渗碳件常见缺陷与对策之欧阳化创编.docx
《渗碳件常见缺陷与对策之欧阳化创编.docx》由会员分享,可在线阅读,更多相关《渗碳件常见缺陷与对策之欧阳化创编.docx(10页珍藏版)》请在冰豆网上搜索。
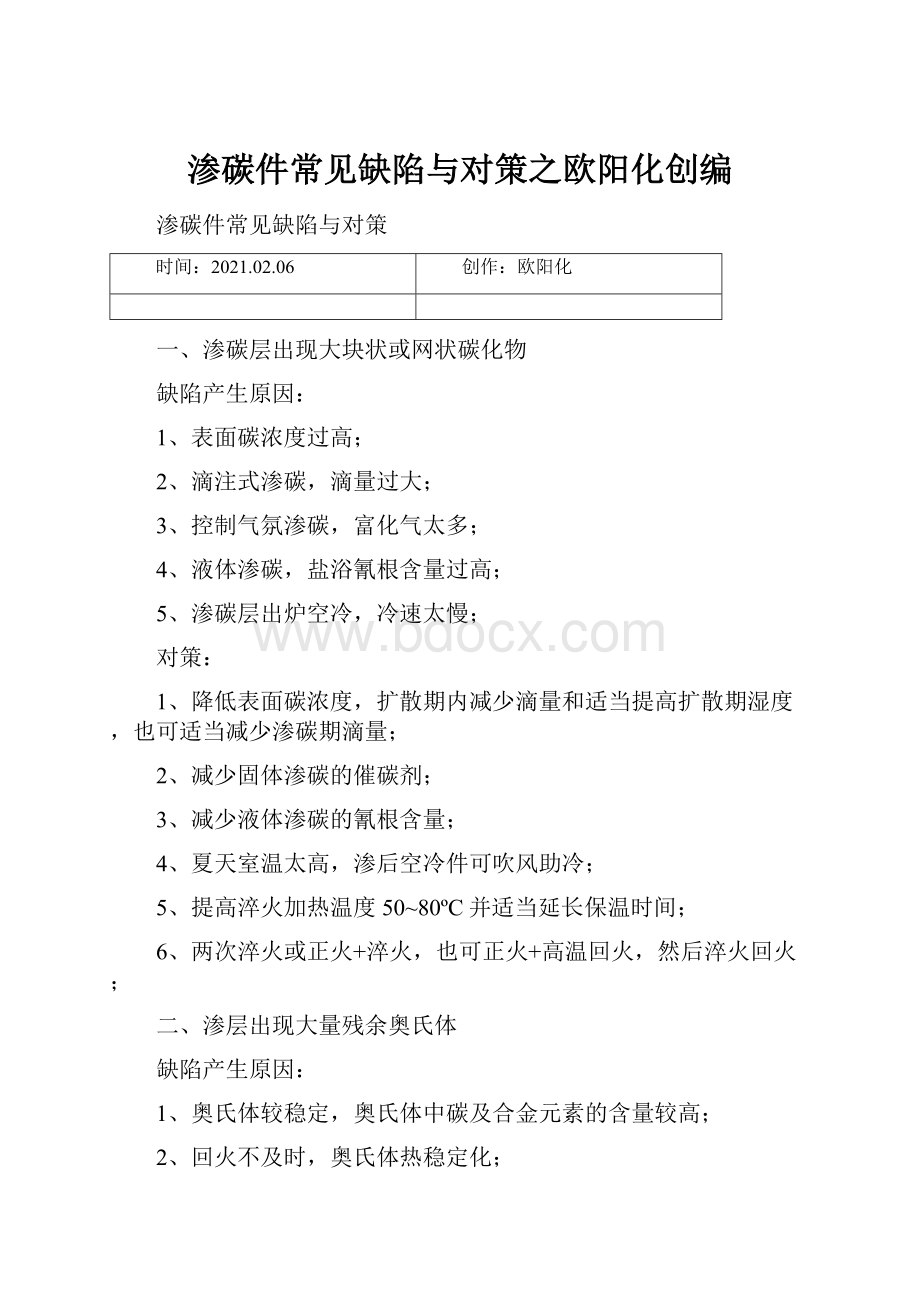
渗碳件常见缺陷与对策之欧阳化创编
渗碳件常见缺陷与对策
时间:
2021.02.06
创作:
欧阳化
一、渗碳层出现大块状或网状碳化物
缺陷产生原因:
1、表面碳浓度过高;
2、滴注式渗碳,滴量过大;
3、控制气氛渗碳,富化气太多;
4、液体渗碳,盐浴氰根含量过高;
5、渗碳层出炉空冷,冷速太慢;
对策:
1、降低表面碳浓度,扩散期内减少滴量和适当提高扩散期湿度,也可适当减少渗碳期滴量;
2、减少固体渗碳的催碳剂;
3、减少液体渗碳的氰根含量;
4、夏天室温太高,渗后空冷件可吹风助冷;
5、提高淬火加热温度50~80ºC并适当延长保温时间;
6、两次淬火或正火+淬火,也可正火+高温回火,然后淬火回火;
二、渗层出现大量残余奥氏体
缺陷产生原因:
1、奥氏体较稳定,奥氏体中碳及合金元素的含量较高;
2、回火不及时,奥氏体热稳定化;
3、回火后冷却太慢;
对策:
1、表面碳浓度不宜太高;
2、降低直接淬火或重新加热淬火温度,控制心部铁素体的级别≤3级;
3、低温回火后快冷;
4、可以重新加热淬火,冷处理,也可高温回火后重新淬火;
三、表面脱碳
缺陷产生原因:
1、气体渗碳后期,炉气碳势低;
2、固体渗碳后,冷却速度过慢;
3、渗碳后空冷时间过长;
4、在冷却井中无保护冷却;
5、空气炉加热淬火无保护气体;
6、盐浴炉加热淬火,盐浴脱氧不彻底;
对策:
1、在碳势适宜的介质中补渗;
2、淬火后作喷丸处理;
3、磨削余量,较大件允许有一定脱碳层(≤0.02mm);
四、渗碳层淬火后出现屈氏体组织(黑色组织)
缺陷产生原因:
渗碳介质中含氧量较高:
氧扩散到晶界形成Cr、Mn、Si的氧化物,使合金元素贫化,使淬透性降低。
对策:
1、控制炉气介质成分,降低含氧量;
2、用喷丸可以进行补救;
3、提高淬火介质冷却能力;
五、心部铁素体过多,使硬度不足
缺陷产生原因:
1、淬火温度低;
2、重新加热淬火保温时间不足,淬火冷速不够;
3、心部有未溶铁素体;
4、心部有奥氏体分解产物;
对策:
1、按正常工艺重新加热淬火;
2、适当提高淬火温度延长保温时间;
六、渗碳层深度不足
缺陷产生原因:
1、炉温低、保温时间短;
2、渗剂浓度低;
3、炉子漏气;
4、盐浴渗碳成分不正常;
5、装炉量过多;
6、工件表面有氧化皮或积炭;
对策:
1、针对原因,调整渗碳温度、时间、滴量及炉子的密封性;
2、加强新盐鉴定及工作状况的检查;
3、零件应该清理干净;
