小油壶盖注塑模设计说明书.docx
《小油壶盖注塑模设计说明书.docx》由会员分享,可在线阅读,更多相关《小油壶盖注塑模设计说明书.docx(19页珍藏版)》请在冰豆网上搜索。
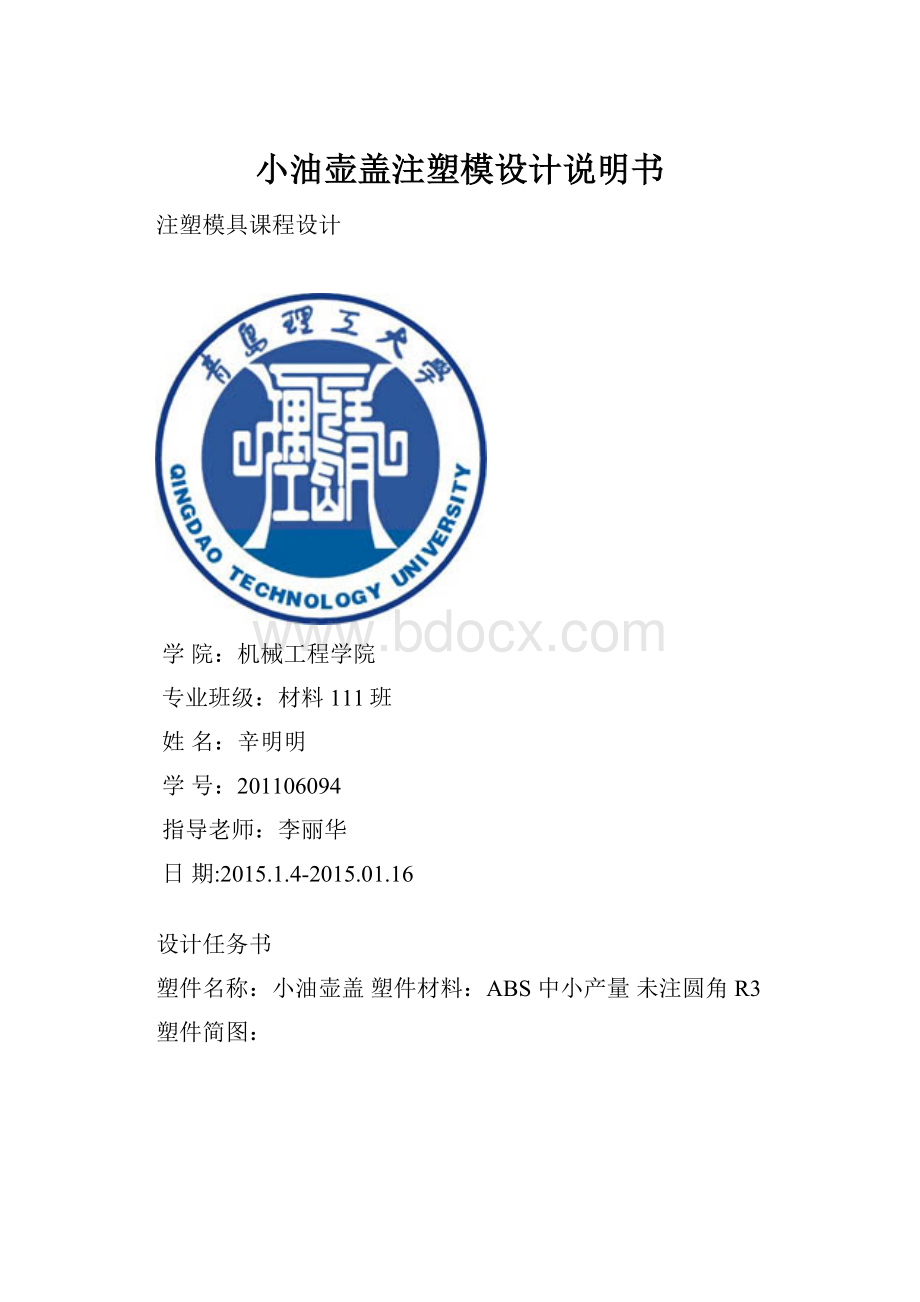
小油壶盖注塑模设计说明书
注塑模具课程设计
学院:
机械工程学院
专业班级:
材料111班
姓名:
辛明明
学号:
201106094
指导老师:
李丽华
日期:
2015.1.4-2015.01.16
设计任务书
塑件名称:
小油壶盖塑件材料:
ABS中小产量未注圆角R3
塑件简图:
在设计之前,学生已具备机械制图、公差与技术测量、机械原理及零件、模具材料及热处理、模具制造工艺、塑料成型工艺及模具设计等方面必要的基础知识和专业知识,并已通过金工和生产实习。
做过注射成型实验:
韧步了解塑料的成型工艺和生产过程,熟悉多种塑料模具的典型结构。
课程设计的内容包括:
(1)独立拟定塑件的成型工艺,正确选用成型设备。
(2)合理地选择模具结构。
根据塑件图的技术要求,提出模具结构方案,并使之结构合理,质量可靠,操作方便。
必要时可根据模具设计和制造的要求提出修改塑件图纸的意见,但必须征得设计者或用户同意后方可实施。
(3)正确地确定模具成型零件的结构形状、尺寸及其技术要求。
(4)所设计的模具应当制造工艺性良好,造价便宜。
(5)充分利用塑料成型优良的特点,尽量减少后加工。
(6)设计的模具应当能高效、优质、安全可靠地生产,且模具使用寿命长。
第1章塑件成型工艺性分析
1.1塑件结构特征分析………………………………………………………4
1.2ABS塑料的性能分析………………………………………………………4
1.3成型工艺过程及参数………………………………………………………4
1.4塑件分型面位置的分析和确定……………………………………………5
1.5塑件型腔数量及排列方式的确定……………………………………………5
第2章注射机的选择及工艺参数的校核
2.1注射量的计算………………………………………………………7
2.2选择注射机………………………………………………………7
2.3注射机参数的校核………………………………………………………7
第3章浇注系统的形式选择和截面尺寸的计算
3.1主流道的设计………………………………………………………8
3.2分流道的设计………………………………………………………8
3.3浇口的设计………………………………………………………9
3.4冷料穴和拉料杆的设计………………………………………………………9
第4章成型零件设计及力学计算
4.1凹模的结构设计及尺寸计算……………………………………………10
4.2凸模的结构设计及尺寸计算……………………………………………10
4.3成型零件钢材的选用……………………………………………10
4.4推出方式的确定……………………………………………10
4.4模架的选取……………………………………………11
第5章冷却系统的设计
5.1冷却介质……………………………………………………12
5.2冷却系统的计算……………………………………………………12设计总结……………………………………………………14
第1章塑件成型工艺性分析
1.1塑件结构特征分析
1.1.1外形尺寸:
该塑件壁厚为3mm,塑件外形尺寸不大,塑料熔体流程不太长,适合于注射成型。
1.1.2精度等级:
未注尺寸按等级公差MT7计算,并对尺寸按入体原则标注。
