4万吨硝基苯生产工艺设计Word文档格式.doc
《4万吨硝基苯生产工艺设计Word文档格式.doc》由会员分享,可在线阅读,更多相关《4万吨硝基苯生产工艺设计Word文档格式.doc(20页珍藏版)》请在冰豆网上搜索。
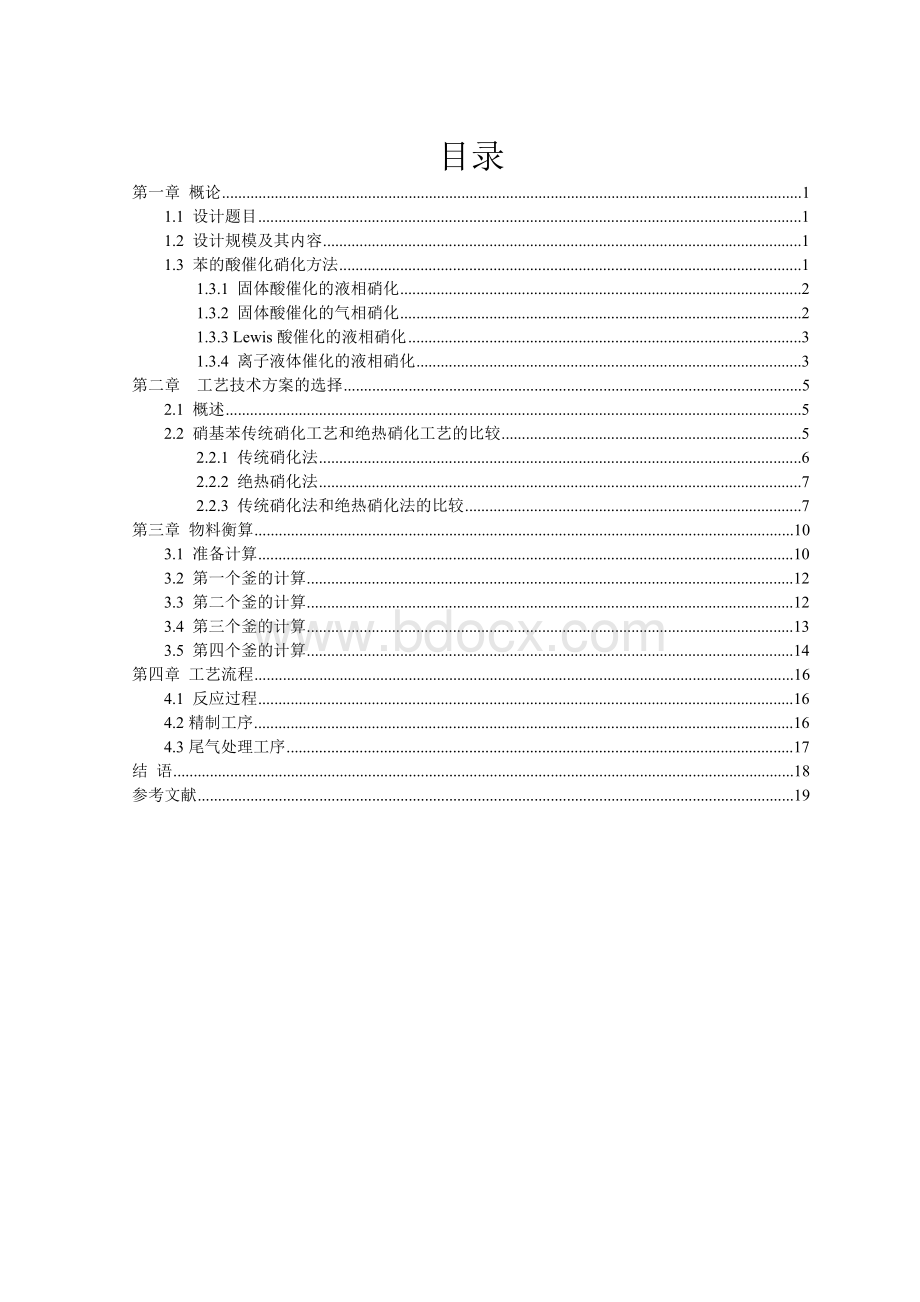
2.2.2绝热硝化法 7
2.2.3传统硝化法和绝热硝化法的比较 7
第三章物料衡算 10
3.1准备计算 10
3.2第一个釜的计算 12
3.3第二个釜的计算 12
3.4第三个釜的计算 13
3.5第四个釜的计算 14
第四章工艺流程 16
4.1反应过程 16
4.2精制工序 16
4.3尾气处理工序 17
结语 18
参考文献 19
第一章概论
1.1设计题目
40kt/a硝基苯生产工艺设计
1.2设计规模及其内容
年产4万吨硝基苯是以苯和硝酸为原料,硫酸为催化剂,在一定反应条件下硝化。
硝基苯的物理性质是,分子式是C6H5NO3,熔点为5.7,沸点为210.8℃,相对密度为1.2037,闪点为90℃,自燃点为495℃。
硝基苯微溶于水,易溶于溶于乙醇、乙醚、苯等有机溶剂。
纯净的硝基苯是无色油状液体,工业品常因含杂质而显黄色,有像杏仁油的特殊气味。
其水溶液有甜味,能随水蒸气蒸发。
易燃易爆。
硝基苯是一种重要的基本有机化工原料,主要用途是制取苯胺,由苯胺进而生产各种有机中间体,也用于生产间硝基苯磺酸钠和偶氮苯等多种医药和染料中间体。
目前工业上制取硝基苯是以苯和硝酸为原料,硫酸为催化剂,在一定反应条件下硝化。
早期采用的是混酸间歇硝化法,逐渐发展了釜式串联、管式、环式或泵式循环等连续硝化工艺,而后又发展了绝热硝化法,这些工艺都是非均相混酸硝化工艺。
硝基苯生产方法按硝化种类可分为硝酸硝化法、混酸硝化法、氮的氧化物硝化法及绝热硝化法;
按反应物料的物理状态来分则有液相硝化、气-液相硝化和气相硝化。
由于硝基苯的非均相混酸硝化工艺中产生废酸、废水需要进行处理,生产过程中对设备的腐蚀较严重。
为此,取代混酸硝化技术的研究受到广泛关注,尤其是催化剂的研究。
新型催化剂及催化工艺可减少污染物的排放,提高资源利用率,降低能源消耗,对深入研究绿色硝化及推动工业化进程具有重要意义。
1.3苯的酸催化硝化方法
目前有四类苯的酸催化硝化方法,主要有固体酸催化的液相硝化、固体酸催化的气相硝化、Lewis酸催化的液相硝化、离子液体催化的液相硝化。
1.3.1固体酸催化的液相硝化
(1)粘土类催化剂催化硝化
这种方法是将硝酸铜负载于蒙脱土形成Claycop,它使用催化剂是乙酸酐、蒙脱土,以少量的发烟硝酸为引发剂,在室温下产率达到92%,不含氧化副产物。
无论是产率还是选择性都优于常规方法,且后处理操作简便,仅过滤除去粘土催化剂即可得到产物。
