汽车轻量化车用铝材行业分析报告Word格式文档下载.docx
《汽车轻量化车用铝材行业分析报告Word格式文档下载.docx》由会员分享,可在线阅读,更多相关《汽车轻量化车用铝材行业分析报告Word格式文档下载.docx(31页珍藏版)》请在冰豆网上搜索。
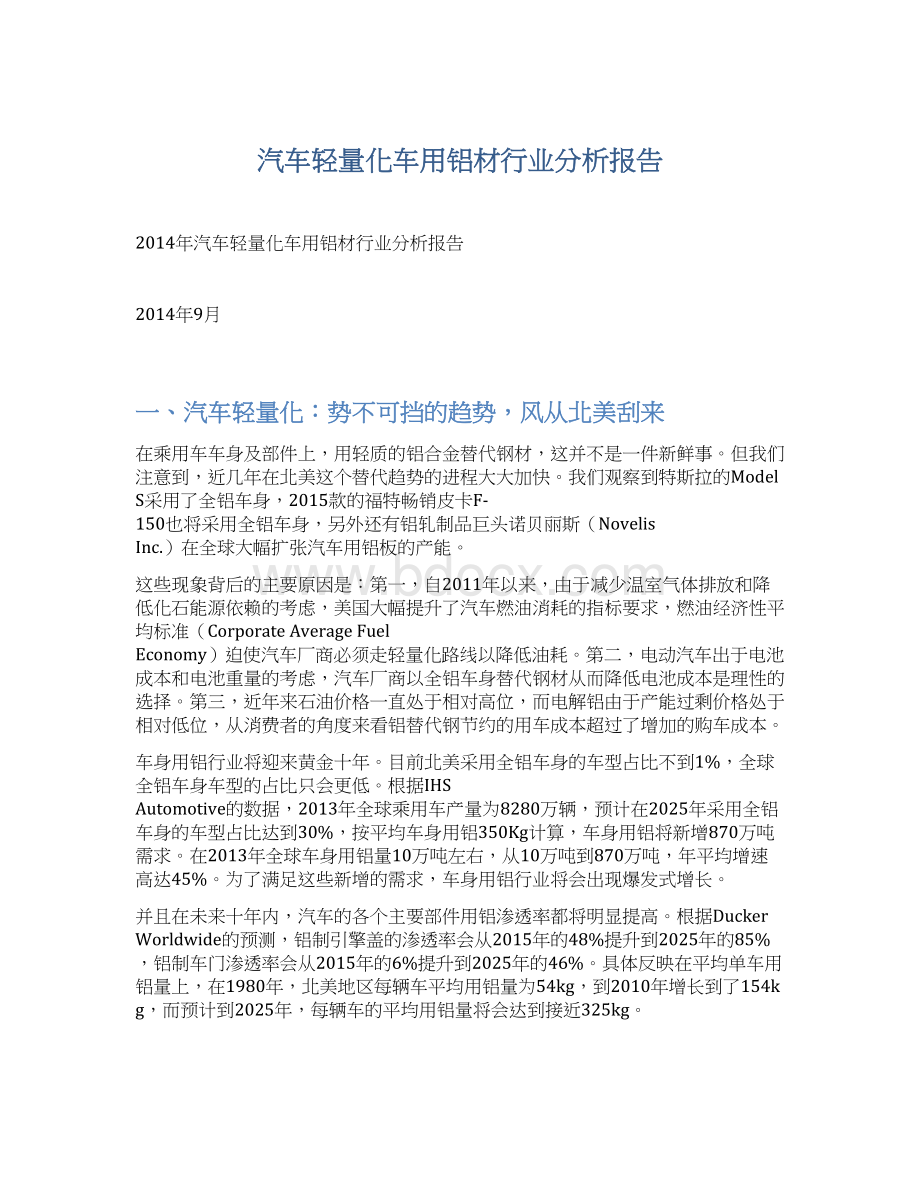
这些现象背后的主要原因是:
第一,自2011年以来,由于减少温室气体排放和降低化石能源依赖的考虑,美国大幅提升了汽车燃油消耗的指标要求,燃油经济性平均标准(CorporateAverageFuelEconomy)迫使汽车厂商必须走轻量化路线以降低油耗。
第二,电动汽车出于电池成本和电池重量的考虑,汽车厂商以全铝车身替代钢材从而降低电池成本是理性的选择。
第三,近年来石油价格一直处于相对高位,而电解铝由于产能过剩价格处于相对低位,从消费者的角度来看铝替代钢节约的用车成本超过了增加的购车成本。
车身用铝行业将迎来黄金十年。
目前北美采用全铝车身的车型占比不到1%,全球全铝车身车型的占比只会更低。
根据IHSAutomotive的数据,2013年全球乘用车产量为8280万辆,预计在2025年采用全铝车身的车型占比达到30%,按平均车身用铝350Kg计算,车身用铝将新增870万吨需求。
在2013年全球车身用铝量10万吨左右,从10万吨到870万吨,年平均增速高达45%。
为了满足这些新增的需求,车身用铝行业将会出现爆发式增长。
并且在未来十年内,汽车的各个主要部件用铝渗透率都将明显提高。
根据DuckerWorldwide的预测,铝制引擎盖的渗透率会从2015年的48%提升到2025年的85%,铝制车门渗透率会从2015年的6%提升到2025年的46%。
具体反映在平均单车用铝量上,在1980年,北美地区每辆车平均用铝量为54kg,到2010年增长到了154kg,而预计到2025年,每辆车的平均用铝量将会达到接近325kg。
乘用车生产是全球充分竞争性行业,民用铝材生产也是全球竞争性行业。
我们认为,北美乘用车铝化率加速提高的趋势,将很快影响到我国以及其他国家。
2013年,中国汽车产量为2200万辆,位居世界第一,目前平均每辆车用铝量比发达国家低15%左右。
在全球乘用车铝化率提高的大趋势下,中国车用铝材生产企业将显著受益。
这个趋势从北美扩散到中国是个必然的进程。
而目前国内乘用车铝材加工行业正处于趋势扩散期间的宝贵“时间差”,也是最佳的投资窗口。
1、愈加严苛的能耗标准,汽车厂商压力空前
为了减少燃油消耗和温室气体排放,美国针对机动车的能耗监管日趋严格。
我们可以看到,自从20世纪70年代美国颁布燃油经济性平均标准(CorporateAverageFuelEconomy)法案后,美国乘用车平均油耗从1978年的13L/100km左右,下降到2014年的6.9L/100km,燃油效率基本上提高了一倍。
