炼铁工艺培训资料.docx
《炼铁工艺培训资料.docx》由会员分享,可在线阅读,更多相关《炼铁工艺培训资料.docx(46页珍藏版)》请在冰豆网上搜索。
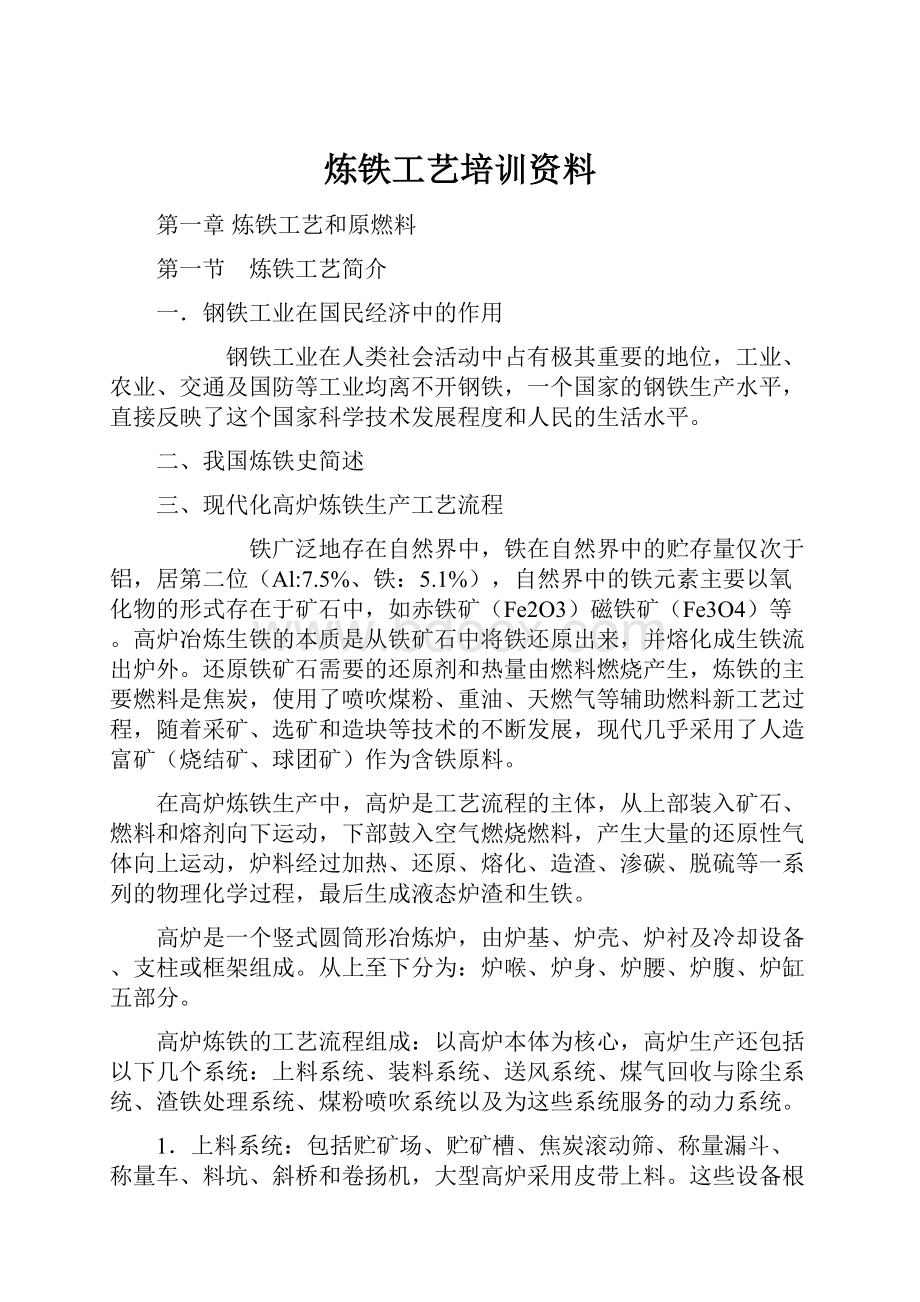
炼铁工艺培训资料
第一章炼铁工艺和原燃料
第一节 炼铁工艺简介
一.钢铁工业在国民经济中的作用
钢铁工业在人类社会活动中占有极其重要的地位,工业、农业、交通及国防等工业均离不开钢铁,一个国家的钢铁生产水平,直接反映了这个国家科学技术发展程度和人民的生活水平。
二、我国炼铁史简述
三、现代化高炉炼铁生产工艺流程
铁广泛地存在自然界中,铁在自然界中的贮存量仅次于铝,居第二位(Al:
7.5%、铁:
5.1%),自然界中的铁元素主要以氧化物的形式存在于矿石中,如赤铁矿(Fe2O3)磁铁矿(Fe3O4)等。
高炉冶炼生铁的本质是从铁矿石中将铁还原出来,并熔化成生铁流出炉外。
还原铁矿石需要的还原剂和热量由燃料燃烧产生,炼铁的主要燃料是焦炭,使用了喷吹煤粉、重油、天燃气等辅助燃料新工艺过程,随着采矿、选矿和造块等技术的不断发展,现代几乎采用了人造富矿(烧结矿、球团矿)作为含铁原料。
在高炉炼铁生产中,高炉是工艺流程的主体,从上部装入矿石、燃料和熔剂向下运动,下部鼓入空气燃烧燃料,产生大量的还原性气体向上运动,炉料经过加热、还原、熔化、造渣、渗碳、脱硫等一系列的物理化学过程,最后生成液态炉渣和生铁。
高炉是一个竖式圆筒形冶炼炉,由炉基、炉壳、炉衬及冷却设备、支柱或框架组成。
从上至下分为:
炉喉、炉身、炉腰、炉腹、炉缸五部分。
高炉炼铁的工艺流程组成:
以高炉本体为核心,高炉生产还包括以下几个系统:
上料系统、装料系统、送风系统、煤气回收与除尘系统、渣铁处理系统、煤粉喷吹系统以及为这些系统服务的动力系统。
1.上料系统:
包括贮矿场、贮矿槽、焦炭滚动筛、称量漏斗、称量车、料坑、斜桥和卷扬机,大型高炉采用皮带上料。
这些设备根据冶炼工艺要求,把矿、焦等原燃料配成一定质量和成分的“料批”运到炉顶装入受料漏斗。
2.装料系统:
钟式炉顶包括:
受料漏斗,旋转布料器,大小钟漏斗,大、小钟,大、小钟平衡杆,探尺,高压操作的高炉还有均压阀和放散阀。
无料钟炉顶包括:
受料罐、上料闸、上密封阀、称料罐、阀门箱、料流调节阀、下密封阀、中心喉管、齿轮箱等。
本系统的任务是均匀地按工艺要求将上料系统到来的炉料装入炉内。
3.送风系统:
包括鼓风机、热风炉、热风总管、换热器等,本系统的任务是把从鼓风机房送出来的冷风加热送入高炉。
4.煤气回收及除尘系统:
包括煤气上升管、煤气下降管、重力除尘器、洗涤塔、文式管、脱水器、电除尘器或布袋除尘器等。
高压高炉还有高压阀组。
本系统的任务是将炉顶引出的含尘量很高的荒煤气净化成合乎要求的气体燃料。
5.渣铁处理系统:
包括出铁场、泥炮、开口机、炉前吊车、铁水罐、渣水罐、铸铁机、堵渣机、冲渣池及其炉前水力冲渣设施等。
本系统的任务是定期将炉内渣、铁出净,保证高炉连续生产。
6.喷吹系统:
喷吹系统目前以喷煤为主,喷吹系统有制粉机、收集罐、贮存罐、喷吹罐、混合器和喷枪。
本系统的任务是磨制、收存和计量后把煤粉或重油从风口喷入高炉。
7.动力系统:
该系统包括水、电、压缩空气、氧气、蒸气等生产供应部门,本系统的任务是为高炉提供保障服务。
制氧提供氧气和氮气。
四、高炉冶炼产品
高炉生产的主要产品是生铁,副产品有炉渣、煤气和炉尘。
生铁、钢和熟铁都是铁碳合金,它们的主要区别是含碳量不同,含碳量小于0.2%的为熟铁,含碳量0.2%-1.7%的为钢,含碳量1.7%以上的为生铁。
高炉生铁含碳量为4%左右。
1.生铁
生铁分为炼钢生铁和铸造生铁,它们的主要区别是含硅量不同。
表1、表2分别为炼钢生铁和铸造生铁。
2.炉渣
炉渣有许多用途。
液态炉渣用水急冷水淬成水渣,是良好的制砖和制水泥原料。
液态炉渣用高压蒸气或压缩空气吹成渣棉,可做绝热材料。
冷凝后的干渣也是制砖和制水泥原料。
3.高炉煤气
每冶炼1吨生铁约产生1700-2500m3煤气,其化学成分有CO2(15-20%),CO(20-30%),H2(1-3%),N2(56-58%)和少量的CH4经除尘后能成为很好的低热值气体燃料,发热值一般为2900-3800KJ/m3,高炉煤气是无色无味透明的气体,由于含CO较高,会使人中毒致死。
当煤气与空气混合,煤气含量达到46-62%,温度达到着火点(650℃)时,就会发生爆炸。
因此,在煤气区域工作时要特别注意防火防爆和煤气中毒。
4.炉尘(瓦斯灰)
炉尘是随着高速上升的煤气带出高炉的细颗炉料,在除尘系统与煤气分离。
炉尘中主要是含铁、含碳,每冶炼1吨生铁约产生10-15Kg炉尘。
炉尘回收后可作为烧结原料,也可制水泥。
我们涟钢的炉尘含碳量达30-50%,可做烧砖用的燃料。
表1 炼钢用生铁GB/T717-1998
铁种
炼钢生铁
铁号
牌号
炼04
炼08
炼010
代号
L04
L08
L010
化学成份
C
≥0.35
Si
≤0.45
>0.45-0.85
>0.85-1.25
Mn
一组
≤0.4
二组
>0.4-1.0
三组
>1.00-2.00
P
特级
≤0.1
一级
≤0.100-0.15
二级
>0.15-0.25
三级
>0.25-0.40
S
特级
≤0.02
一类
>0.02-0.03
二类
>0.03-0.05
三类
>0.05-0.07
五.高炉炼铁主要技术经济指标
对高炉生产技术水平和经济效益的总要求是高产、优质、低耗、长寿和安全,主要指标有:
1.高炉有效容积利用系数η:
它是指每立方米高炉有效容积一昼夜生产炼钢铁的吨数:
η=P/Vu(t/m3.d)
2.冶炼强度I:
分为焦炭冶炼强度和综合冶炼强度两个指标。
焦炭冶炼强度是指每昼夜、每立方米高炉有效容积消耗的焦炭量,即一一昼夜装入高炉的干焦炭(Qk)与有效容积(Vu)的比值:
I焦=Ok/Vu(t/m3.d)
由于采用喷吹技术,将喷吹的燃料量与焦炭量相加后与有效容积之比称为综合冶炼强度:
I综=(O喷+Ok)/Vu(t/m3.d)
3.休风率:
休风率是指高炉休风停产时间占规定日历作业时间的百分数,规定日历作业时间是指日历时间减去计划大、中修时间和封炉时间。
4.生铁合格率:
这是质量指标。
生铁化学成分符合国家标准时称合格生铁。
生产合格生铁占高炉总铁量的百分数即为生铁合格率。
5.焦比K:
它是冶炼1吨生铁所需的干焦量:
K=Qk/(Kg/t)
6.折算焦比K折:
它是将所炼某种生铁折算成炼钢铁以后,计算1吨炼钢铁所需的干焦量:
K折==Qk/PxA(Kg/t)。
7.煤比Y(油比M):
煤比是指冶炼1 吨生铁所喷吹的煤粉量。
Y=Qy/p(Kg/t)
8.综合燃料比:
它是冶炼1吨生铁所需的干焦量与煤粉、重油量之和。
K综=(Qk+Qy+Om)/P(Kg/t)
9.综合焦比:
首先应确定煤粉或油或焦炭的置换比。
喷吹单位重量(体积)的燃料所能代替焦炭的数量称为燃料置换比。
综合焦比是指冶炼1吨生铁所喷吹的煤粉或重油乘上置换比折算成干焦量。
再与冶炼1吨生铁所喷吹的干焦量相加即为综合焦比。
10.生铁成本:
生铁成本是指冶炼1吨生铁所需的费用,包括原料、燃料、动力、工资及管理等费用 。
生铁成本是评价高炉经济效益好坏的重要标志。
表2 铸造用生铁 GB718-82
铁种
铸造用生铁
铁号
牌号
铸34
铸30
铸26
铸22
铸18
铸14
代号
Z34
Z30
Z26
Z22
Z18
Z14
化学成分
C
>3.3
Si
>3.2-3.6
>2.8-3.2
>2.4-2.8
>2.0-2.4
>1.6-2.0
>1.25-1.6
Mn、P、S
第二节 含铁原料和辅助原料
一、铁矿石分类:
根据铁矿石含铁矿物的主要性质,按其矿物组成,通常将铁矿石分为四大类:
磁铁矿、赤铁矿、褐铁矿、菱铁矿
(1)⑴磁铁矿石:
主要含Fe矿物为磁铁矿,化学式为Fe3O4;理论含铁量为72.4%,密度5.2t/m3;颜色为黑色或灰色,有光泽;致密、坚硬、难还原;
(2)⑵赤铁矿石:
主要含Fe矿物为赤铁矿,化学式为Fe2O3;理论含铁量为70%,密度4.9~5.3t/m3;颜色为红色或浅灰色;软、易破碎、易还原;
(3)⑶菱铁矿石:
主要含Fe矿物为菱铁矿,化学式为FeCO3;理论含铁量为48.2%,密度3.8t/m3;颜色为灰带有黄褐;易破碎、焙烧后易还原;
(4)⑷褐铁矿石:
主要含Fe矿物为含结晶水的氧化铁,化学式为mFe2O3nH2O(m=1、2、3;n=1、2、3、4),理论含铁量为55.2~66.1%,密度2.5~5.0t/m3;颜色为黄褐、暗褐或绒黑;疏松、易还原;
