夹层玻璃工艺要点.docx
《夹层玻璃工艺要点.docx》由会员分享,可在线阅读,更多相关《夹层玻璃工艺要点.docx(17页珍藏版)》请在冰豆网上搜索。
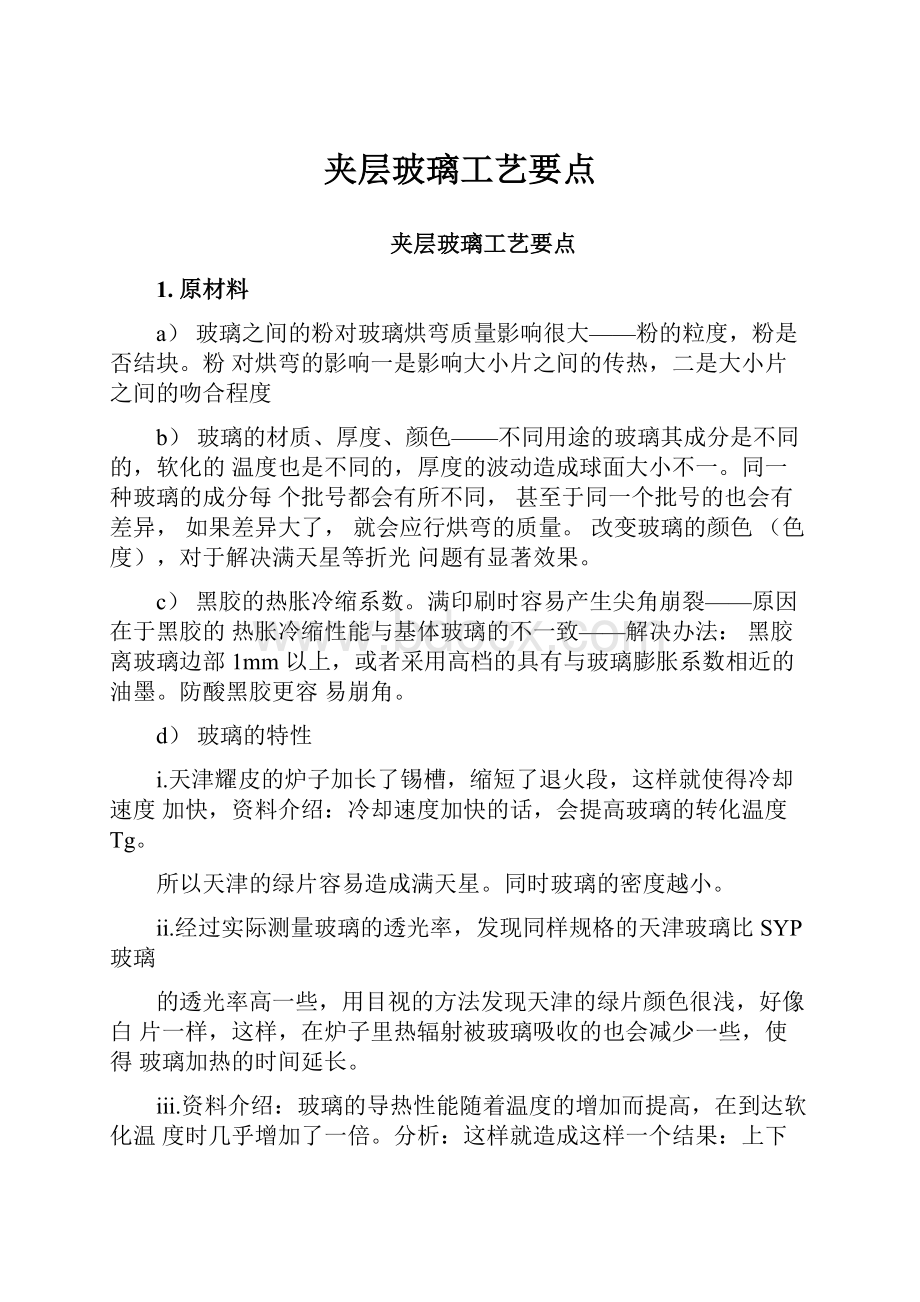
夹层玻璃工艺要点
夹层玻璃工艺要点
1.原材料
a)玻璃之间的粉对玻璃烘弯质量影响很大——粉的粒度,粉是否结块。
粉对烘弯的影响一是影响大小片之间的传热,二是大小片之间的吻合程度
b)玻璃的材质、厚度、颜色——不同用途的玻璃其成分是不同的,软化的温度也是不同的,厚度的波动造成球面大小不一。
同一种玻璃的成分每个批号都会有所不同,甚至于同一个批号的也会有差异,如果差异大了,就会应行烘弯的质量。
改变玻璃的颜色(色度),对于解决满天星等折光问题有显著效果。
c)黑胶的热胀冷缩系数。
满印刷时容易产生尖角崩裂——原因在于黑胶的热胀冷缩性能与基体玻璃的不一致——解决办法:
黑胶离玻璃边部1mm以上,或者采用高档的具有与玻璃膨胀系数相近的油墨。
防酸黑胶更容易崩角。
d)玻璃的特性
i.天津耀皮的炉子加长了锡槽,缩短了退火段,这样就使得冷却速度加快,资料介绍:
冷却速度加快的话,会提高玻璃的转化温度Tg。
所以天津的绿片容易造成满天星。
同时玻璃的密度越小。
ii.经过实际测量玻璃的透光率,发现同样规格的天津玻璃比SYP玻璃
的透光率高一些,用目视的方法发现天津的绿片颜色很浅,好像白片一样,这样,在炉子里热辐射被玻璃吸收的也会减少一些,使得玻璃加热的时间延长。
iii.资料介绍:
玻璃的导热性能随着温度的增加而提高,在到达软化温度时几乎增加了一倍。
分析:
这样就造成这样一个结果:
上下两片玻璃其中一片温度升得比较快,那么它的传热效果越好,传热效果越好又加速了温度的上升,造成两片玻璃温度相差越来越大。
iv.玻璃的热膨胀系数在(5.8〜150)*10-7之间
e)买来的玻璃不可避免带有玻璃屑,这些玻璃屑需要在洗片机内清洗掉,需要控制水温——切割玻璃的煤油需要在较高的水温下才会被融化(70~75度),另外,需要在玻璃进入洗片机之前用高温&高压的循环水喷射清洗,原片洗片机里的毛刷根本就是摆设,起不到清洗的作用(CNC洗片机的毛刷要高出辊道3mm左右)。
另外需要使用合适的清洗剂。
f)发霉玻璃的清洗。
草酸、水、乳化剂、酒精
g)玻璃上的锡点。
锡点很难在预处理前挑选出来,而且刮掉也还会有印子留在上面,合片以后看起来就像夹杂一样,有锡点的玻璃只能报废。
2.切割、磨边、印刷
a)玻璃毛坯尺寸大小,取决于设备的定位精度,一般而言长宽各增加40mm是合适的,如果设备定位精度高的话,定位精度高的话,最小边距可以减少到8mm/每边
