650单机架可逆冷轧机AGC液压伺服系统设计毕业论文Word格式.doc
《650单机架可逆冷轧机AGC液压伺服系统设计毕业论文Word格式.doc》由会员分享,可在线阅读,更多相关《650单机架可逆冷轧机AGC液压伺服系统设计毕业论文Word格式.doc(78页珍藏版)》请在冰豆网上搜索。
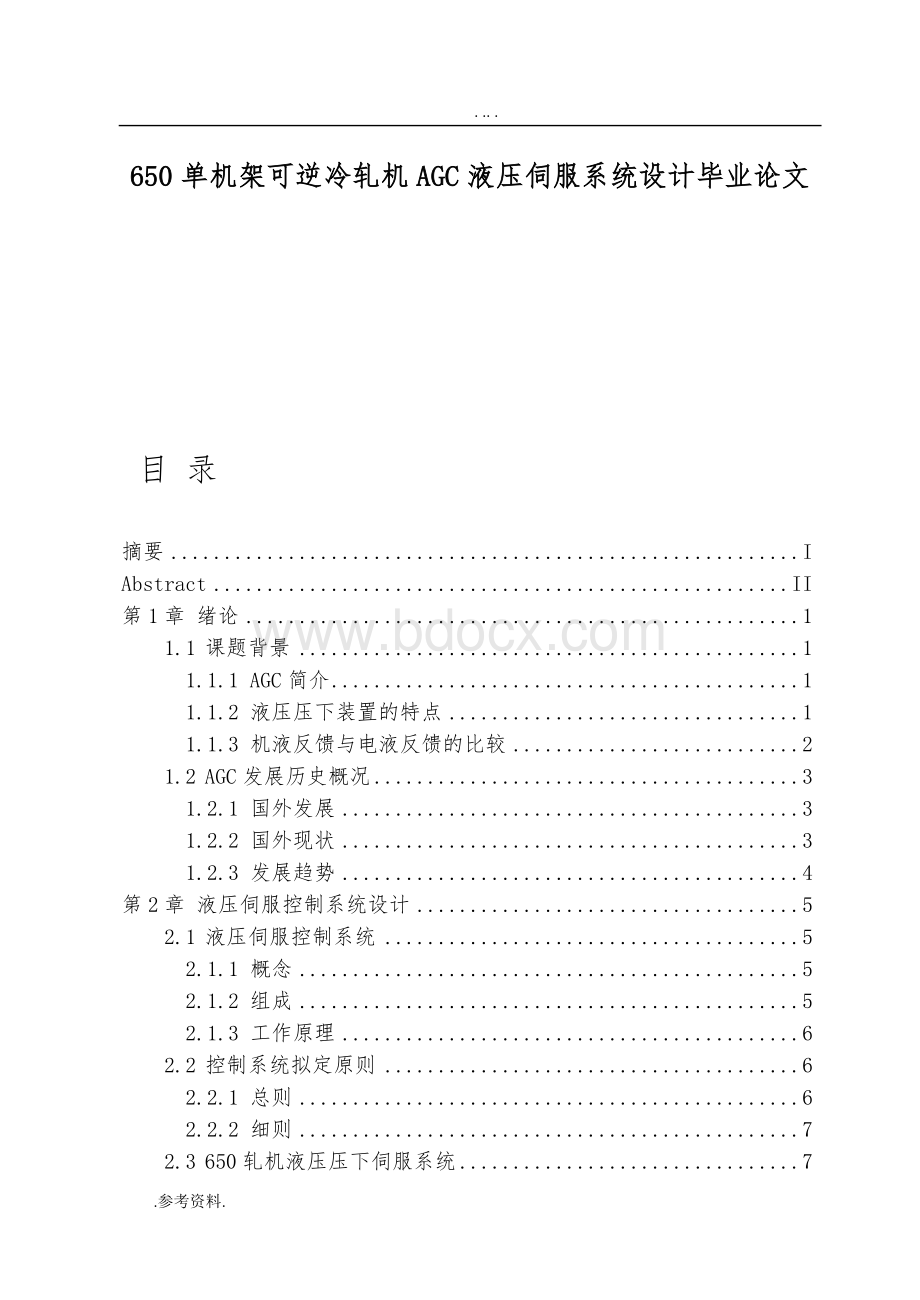
2.2.1总则 6
2.2.2细则 7
2.3650轧机液压压下伺服系统 7
2.3.1明确设计要求 7
2.3.2拟定控制方案,绘制液压原理图 7
2.3.3设计计算动力元件参数 10
第3章液压元件的计算及其选择 12
3.1自制伺服液压缸 12
3.2伺服阀的选择 13
3.3液压泵的选择 13
3.3.1主泵——轴向柱塞泵 13
3.3.2辅泵——叶片泵 14
3.4电机的选择 15
3.5阀类元件的选择 15
3.5.1减压阀 15
3.5.2电磁溢流阀 15
3.5.3单向阀 16
3.5.4电磁换向阀 16
3.5.5电磁水阀 16
3.5.6截止阀 16
3.6液压附件的选择 16
3.6.1蓄能器 16
3.6.2过滤器 18
3.6.3温度计 19
3.6.4电加热器 19
3.6.5液位计 20
3.6.6减震喉 20
3.6.7橡胶接管 20
3.6.8测压排气接头 20
3.6.9压力表 20
3.6.10冷却器 20
3.6.11安全截止阀块 21
3.6.12位置传感器 22
3.6.13压力传感器 22
3.6.14压力继电器 22
第4章泵站的设计 23
4.1油箱的基本设计 23
4.2泵站结构设计注意事项 24
第5章集成块的设计 25
5.1集成块设计规 25
5.2设计步骤 26
5.3空间油路图 27
第6章系统建模仿真 29
6.1轧机液压压下系统建模 29
6.1.1伺服阀 29
6.1.2液压缸和负载 30
6.2系统传递函数及仿真结果 31
结论 35
参考文献 37
致谢 39
附录1外文翻译 41
附录2开题报告 57
附录3文献综述 63
.参考资料.
第1章绪论
1.1课题背景
长期以来,带钢轧机上使用的是电动压下装置。
近年来随着工业的发展,带钢的轧制速度逐渐提高,产品的尺寸进度要求日益严格。
特别是采用厚度自动控制AGC系统以后,电动压下装置由于有传动效率低、运动部分的转动惯量大、反应速度慢、调整精度低等缺点,已不能满足工艺要求。
为了提高产品的尺寸精度,在高速带钢轧机上开始采用液压压下装置。
1.1.1AGC简介
带材厚度自动控制AGC系统是指带材厚度达到设定的目标偏差围而对轧机进行在线调节的一种控制系统。
1.1.2液压压下装置的特点