但是这种方法的缺点是对设备的要求较高,生产的成本也较高。
虽然操做的方法简单,但是设备的维护也是相当的不容易。
(2)分子筛催化剂催化硝化
这种方法是用沸石作催化剂,以等摩尔的硝酸、乙酸酐作为硝化剂,对苯、烷基苯及卤苯在温和条件下进行硝化,异构体的产率可以达到70%~99%。
反应过程中唯一的副产物乙酸可以通过蒸馏来与硝化产物进行分离,催化剂也能够很好的回收。
这种方法以改进型MFI拓扑结构的沸石分子筛、氢型p沸石等为催化剂,选择质量分数为65%的硝酸为硝化剂,进行了苯硝化反应的研究。
硝酸和苯的体积比为1.5~3.5、在常压下,温度为8O~100℃、反应时间3h的条件下,合成硝基苯的收率大于95%。
这种方法的优点很多,但是对于催化剂的回收利用用很高的要求,而且催化剂的制取和购买成本都很高。
1.3.2固体酸催化的气相硝化
(1)分子筛催化剂催化硝化
文献报道,用于苯气相硝化合成硝基苯的沸石分子筛有:
丝光沸石、改性丝光沸石、Y沸石、改性Y沸石、13沸石、ZSM一5等。
ZSM一5、丝光沸石、Y沸石和改性的Y沸石作催化剂,可有效催化硝酸与苯气相硝化反应。
用H2s0、MCM--41为催化剂,以60%~70%的稀硝酸为硝化剂进行苯的气相硝化反应。
实验发现,在苯与硝酸摩尔比为2.5,MCM-41上硫酸负载量为2O%,反应温度150~160℃,空速3279/h条件下,硝化产率大于99%。
采用改性HZSM一5分子筛为催化剂,研究了反应温度、原料配比、空速、水蒸汽含量、沸石硅铝比对苯与NO2进行气相硝化合成硝基苯的影响,硝基苯的收率大于50%。
此类方法优点多多,但是生产操作实现程度有待于考证。
理论的基础有,但是实践的操作还是不够太成熟的。
(2)杂多酸催化剂催化硝化
这种方法是将H2PW12040负载在SiO2、木质活性炭及r—AI2O3,作催化剂对苯气相硝化,考察其对苯与硝酸气相硝化反应的催化活性及影响因素。
通过查文献结果可知,SiO2负载杂多酸对苯气相硝化具有很好的催化活性,而对于20%H2PW12040/SiO2催化剂,苯/硝酸量比为2,反应温度为155~160℃,空速(SV)为682mL/(g·
h),硝基苯产率可达90.6%,且选择性很高,优点也很多。
(3)金属氧化物催化剂催化硝化
这种方法是将含TiO2或ZrO2的混合金属氧化物催化苯与稀硝酸气相硝化反应,大概产率可以达到80%~90%。
并且用聚乙烯醇为模板制备比表面积为200—300m2/g的中孔材料WO3/ZrO2超强酸,使用70%的硝酸作硝化剂,在温度为170℃、常压的反应条件下,产率能达到65%~80%,选择性可以达到99%。
这种方法采用的是金属氧化物作为催化剂,生产成本高,催化剂的含量和不好控制,虽然条件合适的情况下达到的效果很好,但是工业生产设计中条件不好控制。
