完整版机械制造专业毕业设计.docx
《完整版机械制造专业毕业设计.docx》由会员分享,可在线阅读,更多相关《完整版机械制造专业毕业设计.docx(51页珍藏版)》请在冰豆网上搜索。
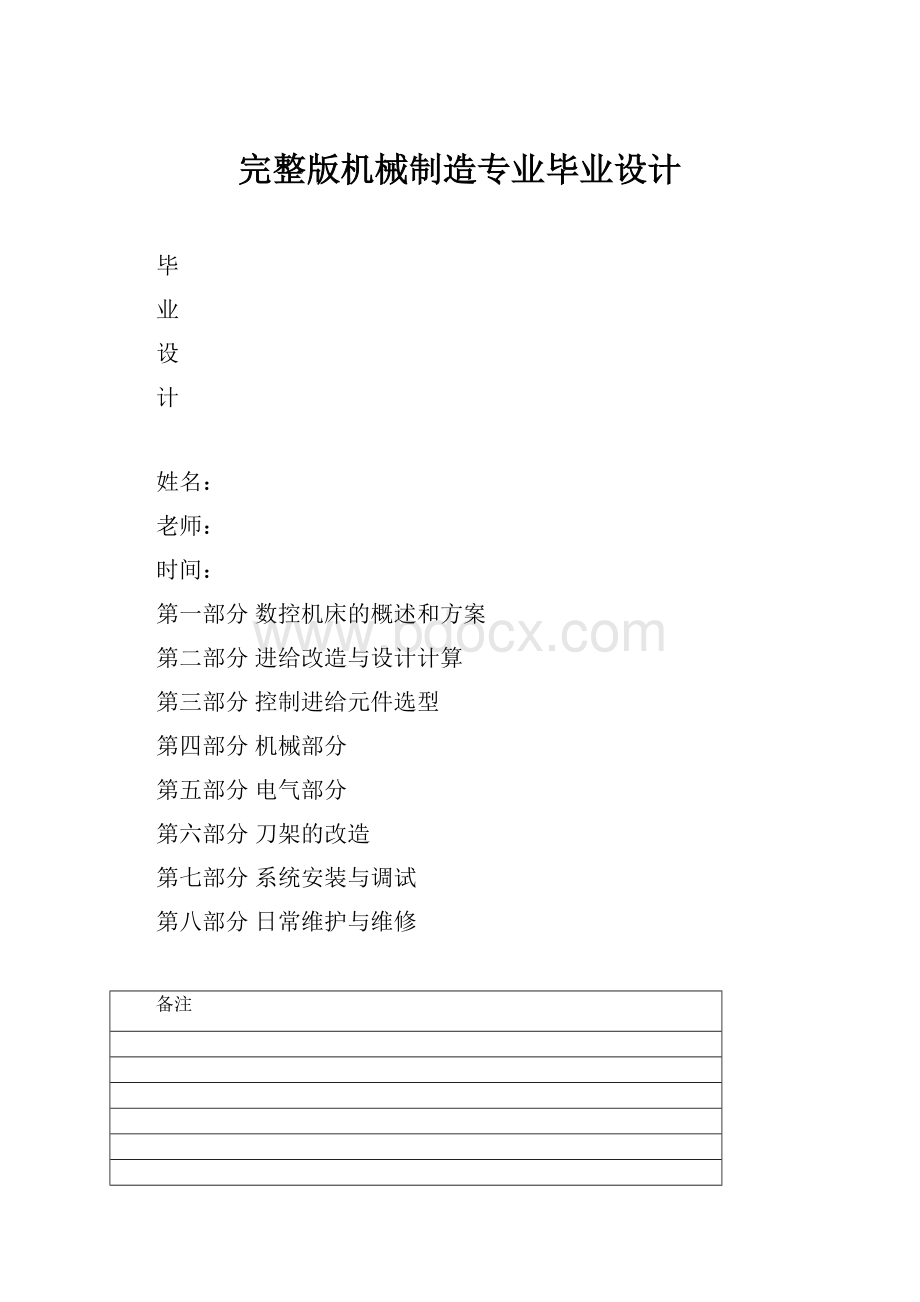
完整版机械制造专业毕业设计
毕
业
设
计
姓名:
老师:
时间:
第一部分数控机床的概述和方案
第二部分进给改造与设计计算
第三部分控制进给元件选型
第四部分机械部分
第五部分电气部分
第六部分刀架的改造
第七部分系统安装与调试
第八部分日常维护与维修
备注
第一部分数控机床的概述和方案
一、机床数控改造的意义
众所周知,制造业是国民经济的基础产业和支柱产业则推动国家技术进步的主要力量.我国制造业正面临极大的考验和国制造业正面临椽支柱产业则推动国家技术进步的主要力早.....