b)冷却液的比例对磨边质量十分重要,正常的比例是1〜3%(冷却液的浓
度为20%)。
焦斑产生的主要原因是磨边速度快,在砂轮与玻璃摩擦处产生高温,高温将水气化,气化的空气泡阻止冷却水与砂轮的接触,又进一步推高了温度。
好的冷却液可以大大提高冷却水气化的温度,进而提高磨边的速度。
但是据了解,很多公司都是用的自来水,采用一个大的沉淀/过滤池过滤掉玻璃粉后重复使用的方式。
冷却液比例过大,不太容易清洗干净,容易在印刷后形成水渍印。
c)冷却水最好使用离心机将玻璃粉等杂质离心掉,这样冷却水中杂质很少,冷却效果好。
沉淀池效果要差很多。
d)玻璃清洗机中有风刀的几个辊道对玻璃的清洁有很大影响,尤其是上辊道必须保持清洁。
要想办法制造一个对上辊道进行自动清洁的装置。
e)解决黑胶中的“浅色亮团”——有人说是水迹印,有人说是霉斑。
可能的原因:
i.发霉的霉斑。
应当出现没有规律。
解决办法:
用药水清洗(草酸、酒精、活性剂、水)
ii.水迹印。
一般有规律地出现。
一般的原因:
1.水没有吹干净——风刀的压力、空气是否干净
2.切割油、冷却液等粘在玻璃上,油脂不容易洗干净。
这种水渍印的特点是:
水渍印比较严重,形状上基本上是直径2〜4mm的
园点成团出现,分布范围局限于玻璃周边30mm以内(偶尔会局部冲到里面去)
3.水滴滴在印刷后的黑胶上(两面都可以看得见)
4.洗片机前面的辊道上或者吸盘上贴了胶布,夏天时胶会漾出来,粘到玻璃上,然后又粘到洗片机的辊道上,洗片机的上下辊道是可以相互接触的,可以从下辊道传染到上辊道,污染后面的玻璃。
5.水脏——过滤网是否及时更换,保持一定的溢流。
6.辊道上结了“垢伽”,印到玻璃上。
主要检查上辊道是否干净。
7.解决办法:
a)吹干前使用去离子水清洗玻璃。
b)清洗剂的毛刷高度调节。
保证解除玻璃2mm左右,如果毛刷调整过度,会造成压伤玻璃,则应当更换毛刷。
c)降低冷却液的浓度;更换切割油等。
d)增加最后一道清洗水的溢流量。
e)提高去离子水温度,但与上面一条受到设备加热能力的制约。
个人设想的理想的清洗过程:
洗片机前先设置一个循环水箱,该水箱要能把水加热到70C以上,使用高压泵将热水喷射到玻璃的上下面,目的是把玻璃加热,将附在玻璃表面的油污软化以利于后面洗片机毛刷能够把油污、玻璃屑等去除干净(玻璃屑一般是被煤油粘在玻璃上的,时间长了煤油干了,不容易洗掉),同时,该水箱必须采用耐腐蚀不锈钢,以便添加洗发霉的药水——如果加了药水,需要再加一段冲洗喷淋装置;然后再进洗片机用毛刷清洗,此时的水温不要太高(40〜50度为宜),水温太高的话会导致毛刷太软,不利于清除顽固的垃圾。
