立式钻床切削头部液压系统设计.docx
《立式钻床切削头部液压系统设计.docx》由会员分享,可在线阅读,更多相关《立式钻床切削头部液压系统设计.docx(23页珍藏版)》请在冰豆网上搜索。
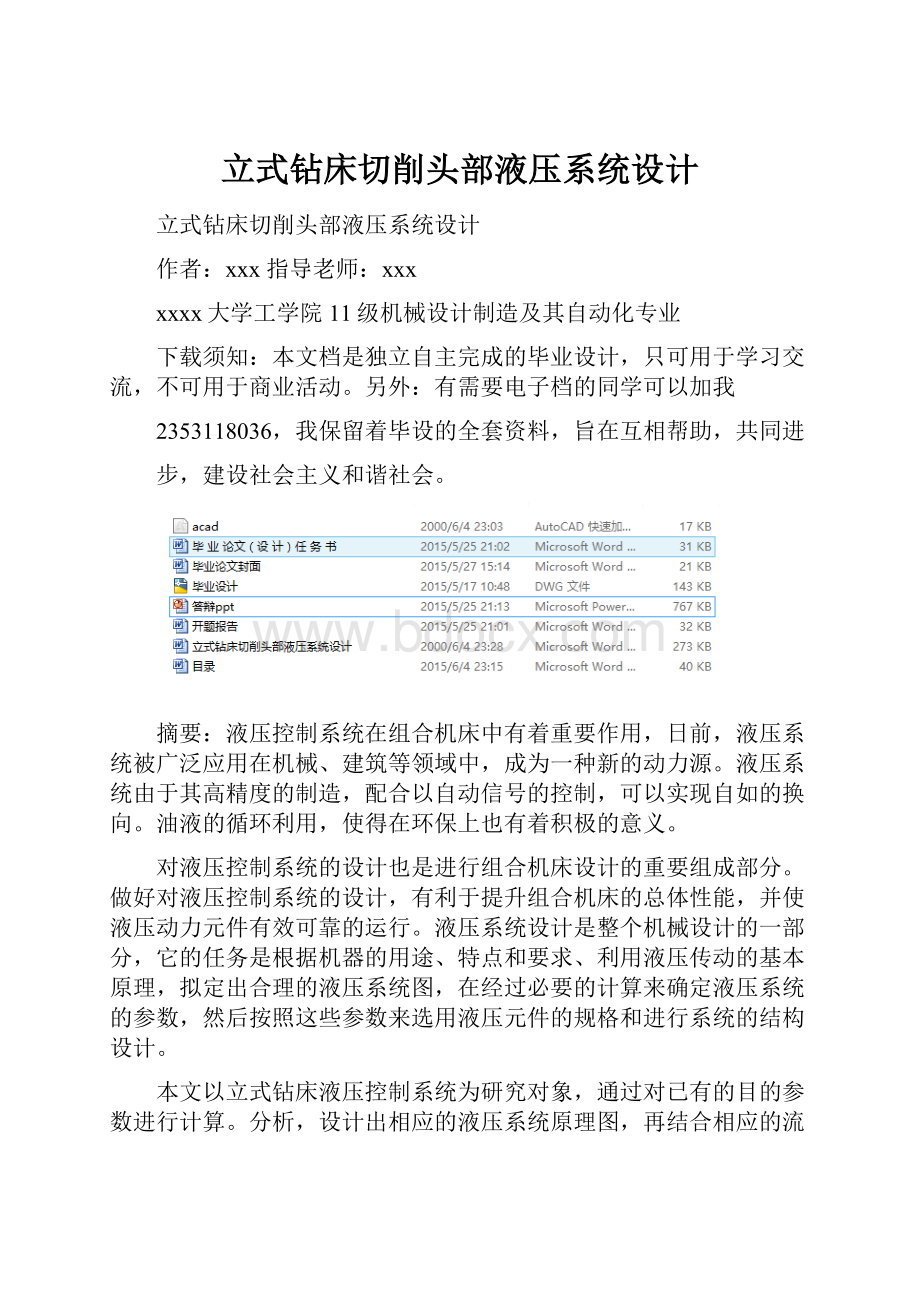
立式钻床切削头部液压系统设计
立式钻床切削头部液压系统设计
作者:
xxx指导老师:
xxx
xxxx大学工学院11级机械设计制造及其自动化专业
下载须知:
本文档是独立自主完成的毕业设计,只可用于学习交流,不可用于商业活动。
另外:
有需要电子档的同学可以加我
2353118036,我保留着毕设的全套资料,旨在互相帮助,共同进
步,建设社会主义和谐社会。
摘要:
液压控制系统在组合机床中有着重要作用,日前,液压系统被广泛应用在机械、建筑等领域中,成为一种新的动力源。
液压系统由于其高精度的制造,配合以自动信号的控制,可以实现自如的换向。
油液的循环利用,使得在环保上也有着积极的意义。
对液压控制系统的设计也是进行组合机床设计的重要组成部分。
做好对液压控制系统的设计,有利于提升组合机床的总体性能,并使液压动力元件有效可靠的运行。
液压系统设计是整个机械设计的一部分,它的任务是根据机器的用途、特点和要求、利用液压传动的基本原理,拟定出合理的液压系统图,在经过必要的计算来确定液压系统的参数,然后按照这些参数来选用液压元件的规格和进行系统的结构设计。
本文以立式钻床液压控制系统为研究对象,通过对已有的目的参数进行计算。
分析,设计出相应的液压系统原理图,再结合相应的流量载荷计算,查阅相应的手册,选定各种液压元件,设计完成,还需根据相应的公式进行校核,以完成液压系统的设计。
关键词:
液压传动,液压元件,回路分析
1绪论
当今世界,机械技术一日千里,为我们所处的时代加上了飞翔的翅膀,机械技术的产生和飞速发展改变了整个人类的生活和思维方式,为人类文明的进程作出了卓越的贡献,液压技术为机械行业做出了很大的贡献。
随着机械行业的不断发展,社会经济的日新月异,特别是机械制造行业,汽车行业,建筑行业,电子行业等等,各个企业已普遍地使用到液压系统,所以研究液压控制系统和使液压控制系统的使用效率提高、节能环保,有重大意义。
液压技术渗透到很多领域,不断在民用工业、在机床、工程机械、冶金机械、塑料机械、农林机械、汽车、船舶等行业得到大幅度的应用和发展,而且发展成为包括传动、控制和检测在内的一门完整的自动化技术。
现今,采用液压传动的程度已成为衡量一个国家工业水平的重要标志之一。
如发达国家生产的95%的工程机械、90%的数控加工中心、95%以上的自动线都采用了液压传动技术。
液压传动相对于机械传动来说,是一门新技术。
自1795年制成第一台水压机起,液压技术就进入了工程领域,1906年开始应用于国防战备武器。
第二次世界大战期间,由于军事工业迫切需要发应快和精度高的自动控制系统,因而出现了液压伺服系统。
20世纪60年代以后,由于原子能、空间技术、大型船舰及计算机技术的发展,不断地对液压技术提出新的要求,液压技术相应也得到了很大发展,渗透到国民经济的各个领域中。
在工程机械、冶金、军工、农机、汽车、轻纺、船舶、石油、航空、和机床工业中,液压技术得到普遍应用。
近年来液压技术已广泛应用于智能机器人、海洋开发、宇宙航行、地震预测及各种电液伺服系统,使液压技术的应用提高到一个崭新的高度。
目前,液压技术正向高压、高速、大功率、高效率、低噪声和高度集成化等方向发展;同时,减小元件的重量和体积,提高元件寿命,研制新的传动介质以及液压传动系统的计算机辅助设计、计算机仿真和优化设计、微机控制等工作,也日益取得显著成果。