1)节省资金。
机床的数控改造同购置新机床相比一般可节省60%左右的费用,大型及特殊设备尤为明显。
一般大型机床改造只需花新机床购置费的13。
即使将原机床的结构进行彻底改造升级也只需花费购买新机床60%的费用,并可以利用现有地基。
2)性能稳定可靠。
因原机床各基础件经过长期时效,几乎不产生应力变形影响精度。
3)提高生产效率。
机床经数控改造后即可实现加工的自动化效率可比传统机床提高3至5倍。
对复杂零件而言难度越高功效提高得越多。
且可以不用或少用工装,不仅节约了费用而且可以缩短生产准备周期
二.改造前的C616普通型车床各参数。
1).C616型普通车床电气控制电路简述
C616型普通车床电路原理图如图4-4所示。
从图4-4中可以看到,C616型普通车床有三台电动机拖动。
其中主轴电动机M1要求能正、反向旋转;润滑电动机M2、冷却泵电动机M3只要求单向运转。
手动操作转换开关SA1用来控制主轴电动机M1的正、反向运转及停止,它有三对触点SA1-1、SA1-2、SA1-3。
在正常情况下,即SA1处于“零”位置时,SA1-1闭合,SA1-2、SA1-3断开;当将SA1的操作手柄扳到“正转”位置时,SA1-2接通,SA1-1、SA1-3断开:
将SA1的操作手柄板到“反转”位置时,SA1-3接通,SA1-1、SA1-2断开。
合上电源开关QS1,中间继电器K通电闭合,继而接触器KM3通电闭合,润滑泵电动机M2启动运转。
将手动操作转换开关SA1板至“正转”位置,接触器KM1通电闭合,主轴电动机M1正向启动运转:
将手动操作转换开关SA1板至“反转”位置,接触器KM2通电闭合,主轴电动机M1反向启动运转。
如图4-1.
(2)改造前主轴传动图。
如图4-2.
(3).C616普通机床参数。
1.最大工件直径*最大工件长度:
320*750
2.床身上:
3203.刀架上:
175
4.主轴孔直径:
345.加工最大长度:
7500
6.刀架行程:
小刀架:
20*207.工作精度:
圆度:
0.005
纵向:
0.06~3.34圆柱度:
0.02300
横向:
0.04~2.45平面度:
0.015300
粗糙度:
3.2
8.主轴转速:
43~2000级数:
129.电机功率:
电机:
2个总容量:
4.125
10.重量:
(毛重:
1.5吨净重:
1.4吨)
11.外形尺寸长×宽×高:
2340×900×1190
12.机床包装尺寸:
2170×900×1185
13.电动机功率:
7.5kw1450rpm
14主轴驱动电机型号:
JOED41-4
15主轴驱动电机功率:
7.5KW;1450rpm
16冷却泵电动机型号:
JCB-22
17冷却泵电动机功率:
0.125KW;3000rpm
三.改进后的C616数控化车床。
简易数控车床即开环式控制将C616车床的纵向进给系统常采用伺服电动机驱动滚轴丝杆,带动装有刀架的拖板作往复直线运动。
其工作原理如图
改进后的C616车床传动系统
1.电动刀架2.横向步进电动机3.横向滚珠丝杆4.大拖板
5.纵向滚珠丝杆6.纵向步进电动机
C616车床的各参数如下:
1.大拖板重量w=1300N
2.小拖板重量w=600N
3.拖板与导轨贴塑板间摩擦系数U=0.04
4.最大走刀抗力FZ(与运动方向相反)=1600N
5.最大主切削力FY(与导轨垂直)=2600N(最大走刀抗力和主切削力可根据普通C616车床的电动机功率和车削时车刀的主偏角为900时计算而得出)
6.横向脉冲当量为V1=0.005毫米脉冲
7.纵向脉冲当量为V=0.01毫米脉冲
8.横向滚珠丝杆导程L=6毫米
9.纵向滚珠丝杆导程L=4毫米
10.滚珠丝杆节圆直径d0=30毫米