最后一遍清洗必须用去离子水,否则玻璃上会遗留不良的离子。
f)使用专用玻璃清洗剂
f)印刷。
i.玻璃的非锡面容易发霉,所以黑胶最好印在锡面上。
ii.宽一点的网框(两边宽出刮刀各30cm以上),可以减少网框刮裂的
几率。
iii.满印刷的玻璃容易出现印到玻璃R边上的情况,要特别注意定位准确。
iv.进入印刷位置前,玻璃的温度最好降下来,这样可以防止黑胶受热挥发,将丝网孔堵塞,造成局部漏印。
v.湿胶厚度一般要求在20卩左右,即可满足透光率1%的要求。
实际
上只要遮蔽性符合要求,厚度越小越节约成本。
但是对国产黑胶要注意,湿胶厚度太薄的话容易印得颜色不均匀。
但是对透光率要求0.1%的产品,要增加湿胶的厚度到30〜40卩、同时粘度要高一一丝网要使用目数较低的丝网,才能满足要求——带来的问题是细线会断线或呈锯齿状,黑胶边缘会呈锯齿状,成本也会大大增加。
g)喷粉的粒度:
一般情况使用250目,特别情况使用300目,但是300目的容易造成玻璃内划伤。
h)要特别注意洗片机的滚道、喷粉机辊道、印刷机辊道等,这些辊道经常会发生其中几个不转的现象,造成玻璃伤。
3.烘弯
a)玻璃的变形是在各种温度条件下都在进行,只不过是进行的速度快慢的问题。
温度高则需要的时间短,温度低则需要的时间长。
玻璃的厚度,当厚度超过3mm时,玻璃越厚,需要的加热时间越长,但是当玻璃比较薄时,越薄需要的加热时间越长——一部分热量穿过玻璃而去。
b)汽车风挡玻璃经常会有两片不同材料的玻璃一起烘弯,要么厚度不同,要么颜色不同。
通常会将有颜色的玻璃放在下面(作为大片),据说有颜色的玻璃吸热量大,容易软化,这样就不会造成两片玻璃压得太紧,而产生折光。
如果是A绿跟F绿搭配,要把F绿作为大片;同样都是一种颜色时,应当把厚的作为大片。
但是,由于两片玻璃成分不同,软化点温度必定会不同,如果两片玻璃软化温度相差太大的话,是很难同步成型的。
c)在烘弯炉中主要是依靠热辐射对玻璃进行加热,由于玻璃传热性能不良,受到辐射的一面玻璃膨胀,造成玻璃翘曲变形,变形的结果又造成大小片之间局部接触过紧,传热较多,而其他部位悬空,大小片之间很少传热,最终造成小片有的地方与大片较贴合,有些地方悬空,造成折光。
d)玻璃的自重也是影响成型的原因,有时候大片玻璃加厚了,在同样的工艺参数条件下,玻璃升温慢,理应球面变小的,但是由于其自身的重量增加了,球面仍然会保持基本不变。
e)冷却风力越大,玻璃的压应力越大。
f)大小片之间的粉的数量不均匀,会造成大小片之间传到热量不均匀,有时候由于大小片玻璃的软化特性相差很大,可以通过增加中间的粉的数量,减少大小片之间的传热,达到分别控制大、小片软化弯曲的目的。