与电动压下装置比较,液压压下装置有以下特点:
1.快速响应性好,调整精度高。
液压压下装置有很高的辊缝调整速度和加速度。
尤其是很大的加速度潜在能力。
在频率响应、位置分辨率诸方面都大大优于电动压下装置。
下表给出了两者动态特性方面的比较。
项目
速度
mm/s
加速度
mm/s2
辊缝改0.1mm的时间s
频率响应宽度围Hz
位置分辨率
mm
电动压下
0.1~0.5
0.5~2
0.5~1.0
0.01
液压压下
2~5
20~120
0.05~0.1
6~20
0.001~0.0025
改善系数
10~20
40~60
12~20
4~10
图1-1电动压下也液压压下的比较
动态性能大幅度提高,使得产品的精度提高,质量更有保证,缩短了加速减速阶段带钢头尾的超差长度,节约了金属及能源,提高了合格率。
2. 过载保护简单、可靠。
液压系统可以有效地防止轧机过负载,保护轧辊和轴承免遭损坏。
当事故停车时,可迅速排出液压缸的压力油,加大辊缝,避免轧辊烧裂或被刮伤。
3. 采用液压压下实现对轧机的“恒辊缝”和“恒压力”的控制,以适应各种轧制及操作情况。
4. 采用标准液压元件,简化了机械结构
5. 较机械传动效率高。
6. 便于快速换辊,提高轧机作业率
1.1.3机液反馈与电液反馈的比较
按制系统的反馈方式,液压压下装置可分为机械反馈式和电液反馈式。
机械反馈式式较早期的液压压下形式,它对油液的过滤精度不象电液伺服阀那样敏感,但它的部件多,结构复杂,惯性较大,响应频率也低,因此,新建的轧机很少采用这种形式。
电液反馈式的主要优点是系统的惯性小,反应灵敏。
随着电液伺服阀的可靠性的提高和自动控制技术的日益发展,采用这种形式的液压压下轧机逐渐增多。
液压压下装置的可靠性主要取决于液压元件和控制系统的可靠性。
液压压下装置要求较高的备品制造精度和设备维护水平以及可靠的自动化系统。
钢铁工业迅速发展的今天,钢材市场的竞争愈演愈烈。
随着国民经济的高速发展,科学技术不断进步,汽车、机械制造、电器和电子行业对板带材的质量提出了更高的要求。
对于板带钢来说,如何生产出厚度、宽度、板形、板凸度、平面形状等指标都符合实际需要的产品是关键的技术所在。
在所有的尺寸精度指标中,厚度精度是衡量板材及带材的最重要的质量指标之一。
厚度自动控制(AutomaticGaugeControl简称AGC)是提高带材厚度精度的重要方法,其目的是获得带材纵向厚度的均匀性,从而生产出合格的产品。
目前,厚度自动控制已成为现代化板带材生产中不可缺少的组成部分。
从50年代初步应用到现在,已发展到十分成熟的地步。
1.2AGC发展历史概况
1.2.1国外发展
板厚控制技术及其理论的发展经历了由粗到细、由低到高的发展过程。