1.3.3Lewis酸催化的液相硝化
(1)粘土负载类催化剂催化硝化
因为质子酸蒙脱土的催化活性不高,但与高价金属离子进行离子交换后催化活性可以得到很好的改善。
用AL3+、Zr4+、Fe3+、Cr3+、Cu2+、La3+、Mn2+等高价金属离子与蒙脱土进行离子交换得到负载型催化剂,对苯与硝酸硝化反应,产率40%~93%,选择性大于96%。
这种方法明显的不如固体酸气化酸化。
所以也效果不是很好。
(2)分子筛负载类催化剂催化绿色硝化
这种方法以三氟甲基磺酸镧系盐作为强Lewis酸催化69%的硝酸硝化苯,得到75%~95%的产率。
这种生产方法硝化产生的废弃物少,但是适用于小规模的生产。
大规模的生产并不适宜。
1.3.4离子液体催化的液相硝化
用改性硅胶作载体,将酸性离子液体固载化后作催化剂进行硝化研究。
结果表明,此类固载化的催化剂表现出比单纯离子液体更高的活性,苯的转化率为49.3%。
此外,此方法在产物分离、催化剂回收利用方面具有明显优势,尤其提供了在工业上进行连续生产的能力。
第二章工艺技术方案的选择
2.1概述
硝化系指有机化合物分子中的氢原子或基团为硝基所取代的反应。
硝化是极为重要的单元反应之一,作为硝化反应的产物,硝基化合物在燃料、溶剂、炸药、燃料、香料、医药、农药和表面活性剂等很多化工领域都有大量的应用实例。
硝基苯是重要的染料、医药中间体,主要用于生产苯胺。
在工业上硝基苯是采用一定浓度的硫酸和硝酸配制的混酸硝化苯来生产的,反应式如下:
硝酸是在硫酸或其它强酸的存在下,形成离子状,和苯发生硝化反应。
硝化反应是强放热反应,它的反应热为14210/mol,在反应的同时,混酸中的硫酸被反应生成的水释稀,还将产生释稀热(约为反应热的7%~10%)。
若反应温度持续升高,会引起副反应,硝酸大量分解,硝基酚类副产物增加,这些酚类副产物是造成硝基苯生产发生爆炸事故的主要原因,同时,硝化反应是非均相反应,反应是在酸层及酸层和有机层的交界面处发生,硝化速度由相间传质和化学动力学所控制,借助强力搅拌,非均相间保持最大界面,强化传质,才能保持反应平稳进行。
所以,必须要控制反应温度适度、搅拌效果良好,才能保证硝基苯生产的安全操作。
硝化反应是强放热反应同时混酸中的硫酸被反应生成的水所稀释时还将产生稀释热。
这样大的热量若不及时移除,势必会使反应温度上升,引起多硝化及氧化等副反应,同时还将造成硝酸大量分解,产生大量红棕色的二氧化氮气体,甚至发生严重事故。
2.2硝基苯传统硝化工艺和绝热硝化工艺的比较
目前国内比较常见的的硝基苯混酸硝化生产方法有传统硝化工艺和绝热法硝化工艺。
它们二者都是采用的是连续式复式反应器进行生产。
而混酸硝化法的优点也很多:
(1)混酸比硝酸会产生更多的硝基正离子,所以混酸的硝化能力强,反应速度快产率高。
