接线盒注塑模具毕业设计说明书论文.docx
《接线盒注塑模具毕业设计说明书论文.docx》由会员分享,可在线阅读,更多相关《接线盒注塑模具毕业设计说明书论文.docx(29页珍藏版)》请在冰豆网上搜索。
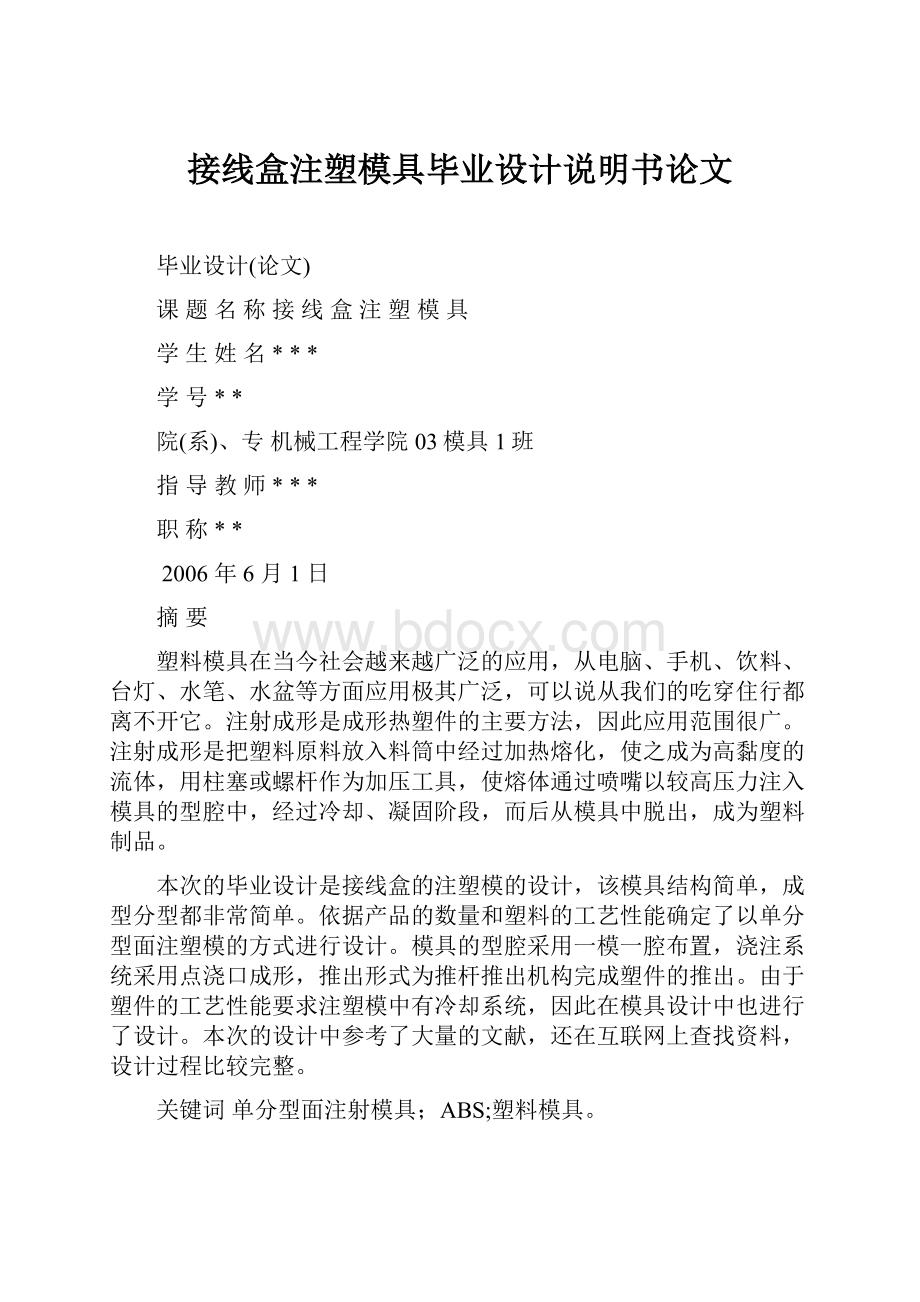
接线盒注塑模具毕业设计说明书论文
毕业设计(论文)
课题名称接线盒注塑模具
学生姓名***
学号**
院(系)、专机械工程学院03模具1班
指导教师***
职称**
2006年6月1日
摘要
塑料模具在当今社会越来越广泛的应用,从电脑、手机、饮料、台灯、水笔、水盆等方面应用极其广泛,可以说从我们的吃穿住行都离不开它。
注射成形是成形热塑件的主要方法,因此应用范围很广。
注射成形是把塑料原料放入料筒中经过加热熔化,使之成为高黏度的流体,用柱塞或螺杆作为加压工具,使熔体通过喷嘴以较高压力注入模具的型腔中,经过冷却、凝固阶段,而后从模具中脱出,成为塑料制品。
本次的毕业设计是接线盒的注塑模的设计,该模具结构简单,成型分型都非常简单。
依据产品的数量和塑料的工艺性能确定了以单分型面注塑模的方式进行设计。
模具的型腔采用一模一腔布置,浇注系统采用点浇口成形,推出形式为推杆推出机构完成塑件的推出。
由于塑件的工艺性能要求注塑模中有冷却系统,因此在模具设计中也进行了设计。
本次的设计中参考了大量的文献,还在互联网上查找资料,设计过程比较完整。
关键词单分型面注射模具;ABS;塑料模具。
Abstract
Plasticmouldintoday'ssocietymoreandmorewideapplication,fromthecomputer,mobilephone,beverage,desklamp,liquidpen,birdbathiswidelyused,etc,itcanbesaidthatfromourfoodandclothinglivescannotgetawayfromitall.Injectionmoldingisforminghotplasticpiecesofmainmethods,sowideapplications.Theplasticinjectionmoldingisingredientsinanitrogen-treatedbarrelwithheatofmelting,makeitbecomethehighviscosityfluid,withpistonorscrewaspressuretool,meltthroughthenozzlewithhigherinjectionmouldcavitypressure,aftercooling,coagulationphase,andthenfromthemoldindecentshape,becomeplasticproducts.
ThegraduationdesignisJunctionboxofinjectionmouldstent,thediestructuresimple,formingthepartingquitesimple.Accordingtothenumberofproductsandplastic'sprocessperformancedeterminedthepartingsurfaceinasingleinjectionmoldwaydesign.Themouldcavityuseamoduleandfourcavitybalancelayout,pouringsystemUSESsomegateforming,rolloutformforpushboardlaunchedinstitutionsplasticpartstolaunchthefinish.Becauseplasticpartsoftheprocessperformancerequirementsofinjectionmoldcoolingsystem,andthereforeinthemolddesignanddesign.Thedesignofthereferenceofalargenumberofliterature,andalsointheInternetformaterial,designprocessiscomplete.
Keywords:
singleinjectionmoldpartingsurface;ABS;Plasticmould.