解放前,我国经济落后,液压工业完全是空白。
解放后,我国经济获得迅速发展,液压工业也和其它工业一样,发展很快。
20世纪50年代就开始生产各种通用液压元件。
当前,我国已生产出许多新型和自行设计的系列产品,如插装式锥阀、电液比例阀、电液伺服阀、电液脉冲马达以及其它新型液压元件等。
但由于过去基础薄弱,所生产的液压元件,在品种与质量等方面和国外先进水平相比,还存在一定差距,我国液压技术也将获得进一步发展,它在各个工业技术的发展,可以预见,液压技术也将获得进一步发展,它
在各个工业部门中的用应,也将会越来越广泛。
现代机械一般多是机械、电气、液压三者紧密联系,结合的一个综合体。
液压传动与机械传动、电气传动并列为三大传统形式,液压传动系统的设计在现代机械的设计工作中占有重要的地位。
2设计要求
一台立式多轴钻孔专用机床,钻削头部件的上、下运动采用液压传动,其工作循环是:
快速下降—工作进给—快速上升—原位停止。
为防止钻削头部件因自重下滑,装有平衡重(设计时可不考虑重力的影响)。
已知数据如下:
最大钻削力Fmax=25000N;钻削头部件质量m=255kg;快速下降行程s1=200mm,工作进给行程s2=50mm,快速上升行程s3=250mm;快速下降速度v1=75mm/s,工作进给速度v2<=1mm/s,快速上升速度v3=100mm/s,加、减速时间△t<=0.2s;钻削头部件上下运动时,静摩擦力为Ffs=1000N;动摩擦力Ffd=500N;液压系统中的执行元件用液压缸,且活塞杆固定。
液压缸采用V型密封圈密封,其机械效率ηcm=0.90。
根据以上条件绘制出液压工作循环图,如下
图2.1循环图
3液压系统工况分析
3.1负载分析
由已知条件快速下降速度v1=75mm/s,工作进给速度v2=1mm/s,快速上升速度v3=100mm/s,加、减速时间=0.2s;钻削头部件上下运动时,静摩擦力为Ffs=1000N;动摩擦力Ffd=500N
其中惯性力的计算
启动时Fa1=2m
=2*255*
=191.25N
减速时Fa2=2m
=2*255*
=188.7N
制动时Fa3=2m
=2*255*
=2.55N
反向启动时Fa4=2m
=2*255*
=255N
反向制动时Fa5=2m
=2*255*
=255N
由此计算各阶段的负载
启动时FL1=Ffs+Fa1=1000+191.25=1191.25N
快速下降时FL2=Ffd=500N
减速时FL3=Ffd-Fa2=500-188.7=311.3N
工作进给时FL4=Ffd+Fmax=500+25000=25500N
制动时FL5=Ffd-Fa3=500-2.55=497.45N
反向启动时FL6=Ffs+Fa4=1000+255.5=1255.5N
减速上升时FL7=Ffd=500N
反向制动时FL8=Ffd-Fa5=500-255.5=244.5N
其阶段负载计算结果如下表
阶段
负载
启动
1191.25N
快速下降
500N
减速
311.3N
工作进给
25500N
制动
497.45N
反向启动
1255.5N
快速上升
500N
反向制动
244.5N
表3.1负载表
3.2运动分析
由以上的速度图,联系物理学中的匀变速直线运动及匀速直线运动位移计算公式,容易计算出各个工作阶段的行程,具体计算结果如下表
工况
速度
行程计算公式
计算结果
启动
0——V1
v1
7.5
快速下降
V1
s1-v1
-
v2
184.9
减速
V1——V2
v1
+
v2
7.6
工作进给
V2
s2-
v2
49.9
制动
V2——0
v2
0.1
反向启动
0——V3
v3
10
快速上升
V3
s3-v3
249.1
