汽车侧门造型可行性分析.docx
《汽车侧门造型可行性分析.docx》由会员分享,可在线阅读,更多相关《汽车侧门造型可行性分析.docx(22页珍藏版)》请在冰豆网上搜索。
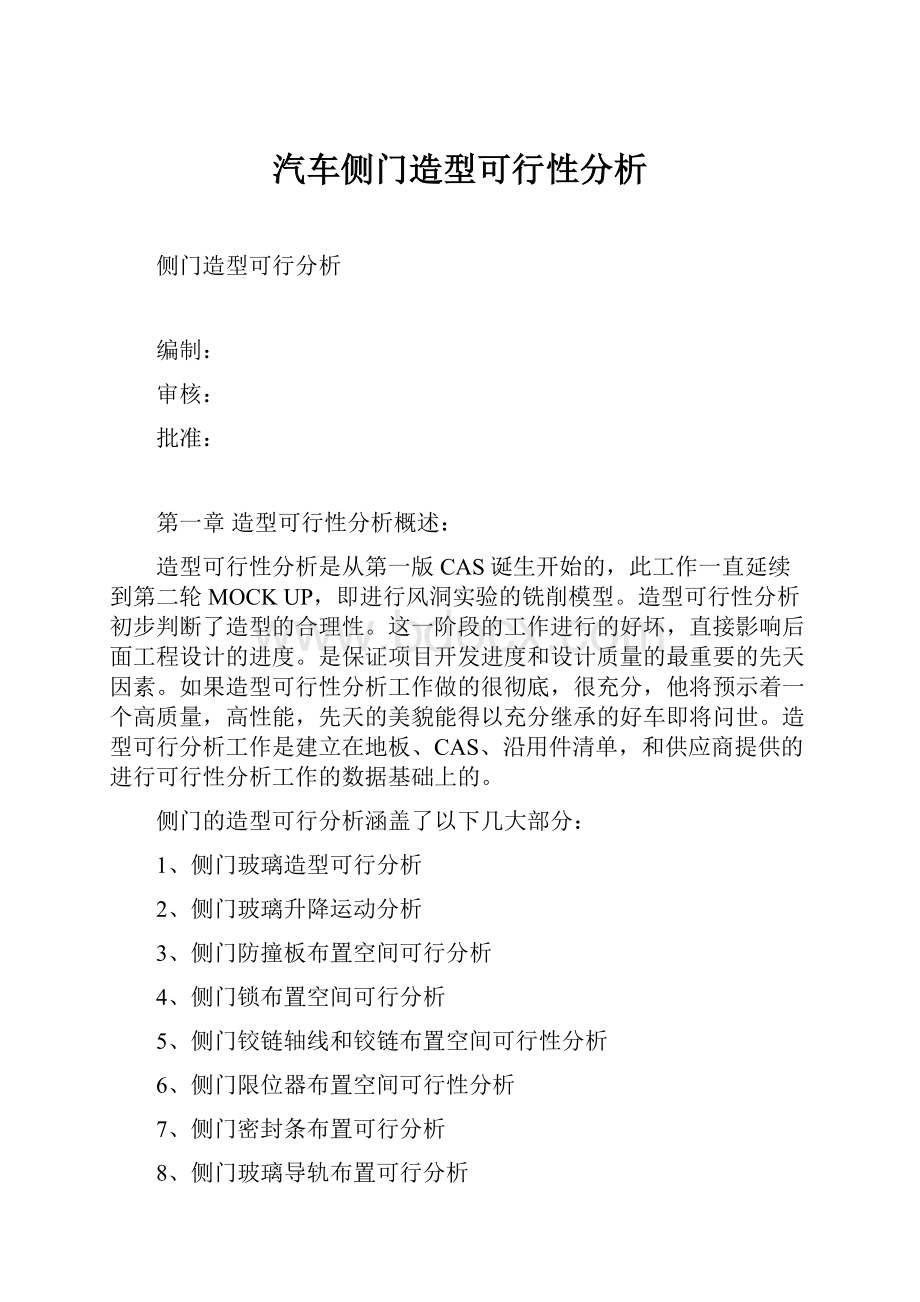
汽车侧门造型可行性分析
侧门造型可行分析
编制:
审核:
批准:
第一章造型可行性分析概述:
造型可行性分析是从第一版CAS诞生开始的,此工作一直延续到第二轮MOCKUP,即进行风洞实验的铣削模型。
造型可行性分析初步判断了造型的合理性。
这一阶段的工作进行的好坏,直接影响后面工程设计的进度。
是保证项目开发进度和设计质量的最重要的先天因素。
如果造型可行性分析工作做的很彻底,很充分,他将预示着一个高质量,高性能,先天的美貌能得以充分继承的好车即将问世。
造型可行分析工作是建立在地板、CAS、沿用件清单,和供应商提供的进行可行性分析工作的数据基础上的。
侧门的造型可行分析涵盖了以下几大部分:
1、侧门玻璃造型可行分析
2、侧门玻璃升降运动分析
3、侧门防撞板布置空间可行分析
4、侧门锁布置空间可行分析
5、侧门铰链轴线和铰链布置空间可行性分析
6、侧门限位器布置空间可行性分析
7、侧门密封条布置可行分析
8、侧门玻璃导轨布置可行分析
9、侧门外开把手布置空间和把手人机工程学分析
10、侧门上下车方便性分析
11、侧门扬声器布置空间分析
12、侧门玻璃升降器布置分析
13、A柱障碍角分析(前门)
14、侧碰性能初步分析
15、侧门分缝线可行性分析(进行车门运动校核,保证运动过程不与周边的件干涉,验证分缝线合理性)
16、设计第一版典型断面分析(初步判断冲压和焊接可行性)
在接下来的章节中,我将详细阐述上面的各项内容。
第二章造型可行性分析的准备工作
要实现一个高质量的造型可行分析,必须满足一定的条件。
我建议,作为项目经理,应该把可行分析工作作为项目开发N多节点中的重中之重。
因为这阶段的准备工作做充分了,可行性分析做好了,将有力的保证以后的项目进度,以后不会浪费钱改造型,不会浪费设计人员无数的工时,不会把先天美貌的车改的越来越丑,而且性能还不能得到保证,最后出来的只能是一个有残疾的,只能远观,不能近看的东西。
下面初步把侧门造型可行性分析要做的准备工作列出来。
侧门造型可行性分析准备工作:
1、初步完成铰链、限位器、玻璃升降器、密封条、玻璃导轨、外开把手供应商的确定。
以便提供初始的数模进行造型可行性分析,在可行分析的过程中将这些部件的大体尺寸,安装位置,空间布置要求确定下来。
以后的详细工程设计中遇到布置空间不够,更改造型的事将大大减少,工作开展难度将大大降低。
笔者认为在此阶段确定这些供应商将事半功倍,同时能大大的吸收各零部件供应商的先进技术。
将大大提高整车技术含量,加大产品的竞争力。
大大增加了产品的附加值。
2、完成详细的沿用件清单,详细的CAD数模并提交给造型部门。
此阶段应完成沿用件的性能评估工作。
尽可能的提高沿用件(包括零件part和部件截面section如玻璃导轨截面,防撞杆截面等)数量。
以降低整车开发成本。
并充分完成沿用件的沿用可行性研究。