绪论
1国际国内塑料成型模具发展概况
80年代以来,在国家产业政策和与之配套的一系列国家经济政策的支持和引导下,我国模具工业发展迅速,年均增速为13%,2003年我国模具工业产值为375亿,至2007年我国模具总产值约为525亿元,其中塑料模约35%左右。
在未来的模具市场中,塑料模在模具总量中的比例还将逐步提高。
我国塑料模工业从起步到现在,历经半个多世纪,有了很大发展,模具水平有了较大提高。
在大型模具方面已能生产48英寸大屏幕彩电塑壳注射模具、6.5Kg大容量洗衣机全套塑料模具以及汽车保险杠和整体仪表盘等塑料模具,精密塑料模具方面,已能生产照相机塑料件模具、多型腔小模数齿轮模具及塑封模具。
如天津津荣天和机电有限公司和烟台北极星模具有限公司制造多腔VCD和DVD齿轮模具,所生产的这类齿轮塑件的尺寸精度、同轴度、跳动等要求都达到了国外同类产品的水平,而且还采用最新的齿轮设计软件,纠正了由于成型收缩造成齿形误差,达到了标准渐开线齿形要求。
还能生产厚度仅为0.08mm的一模两腔的航空杯模具和难度较高的塑料门窗挤出模等等。
注塑模型腔制造精度可达0.02mm~0.05mm,表面粗糙度Ra0.2μm,模具质量、寿命明显提高了,非淬火钢模寿命可达10~30万次,淬火钢模达50~1000万次,交货期较以前缩短,但和国外相比仍有较大差距,具体数据见表1-1。
表1-1国内外塑料模具技术比较表
项目
国外
国内
注塑模型腔精度
0.005~0.01mm
0.02~0.05mm
型腔表面粗糙度
Ra0.01~0.05μm
Ra0.20μm
非淬火钢模具寿命
10~60万次
10~30万次
淬火钢模具寿命
160~300万次
50~100万次
热流道模具使用率
80%以上
总体不足10%
标准化程度
70~80%
小于30%
在模具行业占有量
30~40%
25~30%
成型工艺方面,多材质塑料成型模、高效多色注射模、镶件互换结构和抽芯脱模机构的创新方面也取得较大进展。
气体辅助注射成型技术的使用更趋成熟,如青岛海信模具有限公司、天津通信广播公司模具厂等厂家成功地在29~34英寸电视机外壳以及一些厚壁零件的模具上运用气辅技术,一些厂家还使用了C-MOLD气辅软件,取得较好的效果。
如上海新普雷斯等公司就能为用户提供气辅成型设备及技术。
热流道模具开始推广,有的厂采用率达20%以上,一般采用内热式或外热式热流道装置,少数单位采用具有世界先进水平的高难度针阀式热流道模具。
但总体上热流道的采用率达不到10%,与国外的50%~80%相比,差距较大。
在制造技术方面,CAD/CAM/CAE技术的应用水平上了一个新台阶,以生产家用电器的企业为代表,陆续引进了相当数量的CAD/CAM系统,如美国EDS的UGⅡ、美国ParametricTechnology公司的Pro/Emgineer、美国CV公司的CADS5、英国Deltacam公司的DOCT5、日本HZS公司的CRADE、以色列公司的Cimatron、美国AC-Tech公司的C-Mold及澳大利亚Moldflow公司的MPA塑模分析软件等等。
这些系统和软件的引进,虽花费了大量资金,但在我国模具行业中,实现了CAD/CAM的集成,并能支持CAE技术对成型过程,如充模和冷却等进行计算机模拟,取得了一定的技术经济效益,促进和推动了我国模具CAD/CAM技术的发展。
近年来,我国自主开发的塑料模CAD/CAM系统有了很大发展,主要有北航华正软件工程研究所开发的CAXA系统、华中科技开发的注塑模HSC5.0系统及CAE软件等,这些软件具有适应国内模具的具体情况、能在微机上应用且价格低等特点,为进一步普及模具CAD/CAM技术创造了良好条件。