在1990-2010年二十年间,燃油经济性平均标准基本保持不变。
但从2011年开始,由于奥巴马政府的推动,燃油经济性平均标准开始加速大幅提高,以摆脱美国对于石油能源的依赖和保护生态环境。
从2012年开始,美国国家公路交通安全管理局(NHTSA)发布了新的燃油经济性平均标准,每种车型计算其轮胎占用面积,根据面积相对应燃油消耗标准。
新标准的实施,使得汽车在未来的燃油平均消耗必须大幅减少,导致了汽车厂商必须采取更多的轻量化措施以提高燃油经济性,从而使得汽车用铝量快速增长。
从图中可以看出,横坐标为车辆的轮胎占用面积(平方英尺),纵坐标为油耗(英里每加仑)。
丰田节能汽车的标杆车型2012款普锐斯,轮胎占用面积为45平方英尺(4.18平方米),平均油耗为50英里每加仑(4.7升每百公里)。
而到了2022年,2012款普锐斯的燃油消耗标准将成为45平方英尺以下乘用车必须达到的最低指标(如图中红点所示)。
为了达到越来越严苛的燃油消耗标准,汽车厂商采取的应对措施主要是发展新能源汽车和降低燃油车的能耗。
减少车辆的自重不管对于新能源车或者降低燃油车能耗来说都非常重要,研究表明,汽车所用燃料的60-70%是消耗于汽车自重,如果汽车自重减少10%,可以降低油耗6-8%,降低二氧化碳排放13%。
2、未来北美汽车用铝将迎来黄金十年,铝渗透率将大幅提升
加大铝在汽车部件中的应用成为了汽车厂商的主流选择,从而导致了北美地区汽车行业用铝量快速发展。
在2012年,北美地区汽车行业用铝量为245万吨,综合DuckerWorldwide及其他方的预测,预计2015年北美地区汽车行业用铝量会超过310万吨,相比2012年增长28%。
而到了2025年,预计北美地区汽车行业用铝量会超过600万吨。
我们也注意到北美汽车制造中的平均用铝量在快速上升。
在1980年,北美地区每辆车平均用铝量为54kg,到2010年增长到了154kg,而预计到2025年,每辆车的平均用铝量将会达到接近325kg。
汽车用铝量的增长趋势明显加快。
汽车厂商采用全铝车身制造乘用车已经开始逐渐形成气候。
预计2015年北美生产的1700万辆乘用车中,有超过50万辆的皮卡和电动汽车会使用全铝车身,尽管从比例上来看只有3%,但从绝对量来看这就将使用25万吨铝材。
预计到2025年,超过70%的皮卡都将会采用全铝车身。
在未来的十年内,汽车的各个主要部件用铝渗透率都将明显提高。
预计铝制引擎盖的渗透率会从2015年的48%提升到2025年的85%,铝制车门渗透率会从2015年的6%提升到2025年的46%,这将是铝最容易渗透的两个汽车部件。
另外在车顶、后备箱、保险杠等领域,铝的渗透率也将大幅度提高。
3、新能源车的发展带来轻量化新趋势,小荷才露尖尖角
以电动汽车为代表的新能源汽车加速发展,将大幅带动汽车铝材的需求。