3、准备造型要求(Stylingrequirements),提交给造型部门,同时也是为造型可行性分析工作打下基础。
4、完成系统设计概念描述(DCD)和产品技术定义(PTS),如门上框是采用整体外板冲压,还是分体上框采用滚压等定义。
将系统要达到的性能目标,成本设定提交给造型部门。
5、侧门配置表确定(Equipmenttable)。
6、间隙和面差定义(DTS)
第三章侧门布置详细可行性分析
玻璃成型性分析
对于侧门玻璃在保证造型的同时,还必须保证玻璃的成型性,当CAS出来后这项工作就应该完成,越早确定玻璃的曲率越好。
分析时分别测量玻璃横向的曲率半径和纵向的弦高。
一般要求玻璃的曲率半径大于1200。
如图所示:
A0侧门玻璃曲率(和M11一样)
同时要保证玻璃的轴线和BELT-LINE平行。
玻璃升降运动模拟
玻璃边界:
从外观造型上看应校核玻璃沿B柱的一条边和后视镜安装的面的边、后三角窗的前边缘必须平行,这样玻璃运动才能进行。
•PARELLELTOB-PILLAR
-EDGELINEOFOUTSIDEMIRROR(b)
-EDGELINEOFPATCH-RRDOORORDIVISIONBAR
同时A柱处后视镜后边沿b与Z向的夹角不能小于12°,因为如果倾角越大,当玻璃下降时就越容易撞到门内板,就很难保证玻璃残余于BELT-LINE以上的距离。
一般情况下,我们要求前门玻璃完全下降后玻璃残余在BELT-LINE以上的距离小于3mm,甚至完全下降。
这样能保证驾驶员在驾驶的过程,当把手臂靠在窗台上时,门玻璃不会撑住手臂难受,毕竟玻璃的厚度只有3.2mm。
一般高档的车,都对此距离要求很高,后门玻璃由于受到后轮包络的影响,一般很难完全下降,一般残留在BELT-LINE以上的距离在120mm左右是比较合理的。
当CAS出来后,这时应通知供应商,让他们根据初版的CAS设计升降器,将这个很粗的数模布置在此空间,看空间位置上有没有干涉,玻璃升降器一般很容易和门锁、限位器和内饰护板干涉。
如果与内饰护板干涉则需修改内饰护板造型。
顺便注意一下,对于同一个系列同时开发的几款车,如A0系列,S18系列,B25系列等。
应保证b与Z的夹角的一样,如果前期没有注意,那样将导致开发几个后视镜支座,大大提高了开发成本。
本来开发一个支座就可以用在整个系列上了。
构建玻璃升降运动模型:
1、根据造型提供的玻璃大面。
从大面上截取一个和侧窗尺寸差不多的玻璃小面,分别取A,B柱的棱边模拟玻璃的导轨,此两棱边位于玻璃大面上。
以任意一个棱边拟合一个圆作为玻璃导轨。
得到一个part1.
2、在玻璃小面上两个棱边上做三个点,两个点位于同一个棱边上且这两个点位于拟合的大圆上,一个点位于另一个棱边上且此点位于玻璃大面上。
得到part2
3、将这两个part装在一起,进入DMU模块。
分别进行两个点在线上约束和点在面上的约束:
4、这样即可完成玻璃的升降运动模拟。
这时我们根据残留与BELT-LINE以上的最小玻璃距离要求,就可以把玻璃降到最低位置。
这时检查玻璃在运动过程中与周边件的距离,我们要求两个运动件间的最小距离为10mm。
