扇形板零件的机械加工工艺规程及工艺装备.docx
《扇形板零件的机械加工工艺规程及工艺装备.docx》由会员分享,可在线阅读,更多相关《扇形板零件的机械加工工艺规程及工艺装备.docx(30页珍藏版)》请在冰豆网上搜索。
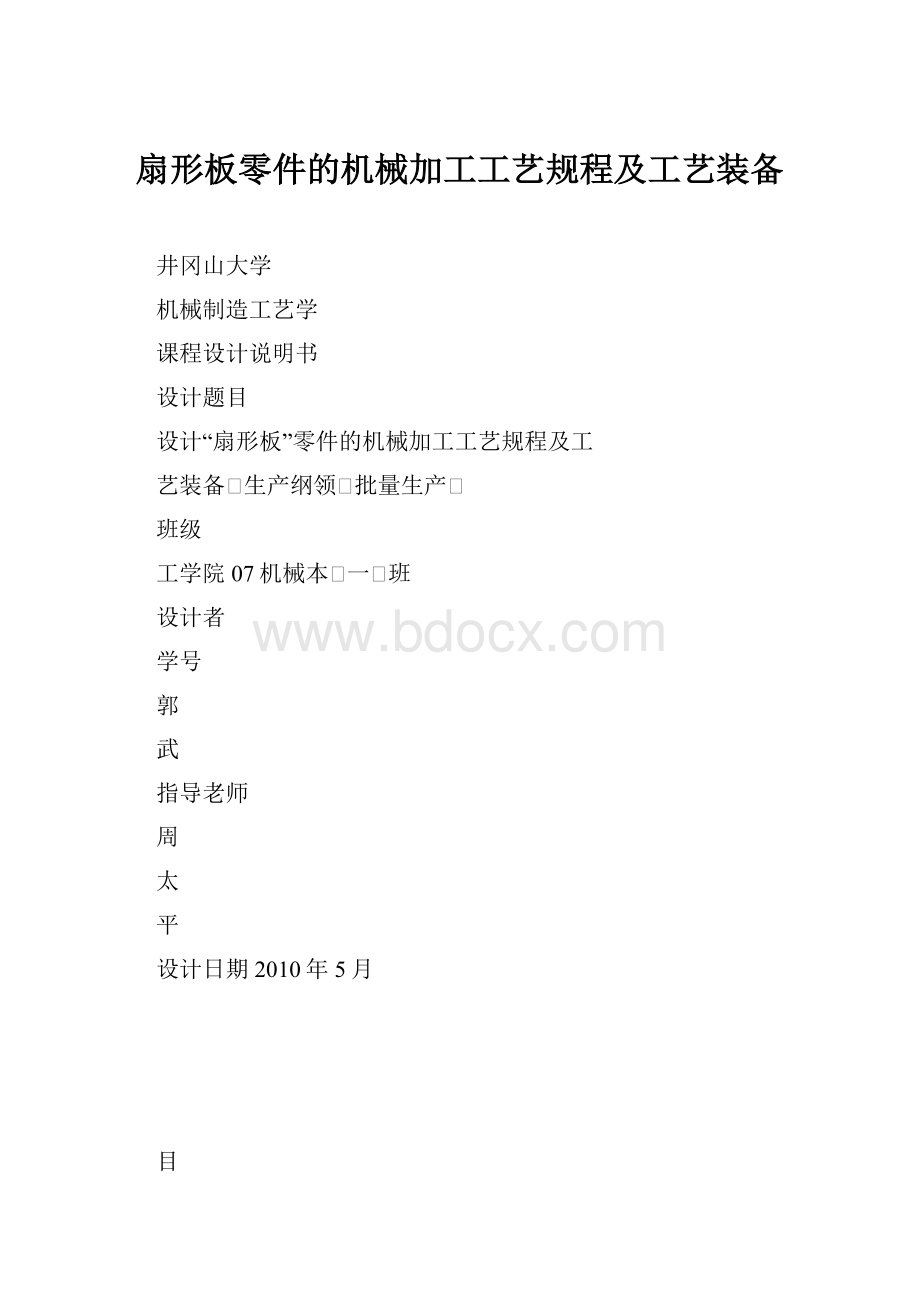
扇形板零件的机械加工工艺规程及工艺装备
井冈山大学
机械制造工艺学
课程设计说明书
设计题目
设计“扇形板”零件的机械加工工艺规程及工
艺装备�生产纲领�批量生产�
班级
工学院07机械本�一�班
设计者
学号
郭
武
指导老师
周
太
平
设计日期2010年5月
目
录
设计任务书„„„„„„„„„„„„„„„„„„„„„„„„1
1绪论„„„„„„„„„„„„„„„„„„„„„„„„„„„2
2扇形板的分析„„„„„„„„„„„„„„„„„„„„„„„3
2.1扇形板的分析„„„„„„„„„„„„„„„„„„„„„3
2.2扇形板的工艺要求„„„„„„„„„„„„„„„„„„„4
3工艺规程设计„„„„„„„„„„„„„„„„„„„„„„„5
3.1加工工艺过程„„„„„„„„„„„„„„„„„„„„„5
3.2确定各表面加工方案„„„„„„„„„„„„„„„„„„5
3.2.1影响加工方法的因素„„„„„„„„„„„„„„„„„5
3.2.2加工方案的选择„„„„„„„„„„„„„„„„„„„„6
3.3确定定位基准„„„„„„„„„„„„„„„„„„„„„„6
3.3.1粗基准的选择„„„„„„„„„„„„„„„„„„„„„6
3.3.2精基准的选择„„„„„„„„„„„„„„„„„„„„„6
3.4工艺路线的拟订
„„„„„„„„„„„„„„„„„„„„7
3.4.1工序的合理组合„„„„„„„„„„„„„„„„„„„„7
3.4.2工序的集中与分散„„„„„„„„„„„„„„„„„„„„8
3.4.3加工阶段的划分„„„„„„„„„„„„„„„„„„„„„9
3.4.4加工工艺路线方案的比较„„„„„„„„„„„„„„„„9
3.5扇形板的偏差�加工余量�工序尺寸及毛坯尺寸的确定
„„11
3.5.1毛坯的结构工艺要求„„„„„„„„„„„„„„„„„„11
3.5.2扇形板的偏差计算„„„„„„„„„„„„„„„„„„„„12
4钻孔夹具设计
4.1研究原始质料
„„„„„„„„„„„„„„„„„„„„13
4.2定位基准的选择„„„„„„„„„„„„„„„„„„„„13
4.3钻削力及夹紧力的计算„„„„„„„„„„„„„„„„„„13
4.4误差分析„„„„„„„„„„„„„„„„„„„„„„„„14
4.5夹具个零件的设计„„„„„„„„„„„„„„„„„„„„14
4.6夹具设计及操作的简要说明„„„„„„„„„„„„„„„15
心得体会
„„„„„„„„„„„„„„„„„„„„„„„„„„16
„„„„„„„„„„„„„„„„„„„„„„„„„„17
参考文献
井冈山大学
工艺与夹具课程设计任务书
设计题目�“扇形板”零件机械加工工艺及3-φ8孔钻夹具设计
设计条件�批量生产
设计内容�
1产品零件图�一张�CAD图�打印�
2产品毛坯图�铸造毛坯��一张�CAD图打印�
3机械加工工艺过程卡片�该零件完整的工艺过程�手写或打印�
4机械加工工序卡片�所设计夹具对应的工序�一张�手写或打印�
5夹具设计�装配图一张�主要零件图三张�全部为1�1铅笔图�
6工艺、夹具设计说明书�6000字以上�用专用纸撰写�
学
班
学
姓
院
级
号
名
工学院
07机械本�1�班
郭武
指导教师
周太平
1绪论
机械设计制造及其夹具设计是我们融会贯通3年所学的知识�将理论与实践
相结合�对专业知识的综合运用训练�为我们即将走向自己的工毕业设计打下良
好的基础。
机械加工工艺是规定产品或零件机械加工工艺过程和操作方法�是指导生产
的重要的技术性文件。
它直接关系到产品的质量、生产率及其加工产品的经济效
益�生产规模的大小、工艺水平的高低以及解决各种工艺问题的方法和手段都要
通过机械加工工艺来体现�因此工艺规程的编制的好坏是生产该产品的质量的重
要保证的重要依据。
在编制工艺时须保证其合理性、科学性、完善性。
而机床夹具是为了保证产品的质量的同时提高生产的效率、改善工人的劳动
强度、降低生产成本而在机床上用以装夹工件的一种装置�其作用是使工件相对
于机床或刀具有个正确的位置�并在加工过程中保持这个位置不变。
它们的研究
对机械工业有着很重要的意义�因此在大批量生产中�常采用专用夹具。
而本次对于扇形板加工工艺及夹具设计的主要任务是�
⑴完成扇形板零件加工工艺规程的制定�
⑵完成钻孔专用夹具的设计。
通过对扇形板零件的初步分析�了解其零件的主要特点�加工难易程度�主
要加工面和加工粗、精基准�从而制定出扇形板加工工艺规程�对于专用夹具的
设计�首先分析零件的加工工艺�选取定位基准�然后再根据切销力的大小、批
量生产情况来选取夹紧方式�从而设计专用夹具。
2扇形板的分析
2.1扇形板的工艺分析
扇形板是一个很重要的零件�因为其零件尺寸比较小�结构形状较复杂�但
其加工孔和表面的精度要求较高�此外还有φ220
孔要求加工�对精度要求
+0.021
也很高。
孔粗糙度要求都是
�所以都要求精加工。
其小头孔与右平面有平
孔有对称度公差要求�因为其尺寸精度、几何形
行度的公差要求�和φ220
+0.021
状精度和相互位置精度�以及各表面的表面质量均影响机器或部件的装配质量�
进而影响其性能与工作寿命�因此它们的加工是非常关键和重要的。
2.2扇形板的工艺要求
一个好的结构不但要应该达到设计要求�而且要有好的机械加工工艺性�也
就是要有加工的可能性�要便于加工�要能够保证加工质量�同时使加工的劳动
量最小。
而设计和工艺是密切相关的�又是相辅相成的。
设计者要考虑加工工艺
问题。
工艺师要考虑如何从工艺上保证设计的要求。
图2.1扇形板的零件图2.1扇形板的零件
图2.2扇形板的零件实体图
该加工有5个加工表面�平面加工包括扇形板左端面、右端面�孔系加工包
�小孔φ8和扇形板外弧面加工。
括φ220
+0.021
⑴以平面为主有�①扇形板左端面的粗、精铣加工�其粗糙度要求是
Ra=3.2�右端面的粗、精铣加工�其粗糙度要求是Ra=6.3及Ra=3.2�
②扇形板R48弧面采用数控机床加工�其粗糙度要求是