反向制动
V3——0
v3
10
表3.2行程表
由以上的负载及运动分析,即可绘制组合工况图:
图3.1速度—位移曲线图
图3.2负载循环图
4执行元件参数确定
4.1选定工作压力
最大负载为25500N,查表初选液压缸工作压力p=3.5MPa
4.2确定执行元件结构参数
液压缸的有效工作面积A1=
=
=8095*10-6m2=8095mm2
有D=
=
=101.52mm,取标准值100mm
由p=3.5MPa,查表得液压缸的内径和活塞杆径d之比取
=0.5,即D=2d,得d=50mm
故标准化后
A1=
=7854mm2
A2=
=5890mm2
流量计算
快进时q1=A1*V1=7854*75mm3/s=589050mm3/s=35.343L/min
工进时q2=A1*V2=7854*1mm3/s=7854mm3/s=0.471L/min
快退时q3=A2*V3=5890*100mm3/s=589000mm3/s=35.34L/min
4.3绘制液压工况图
进油腔(工作腔)、回油腔的压力
快速下降和快速上升时,回油腔的压力均为0,即P1=P3=0,工作进给时,由于回油路上的调速阀产生背压,查表选定工进时回油腔的压力为0.5MPa,即P2=0.05MPa
计算工作腔的压力
快速下降时,由P1’A1-P1A2=
其中负载F1=500N,带入上式计算得P1’=0.071MPa
工作进给时,由P2’A1-P2A2=
其中负载F2=25500N,带入上式计算得P2’=3.61MPa
快速上升时,由P3’A2-P3A1=
其中负载F3=500N,带入上式计算得P3’=0.094MPa
计算输出功率
快速下降时,N1=P1’Q1=0.042kW
工作进给时,N2=P2’Q2=0.028kW
快速上升时,N3=P3’Q3=0.055kW
将以上计算结果绘制成表,如下表
工况
负载(N)
回油腔压力P(MPa)
进油腔压力P’(MPa)
输入流量Q(L/min)
输入功率N(kW)
快速下降
500
0
0.071
35.343
0.042
工作进给
25500
0.5
3.61
0.471
0.028
快速上升
500
0
0.094
35.34
0.055
表4.1液压缸工况表
将以上计算结果绘制成图,即得液压缸的工况图,如下
图4.1液压工况图
5计算和选择液压元件
5.1选择液压泵
由以上的p-t线图可得最大的工作压力为3.61MPa,查表,取进油回路上的总压力损失为0.5MPa,则液压泵的最大工作压力
Pp=3.61+0.5=4.11MPa
由以上的Q-t线图可得最大的流量为35.343L/min,查表取K=1.1,则液压泵的额定流量
Q=1.1*35.343=38.877L/min
计算公称工作压力,选择液压泵
液压泵的公称工作压力
Pr=Pp*1.25=5.13MPa
查液压手册,选择YBN40-JB型限压式变量泵,40系列,调压范围为2-7MPa,驱动功率2.86kW。
5.2电机的选择
液压泵在实际工作过程中,其压力和流量往往大于额定的数值,我们只需计算出其最大值。
一般液压系统中液压泵所需的功率最大值发生在最大的转速下,由此,
P=
=
=3.25kW
其中Pp为泵的最大工作压力
Q为泵的流量
为泵的总效率
由此,查相关电机样本,选择Y112-2电动机,其为Y系列,额定功率4kW。
5.3其他液压元件的选择
各类元件均根据其流量及工作压力选定
滤油器的流量为35.343L/min,查液压手册,选择WU-H63*100SP型网式滤油器,通径为20mm,压力32MPa,流量63L/min。
限压式变量叶片泵选择YBN40N-JB型,选择过程如上述。