二铁矿石质量评价:
决定铁矿石质量的主要因素是其化学成分、物理性质和冶金性能。
优质铁矿石应具备以下几点:
●含铁量高,脉石少
●有害杂质如硫、磷少
●化学成分稳定
●粒度合适、均匀
●具备一定的机械强度和良好的高温冶金性能
分述如下:
⑴铁矿石含铁量
含铁量亦即品位,是衡量铁矿石质量的主要指标。
一般把实际含铁量占理论含铁量70%以上称为富矿,低于此值称为贫矿,有使用价值的铁矿石含铁量一般在23%-65%之间。
富矿经过破碎、筛分可直接冶炼,贫矿需经过选矿富化,造快后才能使用。
有无开采价值,开采后能否直接入炉及其冶炼价值的高低主要取决于含铁量。
我国矿石平均品位33%左右,低于世界铁矿石平均品位11%。
入选原矿品位一般为30~31%,已探明铁矿石储量的97.5%是需要选矿加工的贫铁矿。
我国铁精矿粉品位为51.6%~68%,平均62.35%。
⑵脉石成分
铁矿石的脉石的成分一般都是SiO2、Al2O3、CaO、MgO等,以SiO2为主的脉石称为酸性脉石,以CaO和MgO为主的脉石称为碱性脉石。
现有的铁矿石资源中,绝大多数以酸性为主,含量最高,最应重视的是SiO2,因为铁矿石中SiO2含量的增加,必然需要加入等量以上的CaO,将引起高炉渣量成双倍以上的增加,因此要求SiO2含量少一些,CaO含量多一些,MgO多一些,Al2O3少一些。
⑶有害杂质和有益元素含量
铁矿石中的某些元素对高炉冶炼有不利影响,或使钢铁性能变坏,这些元素称为有害元素或有害杂质。
通常指硫、磷、铅、砷等。
高炉冶炼中要求矿石中的有害元素或有害杂质愈少愈好。
a、硫:
硫对钢最为有害的元素,它使钢铁材料具有热脆性。
b、磷:
磷也是有害元素,它使钢铁材料具有冷脆性。
c、铅:
铅在矿石中一般以硫化物(PbS)存在,它在高炉中很易还原。
铅不熔于生铁且其比重大于生铁,因此沉入炉底,渗入砖缝破坏炉底,甚至使炉底砌砖漂浮。
d、锌:
锌在铁矿石中多以硫化物存在(ZnS)。
锌在高炉极易还原,还原的金属锌在900℃时开始挥发,上升至高炉上部以氧化成ZnO,部分粘结在炉墙上生成炉瘤。
e、砷:
砷在矿石中一般以硫化物存在,它在高炉冶炼过程中全部还原进入生铁,钢中含砷大于0.1%时,它能使钢的脆性增加且焊接性能变坏。
(4)、有益元素
许多铁矿石中常伴有锰、铬、钒、钛、镍、铜等元素,形成多金属和共生矿,这些金属能改善钢材的性能,是重要的合金元素,称为有益元素。
(5)、矿石的还原性
是评价铁矿石质量的重要指标之一。
铁矿石的还原性是指铁矿石被还原气体CO或H2还原的难易程度,还原性好,有利于降低焦比。
影响铁矿石还原性能的主要因素有:
矿物组成、矿石本身结构的致密程度和气孔率等。