如果粉太少的话,容易形成内划伤。
g)随着玻璃加热时间的推移,玻璃的中部逐渐向小车的底部移动,两个侧边逐步上翘向小车的顶部移动,会对玻璃的变形产生影响。
例如:
玻璃的两侧向顶部加热靠近后,玻璃更加软,容易形成网布印;玻璃的中部远离顶部加热后容易形成“平底锅”现象。
h)在玻璃与电热丝之间,如果有其他物体的话,会对玻璃成型带来不利影响。
实践中常常利用此特点改变玻璃的加热效果。
i)电热式的形状、分布、功率分配、电热丝之间的间隔距离等,会影响玻璃的形状。
i.电热板的性能会有差异(加热板本身的吸收热量、传导热量会有很大差异),尤其是更换了电热板以后要验证是否有变化;
ii.同一个加热室内不可能左右对称,不同的加热室也不会发热量的分布完全一致。
iii.随着时间推移,红外传感器检测到的温度也不会恒定一致,尤其是更换了测温探头或清洁了测温探头以后,要重新验证温度——粘在探头上的灰尘会使测温失真。
iv.由于在11区以前,玻璃每个部位的加热已经有差异了,因此在11区测得的玻璃温度只代表了玻璃的局部温度,其他部位的温度很可能是不一样的。
v.当模具增加铁板/减少铁板时,采用同样的加热工艺参数时,加热时间会发生变化,此后应当重新调试产品工艺参数,慢慢提高产量。
j)预热区的温度控制。
0区、1区温度不要一下子提得太高,一方面玻璃温度不可能跟随得上,浪费能源,另一方面也容易造成玻璃裂。
3〜6区提
高温度有利于缩短节拍时间,也可以解决成型区温度微调问题(满天星)。
所以,玻璃的成型并不是到了11区才开始变型的,而是进入成型区就开始局部变形了,一定要充分利用中间几个加热区的温度控制作用。
在工作重要密切关注满炉运行时每个小车的循环时间、温度是否均匀,如果循环时间相差超过20秒,肯定有问题。
理论上来讲,对于采用同样的工艺参数的产品,如果前一车加热时间很长的话,随后的几车加热时间应当减少,但是实践中往往不是这样。
4.烘弯模
a)模具与检具的配合
i.一般情况下,模具的边框外部比检具外部小1~2mm,模具大头的中部比检具的大头中部凹1mm左右,模具的小头中部比检具的小头中部凹2~3mm左右,两侧边中部凹1mm左右。
ii.如果检具有销钉,且销钉离玻璃边缘比较远的话,模具的边框也要比检具的边框小5~7mm左右,这样有利于玻璃边部的吻合度。
iii.将检具倒扣在模具上时,四个砝码的限位螺栓与限位块的距离大约2mm。
iv.要适当考虑模具的热胀冷缩,同时考虑产品的球面大小,如果球面小的话,不锈钢框架就不能太大,否则玻璃容易滑脱,但是太小的话又会造成网布印超过6mm的规定。