11.丝杆总长L=1000毫米
12.定位精度0.01毫米
四、C616普通车床数控改造方案
本次改造的普通车床型号为C616,长度2340毫米。
数控改造主要包括传动系统的机械改造和数控装置的设计。
由于对经济型数控机床的加工精度要求不高,为简化结构、降低成本,拟采用伺服电机控制系统。
通过控制纵、横进给系统,保证改造后的车床具有定位、直线插补、圆弧插补、暂停等功能。
为实现机床所要求的分辨率,采用伺服电机经齿轮减速再传动丝杠;为保证一定的传动精度和平稳性,尽量减小摩擦力,选用滚珠丝杠螺母副。
1. 机械部分的改造:
(1)主传动系统保留原有的主传动系统和变速机构,这样既保留了机床原有的功能,又降低了改造工作量,如果要自动改变切削速度,可采用交流变频调速,这样改造成本较高,本次改造主传动系统主轴电机不动用以前的,传动机构稍做改进。
以提高效率为主。
(2)进给传动系统改造纵、横向传动全部用滚珠丝杠(传动效率高,达到90%)。
(拆除原有的挂轮系统、进给箱、溜板箱、光杆),在溜板下加装滚珠丝杠螺母托架,在滚珠丝杠的头、尾部加装接套、接杆及支承。
(3)刀架部分进行改造装一个伺服电动机,做一个自动换刀机构,使得加工换刀方便。
节约换刀的时间,来提高工作的效率。
2. 数控部分的改造:
为降低改造成本,决定采用开环控制方式对X轴和Z轴进给系统进行改造。
经济型数控结构简单、价格低,调试、维护方便,一般用于精度不高的经济型机床。
本次改造的机床主要用于粗加工。
对卧式车床进行数控化改造,主要是将纵向和横向进给系统改造为用数控装置控制的、能独立运动的进伺服系统;刀架改造成为能自动换刀的回转刀架。
由于加工过程中的切削参数、切削次序和刀具都会按程序自动进行调节和更换,再加上纵向和横向进给联动的功能,数控改装后的车床就可以加工出各种形状复杂的回转零件,并能实现多工序自动车削。
总体方案设计应考虑数控系统的运动方式、伺服系统的类型、数控系统的选择,以及传动方式和执行机构的选择等。
在制定总体方案时,要满足下列要求:
1)卧式车床数控化改造后应具有定位、纵向和横向的直线插补、圆弧插补功能,还要求能暂停,进行循环加工和螺纹加工等,因此,数控系统选择连续控制系统。
2)车床数控化改装后属于经济型数控机床,在保证一定加工精度的前提下,应简化结构,降低成本。
因此,进给系统采用伺服电动机开环控制系统。
3)在卧室车床最大加工尺寸、加工精度、控制速度,以及经济性等条件下,经济型数控车床一般采用经济型数控系统。
4)重新设计自动回转刀架及其控制电路。
5)纵向和横向进给是两套独立的传动链,它们由伺服电动机、齿轮副、丝杠螺母副组成,其传动比应满足机床所要求的分辨率。
6)为了使进给伺服系统的传动精度和平稳性要求,选用摩擦小、传动效率高的滚珠丝杠螺母副,并应有预紧机构,以提高传动刚度,消除间隙。
齿轮副也应消除齿侧间隙的机构。
数控机床进给驱动装置的基本要求
数控系统主要根据输入程序完成对工作台的位置、主轴启停、换向、变速、刀具的选择、更换、液压系统、冷却系统、润滑系统等的控制工作。
而机床为了完成零件的加工须进行两大运动:
主运动和进给运动。
数控机床的主运动和进给运动在动作上除了接受CNC的控制外,在机械结构上应具有响应快、高精度、高稳定性的特点。
第二部分进给改造与设计计算
C616车床改造经济型采用开环进给系统,由于开环系统中没有反馈检测装置,其前向通道中的各种误差就无法通过反馈信息来时加以补偿,从而直接导致了输出位置误差。
因此,需对开进给系统的精度进行分析,然后采用一些必要的措施来加以改善,以提高系统性能。
1.精度分析开环进给系统中影响工作台位移精度的主要因素包括如下几个方面。
.