Ra=3.2。
⑵孔系加工有�①φ220
+0.021
孔的粗镗、半精镗�精镗加工�并且进行倒角1x45°。
其表面粗糙度为Ra=1.6�
②φ8孔钻.铰加工�其表面粗糙度要求
�并且
与左端面的平行度要求为0.08�与φ220
的对称度为
+0.021
0.1。
扇形板毛坯的选择铸造�因为生产率较高�所以可以免去每次造型。
单边余
量一般在
�结构细密�能承受较大的压力�占用生产的面积较小。
�由
[3]由于是中批量生产。
上面主要是对扇形板零件的结构、加工精度和主要加工表面进行了分析�选
择了其毛坯的的制造方法为模锻和中批的批量生产方式�从而为工艺规程设计提
供了必要的准备。
3工艺规程设计
3.1加工工艺过程
由以上分析可知�该扇形板零件的主要加工表面是平面、孔系。
一般来说�
保证平面的加工精度要比保证孔系的加工精度容易。
因此�对于扇形板来说�加
工过程中的主要问题是保证孔的尺寸精度及位置精度�处理好孔和平面之间的相
互关系以及槽的各尺寸精度。
由上面的一些技术条件分析得知�扇形板的尺寸精度�形状精度以及位置关
系精度要求都不是很高�这样对加工要求也就不是很高。
3.2确定各表面加工方案
一个好的结构不但应该达到设计要求�而且要有好的机械加工工艺性�也就
是要有加工的可能性�要便于加工�要能保证加工的质量�同时使加工的劳动量
最小。
设计和工艺是密切相关的�又是相辅相成的。
对于我们设计扇形板的加工
工艺来说�应选择能够满足平面孔系和轴向孔系加工精度要求的加工方法及设
备。
除了从加工精度和加工效率两方面考虑以外�也要适当考虑经济因素。
在满
足精度要求及生产率的条件下�应选择价格较底的机床。
3.2.1影响加工方法的因素
⑴要考虑加工表面的精度和表面质量要求�根据各加工表面的技术要求�
选择加工方法及分几次加工。
⑵根据生产类型选择�在大批量生产中可专用的高效率的设备。
在单件小
批量生产中则常用通用设备和一般的加工方法。
如、柴油机连杆小头孔的加工�
在小批量生产时�采用钻、扩、铰加工方法�而在大批量生产时采用拉削加工。
⑶要考虑被加工材料的性质�例如�淬火钢必须采用磨削或电加工�而有
色金属由于磨削时容易堵塞砂轮�一般都采用精细车削�高速精铣等。
⑷要考虑工厂或车间的实际情况�同时也应考虑不断改进现有加工方法和
设备�推广新技术�提高工艺水平。
⑸此外�还要考虑一些其它因素�如加工表面物理机械性能的特殊要求�
工件形状和重量等。
选择加工方法一般先按这个零件主要表面的技术要求来选定最终加工方法。
再选择前面各工序的加工方法�如加工某一轴的主要外圆面�要求公差为IT6�
表面粗糙度为Ra0.63μm�并要求淬硬时�其最终工序选用精度�前面准备工序
可为粗车——半精车——淬火——粗磨。
3.2.2加工方案的选择
⑴由参考文献机械制造工艺机床夹具课程设计指导表2-6可以确定�平面
的加工方案为�粗铣——精铣�
��粗糙度为Ra6.3�1.6�一般不淬
硬的平面�精铣的粗糙度可以较小。
故左右端面可用粗铣——精铣。
⑵由参考文献机械制造工艺机床夹具课程设计指导表2-5可以确定�
φ22
孔的表面粗糙度要求为1.6�则选择孔的加方案序为�粗镗——半精
