机械制造工艺学课程设计计后托架说明书Word格式.docx
《机械制造工艺学课程设计计后托架说明书Word格式.docx》由会员分享,可在线阅读,更多相关《机械制造工艺学课程设计计后托架说明书Word格式.docx(36页珍藏版)》请在冰豆网上搜索。
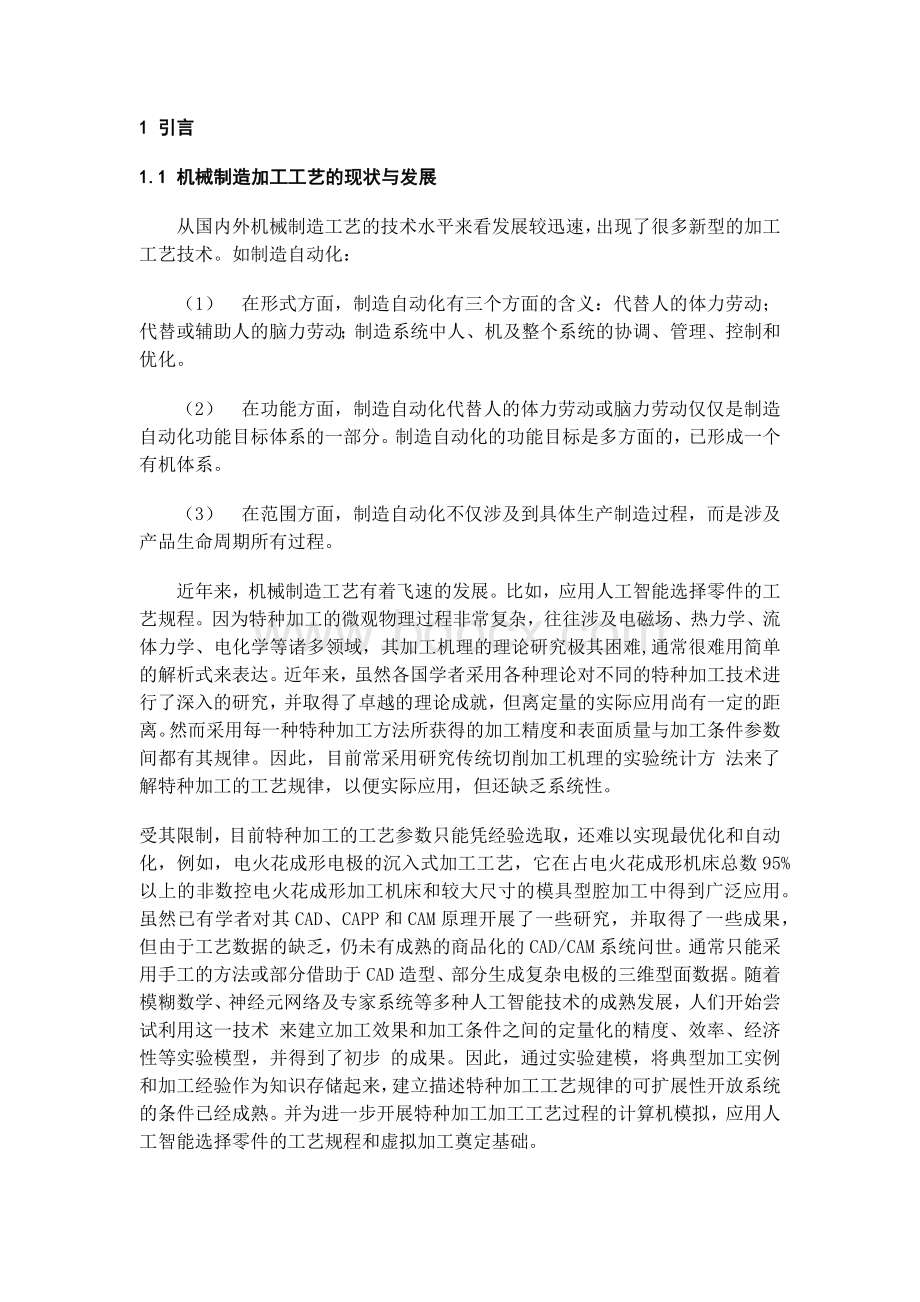
近年来,虽然各国学者采用各种理论对不同的特种加工技术进行了深入的研究,并取得了卓越的理论成就,但离定量的实际应用尚有一定的距离。
然而采用每一种特种加工方法所获得的加工精度和表面质量与加工条件参数间都有其规律。
因此,目前常采用研究传统切削加工机理的实验统计方法来了解特种加工的工艺规律,以便实际应用,但还缺乏系统性。
受其限制,目前特种加工的工艺参数只能凭经验选取,还难以实现最优化和自动化,例如,电火花成形电极的沉入式加工工艺,它在占电火花成形机床总数95%以上的非数控电火花成形加工机床和较大尺寸的模具型腔加工中得到广泛应用。
虽然已有学者对其CAD、CAPP和CAM原理开展了一些研究,并取得了一些成果,但由于工艺数据的缺乏,仍未有成熟的商品化的CAD/CAM系统问世。
通常只能采用手工的方法或部分借助于CAD造型、部分生成复杂电极的三维型面数据。
随着模糊数学、神经元网络及专家系统等多种人工智能技术的成熟发展,人们开始尝试利用这一技术来建立加工效果和加工条件之间的定量化的精度、效率、经济性等实验模型,并得到了初步的成果。
因此,通过实验建模,将典型加工实例和加工经验作为知识存储起来,建立描述特种加工工艺规律的可扩展性开放系统的条件已经成熟。
并为进一步开展特种加工加工工艺过程的计算机模拟,应用人工智能选择零件的工艺规程和虚拟加工奠定基础。
1.2CA6140车床后托架加工工艺规程
为了能具体确切的说明过程,使工件能按照零件图的技术要求加工出来,就得制定复杂的机械加工工艺规程来作为生产的指导性技术文件,学习研究制定机械加工工艺规程的意义与作用就是本课题研究目的。
要制定CA1640车床加工工艺路线。
(1)我们必须仔细了解后托架零件结构,认真分析其零件图,培养我们独立识图能力,增强我们对零件图的认识和了解,通过对零件图的绘制,不仅能增强我们的绘图能力和运用AutoCAD软件的能力。
(2)制订工艺规程、确定加工余量、工艺尺寸计算、工时定额计算、定位误差分析等。
在整个设计中也是非常重要的,通过这些设计,不仅让我们更为全面地了解零件的加工过程、加工尺寸的确定,而且让我们知道工艺路线和加工余量的确定,必须与工厂实际的机床相适应。
这对以前学习过的知识的复习,也是以后工作的一个铺垫。