1.1.3脱模斜度:
凸、凹模斜度均取
1.2ABS塑料的性能分析
1.2.1优点:
(1)综合性能较好、冲击强度较高、化学稳定性、电性能良好。
ABS塑胶制品。
(2)与有机玻璃的熔接性良好、制成双色塑件、且可表面镀铬、喷漆处理。
(3)有高抗冲、高耐热、阻燃、增强、透明等级别。
(4)流动性比HIPS差一点、比PMMA、PC塑胶原料等好、柔韧性好。
(5)ABS塑料具有优良的综合性能,有极好的冲击强度、尺寸稳定性好、电
能、耐磨性、抗化学药品性、染色性,成型加工和机械加工较好。
(6)ABS树脂耐水、无机盐、碱和酸类,不溶于大部分醇类和烃类溶剂,而容易溶于醛、酮、酯和某些氯代烃中。
1.2.2缺点:
热变形温度较低,可燃,耐候性比较差。
ABS塑胶原料注塑工艺ABS的流动性介于PS与PC之间,其流动性与注射温度和压力都有关系,其中注射压力的影响稍大,因此成型时常采用较高的注射压力以降低熔体粘度,提高充模性能。
塑料的处理ABS的吸水率大约为0.2%-0.8%,对于一般级别的ABS,加工前用烘箱以80-85℃烘2-4小时或用干燥料斗以80℃烘1-2小时。
对于含PC组份的耐热级ABS,烘干温度适当调高至100℃,具体烘干时间可用对空挤出来确定。
1.2.3指标:
无毒、无味,外观呈象牙色半透明,或透明颗粒或粉状。
密度为:
1.05—1.18g/cm3
收缩率:
0.4%—0.9%
弹性模量值为0.2Gpa
泊松比为0.394
吸湿性<1%
熔融温度217-237℃。
热分解温度>250℃。
1.3成型工艺过程及参数
1.3.1注射成型过程:
(1)成型前的准备:
对ABS的色泽、粒度和均匀度等进行检验。
进行干燥和预热,控制水分在0.3%以下。
(2)注射过程:
塑件在注射机料筒内经过加热、塑化达到流动状态后,由模具的浇注系统进入模具型腔成型,其过程可分为冲模、压实、保压、倒流和冷却五个阶段。
(3)塑件的后处理:
塑件成型后要进行退火处理。
1.3.2注射成型的工艺参数
注射机:
螺杆式
螺杆转速/(r.min-1):
30—60;
料筒温度(
):
前段200—210;
中段210—230;
后段180—200;
喷嘴温度(
):
180—190直通式
模具温度(
):
50—70;
注射压力(MPa):
70—90;
保压压力(MPa):
50—70;
成型时间(s):
注射时间3—5;
保压时间15—30;
冷却时间15—30;
成型周期40—70;
1.4塑件分型面位置的分析和确定
通过对塑件结构形式的分析,分型面应选在端盖截面积最大且利于开模取
件的底平面上,其位置如下图所示。
1.5塑件型腔数量及排列方式的确定
1.5.1型腔数目的确定
塑件结构简单,根据用途推测批量较大,故采用一模四腔结构形式。
1.5.2排列方式的确定
考虑到塑件自动脱螺纹,所以采用一模四腔,平衡布置,两行两列矩形排布。
这样模具尺寸较小,制造加工方便,生产效率较高,塑件成本较低。
第2章注射机的选择及工艺参数的校核
2.1注射量的计算:
2.1.1塑件的体积:
15.134cm3
2.1.2浇注系统凝料体积:
浇注系统的凝料可以根据经验值计算,一般取塑件体积的0.2—1倍。
此次选取塑件体积的0.5倍。
V浇=7.567cm3
一次注入模具型腔熔料的总体积为:
V总=(15.134+7.567)×4=90.804cm3
2.2选择注射机:
根据V总=90.804cm3,根据公式V公=V总/0.8=113.505cm3