上世纪三十年代以前,板带轧机厚度控制一直属于人工操作阶段。
这一阶段的轧机装机水平较低,厚度控制是以手动压下或简单的电动压下移动辊缝为主。
自三十年代以来,到六十年代进入了常规自动调整阶段。
该阶段中轧制理论的发展和完善为板带轧机的厚度控制奠定了基础。
第三阶段是六十年代至八十年代的计算机控制阶段。
这一阶段主要形成了计算机控制AGC系统,它能最大限度的消除系统不利影响,在各部分独立工作的同时,充分发挥综合优势,使系统更加完善。
第四阶段,八十年代至现在,板厚控制技术向着大型化、高速化、连续化的方向发展。
这一阶段已将板厚控制的全部过程溶于计算机网络控制的过程自动化级和基础自动化级。
两方面的不断追求合在一起,开发出高精度、无人操作的厚度自动控制系统。
1.2.2国外现状
近年来,国外在板形和板厚等控制技术方面取得了许多新的进展。
国外早在五十年代就开始在电动机械压下轧机上采用AGC控制技术以提高带材纵向厚度精度。
国外轧机的厚度控制应用于电动机械轧机和液压轧机、冷轧机和热轧机、连轧机和单机架轧机。
近30年来,国外轧机的装备水平发展很快。
在冷带轧机上广发利用液压压下、液压弯辊、厚度自动控制、板形控制和计算机控制等技术,在新技术运用方面均已采用液压AGC系统与计算机控制相结合的DCS,装设了测量精度高的三测仪表(测厚、测压、测),且装设了板形检测装置。
人工智能(AI)技术已经广泛应用,包括模糊控制(FZ)、专家系统(ES)和人工神经元网络(ANN)技术在AGC系统中的应用,已经取得了巨大成果和经济效益。
我国在这方面的发展也很迅速,如在基础控制方面、计算机控制、控制算法上取得了很大成绩。
智能控制等先进控制技术在轧机轧制力控制等方面也有了初步应用,并取得了一定成果。
我国自行研制的冷热板带轧机的液压AGC系统在轧制线上也得到了成功应用。
我国的现有冷带板的生产已有较大的改善。
然而总体上还存在着装备水平低,单套机组产能低,产品质量有待提高等诸多问题。
近几年,许多引进的轧机相继进行了技术改造,增加液压压下系统,并配备计算机控制系统,实现液压厚度自动控制。
开发实用性、高精度自控系统装备现有的设备,能使我国钢铁冷轧设备的控制水平进一步提高。
1.2.3发展趋势
虽然AGC系统在各个方面有不同程度的发展,但是,由于各方面因素的限制,AGC系统还并不完美。
对于AGC这样一个多变量、强耦合、非线性的实时控制过程,一方面采用最优控制、多变量控制、自适应控制、预测控制等最新控制理论,以追求控制性能的最高水平;
另一方面采用神经网络、模糊控制、遗传算法等智能算法,以追求系统的灵活性和多样性。
以上两方面的追求融合在一起,开发出高精度的厚度自动控制系统是AGC控制技术发展的大趋势。