对于电动汽车而言,消费者最大的诉求就是续航里程,在单体电池容量不变的情况下,增加续航里程就必须安装更多电池。
而电池是电动汽车最主要的成本之一,安装更多电池不仅会显著增加成本,而且带来的车重增加也会消耗更多电能。
电动汽车轻量化的紧迫性远大于传统燃油汽车,使用更多的铝材可以有效的减轻整体重量。
特斯拉的代表车型ModelS采用了全铝车身。
2011年,北美纯电动车厂商特斯拉推出了跨时代产品ModelS,也是特斯拉目前销量最好的一款电动车,2013年全球销量超过2.23万辆。
ModelS除了其充满科技感的设计和构造,突出的亮点是采用了铝合金作为车身框架材料,从而控制了整体车重,给消费者带来了更好的驾驶体验。
ModelS的重量大约为2100Kg,其中铝合金车身占比17%,大约360kg。
采用铝合金作为电动车车身材料,可以有效减少车重,降低制造成本。
欧洲铝业协会(EAA)的研究表明,对于大众高尔夫之类的典型车型,在相同续航里程的情况下,由于铝制电动车携带的电池重量小于钢制电动车,全铝车身比钢制车身需要的电池容量减少了9%。
尽管全铝车身成本较高,但由于减少车重节约的电池成本大于用铝后增加的成本,使得全铝电动车在出厂时就具有明显的价格优势,平均下来每辆铝制电动车比传统钢制电动车便宜635欧元。
4、福特F-150皮卡,传统畅销车型的不一样
福特F-150属于福特的F系列皮卡,是史上最受欢迎的车型之一,24年位居美国最佳销量汽车名单之首。
2013年F-150全年销量达到了76万辆,占据了美国皮卡市场40%的份额。
2015款新福特F-150将采用全铝车身制造,为全球首款采用全铝车身的高量产车,开启了汽车用铝的新时代。
每辆F-150的铝合金使用量超过480Kg,占到整车质量的25%。
采用全铝车身后,整车重量将减轻317Kg,燃油经济性有望提高15-20%。
这是全球首次在高量产车上使用全铝车身,意义非常重大。
之前也有汽车厂商在某些高端车型上采用了全铝车身,譬如奥迪A8等,但都是在豪华车上使用,用量比较小。
F-150在北美的售价在3万美元左右,属于中端车型。
福特F-150作为销量第一的皮卡,采用了全铝车身,标志着传统整车厂大规模用铝的开始,标志着全铝车身从高端车向中端车开始普及。
到2016年,预计福特将会生产85万辆F-150皮卡,每年需求超过40万吨铝材。
5、归根结底,经济因素是乘用车铝替代钢的核心原因
车辆生产中铝替代钢的根本原因,是不同材料背后代表的消费者购车成本和用车成本,经仔细计算比较后厂商和消费者共同做出的理性选择。
整车厂决定是否用铝来替代钢,除了考虑汽车能耗必须满足NHTSA的CAFE标准外,也必须站在消费者的角度考虑购车成本和用车成本。
自09年全球金融危机以来,原油价格从50美金/桶的低位反弹,近年来一直基本维持在100-110美金/桶的区间,居高不下的油价使得用车成本处于高位。