初步选择额定注射量为125cm3的螺杆式注射机。
型号为:
XS-ZY-125
理论注射容量/cm3
125
最大成型面积/cm2
320
螺杆直径/mm
42
最大开合模行程/mm
300
注射压力/MPa
120
模具最大厚度/mm
300
注射行程/mm
115
模具最小厚度/mm
200
注射方式
螺杆式
喷嘴圆弧半径/mm
12
锁模力/kN
900
喷嘴孔直径/mm
4
2.3注射机参数的校核
2.3.1锁模力的校核:
(nA1+Aj)≤Fn
878.99KN≤900KN符合要求。
2.3.2模具与注射机安装部分相关尺寸的校核:
浇口套球面尺寸:
浇口套内主流道始端的球面必须比注射机喷嘴头部球面半径略大一些。
取SR=14mm
第3章浇注系统的形式选择和截面尺寸的计算
3.1主流道的设计
主流道通常位于模具中心塑料熔体的入口处,它将注射喷嘴注射
的熔体导入分流道或型腔中。
主流道的形状为圆锥形,以便熔体的流动和开模是主流道凝料的顺利拔出。
主流道的尺寸直接影响到熔体的流动速度和冲模时间。
另外,由于其与高温塑料熔体及注射机喷嘴反复接触,因此设计中常设计成可拆卸更换的浇口套。
3.1.1主流道的尺寸:
(1)主流道的长度:
小型模具
应尽量小于60mm,本次设计中取50mm进行设计。
(2)主流道小端直径:
d=注射机喷嘴尺寸+(0.5~1)mm=(4+1)mm=5mm
(3)主流道大端直径:
8.5mm,式中
(4)主流道球面半径:
=注射机喷嘴球头半径+(1~2)mm=(12+2)mm=14mm。
(5)球面配合高度:
h=3mm~5mm,取h=3mm。
(6)主流道的平均半径:
3.1.2主流道浇口套:
主流道小端入口处与注射机喷嘴反复接触,易磨损。
对材料的要求严格,因而尽管小型注射模可以将主流道浇口套与定位圈设计成一个整体,但考虑上述因素通常仍然将其分开来设计,以便于拆卸更换。
同时也便于选用优质钢材进行单独加工和热处理。
设计中常采用碳素工具钢(T8A或T10A),热处理淬火表面硬度为53~57HRC。
3.1.3主流道的凝料体积:
3.2分流道的设计
3.2.1单边分流道的长度:
由于塑件较小,所以取单边分流道的长度为L=40mm。
3.2.2分流道的形状与尺寸:
常用分流道形式有圆形、梯形、U形、半圆形及矩形等几种形式,U形分
流道加工较容易,且热量损失与压力损失均不大,所以选择U形截面。
U形截面分流道的宽度b可在5—10mm内选取,取b=6mm
半径R=0.5b=3mm,深度h=1.25R=3.75mm斜角取10°
3.2.3凝料体积:
分流道的长度
=4
40=160mm。
分流道截面积
=
。
凝料体积
=
=160×18.822=3011.52
3.2.3分流道在分型面上的布置形式:
由于塑件在模具内呈两行两列矩形分布,所以分流道采用平衡式辐射状布置。
3.2.4分流道的表面粗糙度:
由于分流道中与模具接触的外层塑料迅速冷却,只有内部的熔体流动状态比
较理想,因此分流道表面粗糙度值不能太低,一般取Ra=1.6,这可增加外层料
熔体的流动阻力,使外层塑料冷却皮层固定,形成绝热层。
3.3浇口的设计
此处采用侧浇口。
因为这类浇口加工和修整方便,应用广泛,普遍适用于
塑件的多型腔模具,且对各种塑料的成型适应性较强。
由于浇口截面小,去
除浇口较容易,且不留明显痕接。
浇口的长度l=0.8—2.0mm,取1.5mm。
侧浇口宽度和侧浇口深度尺寸计算
mm
h=(0.6—0.9)§=1.2—1.8mm取1.6mm