各种控制理论和智能算法的不同组合也在这一领域提供了广阔的探索空间。
第2章液压伺服控制系统设计
2.1液压伺服控制系统
2.1.1概念
液压伺服控制系统是自动控制这一领域中的重要组成部分。
自动控制就是用各类控制装置和仪表包括计算机代替人工,自动地,有目的地控制和操纵机器及生产设备,是生产的性能、机械化和自动化的水平不断提高,自动控制已成为现代化生产的必要条件之一。
研究连续自动控制系统运动规律的理论,一般称为反馈控制理论;
反馈控制理论的基础是线性连续反馈控制理论。
反馈控制是实现自动控制的最基本方法。
液压伺服控制系统以其相应快、负载刚度大、控制功率大等独特的优点在工业控制中得到了广泛的应用。
2.1.2组成
液压伺服控制系统的类型和应用场合相当广泛,然而一个实际的液压控制系统不论如何复杂,都是由输入元件,检测反馈元件、比较元件及转换放大装置(含能源)、执行器和控制对象等基本元件构成。
输入元件——根据系统动作要求,给出输入信号,加于系统的输入端。
比如计算机、电位器、信号发生器等;
比较元件——将反馈信号与输入信号进行比较,产生偏差信号加于放大装置。
其不单独存在;
检测反馈元件——用于检测系统的输出量并转换成反馈信号,加于系统的输入端与输入信号进行比较,从而构成反馈控制。
比如各类常见的传感器;
转换放大装置——将偏差信号的能量形式进行变换并加以放大,输入到执行机构。
比如各类液压控制放大器、伺服阀、比例阀等;
执行器——驱动受控对象动作,实现调节任务。
比如液压马达、液压缸等;
受控对象——和执行器的可动部分相连接并同时运动,在负载运动时所引起的输出量中,可根据需要选择其中某物理量作为系统的控制量;
液压能源——为系统提供驱动负载所需的具有压力的液流,是系统的动力源。
比如液压泵站。
2.1.3工作原理
液压伺服控制系统是利用反馈控制的基本原理将被控制对象的输入信号即输出量,如位移、速度或力等,能自动地、快速而准确地回输到系统的输入端,并与给定值进行比较形成偏差信号,并产生对被控对象的控制作用,使系统的输出量与给定值之差保持在允许的围之。
与此同时,输出功率被大幅度地放大。
液压伺服控制系统的工作原理可由下图说明。
图2-1液压伺服系统的工作原理
2.2控制系统拟定原则
2.2.1总则
电液伺服系统的控制方案主要是根据设计要求,如被控物理量、控制功率的大小、执行器的运动方式、各种动静态性能指标值以及环境条件和价格等因素考虑决定的。
为使所设计的系统具有先进性,应避免在设计中出现重大失误,拟定系统总体方案时应进行同主系统的情况论证和初拟几种方案进行对比分析,初步确定一个较优方案。
2.2.2细则
要求结构简单、造价低、控制精度不需要很高的场合宜采用开环控制。
反之对于外界干扰敏感、控制精度要求高的场合