(3)在这个设计过程中,我们还必须考虑工件的安装和夹紧.安装的正确与否直接影响工件加工精度,安装是否方便和迅速,又会影响辅助时间的长短,从而影响生产率,夹具是加工工件时,为完成某道工序,用来正确迅速安装工件的装置.它对保证加工精度、提高生产率和减轻工韧动量有很大作用。
这是整个设计的重点,也是一个难点。
2CA6140车床后托架的加工工艺设计
机械加工工艺是实现产品设计,保证产品质量,节约能源,降低消耗的重要手段,是企业进行生产准备,计划调度,加工操作,安全生产,技术检测和健全劳动组织的重要依据,也是企业上品种,上质量,上水平,加速产品更新,提高经济效益的技术保证。
在实际生产中,由于零件的生产类型、材料、结构、形状、尺寸和技术要求等不同,针对某一零件,往往不是单独在一种机床上,用某一种加工方法就能完成的,而是要经过一定的工艺过程才能完成其加工。
因此,不仅要根据零件的具体要求,结合现场的具体条件,对零件的各组成表面选择合适的加工方法,还要合理地安排加工顺序,逐步地把零件加工出来。
对于某个具体零件,可采用几种不同的工艺方案进行加工。
虽然这些方案都可以加工出来合格的零件,但从生产效率和经济效益来看,可能其中有种方案比较合理且切实可行。
因此,必须根据零件的具体要求和可能的加工条件等,拟订较为合理的工艺过程。
2.1CA6140车床后托架零件的作用
CA6140车床后托架在卧式机床上,当采用双向引导刀具且有较高的精度要求时,刀具和主轴之间采用浮动卡头连接,在动力头退回原位,刀具又已退离由零件图2.1可得:
CA6140车床后托架是铸造件,从整体夹具刀套的情况下,必须采用托架来支撑刀杆,以防止刀杆产生下垂,保证在下一次刀具循环中,刀具能顺利的重新进入刀套,托架的结构形式同活动模板相似,但其作用仅在于支撑刀杆而不作为是刀具的导向。
托架不起到直
接保证零件的加工精度的作用,但它却间接保证机床能顺利正常的工作。
2.2CA6140车床后托架的结构特点和技术要求
由零件图2.1可得:
CA6140车床后托架是铸造件,从整体形状来看类似长方体。
根据要求主要是加工孔和底平面。
具体特点和技术要求如下:
(1)精加工孔mm,
mm,
mm要求达到的精度等级为。
粗糙度为um,且以底平面为基准,要求平行度公差为,主要满足加工孔的位置精度。
(2)其他各个孔的加工都要以底平面为定位基准。
所以,底平面的形位公差要达到设计要求。
mm、mm粗糙度为mm;
mm为锥孔,且粗糙度为um。
(4)其余未注要求的加工表面为不去除材料加工。
2.3CA6140车床后托架的材料、毛坯和热处理
2.3.1毛坯材料及热处理
毛坯材料:
灰铸铁(HT150),由资料[4]《机械加工工艺手册》表4-71,可得力学性能:
表2.1灰铸铁(HT150)的性能参数
牌号
铸件壁厚
最小抗拉强度
硬度
铸件硬度范围