边框采用5mm的不锈钢板比3mm的不锈钢板强度要好,热稳定性好,吻合度不会随时间而变化。
b)对于球面比较大的产品,要采用两步成型,有利于减少荷叶边。
c)不锈钢边框可以用3mm的,也可以用5mm的,宽度越厚,与玻璃的接触面积越大,模具印越轻。
但是,由于冷却的时候不锈钢比玻璃冷却的快,也更容易造成玻璃在炉子里炸裂。
为了减轻模具印,需要在成型边框上包网布。
5mm边框比3mm边框的模具冷却时间稍微慢一点(不锈钢体积大),对玻璃的应力有好处。
d)模具的变形。
在烘弯的过程中,玻璃对模具边框施加的力量,在水平面上有一个将边框向四周推的分量,这样,模具用的时间久了,边框会越来越大,尤其是3mm的边框,变形会比较快。
另外,对于有关节的模具,在玻璃刚放到模具上时往往只有6个点接触——4个关节加大头边2个点,也就是说每个可以翻转的侧边边框只接触了一个点,时间长了以后容易引起模具变形,尤其是大玻璃。
e)模具使用的钢材越少越好,钢材越多,吸收的能量越多,造成总的电费增加。
但是带来的问题是模具的强度降低,容易变形,稳定性差。
f)飞机。
模具上的层叠铁板是为了吸热,在铁板附近的玻璃会比较平一点(据我分析,加铁板的目的是为了挡住底部加热对玻璃的直接辐射热量)。
但是在靠近铁板的边缘处的玻璃上,容易形成一条亮线。
在模具中放一块石棉,可以给玻璃加热,此处的玻璃弯曲的会多一点。
有时候也会把飞机加到成型框的外面,以减少玻璃的折光,但是吸热的效果要差一些。
但是,现实的模具中,所加的铁板的边缘,放在小车里后,刚好位于底部加热电热丝的空挡上,经常会形成“铁板上方一条凸带,电热丝空挡上方一条平带”的局面,也许把模具沿对称轴线移动一段距离可以解决。
在MG3的角部反翘改进中,采用了两个方案,一个是在角部加了一大块石棉(200*200*20的一半),结果玻璃马上凸出的很厉害,造成了相邻的边缘出现荷叶边;另一个是把模具内腔的铁板从距离侧边大约250mm,加一块铁板延长到侧边边部,结果玻璃也凸出来了,角部由反翘变成了正翘——但是此现象与铁板是吸热的作用相矛盾。
g)关于铁板:
i.层数,一层至三层,但是实际上看到SUPERBt三层铁板,但是铁板上部的玻璃仍然弯曲很厉害。
ii.宽度:
小的有2公分,宽的有10公分,厚度在0.5公分左右。
iii.安装斜度:
有的是平行底部加热板的(一般都是窄的),有的下垂30〜40度的样子。
iv.铁板的组合,可以单独放在模具的内腔或单独放在边框外边,也有在内腔放一条20mm的铁板,外面放若干层宽铁板。
h)在玻璃的四个角部通常玻璃很难软化弯曲,为了保证形状,需要用石墨压在玻璃的上面,稍微施加一点压力。