单向阀的流量为35.34L/min,查液压手册,选择S10P1型单向阀,其通径10mm,最大工作压力31.5MPa,连接形式为板式(代号P),阀的开启压力为0.05MPa(代号为1)。
二位二通的流量为35.34L/min,查液压手册,选择22C—63BH型二位二通。
三位四通的流量为35.343L/min,查液压手册,选择4WE10E2X型三位四通湿式电磁换向阀,通径为10mm,2X系列,A/B/P口的最大工作压力为32MPa,T口的最大工作压力为16MPa,最大流量100L/min。
调速阀的流量为0.471L/min,查液压手册,选择2FRM102X/B型调速阀,最大流量10L/min,通径10mm,3X系列。
液压缸的设计过程见上。
各液压元件的选择如下表所示
液压元件
型号
滤油器
WU-H63*100SP
限压式变量泵
YBN40N-JB
单向阀
S10P1
三位四通
4WE10E2X
二位二通
22C—63BH
调速阀
2FRM102X/B
液压缸
自行设计
表5.1液压元件表
油管的选择
元件之间的连接管道按元件接口尺寸决定。
液压泵选定之后,需重新计算液压缸工作各阶段的进、回油流量。
工况
快进
工进
快退
输入流量(L/min)
Q1=
=
=155.47
Q1=0.471
Q1=Qp=38.877
排出流量(L/min)
Q2=
=
=116.59
Q2=
=
=0.353
Q2=
=51.84
表5.2流量计算表
油箱的选择
油箱容量按液压泵的流量计算,取ζ=7。
V=ζQp=7×38.877=272.139L
故就近取标准值300L
6拟定液压系统原理图
6.1回路方案确定
6.1.1调速回路
快速上升及快速下降均可有简单回路直接完成,但工作进给时,回油路上必须有背压,因此即可设计在回油路上添加一个调速阀,如下
图6.1调速回路设计图
6.1.2速度切换回路
由上述的调速回路只考虑了工作进给时候的回油路背压,但是在快速下降及快速上升时,为使速度达到要求,回油路上不能使用背压,由此考虑在主油路上添加三位四通方向控制阀,在回油路上并联一个二位二通行程控制阀,以此来控制此油路的开通与闭合。
如下图所示
图6.2速度切换回路设计图
上图中,当工作进给状态转换至快速上升状态时,除三位四通需要切换外,还需要对二位二通进行切换,为简化操作过程,再二位二通上并联一个单向阀,下降阶段时单向阀关闭,上升阶段时,单向阀自动打开,此时,油液只经过单向阀流至有杆腔。
除简化操作外,添加单向阀亦可避免油液经过二位二通的右位,承受压力损失。
添加单向阀后,即可得到最终的液压原理图。
如下图所示
图6.3液压系统回路设计图
6.2液压回路分析
电磁铁的电磁动作顺序表如下
电磁铁
动作顺序
1YA
2YA
3YA
快速下降
-
+
+
工作给进
-
+
-
快速上升
+
-
-
停止
-
-
-
表6.1电磁铁动作顺序表
液压油路分析
快进:
进油:
油液从油箱经过滤油器——油泵——三位四通右位进入无杆腔
回油:
无杆腔经过二位二通左位——三位四通右位流回油箱
工进:
进油:
油液从油箱经过滤油器——油泵——三位四通右位进入无杆腔
回油:
油液从无杆腔经过调速阀——三位四通右位流回油箱。
快退:
进油:
油液从油箱经过滤油器——油泵——三位四通左位——单向阀
进入有杆腔
回油:
油液从无杆腔经过三位四通左位流回油箱。
停止时,三位四通处于中位,二位二通处于右位,泵直接卸荷。
7液压系统的性能验算
7.1液压系统的压力损失验算
由于液压系统的管道布置长度均为确定,目前仅对液压元件进行估算
油液流经各液压元件的压力损失如下表所示
元件
Δpn(×105Pa)
元件