硝酸被硫酸稀释后,氧化能力降低,不易产生氧化的副反应。
(2)混酸中的硝酸用量接近理论量,硝酸几乎可全部得到利用。
(3)硫酸比热大,能吸收硝化反应中放出的热量,可以避免硝化的局部过热现象使反应温度容易控制。
(4)浓硫酸能溶解多数有机物(尤其是芳香族化合物),因而增加了有机物与硝酸的混合程度,使硝化易于进行。
(5)混酸对铸铁的腐蚀性小,因而可使用铸铁设备作反应器。
浓硝酸硝化法的缺点:
(1)反应中生成的水使硝酸浓度降低,以致硝化反应速度不断下降或终止。
(2)硝酸浓度降低,不仅减缓硝化反应速度,而且使氧化反应显著增加,有时会发生侧链氧化反应
(3)硝酸浓度降低到一定浓度时,则无硝化能力。
2.2.1传统硝化法
传统硝化法主要分三部分:
反应部分、洗涤提纯部分、废酸提浓部分。
反应部分:
将苯和混酸(混酸的质量组成为硫酸56%、硝酸25%、水19%)同时进入到釜式硝化反应器中进行硝化反应。
硝化反应器一般为带有强力搅拌的反应釜,内部装有冷却蛇管,以导出反应热,硝化温度控制在50℃~100℃。
硝化反应器一般为串联操作,物料在反应器中的停留时间约为15min,产率为96%一98.5%(一般都能达到98%~98.5%)。
反应完成后,反应产物连续由硝化反应器进入分离器,分为有机相和酸相,有机相即为粗硝基苯,去洗涤提纯部分,而酸相即为释稀后的硫酸(组成大约为硫酸67.9%、水31.8%、有机物0.3%),去废酸提浓部分。
洗涤提纯部分:
从分离器来的粗硝基苯先用碱水洗涤,任何带入的硝酸、硫酸、一小部分硝基酚、二硝基酚等杂质都被中和并溶解在碱水中,之后混和物进入分离器分为有机相和水相,有机相是已分离了酸性介质但含有小部分苯的硝基苯,水相进入废水罐中,分离后的有机相再进行水洗,洗涤水来自于脱水塔顶的硝基苯和水的共沸物。
水洗后的硝基苯再去苯回收塔去分离回收苯,苯和水从苯回收塔项馏出进入回流罐,回流罐又分离出有机相苯和水相,分离出的苯循环回硝化过程,水相进入废水罐。
从苯回收塔底出来的即为干燥脱水的产品硝基苯。
废酸提浓部分:
废酸提浓目前一般采用真空浓缩法,利用蒸汽加热浓缩器中的废酸至高温,再真空闪蒸出大量的水分,经过提浓后,68%左右浓度的废酸一般可提浓到88%~93%。
2.2.2绝热硝化法
绝热硝化是国外70年代开发成功的硝化新技术,目前已建成年产22万t硝基苯的生产装置。
绝热硝化也分三部分:
反应部分、洗涤提纯部分及废酸提浓部分,其中的反应部分及废酸提浓部分是作为一个整体来布置的。
同传统硝化方法相比绝热硝化的洗涤提纯部分和传统硝化法基本上是相同的,主要差异在反应部分及废酸提浓部分。
苯是在大量混酸的存在下进入硝化反应釜中硝化的,在传统硝化反应中,混酸:
苯的重量比约为3.2:
1,而在绝热硝化反应中,混酸:
苯的