气孔率大的矿石透气性好,气体还原剂与矿石的接触面增加,加速铁矿石的还原。
(6)矿石的高温性能:
软化性和熔滴性
软化性:
矿石的高温性能是指在高温状态下开始软化温度和软化区间两个方面。
开始软化温度是指铁矿石在一定荷重下加热的开始变形温度;软化区间是指铁矿石软化开始到软化终了的温度范围。
通常矿石的开始软化温度高,则软化区间较窄,反之,则软化区间较宽。
高炉冶炼要求铁矿石具有较高的开始软化温度和较窄的软化区间,以使炉内不会过早地形成初渣,即成渣位置低,软熔区小,有助于改善料柱透气性。
反之,初渣形成过早,初渣中FeO含量高,使炉内透气性变坏,并增加炉缸热负荷,严重影响冶炼过程的正常进行。
测定时将矿石在荷重还原条件下收缩率为4%时的温度定为软化开始温度,收缩率为40%时的温度定为软化终了温度。
熔滴性:
矿石软化后,在高炉内继续下行,被进一步加热和还原,并开始熔融。
在熔渣和金属达到自由流动、积聚成滴前,软熔层透气性极差,出现很大的压力降。
高炉软熔带压力降约占高炉料柱总压力降的60%。
人们对矿石在模拟高炉冶炼条件下的熔滴过程进行研究,测定其滴落开始温度、终了温度及过程压力降作为评价矿石熔滴性能的依据。
高炉操作要求矿石的熔滴温度高些、区间窄些、△Pmax低些为好。
(7)矿石的粒度
铁矿石的粒度过小会影响炉内料柱的透气性,使煤气上升的阻力增大。
粒度过大,又使矿石的加热和还原速度降低。
因而规定粒度小于5㎜的矿粉应在入炉前尽可能筛除。
而粒度上限依矿石本身的还原性而不同,一般来说矿石粒度最大为40~50㎜,最好的范围是25~35㎜。
在缩小铁矿石粒度的同时,还应使粒度均匀。
粒度分布范围较大的矿石应分级入炉。
近年来普遍有降低粒度的趋势。
(8)矿石的气孔率
矿石的气孔率有体积气孔率和面积气孔率两种表示方法;体积气孔率是指矿石的孔隙占总体积的百分比;面积气孔率是指单位体积内气孔表面积的绝对值。
高炉冶炼希望矿石的气孔率要大,烧结矿和球团矿能满足这种要求。
(9)矿石的机械强度和热强度
铁矿石的机械强度是指耐冲击、耐摩擦、耐挤压的强弱程度。
高炉容积的不断扩大对入炉铁矿石的机械强度的要求也相应提高,铁矿石强度低,转运时产生大量粉末,使入炉成本上升,入炉后产生大量粉末,既增加了炉尘损失,又阻塞了煤气通路,降低了料柱透气性,使高炉操作困难。
天然块矿的强度一般都比较好,球团矿次之,烧结矿最差。
热强度:
冶炼条件下矿石可能由于以下两种因素而减低强度:
物理吸附水或化学结晶水的蒸发使矿石破裂;矿石结构发生变化,强度降低或产生裂缝。
一般检查项目有:
①热爆裂性。
通常把具有一定粒度的冷块矿加入预热到一定温度的容器中,按照爆裂成碎片的比例来衡量,或者按一定升温速度下的爆裂程度来衡量。
②低温还原粉化率。
铁矿石还原过程中,在400~600℃和800~1000℃两个温度区间会产生爆裂或强度下降。