一个动件和一个不动件的最小距离为6mm,两个不动件间的最小距离为3mm.
防撞板或防撞杆的布置分析
侧门防撞板的布置受到B-R-LINE的影响,B-R-LINE太靠近分缝线,一方面,侧碰性能很难保证,一方面,将导致防撞板无安装和焊接空间。
所以在造型可研阶段就应该把可行性做足了,因为如果防撞板焊接空间不够,将导致修改造型分缝线。
如果在造型还没有冻结之前解决,修改造型分缝线是非常简单的。
上图为A0车由于防撞板焊接空间不足,修改了造型分缝线。
分析防撞板的布置空间我们主要是通过根据CAS表面和B-R-LINE这两个初始条件设计一个典型断面是方法来判断的,上面的一张图片就是通过CAS和B-R-LINE两个初始条件来设计了一个典型断面。
为了保证足够的焊接空间和工艺空间,我们需要造型部门将分缝线后移7mm。
一般情况下要求安装面处有14mm的焊接空间,同时要考虑工艺性,预留3~5mm的工艺空间,所以在防撞板安装处必须有17~19mm的平面空间。
对侧门防撞板,前门一般是前高后低斜着布置,且防撞板的中心线投影到人体中心线的纵向平面上应该通过H点,这样防撞板或防撞杆在侧碰时能起很好的效果。
前门防撞板的后端,应尽量位于B柱强度最大处(B柱根部强度最强),后门防撞板或防撞杆一般采用前低后高斜着布置,前端也应尽量靠B柱最强处。
同时根据FMVSS214要求侧门在受到挤压时,侵入量不能太大,这样的话防撞板或防撞杆位于碰撞器的中间位置所起的作用是较为理想的。
我们必须协调这些要求,找出防撞板或防撞杆的最佳位置。
对于防撞板前端的安装面和焊接空间常常受到铰链、限位器和线束过孔安装空间的约束,所以前端的安装面必须合理调整这些安装空间,找出合理的防撞板焊接面安装空间。
为了使防撞板在侧碰时迅速起作用,所以防撞板应尽量靠近门外板,一般防撞板距离门外板的间距为3~7mm。
侧门锁布置可行性分析
侧门锁布置时,我们要求侧门锁在绕铰链轴线旋转到关闭状态时,在锁体与锁扣啮合处,该处圆的切线应保证和锁柱垂直。
当得到此位置后,我们需要校核锁与玻璃升降导轨和玻璃的在此处的间隙,保证锁与玻璃升降导轨或玻璃有至少15mm距离。
同时保证门上锁安装面距分缝线的距离(为了获得足够的工艺空间)。
在布置锁时为了获得锁安装的足够空间,有时需要更改造型,改变侧门玻璃的形状、改变A、B、C柱的倾角,改变造型分缝线等等,下图是预留工艺空间的参考。
锁拉杆拉线的布置:
锁拉杆拉线布置时,应尽量让拉杆拉线从玻璃的内侧走,因为拉杆拉线需要与内开把手相连。
这样的话,为了防止锁拉线拉杆在玻璃升降过程中被玻璃撞到使门自动打开,车在行驶过程中产生风险,需要所有的拉杆拉线与玻璃有至少15mm的间隙。
同时锁布置时,让锁位于上下铰链的中间位置,这样锁、上下铰链形成三点,从而有效的保证了门的稳定性。
同时锁尽量不要进入FMVSS214,C-NCAP,EU-NCAP,US-NCAP,IIHS的碰撞器区域。
因为锁是一个功能件,一定要保证侧碰过程中门不能打开。
所以尽量让锁避开侧碰区域,对锁是有好处的。
由于锁的布置空间是受到造型严重影响的,所以在造型阶段就应该有锁很粗的外部轮廓尺寸的3D数模了。