另外可以在角部加一块小的三角形石棉板,也可以解决——石棉板大了的话会造成角部荷叶边。
i)1号炉的模具成型框距离底框比较远,因为它只有顶部加热,最终只能成型“平底锅”形状的玻璃。
其他炉子模具成型框距离底框比较近,因为要使用底部加热。
球面比较平顺(球面小或者曲率半径大)的产品,
在2、3号炉子中容易大小片滑得错位,必要时应当在玻璃边部增加石墨挡块或者陶瓷挡块(陶瓷比较厚的话容易造成玻璃爆边,需要在陶瓷外面包网布防止爆边),以限制玻璃相互滑动。
必须注意的是:
石墨很容易被玻璃磨出凹坑,磨出的凹坑会造成大小片没有很好地贴合在一起,或者石墨的粉末垫在大小片之间,造成吻合度超标或合片后PVB气泡。
经试验,采用陶瓷管容易造成玻璃局部爆边。
据了解福耀采用的是微孔陶瓷做定位块。
j)一组烘弯模一定要做到一致,否则炉子上没有办法生产。
i.在烘弯模加工过程中,如果采用冷作,则必须所有部件都采用冷作,如果采用热弯,则必须都采用热弯,否则,模具进入炉子中走几圈以后,应力释放不一样,会造成成型框变形,而且会在一段时间内不断变形,很难修正过来。
ii.用的钢板材料最好同一批次的,原因同上。
特别强调的是膨胀系数和热变形量。
iii.模具与炉子小车位置的定位一定要准,否则容易造成不同的小车中电热丝与玻璃的相对位置不统一,从而造成玻璃的型面不一致。
k)模具要做到水平——玻璃放在模具上,应当尽可能水平,这样顶部加热会均匀地给玻璃加热,如果不水平的话,靠近顶部的地方加热块,远离顶部的地方加热慢,造成玻璃球面不均匀,甚至满天星。
一般做法:
以四个开口为基准点,四点保持同样的高度,四个开口的高度12〜15cm(视设备情况定,ESU大约28cm)。
l)模具的维护:
通常模具上应当包网布,而网布的接头要放在上下边——因为通常情况下上下边的温度会比较低一点,两侧面温度会比较高一点。
接头放在两侧面的话,容易形成黄豆大小的印子。
另外,时间久了以后粉笔末、玻璃粉等杂质会烧结到不锈钢框架上,造成网布印,所以要定期地抛光不锈钢框架。
m)
5.合片、高压
a)玻璃必须使用去离子水清洗——在CNC处最后一道清洗必须是去离子水,因为普通自来水的钙离子等离子影响PVB与玻璃的粘接。
玻璃的热膨胀系数比PVB小1000倍,在受到高低温变化时,容易形成差动位移,继而产生剪切应力使得玻璃脱胶。
b)隔音PVB
i.本身是三明治结构,中间的隔音膜容易与上下两层PVB之间形成气
泡(中间的隔音膜硬度和熔点比PVB低)。
首诺厂家建议初压温度提高到140度(普通最高138度),高压釜温度提高到145度(普通最高140度),通过提高PVB的流动性来解决问题。
但是这些气泡的空气是从哪里来的?