在400~600℃是因为Fe2O3还原到Fe3O4或FeO有晶格变化和CO的析碳反应,在铁矿石中形成裂缝,乃至粉化。
在800~1000℃则是因为矿石软熔。
常用低温还原粉化和荷重软化两种检验方法来测定。
低温还原粉化测定有静态法和动态法两种方式。
详见下页表。
③热膨胀性。
矿石加热后体积膨胀,球团矿更盛。
一般认为,体积膨胀率在20%以上的球团矿就不宜在高炉中大量使用,因为冶炼时可能造成悬料。
矿石体积膨胀率RSI=(V1-V0)/V0×100%
式中V1、V0——分别为膨胀后体积和原始体积。
(10)、矿石各种指标的稳定性
高炉要保证正常生产,必须有一个相对稳定的冶炼条件,即不但要有足够数量的原料,而且要求各项理化性能相对稳定。
特别是矿石的品位、脉石成分和数量、有害元素、还原性能等指标的波动,会导致各项指标下降(如焦比、产量、效益等)
三、铁矿石的混匀和中和
由于矿山开采的矿石不能直接加入高炉进行冶炼,这是由于原矿含铁量及其它化学成分波动很大,并有多种金属共生物,粒度组成悬殊等原因所致,必须经过加工处理才能使用。
一般天然富矿在入炉前进行整粒和混匀。
贫矿和多种金属共生矿经过选矿去除杂质、回收有用成分,加工成成造富矿后使用。
所以。
铁矿石加工处理的目的,主要是使高炉上精料,以改善高炉生产指标,并做好铁矿资源的综合利用。
1.破碎:
根据对产品的粒度要求不同,可分为粗碎、中碎、细碎及粉碎几个级别,粗碎从1000mm破碎到100mm,中碎是从100mm破碎到30mm,细碎是从30mm破碎到5mm,粉碎是从5mm破碎到1mm以下。
2.筛分:
经过破碎后的天然富矿粒度很不均匀,通过筛分可除去粉未并筛出超过规定粒度上限的大块,进行再破碎,还可完成粒度分级,使原料分级入炉或单级供高炉使用。
3.混匀:
混匀也称中和,目的是在于稳定矿石的各种性质。
混匀后要求矿石品位的波动小于1%,混匀的主要手段是“平铺直取”。
4.焙烧:
焙烧是把矿石在一定的气氛中加热到比其熔点低200-300℃,以改善矿石的化学组成和性质;去除原料中的有害杂质;回收有用元素;同时还可以使矿石组织疏松,便于破碎和提高矿石的还原性。
按照焙烧的气氛不同分为:
氧化焙烧、还原磁化焙烧和氯化焙烧等。
5.选矿:
选矿的目的是为了提高矿石的品位,对于复合矿可回收其中有用成分,除去有害杂质。
选矿的常用方法有磁选和浮选。
四、烧结矿和球团矿
1.烧结矿的质量评价(以一级品为例):
⑴品位:
TFe含量波动范围不超过0.5%
⑵碱度:
R2(=CaO/SiO2)波动范围不超过0.08倍
⑶转鼓和筛分指数:
转鼓(+6.3㎜)≥72%,筛分指数≤8%
⑷粒度:
<5㎜的粉矿应筛除。
(炼铁厂规定入炉矿中<5㎜的不超过5%)
2.球团矿的质量评价
内容有ⅰ:
品位稳定性
ⅱ:
碱度的稳定性以及SiO2的含量
ⅲ:
矿石的含硫量
ⅳ:
粒度范围(国内球团以6~16㎜为宜)
附录:
主要含铁原料化学成分表(以2006年1月炼铁厂的技术专业月报数据为例)
成分
品名
原料化学成分(%)
TFe
FeO
SiO2
Al2O3
CaO
MgO
S
P
烧结矿
55.17
4.29
4.98
1.46
11.97
2.05
0.018
0.048
自产竖窑球团矿
62.99
0.38
5.59
4.54
1.29
1.19
0.006
0.165
湖北竖球
63.55
4.47
1.46
0.99
0.62
0.017
0.022
进口球团
65.86
3.38
0.358
0.325
0.1
0.0157
0.0084
南非矿
65.89
3.01
1.39
0.09
0.1
0.021
0.066
澳矿
63.79
2.92
1.329
0.1169
0.1
0.0315
0.0786
五.熔剂
在目前的原材料条件下,高炉采用“高碱度烧结矿+酸性球团+块矿”的炉料结构,熔剂直接入炉量逐渐减少,现在熔剂多应用于烧结工艺。
(浙江杭钢)
⑴熔剂的主要作用是助熔和造渣。
⑵熔剂按性质分成三大类
●碱性熔剂:
主要有石灰石CaCO3,白云石CaCO3·MgCO3
●酸性熔剂:
主要有硅石SiO2
●中性熔剂:
主要有铁钒土
⑶熔剂成分的波动将引起高炉造渣制度的波动。
有时为了保持烧结矿碱度和基本炉料结构不变,以确保高炉炉况的稳定,需要通过微量调剂使高炉炉渣碱度不发生变化。
当下调碱度时,越来越多的企业不使用硅石,而使用含SiO2量较高的天然块矿(如海南块矿)代替,由于加入量比硅石多,容易控制,避免了炉渣碱度的剧烈波动。
而且由于加入SiO2的同时也带入了铁元素,有助于减少高炉渣量。
当上调碱度时,也可以用转炉钢渣块代替石灰石或者白云石直接入炉。
⑷对碱性熔剂石灰石的质量要求:
一是熔剂中的碱性氧化物(CaO+MgO)含量要高,而酸性氧化物(SiO2+Al2O3)含量要低,一般要求石灰石中酸性氧化物含量不超过3.5%;二是有害杂质S、P含量越少越好;三是要求石灰石有一定的强度和均匀的粒度组成。
大高炉要求25~50mm,小高炉要求10~30mm。
六.辅助原料可分为以下三大类:
●含铁原料:
如碎铁等
●洗炉剂料:
如锰矿、萤石等
●护炉剂料:
如钒钛矿等
●
附录:
铁烧结矿、球团矿的企业标准Q/OHAC100—2004中的有关技术要求:
Ⅰ优质铁烧结矿的技术要求应符合下表规定:
项目名称
化学成分,%
物理性能,%
冶金性能,%
TFe
R
FeO
S
转鼓指数(+6.3mm)
筛分指数(-5mm)
低温还原粉化指数(RDI)(+3.15mm)
还原度指数(RI)
允许波动范围
±0.4
±0.05
±0.5
-
指标
≥57
≥1.7
<9
<0.03
≥72
<6
≥74
≥78