Δpn(×105Pa)
单向阀
0.3~0.5
调速阀
3
换向阀
1.5~3
行程阀
1.5~2
表7.1元件压力损失表
7.1.1快进
由图可知。
进油路上有电磁换向阀,其流量为155.47L/min,其进油路总压力损失为
∑Δpv=0.5ⅹ(
)2=0.472MPa
回油路上单向阀的流量为22L/min,电磁换向阀的流量均为116.59L/min,计算出有杆腔与无杆腔压力之差
Δp=p2-p1=0.5ⅹ(
)2+0.2ⅹ(
)2=0.289MPa
7.1.2工进
工进时,油液在进油路上通过电液换向阀的流量为0.471L/min;油液在回路上通过换向阀的流量是0.353L/min,在调速阀处的压力损失为0.5MPa,折算到进油路上因阀类元件造成的总压力损失为:
∑Δpv=0.5ⅹ(
)2+[0.5ⅹ(
)2+0.5]ⅹ
=0.375MPa
液压缸回油腔的压力p2为
p2=0.5ⅹ(
)2+0.5=0.374MPa
7.1.3快退
快退时,进油路上进油路上单向阀的流量为22L/min,电磁换向阀的流量均为38.877L/min。
油液在回油路上通过换向阀流量为51.84L/min。
进油路的总损失为
∑Δpv1=0.5ⅹ(
)2+0.2ⅹ(
)2=0.108MPa
回油路总压力损失为
∑Δpv2=0.5ⅹ(
)2=0.052MPa
所以,快退阶段,液压泵的工作压力Pp为
Pp=P1+∑Δpv1+∑Δpv2=0.094+0.108+0.052=0.254MPa
超过此压力时,液压泵应卸荷
7.2温升计算
由于工进的过程在整个工作工程中占百分之九十以上,故以工进时的消耗功率计算温升。
工进时液压缸的有效功率为
Pe=Fv2=
=0.025kw
液压泵输入功率Pp
Pp==PⅹQ=
=0.0283kw
发热功率
ΔP=Pp-Pe=0.0283-0.0255=0.003kw
油箱散热面积
A=0.065
=0.065
=337.7dm2=3.377m2
温升
ΔT=
==
ⅹ103=0.2˚C
此系统中,工进时的流量较低,故造成的温升很低,不用设计冷却装置
结论
通过这次对立式组合机床的液压控制系统的设计让我收获了很多,在液压系统中加入了电气控制提高了动力滑台的速度调整范围,工作适应范围更广,提高了工作效率和经济效率。
融合液压和电气控制的系统,更适应设备发展的潮流,提高了机床的自动控制程度,使机床控制灵活,性能稳定,故障减少,维修调试方便。
目前,在实际生产过程中,由于液压系统能提供较大的驱动力,且运动传递平衡、均匀、可靠及控制方便,被广泛应用于机床设备中。
通过实践证明,本文介绍的立式组合机床液压及其控制系统的设计方法,简单易行,可靠性高,对其他具有液压控制的机床设备具有一定的参考价值。
致谢
四年的大学生涯即将结束,而作为大学四年最后一门课程——毕业设计也顺利的结束了。
液压的课程设计内容在平时的课程里不作为重点,历时两个月的毕业设计并不轻松,经历着一次次修改、思考、在修改的过程后,我们学习到了很多的东西。
在此,我要感谢所有在本次毕业设计及论文写作过程中帮助过我的人,这其中有着在图书馆查阅资料时热心的图书馆阿姨,也有在设计中给予帮助的老师和同学,没有他们的帮助,就没有这篇论文的顺利成稿。
在此,我要特别感谢我的毕业设计指导老师——刘微老师,在我写论文的过程中不厌其烦的指导我,及时准确的纠正了我在初稿中的计算及设计上的错误,并在我的图书馆参考资料查阅上也给了一定的指导,这些帮助在本次论文的制作过程中都是十分重要的。
同时,也很感谢一起写论文的同学们,在制图及设计遇到困难的时候,提供了很多的帮助,他们的热情帮助,都是我在本次论文制作中最大的动力!