而积水厂家建议在初压机的恒温段降低温度到8
0〜90度,时间不少于20分钟,以利于空气的排除;在高压釜中冷却到35度以下再放气,同时放气要慢慢地放(安装一个限流阀)。
ii.按照供应商的意见,解决隔音PVB的气泡问题要采取以下措施:
1.合片之前最好用去离子水清洗一遍,最少也要用无静电布擦去玻璃上的粉等物质。
2.合片、套真空套管时环境温度最好在18C以下。
3.延长在初压机机里抽真空的时间,正常速度的60%左右(每小时60〜70片)。
4.确保真空套管没有漏气。
必要时采用大通道、厚截面的真空管。
5.初压后,高压前,使用磷酸三丁酯(C12H27O4P)――简称TBP,用注射器打在两侧边的PVB与玻璃的两个夹缝中,让TBP自然流淌下去,此方法效果最好。
6.高压釜的温度提高到140〜145C(普通PVB138C),降温、降压到35C以下才可以开始放气,放气要尽量缓慢(必要时安装
放气的节流阀一一普通PVB5分钟放光,隔音PVB要放30分钟)
7.更换成不同纹路的PVB。
8.个人以为:
a)空气或水分没有被排除干净。
隔音PVB气泡也是主要出现在玻璃边缘部位,说明总的合片、高压工艺是可以的,关键在于在高压釜中高压过程中,在玻璃的边缘部位,由于此处是开口的,玻璃对PVB的挤压力比较小,残留在PVB中的空气在高压下被压缩,一旦高压卸去就会恢复原状——而处于玻璃中间的气泡由于周边PVB的粘接力量作用,就无法恢复原样。
这种情况下,封闭油也许是最好的解决方法。
b)玻璃大小片的贴合程度不好。
大小片玻璃在边缘处总会有些不贴合,在高压釜中受到中间部位的玻璃相互压紧的影响,也会相互靠拢,把PVB向中间挤,一旦出了高压釜,这些部位又会回弹开来,这样就把PVB“撕裂”了,空气就进来了。
又由于隔音PVB是三明治结构,更容易被“撕裂”。
c)PVB可以拉伸10%使用,不影响安全性(宽度要适当加宽)。
但是隔音PVB要注意,过度拉伸会破坏隔音膜的结构,在打折光房间将玻璃抬
至V靠近白板的地方可以清楚地看到隔音膜的结构。
另外,隔音PVB不能折叠、划伤,否则会在玻璃上留下痕迹。
d)总的来讲,首诺的PVB要比积水的好,气泡少。
曾经发生这样的事:
积水的PVB气泡很多,来不及返泡,放了将近2个星期,结果气泡自己消失了。
后来在夏天高压积水的PVB时,在正常高压程序结束后,再用1.2〜2个大气压,38-40C条件处理30分钟,结果气泡大大减少。
e)气泡问题解决:
i.夏天时节初压气泡多。
夏天的时候,夏天空气中的水气,在玻璃上
附着了大量的水气,很难把这些水气清除掉。
合到PVB里,时间久
了就会返成气泡,为了减少玻璃上附着的水气,首要条件是保证合片室的温度、湿度越低越好,其次,在上片之前要准备4车的玻璃提前放到空调上片间冷却,降低玻璃的温度。
如果玻璃温度比较高,PVB上的花纹贴合在玻璃上后,很快就融化掉了,就没有了空气排出的通道。
ii.PVB拆封后放的时间太长,PVB吸潮(尤其是边部更容易吸潮)。
所以必须控制好PVB的存放条件和时间。
iii.另外就是保证抽真空的真空度和时间、温度。
个人理解:
应当适当降低初始段的温度,以利于空气的排除。
这里需要注意的是:
抽真空主要是抽去其中的空气,但是并不能抽去其中的水汽,要想抽去水汽则希望温度稍高一点。
所以,两者是相矛盾的。
iv.初压后的玻璃要及时进高压釜高压,否则在外面放得时间长了后,
空气中的潮气进入PVB的边缘,就容易引起气泡。