1).齿隙误差。
例如减速齿轮传动间隙滚珠丝杠和螺母副之间的传动间隙等。
2).滚珠丝杠的螺距累积误差。
3).滚珠丝杠、螺母支架、轴承等机械部件的受力变形和热变形引起的误差。
4).工作台导轨的误差。
由以上各项误差构成了开环进给系统的综合误差。
2.提高精度的措施针对上述误差的确来源,可采取一些措施进行改善。
首先从系统构成各个环节入手,在可能的情况下,尽量选择性能较好,精度较高的部件实现进给驱动。
1)驱动入手,尽量选择更理想的驱动电路来实现电动机的控制。
。
2)从软件入手,根据齿隙误差的特点,当工作台运动方向改变时可利用软件进行校正。
3)从控制原理方面入手,对于精度要求较高的大型数车床,针对开环系统的不足,可在其基础之上增设一套工作台位移检测装置,如直光栅或感应同步器等,用监视并补偿前向通道的误差,当系统中没有传动误差时,由反馈电路发出一定数目的附加脉冲,用以补偿伺服电动机多走或少走的步数。
可见该系统中机床本身并不含在定位伺服系统中,而是处于补偿回路中,使系统易于调试,类似于开环,但系统精度又接近于开环。
工作步骤方框图如下图
工作步骤方框图
不统庐偿步进电动机多走或主加税一求较高的大型数车床,针对开环系统的不足,可在其基础之上增设一
一.纵向进给的设计与计算
纵向滚珠丝杠纵向滚珠丝杠必须采用三点式支承形式。
伺服电动机有布置,可以放在丝杠有任一端。
在左端设计一个专用轴承支承座,而在丝杠托架处布置步进电动机和减速齿轮。
如下图。
纵向进给系统的设计计算已知条件:
工作台重量:
W=80kgf=80N(根据图纸粗略计算)
时间常数:
T=25ms
滚珠丝杠基本导程:
L0=6mm
行程:
S=640mm
脉冲当量:
δp=0.01mmstep
快速进给速度:
Vmax=2mmin
(1)切削计算由〈〈机床设计手册〉〉可知,切削功率
Pc=NηK
式中N——电机功率,查机床说明书,N=7.5KW;
η——主传动系统总效率,一般为0.6~0.7取η=0.65;
K——进给系统功率系数,取为K=0.96。
则:
=7.50.650.96kw=4.68kw
切削功率应按在各种加工情况下经常遇到的最大切削力(或转矩)和最大切削转速(或转速)来计算,即
=或=
式中——主切削力(N)——切削速度()
T——切削转矩(N·m)n——主轴转速()
设按最大切削速度来计算,取V=,则主切削力
==2808N
由《机械设计手册》可知,在外圆车削时
=(0.1~0.55),=(0.15~0.65)
取=0.5=0.52808N=1404N=0.6=0.62808N=1684.8N
2).纵向滚珠丝设计计算
滚珠丝杠副已经标准化,因此,滚珠丝杠副有设计归结为滚珠丝杠副型号的选择。
1).计算作用在丝杠上的最大动负荷:
首先根据切削力和运动部件的重量引起的进给抗力,计算出丝杠的轴向载荷,再根据要求的寿命值计算出丝杠副应能承受的最大动载荷.