如果锁是沿用件,则没必要让供应商参与可行性分析,如果锁是新开发件,则供应商应该在这之前就确定了,并让他们参与到这个阶段的锁布置可行性分析中来。
这样一方面我们可以做到集思广益,能够充分的应用锁零部件这一领域的先进技术,因为在这一阶段,布置空间对锁的限制条件很少,大多是可以通过调整造型来完成的。
对利用新技术的是非常有利。
铰链轴线和铰链布置可行性分析
在布置铰链轴线时,为了保证车门有自动关闭的趋势,所以要求铰链轴线在YZ平面向车内倾斜0~2°,在XZ平面内向车后倾斜0~2°。
铰链轴线布置时,铰链轴线越靠车门前方和车门外板,对车门运动过程中的间隙越有利。
门的侵入量越小,对侧围强度的影响就越小,对提高整车安全性和防止门下垂就越好。
通过下图我们可以清晰的看到铰链轴线对侧围强度的影响:
上图中铰链轴线非常靠车门前端和车门外侧(蓝色示意图)是时候,车门与翼子板的间隙是越来越大,门与翼子板或周边件的干涉的可能性越来越小。
距离侧围的越来越远,侧围的强度得到了很大的提高,改善了侧碰安全性。
铰链轴线的校核方法:
韩国人的校核方法是将门向车外(PF认为没有必要)和车前各移动1mm,然后做门的旋转运动,要保证门与周边件的间隙最小为0.5mm.,现在A0系列车型是结合PF和CES的方法校核的。
在铰链轴线布置好之后,我们应将铰链3D数模布置到CAS数据中,上下铰链距离越大越好,一般上下铰链间距要求大于门沿X向最长长度的1/3.。
铰链布置好之后,我们应考虑工具过孔和铰链安装面的空间。
要求有足够的安装空间,工具与周边件的间隙大于3mm。
铰链的安装面是要考虑沿用件的限制的,A0是沿用M14的前挡板,前期造型可行性分析不足,导致现在前门的铰链安装面空间严重影响工具过孔空间,不得不开发了一种新的弯头工具来安装铰链,大大提高了开发成本。
如果前期可行性做足了,通过调整B-R-LINE和PARTINGLINE就可以解决此问题,达到我们想要的结果。
铰链轴线和铰链的布置是一个非常庞大的工程,其涉及的周边条件非常多,造型对其的布置影响非常大,所以前期造型未冻结前,应充分把这个问题考虑透了。
侧门限位器布置可行性分析
限位器布置时,要考虑其与周边件的关系,玻璃、导轨、线束,防撞板直接影响着限位器的布置,一般要求限位器与玻璃的间隙在15mm左右,最小10mm。
与防撞板、导轨、线束的距离10mm。
限位器一般布置上下铰链的中间位置,限位器轴线越靠近B-R-LINE,对限位器布置越有利。
当我们把限位器旋转点确定后,限位盒的旋转中心一般距离限位器旋转中心在33~35mm。
具体限位器模拟我就不在这做阐述了。
下图是限位器造型线模拟图:
限位臂造型中心线
限位器轴线
铰链轴线
密封条、玻璃导轨布置和A柱障碍角可行性分析
密封条道数是根据整车级别和舒适性来决定的,在整车PTS中已经有了要求。
在造型可行性分析阶段就是要找到足够的空间,保证达到整车设定的要求。
如:
是采用两道还是一道密封,密封条布置门上还是侧围上。
侧门上框玻璃尼槽的结构形式等等。
这个阶段都必须分析确定完成。