4、渗层过薄,可以补渗,补渗的速度是正常渗碳的1/2,约为0.1mm/h左右;
七、渗层深度不均匀
缺陷产生原因:
1、炉温不均匀;
2、炉内气氛循环不良;
3、炭黑在表面沉积;
4、固体渗碳箱内温差大及催渗剂不均匀;
5、零件表面有锈斑、油污等;
6、零件表面粗糙度不一致;
7、零件吊挂疏密不均;
8、原材料有带状组织;
对策:
1、渗碳前严格清洗零件;
2、清理炉内积炭;
3、零件装夹时应均匀分布间隙大小相等;
4、经常检查炉温均匀性;
5、原材料不得有带状组织;
6、经常检查炉温、炉气及装炉情况;
八、表面硬度低
缺陷产生原因:
1、表面碳浓度低;
2、表面残余奥氏体多;
3、表面形成屈氏体组织;
4、淬火温度高,溶入奥氏体碳量多,淬火后形成大量残余奥氏体;
5、淬火加热温度低,溶入奥氏体的碳量不够,淬火马氏体含碳低;
6、回火温度过高;
对策:
1、碳浓度低,可以补渗;
2、残余奥氏体多,可高温回火后再加热淬火;
3、有托氏体组织,可以重新加热淬火;
4、严格热处理工艺纪律;
九、表面腐蚀和氧化
缺陷产生原因:
1、渗剂不纯有水、硫和硫酸盐;
2、气体渗碳炉漏气固体渗碳时催渗剂在工件表面融化,液体渗碳后,工件表面粘有残盐;
3、高温出炉,空冷保护不够;
4、盐炉校正不彻底,空气炉无保护气氛加热,淬火后不及时清洗;
5、零件表面不清洁;
对策:
1、严格控制渗碳剂及盐浴成分;
2、经常检查设备密封情况;
3、对零件表面及时清理和清洗;
4、严格执行工艺纪律;
十、渗碳件开裂
缺陷产生原因:
1、冷却速度过慢,组织转变不均匀;
2、合金钢渗后空冷,在表层托氏体下面保留一层未转变奥氏体在随后冷却或室温放置时,转变成马氏体,比容加大,出现拉应力;
3、第一次淬火时,冷却速度太快或工件形状复杂;
4、材质含提高淬透性的微量元素(Mo、B)太多等;
对策:
1、渗后减慢冷却速度,使渗层在冷却过程中完全共析转变;
2、渗后加快冷却速度,得到马氏体+残余奥氏体。
松弛内层组织转变产生的拉应力;
3、淬火开裂应减慢冷却速度、含微量元素作工艺试验,或提高淬火介质温度;
十一、高合金钢氢脆
缺陷产生原因:
1、炉气中含氢太高;
2、渗碳温度太高利于氢扩散;
3、渗后直接淬火,氢来不及析出以过饱和状态存在于钢中;
对策:
1、渗碳后缓慢冷却;
2、直接淬火后,迅速在250ºC以上回火;
3、零件出炉前停止供给渗剂,通入氮气排氢后,直接淬火;
十二、渗层碳浓度低
缺陷产生原因:
1、炉内碳势低,温度低,滴量少,炉子漏气;
2、工件表面形成碳黑或被炭黑覆盖,装炉量太多;
3、炉子气氛不均匀,炉压太低,使炉子局部造成死角;
4、工件间距离太小,炉子循环不畅;
5、渗后冷却时脱碳;
对策:
1、渗碳时,经常检查炉温、渗剂滴量;
2、注意炉气、炉压;
3、防止炉子漏气和风扇停转、反转;
