气门摇杆支座机械制造课程设计说明书.docx
《气门摇杆支座机械制造课程设计说明书.docx》由会员分享,可在线阅读,更多相关《气门摇杆支座机械制造课程设计说明书.docx(12页珍藏版)》请在冰豆网上搜索。
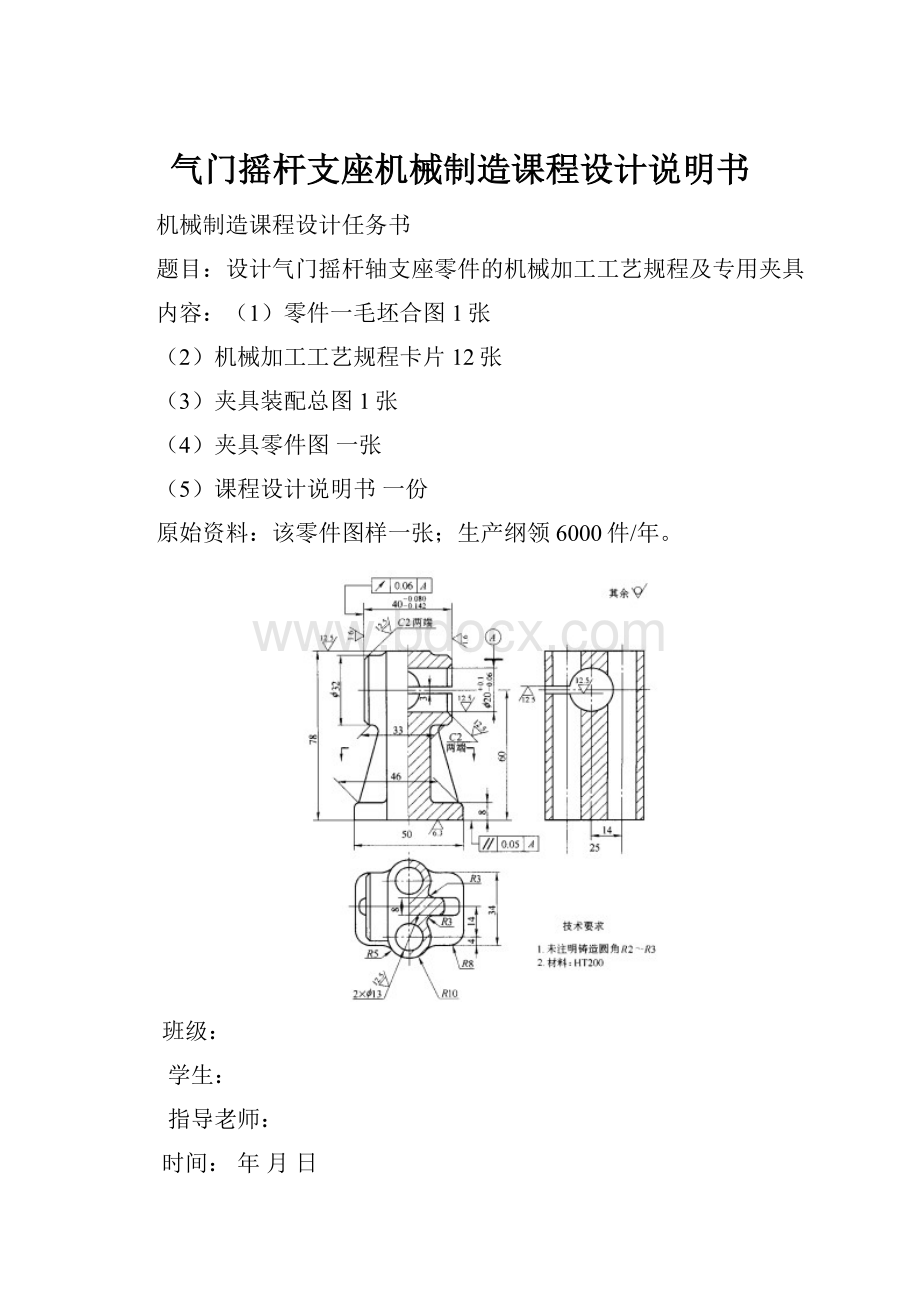
气门摇杆支座机械制造课程设计说明书
机械制造课程设计任务书
题目:
设计气门摇杆轴支座零件的机械加工工艺规程及专用夹具
内容:
(1)零件一毛坯合图1张
(2)机械加工工艺规程卡片12张
(3)夹具装配总图1张
(4)夹具零件图一张
(5)课程设计说明书一份
原始资料:
该零件图样一张;生产纲领6000件/年。
班级:
学生:
指导老师:
时间:
年月日
第一部分:
设计目的…………………………………………………1
第二部分:
设计步骤
一、零件的作用…………………………………………1
二、确定毛坯,画毛坯——零件合图………………2
三、工艺规程设计……………………………………3
四、加工工序设计……………………………………8
五、时间定额计算………………………………………10
六、夹具设计…………………………………………12
设计目的:
机械制造课程设计是在学完了机械制造(含机床夹具设计)和大部分专业课,并进行了生产实习的基础上进行的一个教学环节。
这次设计使我们能综合运用机械制造工艺学中的基本理论,并结合生产实习中学到的实践知识,独立地分析和解决工艺问题。
初步具备了设计一个中等复杂程度零件(气门摇杆轴支座)的工艺规程的能力和运用夹具设计的基本原理和方法,拟订夹具设计方案,完成家具结构设计的能力,也是熟悉和运用有关手册,图表等技术资料及编写技术文件技能的一次实践机会,为今后的毕业设计及未来从事的工作打下良好的基础。
由于能力所限,经验不足,设计中还有许多不足之处,希望各位老师多加指导。
一.零件的分析
(一)零件的作用
气门摇杆轴支座是柴油机一个主要零件。
是柴油机摇杆座的结合部,Ø20(+0.10—+0.16)孔装摇杆轴,轴上两端各装一进气门摇杆,摇杆座通过两个Ø13mm孔用M12螺杆与汽缸盖相连,3mm轴向槽用于锁紧摇杆轴,使之不转动。
(二)零件的工艺分析
由附图1得知,其材料为HT200。
该材料具有较高的强度,耐磨性,耐热性及减振性,适用于承受较大应力,要求耐磨的零件。
该零件上主要加工面为上端面,下端面,左右端面,2-Ø13mm孔和Ø20(+0.1——+0.06)mm以及3mm轴向槽的加工。
Ø20(+0.1——+0.06)mm孔的尺寸精度以及下端面0.05mm的平面度与左右两端面孔的尺寸精度,直接影响到进气孔与排气门的传动精度及密封,2——Ø13mm孔的尺寸精度,以上下两端面的平行度0.055mm。
因此,需要先以下端面为粗基准加工上端面,再以上端面为粗基准加工下端面,再把下端面作为精基准,最后加工Ø20(+0.1——+0.06)mm孔时以下端面为定位基准,以保证孔轴相对下端面的位置精度。