曾经S12在造型阶段只分析布置的门洞上密封条的可行性,但后面要出口美国,提高舒适性,需要在门上在加第二道密封。
此时由于造型可行性分析的时候没考虑,导致后面密封条在门上卡槽没有安装空间,与玻璃导轨干涉,后面不得不对造型做改动。
对于玻璃尼槽它的结构形式对A柱障碍角有着直接或间接的影响。
前期我们可以通过输入密封条截面和玻璃导轨截面,判断空间是否足够。
从图中我们可以看到造型分缝线太靠前导致玻璃导轨布置空间不足,所以必须修改造型,使分缝线后移
玻璃导轨
玻璃升降器、扬声器的布置
门内板上要给玻璃升降器、扬声器留出安装面,同时又要保证安装过孔和工具过孔,空间相当的紧张,合理的分缝线和B-R-LINE将是保证这些部件得到合理布置的基础。
前期就应该要求供应商根据CAS面提供初版的3D玻璃升降器数模,和扬声器(可能是沿用件)进行空间布置分析。
侧门外开把手布置空间和人机工程学分析
在CAS数据出来后,我们应马上要求供应商提供初版轮廓尺寸的外把手3D数模,进行把手空间布置。
(把手3D可以考虑沿用已有车型的把手)。
如果前期不校核,把手离门分缝线太近,将导致把手布置不下,把手内部的部件凸出与门钣金轮廓。
同时把手布置空间不能将BELT-LINE外加强板大大削弱。
否则将影响整车碰撞安全性能和门的刚度和强度。
外把手布置时,当把手绕把手旋转轴转动35~45°时,外开把手不能与CAS干涉。
把手转到极限位置
把手边缘距离分缝线的参考数据:
把手人机工程学:
把手的高度,需要从人机工程的角度出发,考虑开门时的舒适性,所以把手不能太高也不能太低。
一般要求侧门外开把手的高度为900~920(距离地面线)。
造型时还必须考虑把手空间。
尺寸参考下图:
topview
sideview
上下车方便性分析
上下车方便性尤其受到下面空间尺寸的影响,如图所示:
下面是一些BENCHBMARK的L18和L19参考尺寸:
ThedimensionL18andL19inSAE
同时在造型可行性分析阶段,我必须校核座椅的R点是否位于B-R-LINE之前,R点位于B-R-LINE之前有利于上下车方便性。
做这个修改将影响到侧门的造型分缝线。
侧碰性能初步分析
在造型可行性分析阶段,当CAS和B-R-LINE出来后,我就可以初步判断整车的碰撞性能,以及今后结构设计,性能提升的空间。
在造型可行性分析中,我们必须尽量确保有足够大截面的B柱,B柱的截面大小受到B-R-LINE的影响,B-R-LINE又影响门的造型分缝线。
通过综合分析我们应尽量获取最大限度的B柱截面。
在门槛处,我们尽量让造型给门和门槛留有足够大重叠量,提高侧碰性能。
在C柱位置,我们也应尽量让门与侧围的重叠量尽量大。
一般要求门与侧围重叠量大于60mm。
设计第一版典型截面
CAS出来后,我们根据B-R-LINE设计典型截面开始分析布置空间,工艺可行性,侧碰性能等等。
全车一般有35~40个截面。
是我们初步判断造型可行性必不可少的手段。
具体分布位置如图所示。
sideview
rearandfrontview
topview
上图中所有典型截面,是造型可行截面必须设计的典型截面。
他们对整车以后的结构设计有着巨大的这道作用。