近年来,国内已较广泛地采用一些新的塑料模具钢,如:
P20,3Gr2Mo、PMS、SMⅠ、SMⅡ等,对模具的质量和使用寿命有着直接的重大影响,但总体使用量仍较少。
塑料模具标准模架、标准推杆和弹簧等越来越广泛得到应用,并且出现了一些国产的商品化的热流道系统元件。
但目前我国模具标准化程度的商品化程度一般在30%以下,和国外先进工业国家已达到70%~80%相比,仍有差距。
2我国模具设计技术今后发展方向
(1)提高大型、精密、复杂、长寿命模具的设计水平及比例。
这是由于塑料模成型的制品日渐大型化、复杂化和高精度要求以及因高生产率要求而发展的一模多腔所致。
(2)在塑料模设计制造中全面推广应用CAD/CAM/CAE技术。
CAD/CAM技术已发展成为一项比较成熟的共性技术,近年来模具CAD/CAM技术的硬件与软件价格已降低到中小企业普遍可以接受的程度,为其进一步普及创造良好的条件;基于网络的CAD/CAM/CAE一体化系统结构初见端倪,其将解决传统混合型CAD/CAM系统无法满足实际生产过程分工协作要求的问题;CAD/CAM软件的智能化程度将逐步提高;塑料制件及模具的3D设计与成型过程的3D分析将在我国塑料模具工业中发挥越来越重要的作用。
(3)推广应用热流道技术、气辅注射成型技术和高压注射成型技术。
采用热流道技术的模具可提高制件的生产率和质量,并能大幅度节省塑料制件的原材料和节约能源,所以广泛应用这项技术是塑料模具的一大变革。
制订热流道元器件的国家标准,积极生产价廉高质量的元器件,是发展热流道模具的关键。
气体辅助注射成型可在保证产品质量的前提下,大幅度降低成本。
目前在汽车和家电行业中正逐步推广使用。
气体辅助注射成型比传统的普通注射工艺有更多的工艺参数需要确定和控制,而且常用于较复杂的大型制品,模具设计和控制的难度较大,因此,开发气体辅助成型流动分析软件,显得十分重要。
另一方面为了确保塑料件精度,继续研究开发高压注射成型工艺与模具也非常重要。
(4)开发新的成型工艺和快速经济模具。
以适应多品种、少批量的生产方式。
(5)提高塑料模标准化水平和标准件的使用率。
我国模具标准件水平和模具标准化程度仍较低,与国外差距甚大,在一定程度上制约着我国模具工业的发展,为提高模具质量和降低模具制造成本,模具标准件的应用要大力推广。
为此,首先要制订统一的国家标准,并严格按标准生产;其次要逐步形成规模生产,提高商品化程度、提高标准件质量、降低成本;再次是要进一步增加标准件的规格品种。
(6)应用优质材料和先进的表面处理技术对于提高模具寿命和质量显得十分必要。
(7)研究和应用模具的高速测量技术与逆向工程。
采用三坐标测量仪或三坐标扫描仪实现逆向工程是塑料模CAD/CAM的关键技术之一。
研究和应用多样、调整、廉价的检测设备是实现逆向工程的必要前提。
1塑件分析
1.1塑件的工艺分析
塑件如图所示:
产品名称:
接线盒注塑模具
产品材料:
ABS
产品数量:
大批量生产
塑料尺寸:
如下图
工件图
该塑料制件外形如上图所示,从图中可以看出该制品形为盒状。
该制件结构简单,有一定的配合尺寸精度要求;塑件设计应本着在保证使用性能,物理性能,力学性能和耐摩擦性能,同时还应力求结构简单、壁厚均匀、成型方便。
在设计塑件时,还要考虑其模具的总体结构,使模具型腔易于制造,模具脱模和推出机构简单。
塑件形状有利于模具分型、排气、补缩和冷却。
此外,在塑件成型以后尽量不再进行机械加工。
1.2塑件材料的分析