金相组织
HT150
2.5-10
10-20
20-30
30-50
175
145
130
120
H175
150-200
铁素体+珠光体
灰铸体一般的工作条件:
(1)承受中等载荷的零件。
(2)磨檫面间的单位面积压力不大于490KPa。
毛坯的热处理:
灰铸铁(HT150)中的碳全部或大部分以片状石墨方式存在铸铁中,由于片状石墨对基体的割裂作用大,引起应力集中也大;
因此,使石墨片得到细化,并改善石墨片的分布,可提高铸铁的性能。
可采用石墨化退火,来消除铸铁表层和壁厚较薄的部位可能出现的白口组织(有大量的渗碳体出现),以便于切削加工。
2.3.2毛坯的结构确定
1.毛坯的结构工艺要求:
CA6140车床后托架为铸造件,对毛坯的结构工艺有一定要求:
(1)铸件的壁厚应和合适,均匀,不得有突然变化。
(2)铸造圆角要适当,不得有尖角。
(3)铸件结构要尽量简化,并要有和合理的起模斜度,以减少分型面、芯子、并便于起模。
(4)加强肋的厚度和分布要合理,以免冷却时铸件变形或产生裂纹。
(5)铸件的选材要合理,应有较好的可铸性。
2.毛坯形状、尺寸确定的要求:
设计毛坯形状、尺寸还应考虑到:
(1)各加工面的几何形状应尽量简单。
(2)工艺基准以设计基准相一致。
(3)便于装夹、加工和检查。
(4)结构要素统一,尽量使用普通设备和标准刀具进行加工。
在确定毛坯时,要考虑经济性。
虽然毛坯的形状尺寸与零件接近,可以减少加工余量,提高材料的利用率,降低加工成本,但这样可能导致毛坯制造困难,需要采用昂贵的毛坯制造设备,增加毛坯的制造成本。
因此,毛坯的种类形状及尺寸的确定一定要考虑零件成本的问题但要保证零件的使用性能。
在毛坯的种类、形状及尺寸确定后,必要时可据此绘出毛坯图。
2.4工艺过程设计中应考虑的主要问题
2.4.1加工方法选择的原则
(1)所选加工方法应考虑每种加工方法的经济、精度要求相适应。
(2)所选加工方法能确保加工面的几何形状精度,表面相互位置精度要求。
(3)所选加工方法要与零件材料的可加工性相适应。
(4)加工方法要与生产类型相适应。
(5)所选加工方法企业现有设备条件和工人技术水平相适应。
2.4.2加工阶段的划分
按照加工性质和作用的不同,工艺过程一般可划分为三个加工阶段:
(1)粗加工阶段
粗加工的目的是切去绝大部分多雨的金属,为以后的精加工创造较好的条件,并为半精加工,精加工提供定位基准,粗加工时能及早发现毛坯的缺陷,予以报废或修补,以免浪费工时。
粗加工可采用功率大,刚性好,精度低的机床,选用大的切前用量,以提高生产率、粗加工时,切削力大,切削热量多,所需夹紧力大,使得工件产生的内应力和变形大,所以加工精度低,粗糙度值大。
一般粗加工的公差等级为,粗糙度为um。