F=ffF
式中——工作负载(N),指数控机床工作时实际作用在滚珠丝杠上的轴向力;
u——运转系数,一般运转系数f取1.2~1.5,有冲击的运转f取1.5~2.5;
T——硬度系数,为60HRC时,为1;f为<60HRC时,f>1;
n——寿命(以 转为单位1,如1.5则为150万转)。
寿命G可按下式计算:
G=
式中n——滚珠丝的转速(rmin)T——使用寿命时间(,进给量f=6mmr,车削直径D=80mm的外圆时,丝杠的转速
N==rmin=400rmin
则G==万转=36万转
根据工作负载、寿命G,取=1.2,=1,计算出滚珠丝杠副承受的最大动负荷
==N=4437.55N
由查滚珠丝杠地产品或《机床设计手册》,选择丝杠的型号。
例如参照某厂滚珠丝杠的样本,选择滚珠丝杠的直径为32mm,型号为JWB005其额定动载荷是20500N,强度足够用。
2).效率计算:
根据机械原理,丝杠螺母副的传动效率为
=
式中——螺纹的螺旋升角,该丝杠为25′;Φ——摩擦角,Φ约等于10′。
则==0.953
3).刚度验算:
滚珠丝杠工作时受轴向力和扭转的作用,将引起基本导程的变化,因滚珠丝杠受扭时引起的导程变化量很小,可忽略不计,故工作负载引起的导程变化量为
=
式中E——弹性模量,对于钢,E=20.6N;
S——滚珠丝杠截面积(按丝杠螺纹底径确定d,若d=2.77cm),
则△=cm=7.712cm
丝杠1m长度上导程变形误差△为
△=△=7.712=12.85
因3级精度丝杠允许的螺距误差为15,故此丝杠的精度足够。
二、横向进给系统有设计计算
已知条件:
工作台重量W=1300N,时间常数t=25ms,滚珠丝杠基本导程=6mm(左旋),行程S=1100mm,脉冲当量δp=0.05mmstep快速进给速度=2mmin。
《机床设计手册》可知,切削功率。
(1)切削计算由〈〈机床设计手册〉〉可知,切削功率脉冲当量
Pc=NηK
式中N——电机功率,查机床说明书,N=7.5KW;
η——主传动系统总效率,一般为0.6~0.7取η=0.65;
K——进给系统功率系数,取为K=0.96。
则:
=7.50.650.96kw=4.68kw
2).横向滚珠丝设计计算
滚珠丝杠副已经标准化,因此,滚珠丝杠副有设计归结为滚珠丝杠副型号的选择。
1).计算作用在丝杠上的最大动负荷:
首先根据切削力和运动部件的重量引起的进给抗力,计算出丝杠的轴向载荷,再根据要求的寿命值计算出丝杠副应能承受的最大动载荷.