丙烯腈-丁二烯-苯乙烯共聚物ABS树脂微黄色或白色不透明,是丙烯腈-丁二烯-苯乙烯共聚物。
丙烯腈使聚合物耐油,耐热,耐化学腐蚀,丁二烯使聚合物具有优越的柔性,韧性;苯乙烯赋予聚合物良好的刚性和加工流动性。
因此ABS树脂具有突出的力学性能和良好的综合性能。
同时具有吸湿性强,但原料要干燥,它的塑件尺寸稳定性好,塑件尽可能偏大的脱模斜度。
1.2.1ABS塑料主要的性能指标:
密度(Kg.dm-3)1.13——1.14
收缩率%0.3~0.8
熔点℃130~160
热变形温度45N/cm65~98
弯曲强度Mpa80
拉伸强度MPa35~49
拉伸弹性模量GPa1.8
弯曲弹性模量Gpa1.4
压缩强度Mpa18~39
缺口冲击强度kJ/㎡11~20
硬度HRR62~86
体积电阻系数Ωcm1013
击穿电压Kv.mm-115
介电常数60Hz3.7
1.2.2ABS的注射成型工艺参数:
注塑机类型:
螺杆式
喷嘴形式:
通用式
料筒一区150——170
料筒二区180——190
料筒三区200——210
喷嘴温度180——190
模具温度50——70
注塑压60——100
保压40——60
注塑时间2——5
保压时间5——10
冷却时间5——15
周期15——30
后处理红外线烘箱
温度(70)
时间(0.3——1)
2.塑件成型的基本过程
注塑成型是把塑料原料(一般经过造粒、染色、添加剂等处理之后的颗粒)放入料间当中,经过加热溶化使之成为高粘度的流体-----熔体用柱塞或螺杆作为加压工具,使得熔体通过喷嘴以较高的压力(约20~85mpa),溶入模具的型腔中经过冷却、凝固阶段,而后从模具中脱出,成为塑料制品。
塑化过程
现代式的注射机基本上采取螺杆式的塑化设备,塑料原粒(称为物料)自从送料斗以定容方式送入料筒,通过料筒外的点加热装置和料筒内的螺杆旋转所产生的摩擦热,使物理熔化达到一定的温度后即可注射,注射动作是由螺杆的推进来完成的。
充模过程
熔体自注射机的喷嘴喷出来后,进入模具的型腔内,将型腔内的空气排出,并充满型腔,然后升到一定压力,使溶体的密度增加,充实型腔的每一个角落。
充模过程是注射成型的最主要的过程,由于塑料溶体的流动是非牛顿流动,而且粘度很大,所以在压力损耗,粘度变化,多般汇流等现象左右塑件的质量,因此充模过程的关键问题------浇注系统的设计就成为注射模具设计过程的重点,现代的设计方法已经运用了计算机辅助设计以解决浇注系统设计中疑难问题。
冷却凝固过程
热塑性塑料的注射成型过程是热交换过程,即:
塑化——注射充模——固化成型
加热——理论上绝热——散热
热交换效果的好坏决定了塑件的质量,模具设计时,散热交换也要充分考虑,在现代设计方法中也采用了计算机辅助设计来解决问题。
脱模过程
塑件在型腔内固化后,必须采取机械的方式把它从型腔内取出,这个动作由脱模机构来完成。
不合理的脱模机构对塑件的质量影响很大,但塑件的几何形状是千变万化的,必须采用最有效和最好的脱模方式。
因此,脱模机构的设计也是注射模具设计的一个主要环节,由于标准化的推广,许多标准化的脱模机构零部件也有商品供应。
由3.1至3.4形成了一个循环,就完成了一次成型乃至很多塑件
3注塑设备的选择
3.1估算塑件体积质量
由UG的测量体功能可以测出塑件的体积,如图所示:
可以得出该塑件的体积为V=97344mm³该塑件的材料为abs密度为1.13—1.14所以M=97344*1.13=110.000g
3.2选择注塑机
根据《模具设计与制造简明手册》表2-40选择注射机XS-ZY-500螺杆式注射机,其参数如下:
额定注射量:
500
螺杆直径:
65mm
注射压力:
104Mpa
锁模力:
3500KN
模板行程:
500mm
模具最大厚度:
450mm
模具最小厚度:
300mm
模板尺寸:
700×850mm
拉杆空间:
500×440mm
定位孔直径:
150mm
合模方式:
液压—机械
4塑料件的工艺尺寸的计算
查有关手册得ABS的收缩率为S=0.4%~0.8%,故平均收缩率为:
S=(0.8-0.4)%/2=0.2%=0.002,根据塑件尺寸公差要求,模具的制造公差取
=Δ/3。
——型腔径向尺寸(mm);
——型腔深度尺寸(mm);
——型芯径向尺寸(mm);
——型芯高度尺寸(mm);
——模具制造偏差(mm);
——平均收缩率(mm/mm);
——模具磨损量
磨损严重时
=Δ/2
磨损轻微时
=Δ/5~Δ/8
不考虑磨损时,去掉各式中的
型腔成型尺寸计算见表4-1
已知:
平均收缩率
=0.05;模具的制造公差取
=Δ/3;修正系数X=0.5
类别
模具零
件名称
塑件
尺寸
计算公式
计算结果
型腔尺寸计算
型腔径向
尺寸计算
38
L
=[(1+S)L-X
]
38.2
23
23.1
15
15.1
7
7.1
5.5
5.5
型腔深度
尺寸计算
16.5
16.6
型芯尺
寸计算
型芯径向
尺寸计算
6
6.1
型芯高度
尺寸计算
6
型腔壁厚的确定
塑料模具型腔的侧壁和底壁厚度计算是模具设计中经常遇到的问题,尤其对大型模具更为突出。
目前常用的计算方法有按强度条件计算和按刚度条件计算两类,但塑料模具要求既不许因强度不足而发生明显变形,甚至破坏,也不许刚度不足而变形过大的情况,因此要求对强度和刚度加以考虑。
对于型腔主要受到的力是塑件熔体的压力,在塑件熔体的压力作用下,型腔将发生内应力及变形。
如果型腔侧壁和底壁厚度不够。
当型腔中产生的内应力超过材料的许用应力时,型腔发生强度破坏,与此同时,刚度不足则发生弹性变形,从而产生溢料现象,将影响塑件成型质量,所以模具对刚度和强度都有要求。
但是,实践证明,模具对强度和刚度的要求并非同时兼顾,对大型腔,按刚度条件,对小型腔则按强度条件计算即可。
(在本设计中按强度条件来计算)
5分型面的设计
分型面的选择主要考虑以下几个问题:
(1)分型面不仅应选择在对制品外观没有影响的位置,而且还必须考虑如何能比较方便地清除分型面产生地溢料飞边。
同时,还应避免分型而产生飞边;
(2)分型面的选择应有利于脱模,否则,模具结构便会变得比较复杂。
通常,分型面的选择应尽可能使制品在开模后滞留在动模一侧;
(3)分型面不影响制品的形状和尺寸精度;
(4)分型面应尽量与最后填充的型腔表面重合,以利于排气;
(5)选择分型面是,应尽量减少脱模斜度给制品大小端尺寸带来的差异;
(6)分型面应便于模具加工;
(7)选择分型面时,应尽量减少制品在分型面上的投影面积,以防止面积过大,造成锁模困难,产生严重的溢料;
6注塑机有关参数的校核
每副模具都只能安装在与其相适应的注塑机上进行生产,因此模具设计与所用的注塑机关系十分密切。
在设计模具时,应校核注塑机的一些技术参数
6.1最大注塑量的校核
注塑机的最大注塑量应大于制品的质量,其中包括了主流道及浇口的凝料。
通常注塑机的实际注塑量最好是在注塑机理论注塑量的80%之间。
故有公式
0.8M机≥M塑+M浇(5.1)
M塑+M浇=27.41g因此,最大的注塑量符合工作的需要。
6.2注塑压力校核