+0.021
0
镗---精镗。
并且进行倒角1x45°。
⑶小孔φ8加工方法�零件毛坯不能直接锻出孔�只能锻出一个小坑�以便
在以后加工时找正其中心�但其表面粗糙的要度求为
�并且其孔径较小�
所以选择加工的方法是钻——-铰----精铰。
⑷R48圆弧面的加工方法�采用数控机床进行加工。
3.3确定定位基准
3.3.1粗基准的选择
选择粗基准时�考虑的重点是如何保证各加工表面有足够的余量�使不加工
表面与加工表面间的尺寸、位子符合图纸要求。
粗基准选择应当满足以下要求�
⑴粗基准的选择应以加工表面为粗基准。
目的是为了保证加工面与不加工
面的相互位置关系精度。
如果工件上表面上有好几个不需加工的表面�则应选择
其中与加工表面的相互位置精度要求较高的表面作为粗基准。
以求壁厚均匀、外
形对称、少装夹等。
⑵选择加工余量要求均匀的重要表面作为粗基准。
⑶应选择加工余量最小的表面作为粗基准。
这样可以保证该面有足够的加
工余量。
⑷应尽可能选择平整、光洁、面积足够大的表面作为粗基准�以保证定位
准确夹紧可靠。
有浇口、冒口、飞边、毛刺的表面不宜选作粗基准�必要时需经
初加工。
要从保证孔与孔、孔与平面、平面与平面之间的位置�能保证扇形板在整个
加工过程中基本上都能用统一的基准定位。
从零件图分析可知�主要是选择加工
扇形板底面的装夹定位面为其加工粗基准。
故选用零件的右端面做为粗基准
3.3.2精基准选择的原则
⑴基准重合原则。
即尽可能选择设计基准作为定位基准。
这样可以避免定
位基准与设计基准不重合而引起的基准不重合误差。
⑵基准统一原则�应尽可能选用统一的定位基准。
基准的统一有利于保证
各表面间的位置精度�避免基准转换所带来的误差�并且各工序所采用的夹具比
较统一�从而可减少夹具设计和制造工作。
⑶互为基准的原则。
选择精基准时�有时两个被加工面�可以互为基准反
复加工。
自为基准原则�有些精加工或光整加工工序要求余量小而均匀�可以选择加
工表面本身为基准。
。
此外�还应选择工件上精度高。
尺寸较大的表面为精基准�以保证定位稳固
可靠。
并考虑工件装夹和加工方便、夹具设计简单等。
要从保证孔与孔、孔与平面、平面与平面之间的位置�能保证扇形板在整个
加工过程中基本上都能用统一的基准定位。
从扇形板零件图分析可知�它的左端
面与φ220
�适于作精基准使用。
但用一个平面和一个孔定位限制工件自由
+0.021
度不够�在加上一个圆柱销定位�则可以满足整个加工过程中基本上都采用统一
的基准定位的要求。
选择精基准的原则时�考虑的重点是有利于保证工件的加工精度并使装夹
准。
3.4工艺路线的拟订
对于批量生产的零件�一般总是首先加工出统一的基准。
扇形板的加工的第
一个工序也就是加工统一的基准。
具体安排是先以孔和面定位粗、精加工扇形板
右端面。
后续工序安排应当遵循粗精分开和先面后孔的原则。
3.4.1工序的合理组合
确定加工方法以后�就按生产类型、零件的结构特点、技术要求和机床设备
等具体生产条件确定工艺过程的工序数。
确定工序数的基本原则�
⑴工序分散原则
工序内容简单�有利选择最合理的切削用量。
便于采用通用设备。
简单的机
床工艺装备。