厂家介绍:
PVB只有在大于135度,高压状态以后,组织结构发生变化,特性改变,才能稳定下来,不再受水汽的影响,在此之前,吸水性很强的。
v.玻璃烘弯的质量。
烘弯的大小片边缘贴合程度差的话,会造成高压后玻璃边缘的气泡。
特别要注意用了石墨挡圈的玻璃,石墨挡圈磨损后形成的凹痕会造成此处大小片不贴合。
vi.玻璃上有脏东西,脏东西阻止玻璃与PVB的链接,形成气泡。
vii.返泡后的部位容易回弹,再次形成气泡。
实践中发现:
一些小气泡,不去管
它,存放一段时间后,气泡自然消失,一点也看不出痕迹。
viii.如果玻璃出现靠近中间部位的气泡,很可能是初压机的真空管漏气,初压时空气憋在玻璃中,高压釜中虽然强行将玻璃与PVB粘合在一起,时间留了以后气泡自己慢慢又聚集在一起了。
ix.真空管子的截面形状需要改进,增加与玻璃贴合面的面积,减少漏气。
用依维柯的大截面的管子效果就是好些。
f)高压釜用的小车:
在保证结构强度的前提下,尽量少用材料,因为这些材料也是要吸收热量的,会增加高压釜的能源消耗。
隔开玻璃的插件要用阻燃塑料或木头。
插件要用铁杆压紧,目的是防止在叉车运输过程中插件自己跳出。
另外,片与片之间的距离要合适,以便每车多放几片玻璃。
g)有时候,玻璃从高压釜出来后,可以看见很多的封边油聚集在玻璃上,如果在出缸之前,这些油被风机吹到电加热丝上,就会造成烧缸。
尤其是隔音pvb其中的增塑剂比较多,容易挥发出来。
h)高压釜冷却散热器漏水,漏到高压釜内部,会造成气泡增多。
i)玻璃上的锡点常常会被认为是夹杂,在放大镜下观看,锡点是有金属光泽的,线头则是纤维状的。
j)玻璃进入合片室前,对玻璃要进行清洁,最好是采用唐纳利喷砂机器一样的机械,通过高压气体吹掉浮灰,同时马上吸走。
现有的清粉机该清理的地方都没有清理到。
烘弯缺陷的解决方案
1.崩角
a)崩角的机理主要是因为玻璃局部收缩不均匀造成的。
同时,由于大片的面积比小片的面积大,在玻璃弯曲后,大片对小片有一定的挤压力,所以,一般崩角都是在小片上。
b)具体原因:
i.黑胶满印刷。
黑胶的收缩率与玻璃的收缩率不一致(一般而言,玻璃的热胀冷缩为83〜89,黑胶为79以下)。
需要扩大黑胶边缘与玻璃边缘的距离。
ii.玻璃角部太尖。
一般的黑胶印刷的最小R>4,防酸黑胶R>6。
iii.玻璃直接接模具边框,同时成型后冷却速度过快。
需要降低冷却风机风量。
并不是不包网布就一定会崩角。
iv.玻璃退火不良。
v.CNC磨边产生应力。
vi.奇怪的是,同样的玻璃,同样的工艺参数,每批不一样,甚至同一批在不同的时间段也不一样,有时候严重,有时候没有崩角现象。
c)解决办法:
i.降低冷却风机的风量,但是不能随意调整应力风机的风量。
ii.改变角部R大小。
提高磨边质量。
iii.更换玻璃厂家。
iv.增加玻璃之间的粉量,对改善崩角没有意义。
v.模具的边框改用厚一些的边框,厚边框降温慢,冷却过程中与玻璃温差变化较小。
2.反翘
a)反翘一般发生在角部,是由于平面玻璃变成立体玻璃时,玻璃的挤压造成的,角部受到两个方向的挤压——也就是材料堆积,容易造成反翘。
b)解决办法:
i.烘烤时局部热量控制,对角度增加加热热量
ii.修改模具的角部——下凹。
使玻璃向凸面凸起,变成正翘。
iii.在角部压衬了石墨块的重物。
需要注意会有压块的痕迹
iv.在角部使用石棉材料增加角部的温度。
v.在角部加铁板。
像