注塑压力校核是校验注塑机的最大注塑压力能不能满足该制品成型的需要,制品成型所需的压力是由注塑机类型、喷嘴形式、塑料流动性、浇注系统和型腔的流动阻力等因素决定的,例如螺杆式注塑机,其注塑机压力传递比柱塞式注塑机好,因此注塑压力可取得小一些,流动性差的塑料的或细长流程塑件注塑压力应取得大一些。
可参考各种塑料的注塑成型工艺确定塑件的注塑压力,再与注塑机额定压力相比较。
那么查《塑料模具手册》可得,其额定注塑压力大于所需的注塑压力。
因此所选择的是符合要求的。
6.3锁模力的校核
当高压的塑料熔体充满模具型腔时,会产生一个很大的力,使模具的分型面涨开,其值等于制件和浇口流道系统在分型面上投影面积之和乘以型腔内塑料压力。
而作用在这个面积上的总力,应小于注塑机的额定锁模力P,否则在注塑时会因模具不紧产生严重的溢边现象。
型腔内塑料压力,可以按公式计算。
而经查《塑料模具设计》中SPVC在型腔里的理论注塑压力在40MP~80MP之间。
而只有F机锁≥P模×A的不等式成立时,才能符合要求。
式中F机锁—表示注塑机的最大锁模力;
P模—表示为熔融型料在型腔内的压力;
A—表示为塑件和浇注系统在分型面上的投影之和;
故有;F机锁=400kn>P模×A=80MP×2936㎜2=189.88kn
所以符合要求。
6.4模具与注塑机安装部分相关尺寸校核
模板尺寸和拉杆间距是否相适合
因为要满足上述要求,只有达到模具长×宽<拉杆间距这样的条件。
而确有,模具长×宽=300×350(mm×mm)<拉杆间距=440×500(mm×mm)成立,所以也是满足要求的。
模具闭合高度的校核
通过前章各模板的尺寸选定和计算,模具实际厚度H模为370mm,而注塑机最小厚度
H最小为300mm,
即;H模>H最小也满足要求。
6.5开模行程与顶装置的校核
在此,本文所选注塑机的最大开模行程与模具厚度的关时的校核。
且该模具结构则属于有侧向抽芯开模动作的结构,故注塑机的开模行程要求符合下式;
S机-Hc>H1+H2+(5~10)mm(5.2)
式中;S机—注塑机板间的最大开距,(mm)
Hc—完成侧抽芯距离l所需要的开模行程,(mm)
H1—开模要顶出的距离,(mm)
H2—塑件的高度,(mm)
而当,Hc≤H1+H2可以按S机-(H模H最小)>H1+H2+(5~10)mm进行计算
式中,HM—成型模板的高度,(mm)
那么可以解得不等式;
S机-(H模H最小)=300-(270-170)>60+116+(5~10)mm=181~186mm,
故也满足要求。
7脱模机构的设计与合模导向结构设计
7.1脱模力计算
矩环形薄壁制品s/d
0.05F=
(N)
r——型芯平均半径(m)
S——制品壁厚(m)
E——塑料弹性模量(Mpa)
Q——塑料平均收缩率(%)
l——制品对型芯的包容长度(m)
f——制品与型芯静摩擦系数f=0.1~0.2
——脱模斜度(
)取1
m——塑料的泊松比m=0.38~0.42
k
——系数k
=2
/(cos
+2
cos
)
k
——系数k
=1+fsin
cos
1
A——盲孔制品型芯在脱模方向投影面积(m
)
已知
,
,
,
,
,
,
、
F=
+0.1*0.029=6052N
7.2脱模结构设计
塑件冷却后由于有少量的收缩,塑件会紧抱在型芯上,所以在脱出产品时不像冲压件那么可以自动脱落。
这样,我们必须设计推出机构将塑件顶出,推出机构设计时我们考虑的是要使塑件各部分受力均匀,在此设计中,我们必须采用一模一腔的结构,再利用顶针和斜抽滑块把产品推出,这样每个产品的受力相同且均匀。
开模时,由于脱模机构的作用模具从定模座板与推料板处首先分型,滑块在斜槽导板的作用下,向两边运动直到斜抽芯完成