而铝价从09年反弹至11年的高点后,便一直处于下跌空间,尽管最近有所反弹,但仍处于2000美金/吨左右的相对低位。
整车厂商提高车辆用铝的比重会增加消费者的购车成本,但同时也会降低消费者的用车成本。
在同样满足燃油消耗和排放标准的前提下,只有使用铝材降低的用车成本大于增加的购车成本时,整车厂商才会有动力去用铝材替代钢材。
我们判断目前的铝价和油价水平,已经达到或者超过了成本的均衡点,使得整车厂商愿意用铝材去替代钢材,从而满足消费者的需求。
这也解释了福特F-150这类高销量车开始采用铝制车身的原因。
6、诺贝丽斯,汽车铝材巨头在北美的产能扩张
诺贝丽斯(NovelisInc.)是全球领先的铝轧制产品生产巨头,专注于铝材加工行业,产品包括汽车铝材、易拉罐罐料、铝箔等。
在2013财年全年公司的收入为约100亿美元,其下游客户包括奥迪、宝马、福特、捷豹路虎等主流整车厂商。
近几年诺贝丽斯大幅扩张产能,以面对汽车轻量化的需求。
诺贝丽斯的2013财年(截止于2014年3月31日)年报披露,在2013财年公司的轧铝产品产量为289.5万吨。
但根据公司的投资计划,从2012年12月至2015年12月的三年时间里,诺贝丽斯将扩张合计117万吨的汽车铝材产能,也即扩张40%的总产能来应对汽车轻量化带来的新需求。
乘用车用铝供需出现缺口,利好诺贝丽斯等龙头企业。
分析诺贝丽斯的2013财务报表可以发现,正因为全球汽车厂商对于铝材的需求非常旺盛,目前公司的产能无法满足迅速增长的需求,所以公司这几年在大规模新建产能。
汽车铝材的毛利率明显高于易拉罐、铝箔等传统铝加工产品,这也解释了诺贝丽斯近两年的毛利率在稳步上升。
公司看好未来相当长时期内的全球汽车用铝需求。
仅在2013财年,诺贝丽斯就投入了超过7亿美金在全球扩张产能。
汽车铝材加工生产是重资产行业,新建一条年产12万吨的铝材生产线就需要2亿美元以上的投入,并且新建产能订购生产设备需要一个较长的周期,铝材加工厂商只有在行业的长景气周期里才会考虑扩张产能。
诺贝丽斯大规模新建产能是经过慎重考虑的,也从侧面验证了汽车铝材加工行业的未来景气度。
二、选择铝合金的原因
铝及铝合金是现代社会使用最广泛的金属材料之一。
选择铝合金材料替代钢材是目前整车厂商最现实、最可能的选择。
铝的密度仅为钢铁的1/3,使用成本远低于钛合金、碳纤维等材料。
铝是全球产量最大的有色金属,2013年全球共消费了5170万吨铝。
铝合金除了适合大规模应用外,并且完全无害对环境友好,易于回收。
有资料显示,自1888年以来,约75%的铝金属今天依然在使用当中。
再生铝的能耗相当于原铝生产能耗的5%,但废钢的再生能耗相当于精钢冶炼能耗的25%-60%。
铝材的应用非常广泛,小到拉链,手机,易拉罐,大到轮船,火车,飞机等。
铝材的用途可以主要分为建筑业,交通运输业,电子电气及机械装备等。