请允许我在此向所以在本次论文制作过程中帮助过我的老师、同学们表示最诚挚的感谢。
参考文献
1.明仁雄主编.液压传动与气压传动.北京:
国防工业出版社,2003
2.雷天觉主编.新编液压工程手册.北京:
北京理工大学出版社,1998
3.路甬祥主编.液压气动技术手册.北京:
机械工业出版社,2002
4.成大先主编.机械设计手册.单行本.液压传动.北京:
化学工业出版社,2004
5.朱梅,朱光力主编.液压与气动技术.西安:
电子科技大学出版社,2004
6.陈启松主编.液压传动与控制手册.上海:
上海科学出版社,2006
7.姜佩东主编.液压与气动技术.北京:
高等教育出版社,2006
8.左健民主编.液压与气动传动.北京:
机械工业出版社,2000
9.周士昌主编.液压系统设计图集.北京:
机械工业出版社,2003
TitleVerticaldrillingmachinecuttingheadhydraulicsystemdesign
Abstract
Hydrauliccontrolsystemplaysanimportantroleinthemodularmachinetool,afewdaysago,thehydraulicsystemiswidelyusedinmachinery,constructionandotherfields,hasbecomeanewsourceofpower.Hydraulicsystembecauseofitshighprecisionmanufacturing,cooperatewithautomaticcontrolsignal,wecanachieveatthereversing.Oilrecycling,andhasapositivesignificanceinenvironmentalprotection.
Thedesignofthehydrauliccontrolsystemisanimportantpartofmodularmachinetooldesign.Doagoodjobinthedesignofthehydrauliccontrolsystem,whichisbeneficialtoimprovetheoverallperformanceofthemodularmachinetool,andmakesthehydraulicpowercomponenteffectiveandreliableoperation.Hydraulicsystemdesignisapartofthewholemachinedesign,itstaskisaccordingtothepurposes,featuresandrequirementsofthemachine,usingthebasicprincipleofhydraulictransmission,andformulateareasonablehydraulicsystemdiagram.
Inthispaper,verticaldrillingmachinehydrauliccontrolsystemastheresearchobject,throughtotheexistingobjectiveparametertocalculate.Analysis,designedthecorrespondinghydraulicsystemschematicdiagram,coupledwiththecorrespondingtrafficloadcalculation,refertothecorrespondingmanuals,selectedallkindsofhydraulic