由参考文献
(1)中有关孔的加工的经济精度机床能达到的位置精度可知上述要求可以达到的零件的结构的工艺性也是可行的。
二.确定毛坯,画毛坯——零件合图(附图2)
根据零件材料确定毛坯为铸件,已知零件的生产纲领为6000件/年,通过计算,该零件质量约为3Kg,由参考文献(5)表1—4、表1—3可知,其生产类型为大批生产,毛坯的铸造方法选用砂型机器造型。
此外,为消除残余应力,铸造后安排人工时效处理。
参考文献
(1)表2.3—12;该种铸造公差等级为CT10~11,MA-H级。
参考文献
(1)表2.3-12,用查表方法确定各表面的加工余量如下表所示:
加工表面
基本尺寸
加工余量等级
加工余量数值
说明
上端面
48mm
H
4mm
单侧加工
下端面
50mm
H
3mm
单侧加工
左端面
35mm
H
3mm
单侧加工
右端面
35mm
H
3mm
单侧加工
三、工艺规程设计
(一)定位基准的选择:
精基准的选择:
气门摇杆轴支座的下端面既是装配基准又是设计基准,用它作为精基准,能使加工遵循基准重合的原则,实现V形块十大平面的定位方式(V形块采用联动夹紧机构夹紧)。
Ø20(+0.1——+0.06)mm孔及左右两端面都采用底面做基准,这使得工艺路线又遵循“基准统一”的原则,下端面的面积比较大,定位比较稳定,夹紧方案也比较简单,可靠,操作方便。
粗基准的选择:
考虑到以下几点要求,选择零件的重要面和重要孔做基准。
第一,在保证各加工面均有加工余量的前提下,使重要孔或面的加工余量尽量均匀,此外,还要保证定位夹紧的可靠性,装夹的方便性,减少辅助时间,所以粗基准为上端面。
镗削Ø20(+0.1——+0.06)mm孔的定位夹紧方案:
方案一:
用一菱形销加一圆柱销定位两个Ø13mm的孔,再加上底面定位实现,两孔一面完全定位,这种方案适合于大批生产类型中。
方案二:
用V形块十大平面定位
V形块采用联动夹紧机构实现对R10的外圆柱表面进行定位,再加底面实现完全定位,由于Ø13mm孔的秒个精度不需要很高,故用做定位销孔很难保证精度,所以选择方案二。
(二)制定加工工艺路线
根据各表面加工要求,和各种加工方法能达到的经济精度,确定各表面及孔的加工方法如下:
上端面:
精铣。
下端面:
粗铣
左端面:
粗铣—精铣右端面:
粗铣—精铣
2—Ø13mm孔:
钻孔。
3mm轴向槽—精铣
Ø20(+0.1—+0.006)mm:
钻孔—粗镗—精镗
因左右两端面均对Ø20(+0.1—+0.006)mm孔有较高的位置要求,故它们的加工宜采用工序集中原则,减少装次数,提高加工精度。
根据先面后孔,先主要表面后次要表面和先粗加工后精加工的原则,将端面的精铣和下端面的粗铣放在前面,下端面的精铣放在后面,每一阶段要首先加工上端面后钻孔,左右端面上Ø20(+0.1—+0.006)mm孔放后面加工。