生产准备工作量少�产品更换容易。
对工人的技术要求水平不高。
但需要设备和工人数量多�生产面积大�工艺路线长�生产管理复杂。
⑵工序集中原则
工序数目少�工件装�夹次数少�缩短了工艺路线�相应减少了操作工人数
和生产面积�也简化了生产管理�在一次装夹中同时加工数个表面易于保证这些
表面间的相互位置精度。
使用设备少�大量生产可采用高效率的专用机床�以提
高生产率。
但采用复杂的专用设备和工艺装备�使成本增高�调整维修费事�生
产准备工作量大。
一般情况下�单件小批生产中�为简化生产管理�多将工序适当集中。
但由
于不采用专用设备�工序集中程序受到限制。
结构简单的专用机床和工夹具组织
流水线生产。
加工工序完成以后�将工件清洗干净。
清洗是在
的含0.4%�1.1%
苏打及0.25%�0.5%亚硝酸钠溶液中进行的。
清洗后用压缩空气吹干净。
保证零
件内部杂质、铁屑、毛刺、砂粒等的残留量不大于
。
3.4.2工序的集中与分散
制订工艺路线时�应考虑工序的数目�采用工序集中或工序分散是其两个不
同的原则。
所谓工序集中�就是以较少的工序完成零件的加工�反之为工序分散。
⑴工序集中的特点
工序数目少�工件装夹次数少�缩短了工艺路线�相应减少了操作工人数和
生产面积�也简化了生产管理�在一次装夹中同时加工数个表面易于保证这些表
面间的相互位置精度。
使用设备少�大量生产可采用高效率的专用机床�以提高
生产率。
但采用复杂的专用设备和工艺装备�使成本增高�调整维修费事�生产
准备工作量大。
⑵工序分散的特点
工序内容简单�有利选择最合理的切削用量。
便于采用通用设备�简单的机
床工艺装备。
生产准备工作量少�产品更换容易。
对工人的技术水平要求不高。
但需要设备和工人数量多�生产面积大�工艺路线长�生产管理复杂。
工序集中与工序分散各有特点�必须根据生产类型。
加工要求和工厂的具体
情况进行综合分析决定采用那一种原则。
一般情况下�单件小批生产中�为简化生产管理�多将工序适当集中。
但由
于不采用专用设备�工序集中程序受到限制。
结构简单的专用机床和工夹具组织
流水线生产。
由于近代计算机控制机床及加工中心的出现�使得工序集中的优点更为突
出�即使在单件小批生产中仍可将工序集中而不致花费过多的生产准备工作量�
从而可取的良好的经济效果。
3.4.3加工阶段的划分
零件的加工质量要求较高时�常把整个加工过程划分为几个阶段�
⑴粗加工阶段
粗加工的目的是切去绝大部分多于的金属�为以后的精加工创造较好的条
件�并为半精加工�精加工提供定位基准�粗加工时能及早发现毛坯的缺陷�予
以报废或修补�以免浪费工时。
粗加工可采用功率大�刚性好�精度低的机床�选用大的切前用量�以提高
生产率、粗加工时�切削力大�切削热量多�所需夹紧力大�使得工件产生的内
应力和变形大�所以加工精度低�粗糙度值大。
一般粗加工的公差等级为IT11�
IT12。
粗糙度为Ra80�100μm。
⑵半精加工阶段
半精加工阶段是完成一些次要面的加工并为主要表面的精加工做好准备�保
证合适的加工余量。
半精加工的公差等级为IT9�IT10。
表面粗糙度为Ra10�
1.25μm。
⑶精加工阶段