由于浇口体积较小,所以浇口凝料的体积忽略不计。
3.4冷料穴和拉料杆的设计
冷料穴一般设置在主流道和分流道的末端,其作用就是存放两次注射间隔而产生的冷料和料流前锋的“冷料”,防止“冷料”进入型腔而形成各种缺陷。
此次设计仅有主流道冷料穴。
由于采用推件板推出机构,故采用与球头形拉料杆匹配的冷料穴。
第4章成型零件设计及力学计算
4.1凹模的结构设计及尺寸计算
根据对塑件的结构分析,本设计中采用整体嵌入式凹模,这种结构
加工效率高,装拆方便,容易保证形状和尺寸精度。
由材料的参数可知,ABS的收缩率为0.4%--0.9%,所以平均收缩率=0.75%
塑件尺寸公差按照MT7级计算。
查表得公差=0.021mm模具制造公差去塑件公
差的1/3.
凹模深度尺寸计算公式为:
=
=cm
4.2凸模的结构设计及尺寸计算
凸模是成型制品的内表面的成型零件,通常可以分为整体式和组合式两种
类型。
本例设计中采用整体嵌入式凸模。
通过对塑件的结构分析可知,该塑件包紧力较大,所以设在动模部分。
模具的制造公差为塑件公差的1/3
凸模深度尺寸计算公式为:
公差=0.021mm
=
=cm
凸模径向尺寸计算公式为:
公差=0.025mm
=
=mm
4.3成型零件钢材的选用
根据对成型塑件的综合分析,该塑件的成型零件要有足够的刚度、强度、
磨性及良好的抗疲劳性能,同时考虑它的机械加工性能和抛光性能。
又因
该塑件为大批量生产,所以构成型腔的嵌入式凹模钢材选用P20(美国牌号)。
对于成型塑件内螺纹的螺纹型芯来说,由于脱模时与塑件的磨损严重,因此
钢材选用高合金工具钢Cr12MoV。
4.4推出方式的确定
根据塑件的成型特点,确定模具型腔在定模部分。
模具的型芯在动模部分。
塑件成型开模后,塑件和型芯一起留在动模一侧。
该塑件有螺纹孔,螺纹部分是由螺纹型芯成型的,由于成型塑件的塑料有很好的弹性,可以采用强制脱模的方式,但需要较大的脱模力,故采用脱模板推出机构。
4.4模架的选取
根据模具型腔布局的中心距和凹模嵌件的尺寸可以计算出凹模嵌件所占的平面尺寸为158x158mm,又考虑凹模最小壁厚,导柱、导套的布置等,再同时参考小型标准模架的选型经验公式,可确定模架序号及结构。
4.4.1小型标准模架的选型经验公式:
塑件在分型面上的投影宽度
须满足:
;塑件在分型面上的投影长度
须满足:
。
式中,
是推板宽度(mm);
是复位杆在长度方向的间距(mm);
是复位杆直径(mm)。
根据上式求得
=158mm,
=158mm。
参照模具设计大典,可确定选用模架序号为3号(
),模架结构为A4型。
4.4.2模架各尺寸:
A板尺寸。
A板是定模型腔板,塑件高度为28mm,凹模嵌件深度35mm,又考虑在模板上还要开设冷却水道,还需要留出足够的距离,故A板厚度取50mm。
B板尺寸。
B板是型芯固定板,按模架标准板厚取50mm。
C板(垫块)尺寸。
垫块=推出行程+推板厚度+推杆固定板厚度+(5~10)mm=28+16+20+(5~10)mm=69~74mm,初步选定C为80mm。
经上述尺寸的计算,模架尺寸已经确定为模架序号为3号,板面为
模架结构形式为A4型的标准模架。
其外形尺寸为:
。
4.4.2导向机构的确定:
该塑件的要求精度不算高,塑件形状,型腔分布对称,无明显单边注射倾向,可采用模架本身所带的导柱导向定位机构,在动模板、脱模板、定模板间使用4对导柱,导柱的长度要确保推件板推出塑件不脱落,在定模板与定模座板间采用2对导柱,保证了浇注系统凝料方便取出,定位精度高。