初步拟订加工路线如下:
工序号
工序内容
铸造
时效
涂漆
00
车上端面
01
钻两通孔
02
精铣下端面
03
铣右端面
04
钻通孔¢18mm
05
镗孔Ø20mm,孔口角1*45度
06
铣左端面
07
铣轴向槽
08
检验
09
入库
上述方案遵循了工艺路线拟订的一般原则,但某些工序还有一些问题还值得进一步讨论。
如车上端面,因工件和夹具的尺寸较大,在卧式车床上加工时,它们惯性力较大,平衡困难;又由上端面不是连续的圆环面,车削中出现断续切削容易引起工艺系统的震动,故改动铣削加工。
工序03应在工序02前完成,使上端面在加工后有较多的时间进行自然时效,减少受力变形和受热变形对2—Ø13mm通孔加工精度的影响。
修改后的工艺路线如下:
序号
工序内容
简要说明
01
02
03
04
05
06
07
08
09
10
铸造
时效
涂漆
精铣上端面
精铣下端面
钻两通孔
铣右端面
钻通孔Ø18
镗孔到Ø20,孔口倒角1*45度
铣左端面
铣轴向槽
检验
入库
消除内应力
防止生锈
先加工粗基准面
加工经基准
先面后孔
先面后孔
后镗削余量
次要工序后加工
(三)选择加工设备及刀、夹、量具
由于生产类型为大批生产,故加工设备适宜通用机床为主,辅以少量专用机床的流水生产线,工件在各机床上的装卸及各机床间的传动均由人工完成。
粗铣上端面:
考虑到工件的定位夹紧方案及夹具结构设计等问题,采用立铣选择X1632立式铣床。
(参考文献
(1)表6-18),选择直径D为Ø80mm立铣刀,参考文献
(1)表7-88,通用夹具和游标卡尺。
粗铣下端面:
采用上述相同的机床与铣刀,通用夹具及游标卡尺。
精铣下端面:
采用上述相同的机床与铣刀,通用夹具及游标卡尺。
粗铣左端面:
采用卧式铣床X1632,参考文献
(1)表6—21,采用以前的刀具,专用夹具及游标卡尺。
精铣左端面:
采用卧式铣床X1632,参考文献
(1)表6—21,专用夹具及游标卡尺。
钻2-Ø18mm孔:
采用Z3025B*10,参考文献
(1)表6—26,通用夹具。
刀具为d为Ø18.0的直柄麻花钻,参考文献
(1)表7—111。
钻Ø18孔:
钻孔直行为Ø118mm,选择摇臂钻床Z3025参考文献
(1)表6—26,采用锥柄麻花钻,通用夹具及量具。
镗Ø20(+0.1——+0.06)mm孔:
粗镗:
采用卧式组合镗床,选择功率为1.5KM的ITA20镗削头,参考文献
(1)白喔—88。
选择镗通孔镗刀及镗杆,专用夹具,游标卡尺。
四、加工工序设计
经查参考文献
(1)表3—12可得,铣削上端面的加工余量为4mm,又由零件对上顶端表面的表面精度RA=12.5mm可知,粗铣的铣削余量为4mm。
底面铣削余量为3mm,粗铣的铣削余量为2mm,精铣余量1mm,精铣后公差登记为IT7~IT8。
