股;
②导轨与尖轨跟部,先直尖轨,后曲尖轨。
③基本轨焊接,先直股,后曲股;
④道岔前后钢轨焊接顺序:
先岔前,再岔后;
先直股,再曲股。
设计提供的道岔钢轨焊接的锁定轨温是32±
5℃
六、施工作业环境及施工设备和产品使用技术要求
1、寒冷、刮风及下雨天焊接时,必须搭设帐篷,并对焊接区域做好保温措施。
气温低于0℃及大风、大雨天气严禁焊接。
当温差变化大时必须使用拉轨器在保证轨缝大小稳定的情况下进行焊接。
2、铝热焊剂应当密封包装,要有干燥的储藏环境,要有包装标记,便于识别产品类型,生产日期。
3、砂模是预制好的,并与待焊钢轨断面吻合;
包装上有标记,便于识别产品类型,生产日期;
不得受潮、破损、开裂。
4、坩埚使用前不得受潮、破损、开裂。
配备限制钢水飞溅的坩埚盖;
坩埚底部易熔塞用来控制钢水流下的时间,必须保持完好状态。
5、冬季使用氧气、丙烷采取保温措施,以保证气体的压力正常。
七、施工作业步骤
7.1施工准备
7.1.1检查施工现场,焊接前专人根据焊接物品清单进行清点以防漏带,影响施工。
7.1.2检查施工机具且试用,保证焊接前设备的完好率100%。
用肥皂水检测氧气瓶、燃气瓶及其他系统,如有漏气情况不能使用。
7.1.3检查轨道的平直度和表面情况。
检查钢轨端头有无裂缝、倾斜或其它缺陷,当轨端有低接头时必须锯掉低接头。
有大于2mm深的掉角等必须锯除。
7.1.4检查轨缝大小与位置以及接头相错量情况。
焊缝不得落在轨枕上,轨缝位置须距轨枕边100mm以上,保证左右股钢轨拉伸时接头相错量满足小于100mm的要求。
7.1.5测量轨温。
在钢轨背光一侧测量轨温,当轨温低于0℃时不进行焊接。
7.1.6焊接钢轨两侧50m范围内必须严格按规定上紧扣件,确保焊接时轨缝间隙不得发生移动,影响焊接质量甚至发生钢水泄露。
7.2轨端干燥
7.2.1对轨端除锈去污前可用预热枪对钢轨焊缝两侧1米范围内烘烤,充分排除钢轨表面水分及油污。
7.3轨端除锈去污
7.3.1用带有钢丝刷的角磨机对焊接钢轨端部、两侧、轨头和轨底的锈污进行打磨清洁,范围为100-150mm,特别要重视轨底的清洁,轨端不垂直度≤1mm。
7.4对轨
7.4.1轨缝调整:
在轨头和轨底的两侧进行测量,同等条件下,轨缝须满足25±
2mm。
焊接过程中保持间隙不变,从对轨开始禁止在焊缝两端各50m范围内松扣件、起拨线路、拉轨撞轨和通行车辆,直至焊接完毕,轨温降至300℃以下为止或浇注30分钟以后。
7.4.2尖点对正:
将1m直尺的中点与焊缝隙中点重合,用钢楔子或者对轨架进行高度调节,使焊缝两侧0.5m处钢轨轨顶面与直尺的间隙为1.6mm左右。
7.4.3水平对直:
用1m直尺分别紧贴钢轨的轨头、轨腰,并用钢板尺紧贴轨脚,一般情况下必须做到三处均密贴方为水平对正。
必须保证接头的作用面一侧水平对正,钢轨内侧纵向要求平直,以1m直尺同时测量两轨平顺度,错动不大于0.2mm。
7.4.4対轨先调高低,后调水平,最后调整不等倾斜。
7.5砂模安装
7.5.1检查砂模应无受潮、无裂纹、无变形,各组件完整,状态良好。
有裂痕或受潮的砂型不能使用;
7.5.2砂模浇注孔略作休整,防止高温时砂粒脱落;
7.5.3将砂模与钢轨接触面进行摩擦,使砂模与钢轨结合部位密贴;
7.5.4如果砂模与钢轨接触面吻合不好,则会发生漏钢水的严重后果;
7.5.5底模一定要对中,并且与钢轨紧贴。
7.5.6砂模浇注孔要与左右轨角对称,以确保两侧轨底受热均衡;
7.5.7砂型中央与轨缝中央一致,砂型与钢轨垂直,两片砂型要对齐。
7.5.8在扭紧夹具时,应由一人完成,均匀夹紧。
7.5.9要试放分流塞,使分流塞在砂型中高低松紧合适。
7.6封箱
封箱过程是比较关键的步骤之一,在操作的时候应该特别留意,如果封箱不严密,会发生漏钢水的问题,封箱完成后,焊接负责人应该检查封箱是否达到要求,以确保焊接质量。
7.6.1在封箱时要盖上一块干净的纸板,防止砂粒落入砂型中形成夹渣;
7.6.2封箱先从轨底开始,从下往上按顺序进行,分两遍抹成
7.7预热过程的控制
7.7.1工作压力控制
氧气压力为0.49MPa,丙烷压力为0.07MPa。
针对60kg/m的钢轨预热时间为5分钟左右,轨头颜色变为红色。
在调压过程中,将预热枪上的氧气和丙烷开关全部打开,顺时针调节调压表,调节氧气和丙烷的压力。
7.7.2预热火焰的调节