导柱直径d=25mm推杆直径d=10mm推杆固定板厚20mm
导柱导套的形式
第5章冷却系统的设计
5.1冷却介质
本次设计的材料为ABS,查表得成型温度为200-270℃,模具温度为
40--80℃,所以选用常温水进行冷却。
5.2冷却系统的计算
塑料制品的体积:
。
塑料制品的质量:
平均壁厚为2--4mm,所以水孔直径可取10~12mm,取10mm。
5.2.1冷水的体积流量公式为:
qv—冷却介质的体积流量,
q—单位时间内树脂在模具内释放的热量,KJ/kg;
c—冷却水的比热容J/(kg.k);
ρ—冷却介质的密度,
;
θ1—冷却介质的出口温度,℃;取60℃
θ2—冷却介质的进口温度,℃;取20℃
M—单位时间(每小时)内注入模具的塑料质量,Kg/h;设每分钟两次,得M=2×60×0.073kg/min=8.76kg/h
查表得单位时间内ABS在模具中释放的热量为q=4×105J/kg
冷却水的比热容为:
c=4.2×10³J/(kg℃)
冷却水的密度:
ρ=1000kg/m3
=0.0004
5.2.2冷却水在管道内的流速V
公式10-16[1]得:
=0.51m/s
式中
V—冷却介质的流速,m/s;
qv—冷却介质的体积流量,m3/s;
d—冷却水管的直径,mm。
5.2.3冷却水的表面传热系数α
由表11-4得,用插值法求的取Ф=10.25。
α=
=3716.3W/(m2·K)
式中
Ф—与冷却介质温度有关的物理系数;
ρ—冷却介质在一定温度下的密度,kg/m3;
v—冷却介质在圆管中的流速,m/s;
d—冷却水管的直径,m。
5.2.4冷却水管总传热面积:
A=
=0.013m2
式中
α—冷却管道孔壁与冷却介质之间的传热膜系数,W/(m2·K)
θm—模具成型表面温度,℃。
θw—冷却水的平均温度,℃。
5.2.5冷却管道总长度:
由公式得:
L=A/πd=0.013/(3.14×0.01)=0.41m=410mm
所以,最少需要两根冷却管道。
5.2.5冷却系统的布置形式:
设计总结
本次课程设计是大学生活中的最后一个课程设计,具有非同寻常的意义。
它是对这一学期中所学知识的一个总结概括,更是一次检验,让我们每个人都能清楚自己学习的效果。
确定了自己的课程设计题目后,开始可以说脑中是一片空白,很茫然,不知所措无从下手。
于是就在互联网上查找相关的资料,掌握了第一手资料。
接着我又到图书馆查找相关的专业书籍,寻找塑料注塑模具的设计思路和一些塑料注塑模具设计与制造的实例进行参考。
这些实例和思路就为我的课程设计创造了“骨架”,接下去就要为这个“骨架”添加“血肉”,最后使它生动完整。
此次课程设计,让我学到了许多知识,包括课本上学不到的知识。
当然,在设计过程中也出现了一些难题。
通过翻阅相关的书籍,在网络上寻找答案和经过指导老师的悉心指教和帮助后最终才得以解决。
本次课程设计,也让我学会了齐心协力、共同协作、努力创新,自始至终都抱着一颗坚定的信念,在漫长而又短暂的设计过程中用到了很多以前上课时学的知识,尤其是老师上课教给我们的一些分析问题、解决问题的思想在这次课程设计中都得到了很好的印证,使我在这些方面能够很快的领会。
即将毕业的我,在以后的工作中将面临着许多的问题或麻烦。
我们应该善于采集和利用各种信息资源,扩展知识面和能力;培养严谨、科学、创新与创业、艰苦奋斗、团体协作的精神;增强环境保护意识,做到清洁生产和文明生产,力求最大限度地获得企业效益和社会效益。