取每齿进给量为fz=0.2mm/z(粗铣)
取每齿进给量为f=0.5mm/r(精铣)
粗铣走刀一次ap=2mm,精铣走刀一次ap=1mm
初步取主轴转速为150r/min(粗铣),取精铣主轴的转速为300r/min,又前面已选定直径D为Ø80mm,故相应的切削速度分别为:
校核粗加工。
V粗=πDn/1000=3.14*80*150/1000=37.68
V精=πDn/1000=3.14*80*300/1000=75.36
又由机床切削功率P=167.9*10^-5ap^0.9f2aeznkpm
取Z=10个齿,pm=1.代入得:
pm=167.9*2.0^0.9*(0.2)^50*2.5*10*1
pm=0.861(km)
又因前查的机床的功率为1.5kw/h若效率为0.8P,则
1.8P=6.0>pm
故选择主轴的转速为150m/min
(2)工序5中的粗镗ø18工序。
Ø18粗镗余量参考文献[1]表3-83取粗镗为1.8mm,粗镗切削余量为0.2mm,铰孔后尺寸为 20H8,各工部余量和工序尺寸公差列于表2-3
加工表面
加工方法
余量
公差等级
工序尺寸及公差
Ø18
粗镗
1.8
____
ø19.8
Ø19.2
精镗
0.2
H8
20H8
孔轴线到底面位置尺寸为60mm
因精镗与粗镗的定位的下底面与V型块,精镗后工序尺寸为20.02±0.08mm,与下底面的位置精度为0.05mm,与左右端面的位置精度为0.06mm,且定位夹紧时基准重合,故不需保证。
0.06mm跳动公差由机床保证。
粗镗孔时因余量为1.9mm,故ap=1.9mm,
查文献[1]表2.4-8
取V=0.4m/s=24m/min
去进给量为f=002mm/r
n=1000V/πd=1000*24/3.14*20=380r/min
查文献的Fz=9.81*60^nFzCFzapXFzV^nFzKFz
pm=FzV*10^-3
CF2=180,
XFz=1
Yfz=0.75
nFz=0
Rfz=9.81*60°*180*2.75ˊ*0.2^0.75*0.4°*1
=1452N
P=0.58kw
取机床效率为0.85
0.78*0.85=0.89kw>0.58kw
故机床的功率足够。
五、时间定额计算
下面计算工序5的时间定额
(1)机动时间
粗镗时:
L/(f*n)=45/0.2*380=7.5s
精镗时:
f取0.1mm/s
L/(f*n)=45/0.1*380=15s
总机动时间:
T=7.5+15=22.5s
(2)辅助时间:
操作内容
每次时间
(min)
粗镗
精镗
操作次数
时间min
操作次数
时间min
装夹
2
1
2
-
-
换刀
1
1
1
1
1
测量
0.1
1
0.1
1
0.1
卸夹
1.5
-
-
1
1.5
开机到开始的时间
0.3
1
1
1
0.3
退刀
0.1
1
1
1
0.1
所以辅助时间Ta为:
Ta=2+1+0.1+1.5+0.3*2+0.1*0.1*2
=6.5min
作业时间为Ta+Tb=605+0.37=6.87min
该工序单位加工时间为6.87min
五、填写机械加工工艺卡和机械加工工序卡
工艺文件详见附表。
六、夹具设计
本次设计的夹具为第5道工序粗——精镗Ø20(+0.1—+0.06)mm孔。
该夹具为双支承前后引导镗床夹具。
1、确定设计方案
该孔的设计基准为下端面,故以下端平面做定位基准,实现“基准重合”原则;另加两V形块从前后两方向实现对R10的外圆柱面进行夹紧,从对工件的结构形状分析,若工件以下端面朝下放置在支承板上,定位夹紧就比较稳定,可靠,也容易实现。
工件以下端面在夹具上定位,限制了三个自由度,其余三个自由度也必须限制。
用哪种方案合理呢?
方案1 在2—Ø13的通孔内插入一现边销限制一个移动自由度,再以两孔的另一个孔内侧面用两个支承钉限制一个移动自由度和一个转动自由度。
这种定位方案从定位原理上分析是合理的,夹具结构也简单。
但由于孔和其内侧面均不规定其精密度,又因结构原因,夹紧力不宜施加在这样的定位元件上,故工件定位面和定位元件之间很可能会接触不好,使定位不稳定。
这个方案不宜采用。
方案2 用两个V形块夹紧前后两外圆柱面,用两铰链压板压在工件的下端,这样就限制了两个移动自由度和一个转动自由度,这种方案定位可靠,可实现完全定位。
2计算夹紧力并确定螺杆直径
参考文献(3)表1-2-11,因夹具的夹紧力与切削力方向相反,实际所需夹紧力F夹与切削力F之间的关系F夹=KF
安全系数K在夹紧力与切削力方向相反后时,K=3,由前面的计算可知F=1452.3N
所以F夹=KF=3*1452.3=4356.9N
F0=F夹/2=1178.4(N)
参考文献3表1-24,从强度考虑,用一个M10的螺柱完全可以满足要求,M10的许应夹紧为3924N,所以螺杆直径为d=10mm
3.定位精度分析
Ø20(+0.10—+0.16)孔的精加工是在一次装夹下完成的,具体采用的是前后支撑引导的夹具机构,机床与镗杆之间所采用的是浮动连接,故机床主轴振动可略不计,Ø20(+0.10—+0.16)孔的加工精度主要由镗模来保证。
图见附表。
因为孔的轴线与底面的平行度要求为0.05。
故两镗模装配后同轴度要求应小于0.05,又因为镗套与镗杆Ø18H6(+0.03—0)/h5(0—-0.009),其最大间隙为
Xmax=0.013+0.009=0.022mm
=0.022/310=0.00007
被加工孔的长度为42mm
取两孔同轴度误差为0.03mm
则ΔT1=2×42×0.00007=0.006
ΔT2=0.03mm
所以ΔT=ΔT1+ΔT2=0.036
又以为
0.036<0.05
0.006<0.06
所以夹具能满足零件加工精度的要求。
零件图,零件——毛坯合图另附
参考文献:
(1)
(2)
(3)