精加工阶段切除剩余的少量加工余量,主要目的是保证零件的形状位置几精
度,尺寸精度及表面粗糙度,使各主要表面达到图纸要求.另外精加工工序安排在
最后,可防止或减少工件精加工表面损伤。
精加工应采用高精度的机床小的切前用量�工序变形小�有利于提高加工精
度�精加工的加工精度一般为IT6�IT7�表面粗糙度为Ra10�1.25μm。
此外�加工阶段划分后�还便于合理的安排热处理工序。
由于热处理性质的
不同�有的需安排于粗加工之前�有的需插入粗精加工之间。
但须指出加工阶段的划分并不是绝对的。
在实际生活中�对于刚性好�精度
要求不高或批量小的工件�以及运输装夹费事的重型零件往往不严格划分阶段�
在满足加工质量要求的前提下�通常只分为粗、精加工两个阶段�甚至不把粗精
加工分开。
必须明确划分阶段是指整个加工过程而言的�不能以某一表面的加工
或某一工序的性质区分。
例如工序的定位精基准面�在粗加工阶段就要加工的很
准确�而在精加工阶段可以安排钻小空之类的粗加工。
3.4.4加工工艺路线方案的比较
在保证零件尺寸公差、形位公差及表面粗糙度等技术条件下�成批量生产可
以考虑采用专用机床�以便提高生产率。
但同时考虑到经济效果�降低生产成本�
拟订两个加工工艺路线方案。
见下�
1.工艺路线方案一:
工序1�粗铣零件的右端面�以左端面为粗基准。
工序2�粗铣零件的左端面�以右端面为粗基准。
工序3�精铣零件的右端面�以左端面为精基准。
工序4�精铣零件的左端面�以右端面为精基准。
工序5�用数控机床加工R48外圆弧�以右端面和孔为基准。
工序6�对φ220
孔进行粗镗�以又端面为基准。
+0.021
工序7�对φ220
孔进行半精镗�以又端面为基准。
孔进行倒角1X45°�以又端面为基准。
+0.021
工序8�对φ220
+0.021
工序9�对φ220
孔进行精镗�以又端面为基准。
+0.021
工序10�对φ8孔空进行钻——铰----精铰。
以φ220
孔和右端面为基准。
+0.021
工序11�清洗表面。
工序12�剔除毛刺。
工序13�终检。
工艺路线方案二�
工序1�用数控机床加工R48外圆弧�以右端面和孔φ220
+0.021
为基准。
工序2�粗精铣左端面�以R48外圆弧为基准。
工序3�粗精铣右端面�以以R48外圆弧和左端面为基准。
工序�对φ220
+0.021
孔进行粗镗——半精镗---精镗。
并且进行倒角1x45°�以
又端面为基准。
工序4�对φ8孔空进行钻——铰---精铰。
以φ220
+0.021
孔和右端面为基准。
工序5�对φ220
孔进行粗镗——半精镗---精镗。
并且进行倒角1x45°。
+0.021
工序11�清洗表面。
工序12�剔除毛刺。
工序13�终检。
3.工艺方案比较与分析。
⑴从工序可以看出�方案二由于铣面夹具设计非常难遭价太高所以。
并且由于
φ8和φ222
有对称度要求�故应先加工φ22
φ8。
还有对于倒角是�
0.021
+0.021
0
0
我们应把倒角放在精铰前。
再加工由以上分析�方案一为合理、经济的加工工艺路线方案。
3.5扇形板的偏差�加工余量�工序尺寸及毛坯尺寸的确定
扇形板的铸造采用的是HT150铸造制造,其材料是HT150,生产类型为批量生