F=ffF
式中各符号代表的意思在计算纵向是时候已经说明(请参考纵向丝杠计算一下同理)。
寿命G可按下式计算:
G=
工作负载的数值可用《机床设计手册》中进给牵引力的实验公式计算,对于三角或综合导轨
=k+()
则 =[1.15921.6+0.16(2808+1300)]N=1717.12N
当机床以线速度V=100mmin,进给量f=6mmr,车削直径D=80mm的外圆时,丝杠的转速
N==rmin=400rmin
则G==万转=36万转
根据工作负载、寿命G,取=12,=1,计算出滚珠丝杠副承受的最大动负荷
==1.211717.12N=5426.842N
由查滚珠丝杠地产品或《机床设计手册》,选择丝杠的型号。
例如参照某厂滚珠丝杠的样本,选择滚珠丝杠的直径为32mm,型号为JWB005,其额定动载荷是24500N,强度足够用。
其刚度和效率跟纵向的一样的。
所以我所选的滚珠丝杠是纵、横两项通用的只是长度不同。
三、伺服电动机的选型
1).脉冲当量的选择
脉冲当量:
一个指令脉冲使伺服电动机驱动拖动的移动距离=0.01mmp(纵向输入一个指令脉冲工作台移动0.01毫米,横向入一个指令脉冲工作台移动0.05毫米)
伺服电动机与滚珠丝杆间的传动比i===1
齿轮的模数根据C616车床,挂轮齿类比确定。
2).等效负载转矩的计算
空载时的摩擦转矩TLF
TLF===0.075N.M
车削加工时的负载转矩TL
TL==
=1.65N.M
u----摩擦系数w----拖板重量L----导程i----传动比FZ---最走刀抗力Fy------最大切削力(N)----滚动丝杆传动效率
C.伺服电机的主参数计算:
(1)最大切削力负载转矩
T=i
式中——丝杠上的最大轴向负载N——丝杠导程m。
——滚珠丝杠的机械效率。
预加i——传动比
——因滚珠丝杠螺母预加再载荷引起的附加摩擦转矩N.m
——滚珠丝杠轴承的摩擦转矩N.m
计算得T=9.154N.m
(2)惯量匹配
电动机轴惯量J=m=0.00073kg.m
滚珠丝杠的惯量J==0.00057kg.m
联轴节的惯量(查表得)J=0.0003kg.m
负载惯量J=J+J+J=0.0016kg.m
所以电动机的惯量J应J16根据以上计算数据正确的选择材料,要做到及经济型又使用型,这两个加起来才是我们的真正目的。
第三部分控制进给元件选型
一.主轴电动机的选择:
因考虑到经济的原因和使用的原因,主轴电动机不加更换,其原因又一下几点:
1)考虑到安装和位置的方面该电动机刚好合适也方便我们改进。
2)经过测试该电动机的性能符合我们的改进要求。
3)该电动机以满足了我们所选变频器的要求。
二.变频器的选择:
根据主轴电动机的参数要求我们选择型号为FR-A540-11K-CH的变频器。
变频器的参数。
(1)型号:
FR-A540-11K-CH
(2)功率:
11KW(3)电流:
17A
(4)适用电动机容量:
11KW(5)额定容量:
17.5KVA
(6)额定电流:
23A(7)过载能力:
150%60s200%0.5s
(7)电压:
三相380V(8)再生制动转矩最大值:
100%5s
(9)再生制动转矩允许使用率:
连续(10)额定交流电压频率:
380V50HZ
(11)交流电压允许波动范围:
323~528V50HZ
(12)频率允许波动范围:
正负5%(13)电源容量:
20KVA
(14)保护结构:
封闭型(ZP20)(15)冷却方式:
强制冷却
(16)大约重量:
13KG(17)调速范围:
4~~120HZ
图片:
三菱变频器
FR-A540变频器
选择变频器的要求:
(1)所选变频器的功率大于主轴电动功率的(1.5~~2.0)倍.