(2)半精加工阶段
半精加工阶段是完成一些次要面的加工并为主要表面的精加工做好准备,保证合适的加工余量。
半精加工的公差等级为。
表面粗糙度为um。
(3)精加工阶段
精加工阶段切除剩余的少量加工余量,主要目的是保证零件的形状位置几精度,尺寸精度及表面粗糙度,使各主要表面达到图纸要求.另外精加工工序安排在最后,可防止或减少工件精加工表面损伤。
精加工应采用高精度的机床小的切前用量,工序变形小,有利于提高加工精度.精加工的加工精度一般为,表面粗糙度为um。
(4)光整加工阶段
对某些要求特别高的需进行光整加工,主要用于改善表面质量,对尺度精度改善很少。
一般不能纠正各表面相互位置误差,其精度等级一般为,表面粗糙度为um。
此外,加工阶段划分后,还便于合理的安排热处理工序。
由于热处理性质的不同,有的需安排于粗加工之前,有的需插入粗精加工之间。
2.4.3工序的合理组合
确定加工方法以后,就按生产类型、零件的结构特点、技术要求和机床设备等具体生产条件确定工艺过程的工序数。
确定工序数的基本原则:
(1)工序分散原则
工序内容简单,有利选择最合理的切削用量。
便于采用通用设备。
简单的机床工艺装备。
生产准备工作量少,产品更换容易。
对工人的技术要求水平不高。
但需要设备和工人数量多,生产面积大,工艺路线长,生产管理复杂。
(2)工序集中原则
工序数目少,工件装,夹次数少,缩短了工艺路线,相应减少了操作工人数和生产面积,也简化了生产管理,在一次装夹中同时加工数个表面易于保证这些表面间的相互位置精度。
使用设备少,大量生产可采用高效率的专用机床,以提高生产率。
但采用复杂的专用设备和工艺装备,使成本增高,调整维修费事,生产准备工作量大。
一般情况下,单件小批生产中,为简化生产管理,多将工序适当集中。
但由于不采用专用设备,工序集中程序受到限制。
结构简单的专用机床和工夹具组织流水线生产。
2.4.4加工顺序的安排
零件的加工过程通常包括机械加工工序,热处理工序,以及辅助工序。
在安排加工顺序时常遵循以下原则:
见下表
表2.2加工工序安排原则
工序类别
工序
安排原则
机械加工
1.
对于形状复杂、尺寸较大的毛坯,先安排划线工序,为精基准加工提供找正基准。
2.
按“先基准后其他”的顺序,首先加工精基准面。
3.
在重要表面加工前应对精基准进行修正。
4.
按“先主后次,先粗后精”的顺序。
5.
对于与主要表面有位置精度要求的次要表面应安排在主要表面加工之后加工。
热处理
退火与正火
毛坯预备性热处理,应安排在机械加工之前进行。
时效
为消除残余应力,对于尺寸大结构复杂的铸件,需在粗加工前、后各安排时效处理;
对于一般铸件在铸造后或则粗加工后安排时效处理;
对于精度高的铸件,在半精加工前、后各安排一次时