产�采用铸造毛坯。
3.5.1毛坯的结构工艺要求
扇形板为铸造件�对毛坯的结构工艺性有一定要求�
�1�由于铸造件尺寸精度较高和表面粗糙度值低�因此零件上只有与其它机
件配合的表面才需要进行机械加工�其表面均应设计为非加工表面。
�2�工艺基准以设计基准相一致。
�3)便于装夹、加工和检查。
(4)结构要素统一�尽量使用普通设备和标准刀具进行加工。
在确定毛坯时�要考虑经济性。
虽然毛坯的形状尺寸与零件接近�可以减少
加工余量�提高材料的利用率�降低加工成本�但这样可能导致毛坯制造困难�
需要采用昂贵的毛坯制造设备�增加毛坯的制造成本。
因此�毛坯的种类形状及
尺寸的确定一定要考虑零件成本的问题但要保证零件的使用性能。
在毛坯的种类
形状及尺寸确定后�必要时可据此绘出毛坯图。
3.5.2扇形板的偏差计算
⑴扇形板左右端面的偏差及加工余量计算
左右端面加工余量的计算。
根据工序要求�其加工分粗、精铣加工。
各工步
余量如下�
粗铣�由机械余量加工手册知�其单边余量值规定为1.4—1.8mm�现取
1.5mm。
可知其粗铣时精度等级为IT12�粗铣平面时厚度偏差取
精铣�由机械余量加工手册知�其单边余量值规定为0.7mm。
铸造毛坯的基本尺寸为32mm�由机械余量加工手册知锻件复杂系数S2�重
0.608kg�则锻件偏差为+1.1-0.5
mm。
毛坯的名义尺寸为�32+1.5+0.7=34.2mm
毛坯最小尺寸为�34.2-0.5=33.7mm
毛坯最大尺寸为�34.2+1.1=35.3mm
粗铣后最大尺寸为�32+0.7=32.7mm
粗铣后最小尺寸为�32.7-0.21=32.49mm
精铣后尺寸与零件图尺寸相同�且保证各个尺寸精度。
⑵φ220
孔的偏差及加工余量计算
+0.021
该孔精度要求为IT7�由考参考文献1知确定工序尺寸及余量为�
第一次钻20
粗镗�φ21.8mm
2Z=1.8mm
扩孔钻21.8
半精镗�粗铰�:
φ21.94mm
2Z=0.14�Z为单边余量�
2Z=0.06mm�Z为单边余量�
精镗�精铰�:
φ220
+0.021
mm
锻件毛坯孔的基本尺寸分别为�22-1.8-0.14-0.06=20mm
�3�φ8孔孔的偏差及加工余量计算
该孔精度设为为IT7�由考参考文献1知确定工序尺寸及余量为�
钻孔�φ7.8mm
粗铰�φ7.96mm
2Z=0.16mm�Z为单边余量�
精铰�φ8H7mm
2Z=0.04mm�Z为单边余量�
该孔就可达到精度要求。
�4�外圆弧表面沿轴线长度加工余量及公差。
由机械余量加工手册知锻件复杂系数S1�重1.25kg�则锻件偏差为+1.1
-0.5mm。
长度方向的余量由机械余量加工手册其余量规定值是2.0—2.5mm现取2.0mm。
4.夹具设计
4�1研究原始质料
利用本夹具主要用来钻圆周面上孔φ8�加工时要满足粗糙度要求。
为了保
证技术要求�最关键是找到定位基准。
同时�应考虑如何提高劳动生产率和降低
劳动强度。
4�2定位基准的选择
由零件图可知�左右端面进行了粗、精铣加工�φ220
孔进行了粗、半
+0.021
精、精镗加工。
因此�定位、夹紧方案有�
方