(2)所选变频器要又足够的调速范围。
(3)所选变频器要具有过载保护,过流保护型。
选择FR-A540变频器的好趣:
1)它满足以前主轴电动机的转速的要求,可就利用以前的主轴电动机。
2)它和所选系统搭配较好,提高了加工的精度。
3)它结构简单,控制方便不需要人工调速。
提高了加工效率。
4)选变频器控制后,就可以去掉以前的所有变速齿轮,更方便维修。
通过第二部分的计算和根据机床的要求我所选变频器正好满足以上条件,也满足啦机床加工精度的要求。
三.滚珠丝杠螺母副选择:
所选滚珠丝杠的型号参数
(1)型号:
JWB005
(2)额定动载荷:
20500N
(3)滚珠丝杠的直径:
32mm(4)导程:
6mm
(5)行程:
1100mm(6)最大载荷:
5426.84
(7)减速比:
H速度5L速度20(8)综合效率%:
H速度63L速度37
(9)容许输入最大功率:
H速度0.25L速度0.12
(10)保持扭矩(N·m):
H速度0.69L速度0.14
(11)容许输入轴扭矩(N·m):
9.8
(10)空载扭矩(N·m):
0.0745
(13)最大载荷时丝杆回转扭矩(N·m):
4.3
选择滚珠丝杠的要求:
1)所选丝杠的载荷力要大于切削的最大载荷力。
2)所选丝杠要适合机床的长度要求和精度要求。
3)所选丝杠要满足伺服电机的要求。
因为以前的丝杠的精度没达到机床的要求,所用的导程不同和伺服电机不能很好的搭配,影响了加工精度的要求。
为了提高机床的精度和根据计算决定更换纵、横方向的丝杠螺母。
又因为机床的时间用的长了,轨道就有磨损根据机床的要求,要给车床轨道打磨提高机床的精度。
以上滚珠丝杠参数是由第二部分计算得的到,在加上查找该型号的计算参数通过比较以上数值满足我们所改造机床的要求
四.伺服电动机选择:
所选伺服电动机的型号及参数
额定输出功率1.2Kw额定转矩1.27N.m
瞬间最大转矩3.82N.m额定转矩3000rpm
最高转矩3600rpm电机转矩惯量0.3Kg.cm
转矩系数0.712N.mA额定相电流2.5A
瞬间最大相电流7.33A电枢绕组相电阻5.58
电枢绕组相电感17.33mH机械时间常数1.08ms
电器时间常数3.11ms重量1.4Kg
编码器2500PR负载惯量负载惯量电动机转子惯量10(倍)
其伺服电动机的有点是:
体积小、精度高、转速高。
它适应工作的环境是:
绝缘电阻——500VDC100MMin绝缘强度——1500VAC1Min环境温度——-20~+50摄氏度绝缘等级——B级
伺服电动机选择的要求
(1)最大切削负载转矩不得超过电动机的额定转矩。
(2)电动机的转子惯量应与负载惯量匹配。
(3)快速时的加速性能。
(4)要满足与滚珠丝杠的传动要求,使达到最高精度。
因为为了提高机床的效率和精度,我们要对机床的纵、横方向进行改造把以前的手动进给改为伺服电机自动进给,所以要把以前的大拖把去掉,换上伺服电机控制来提高精度。
所以根据第二部分的计算和其它硬件的搭配我们选出了合适的伺服电机。
五.系统选择:
在此选择FANUC生产的0imateB系统
其该系统的操作面板。
如图4-3.
该系统的特点:
1整体软件功能包,清晰的显示器,高性能的交流伺服电动机和放大器
丰富的先进功能
o高速高精度控制功能。
o零件程序多段预读控制,实现切削速度的最佳加速度和减速度。
o伺服采用HRV控制,提高系统的鲁棒性和实现高增益的速度控制。
o大大降低位置指令的延时,缩短定位时间。
oPowerMateCNC管理:
除CNC控制轴外,,并可在CNC上进行设定和显示。
2丰富的维修功能
o报警历史记录操作历史记录:
报警信息自动地存到CNC存储器内,并且可以显示:
也可自动记录所有的操作。
这两项功能可方便地检查故障。
o伺服波形显示:
各种伺服数据,如位置误差、指令脉冲、转矩指令以波形显示在CNC的显示屏上,不用示波器就可方便地检查伺服故障。
FANUC0imateB系统的优点:
1)结构简单,控制方便精确。
2)所选系统体积较小站的面积较小,便于安装和接线。
3)所选系统符合各硬件的要求。
4)次系统满足拉加工的要求和精度的要求,而且价格比较合适。
5)所选系统体积较小
6)所选系统满足所选伺服电机的要求。
基本功能、选配功能
系统的基本功能:
快速最高2mmin、螺距误差补偿、刀具半径补偿、主轴模拟电压控制(变频主轴)、
通讯接口、用户输入48点输出48点、主轴由变频器直接外部控制调速。
尾座、4工位电动刀架(单向选刀)、防护门检测、压力检测、机床硬限位检测等功能。
基本附件
开关电源:
GSK-PC(已装配)
注:
与驱动器等部件配套供货时,相应的插头随电缆提供。
附件电缆:
10芯绞合屏蔽电缆1