先稍开丙烷阀门,然后点火逐渐交替打开两个阀门,直至丙烷阀门完全打开为止,再通过调节氧气阀门来调节火焰大小,使火焰的长度保持在15-20mm,火焰为中性焰,预热枪头应距轨头50mm;
7.7.3密切关注整个预热过程
在预热过程中,应该密切关注轨头受热颜色变化过程,预热时间为5分钟左右,其颜色为鲜红色;
7.7.4预热枪头须调至轨缝中央,以保证预热效果。
7.7.5预热完后,先关氧气开关,枪头朝上,注意安全。
7.8坩埚的使用
7.8.1使用坩埚前须检查坩埚,受损,受潮的坩埚不能使用。
7.8.2须清除坩埚内的杂物,易熔塞表面须干净。
7.8.3从焊剂包装中取出焊剂,混合均匀后(反复倾倒三次),将焊剂旋转倒入坩埚中,并使其顶部形成锥形,插入高温火柴,盖上坩埚盖,预热完成后,立即放入分流塞并将坩埚安置在砂模侧模板顶部定位槽内。
7.9焊剂高温反应
焊剂反应时间:
8-15秒;
镇静时间:
8-18秒(若大于30s,燃烧不均匀)。
注意:
焊剂反应及浇注过程中,操作者应该距离坩埚3米以上的距离,确保人身安全。
反应完成后,如果钢水不能漏下来,应该让钢水在坩埚中冷却了20分钟后才能移动坩埚。
7.10拆模
浇铸完成后1分钟,移去坩埚,并将其放在安全的地方,然后移去灰渣盘,并将灰渣倒入坩埚中,保持环境干净。
浇铸完成5分钟后,先拆除侧模板和夹紧装置,再拆除底模板。
注意a、在拆摸过程中要小心,不要将砂型一起脱下,造成钢水流出。
b、拆摸后,及时将轨面清理干净,防止推瘤时残渣拉伤轨面。
7.11推瘤
浇铸完成6.5分钟以后开始推瘤。
浇铸棒在推瘤完成20分钟后打掉。
注意a、推瘤过早会因为焊头硬度不够而拉伤轨面。
b、推瘤过迟会给推瘤带来困难。
C、打掉浇铸棒时,要注意敲击方向,不能由内向外敲击。
7.12热打磨
7.12.1推瘤完成后,就可以进行粗打磨。
焊后接头温度降低到300度以下才能放车通行。
7.12.2打磨焊头使其轮廓与两侧钢轨相同。
7.12.3打磨后,焊头处的凸出量不小于0.5mm。
7.13冷却打磨
7.13.1当轨温降至常温时进行冷打磨,打磨位置包括轨顶及内侧工作面、轨底上表面、轨底。
7.13.2使钢轨表面整体平齐。
7.13.3焊缝两侧100mm范围内不得有明显的压痕、碰痕、划伤等缺陷。
7.13.4焊头须打磨至0——+0.3毫米,不能低凹。
时速200公里以上线路打磨要求为0——+0.2毫米。
7.14外观及探伤检查
焊头冷却到50℃以下对钢轨焊头进行探伤。
焊缝探伤分为目测和仪器检测。
焊缝表面的缺陷主要有划伤、碰伤等,可以通过目测判断;
焊缝内部的缺陷主要有气孔、夹杂、未焊透等,可通过仪器进行探伤。
焊接接头的轨头工作面经过外形精整后的表面不平度应满足:
在焊缝中心线两侧各500mm范围内,表面不平整度不大于0.2mm。
轨顶面及轨头侧面工作边母材打磨深度不应超过0.5mm。
7.15经打磨后的焊接接头轨头部位满足
7.15.1不应出现裂纹;
7.15.2可出现1个最大尺寸为1mm的气孔;
7.15.3在轨头下鄂与焊筋边缘交界处半径为2mm的区域内,可出现1个最大尺寸为1mm的气孔、夹渣或夹砂;
7.16焊接接头焊筋表面应满足:
7.16.1最多可出现3个最大尺寸不超过2mm的气孔;
7.16.2焊筋表面夹渣或夹砂等缺陷的尺寸应符合下表的规定,这些缺陷不应侵入钢轨的横断面内;
焊筋表面夹渣或夹砂等缺陷的最大尺寸
缺陷面积mm2
缺陷深度mm
≤10
≤3
≤15
≤2
≤20
≤1
7.17收尾工作
7.17.1检查焊好的接头,做好原始记录并编写焊接序号。
7.17.2清理道床,按标准方枕。
7.17.3加强捣固焊接接头两侧的两根轨枕。
7.17.4将轨道恢复正常,并进一步清理焊接现场。
7.17.5把灰渣、废钢料、砂模等清理干净,装入坩埚中,在离开的时候带到指定的场所处理。
禁止将其乱丢在铁路沿线,造成对铁路沿线的污染。
八、焊接接头直线度和表面质量要求
8.1平直度要求
轨头工作面1m长度平直度允许的最大偏差应符合表1规定。
表1平直度允许的最大偏差
线路设计速度km/h
轨顶面垂直方向最大偏差mm
轨头侧面工作边水平方向最大偏差mm
160
+0.3
注:
①轨头侧面“+”表示凹进,使轨距扩大;
②轨顶面“+”表示高出钢轨母材基准面。
8.2表面质量要求
8.2.1焊接接头的轨头工作面经外形精整后的表面不平度应满足:
在焊缝中心线两侧各100mm范围内,表面不平度不大于0.2m