Ⅱ普通铁烧结矿的技术要求应符合下表规定:
项目名称
化学成分,%
物理性能,%
冶金性能,%
碱度
品级
TFe
R
FeO
S
转鼓指数(+6.3mm)
筛分指数(-5mm)
低温还原粉化指数(RDI)(+3.15mm)
还原度指数(RI)
允许波动范围
不大于
1.5~2.5
一级
±0.5
±0.08
11
0.07
68
7
≥74
≥78
二级
±1.0
±0.12
12
0.10
65
9
≥72
≥75
Ⅲ球团矿的技术要求应符合下表的规定:
品级
化学成分,%
物理性能,%
冶金性能,%
TFe
R
FeO
S
转鼓指数(+6.3mm)
抗压强度(N/个球)
筛分指数(-5mm)
膨胀率
还原度指数(RI)
允许波动范围
不大于
一级
±0.5
±0.08
1
0.05
≥90
≥2000
<5
≤15
≥65
二级
±1.0
±0.12
2
0.08
≥86
≥1500
<5
≤20
≥65
第三节 燃料
高炉用燃料主要有焦炭和喷吹用煤粉。
下面仅仅介绍焦炭的有关内容:
⒈焦炭的作用
发热剂:
焦炭在高炉冶炼中作为主要的能量来源,使高炉内各种化学反应得
以进行。
高炉冶炼所需消耗的热量有70-80%来自燃料的燃烧。
还原剂:
焦炭中的固定碳(C)和它燃烧产生的CO、H2与铁矿矿石中各级氧气物反应,将铁还原出来。
料柱骨架:
高炉内的矿石和熔剂下降到高温区时,全部软化和熔化成液体,焦炭则即不熔化也不软化,因而成了高炉内支承料柱的骨架。
⒉焦炭的化学成分
焦炭的化学成分决定了其化学性质。
化学成分包含有五个方面,即固定碳、灰分、硫分、挥发分、水分的百分含量。
⒊对焦炭的质量要求
亦即其化学成分的要求,有以下五各方面:
⑴固定碳和灰分是焦炭的主要组成部分,两者互为消长关系。
固定碳含量高,单位焦炭提供的热量和还原剂就多,灰分含量就低。
灰分含量高所带来的不良影响有:
①因灰分中80%是SiO2和Al2O3,灰分高,则高炉渣量增加。
②灰分在炼焦过程中不能熔融,对焦炭中各种组织的黏结很不利,使裂纹增多,强度降低。
③灰分与焦炭的膨胀性不同,在高炉内加热后,灰分颗粒周围产生裂纹,使焦炭碎裂、粉化。
④灰分中的碱金属和Fe2O3等都对焦炭气化反应起催化作用,使焦炭反应性指数增高,影响反应后强度。
因此要求固定碳含量高而灰分含量低。
⑵硫分
高炉燃料(焦炭和煤粉)所带入的硫量约占高炉硫负荷的80%,因此要求其含量尽可能低。
还有磷、碱金属等杂质含量尽可能低。
⑶挥发分
挥发分是焦炭成熟程度的标志。
挥发分含量低,说明结焦后期热分解与热缩聚程度高,气孔壁材质致密,有利于焦炭显微硬度,耐磨强度和反应后强度的提高,因此挥发分含量以低为好。
⑷水分
焦炭水分波动引起入炉干焦量变化,即焦炭真实负荷的波动,因而要求焦炭水分在稳定的前提下尽可能低,水分越高,焦粉粘附在焦块上,不易筛除而