4、工件之间距离大于1cn;
5、经常烧碳黑,清理炉内积炭,渗后入冷却井冷却,在井中倒煤油或甲醇保护;
十三、渗碳层过厚
缺陷产生原因:
1、渗碳温度太高,保温时间太长;
2、滴量过大,炉内碳势高;
3、试样检验不准;
对策:
1、针对原因,采取工艺措施;
2、渗层超过图样上限要求,不合格,但与图样规定相差0.05mm时,可以仲裁合格或申请回用;
十四、渗碳件畸变过量
缺陷产生原因:
1、渗碳时装炉方法或夹具选择不当;
2、渗碳温度太高,炉气、炉压不均和不稳定;
3、直接淬火温度过高;
4、不适当安排两次淬火;
5、加热方式不当,淬火剂及冷却方式不当;
6、淬火返修次数太多;
7、零件上渗碳层的浓度和深度不均匀,淬火时造成无规则翘曲;
8、工件形状复杂,壁厚不均匀,有的面渗碳,有的面不渗碳或少渗碳;
对策:
1、长杆状件应垂直吊放,平板零件要平放,零件在夹具上要平稳不能受预应力,出炉操作要平稳、炉温要适当;
2、直接淬火应预冷,尽量用一次淬火代替二次淬火,正确选择热处理工艺;
3、预先留出机加工余量;
十五、渗碳速度很慢
缺陷产生原因:
1、温度过低;
2、渗剂太多,零件表面积炭;
3、渗剂含硫量过多;
4、风扇轴承用MoS2润滑,润滑油进入炉内,使硫增加;
5、风扇轴承漏气、氧气进入炉中;
6、风扇轴冷却水渗漏入炉;
对策
针对缺陷采取相应措施。
十六、渗碳件淬火后表面剥落
缺陷产生原因:
1、固体渗碳剂活性过分强烈;
2、渗碳温度过高,大量碳原子渗入工件表面来不及扩散,过渡不好形成表面碳浓度过高;
对策:
1、将高碳势件在保护气氛中(碳势(体积分数)为0.8%)加热2~4h,以减少表面碳浓度;
2、也可将此件在质量分数为3%~5%的苏打和木炭中加热至920~940ºC,保温2~4h,以减少表面碳浓度;
十七、零件上出现玻璃状凸瘤
缺陷产生原因:
1、固体渗碳时,渗碳中由于SiO2质量分数2%以上所致;
2、SiO2高温和Na2CO3作用,生成玻璃状物质粘附在工件表面,形成凸瘤;
对策:
1、固体渗碳时,渗剂应纯净;
2、旧渗碳剂彻底筛去尘埃;
3、去除渗剂中砂石及封口用耐火粘土;
十八、渗碳件出现反常组织(游离铁素体,游离渗碳体或网状铁素体在二次渗碳体周围)
缺陷产生原因:
1、钢中和渗碳介质中含氧量过高所致,使淬火时出现软点使耐磨性降低;
2、渗碳剂应干燥去水分;
对策:
1、适当提高淬火温度延长保温时间,使组织均匀化;
2、选用淬火烈度大的淬火介质;
十九、过热
缺陷产生原因:
1、渗碳时过势或淬火加热时过势,使晶粒长大,脆性增加;
2、渗碳时过势,不但表层含碳量增加,同时碳化物也增加,出现莱氏体;
对策:
1、采用正火,使晶粒细化;
2、盐炉加热淬火,工件不能紧靠电极;
3、检查仪表是否失灵;
时间:
2021.02.06
创作:
欧阳化