车间工艺管理规定.docx
《车间工艺管理规定.docx》由会员分享,可在线阅读,更多相关《车间工艺管理规定.docx(14页珍藏版)》请在冰豆网上搜索。
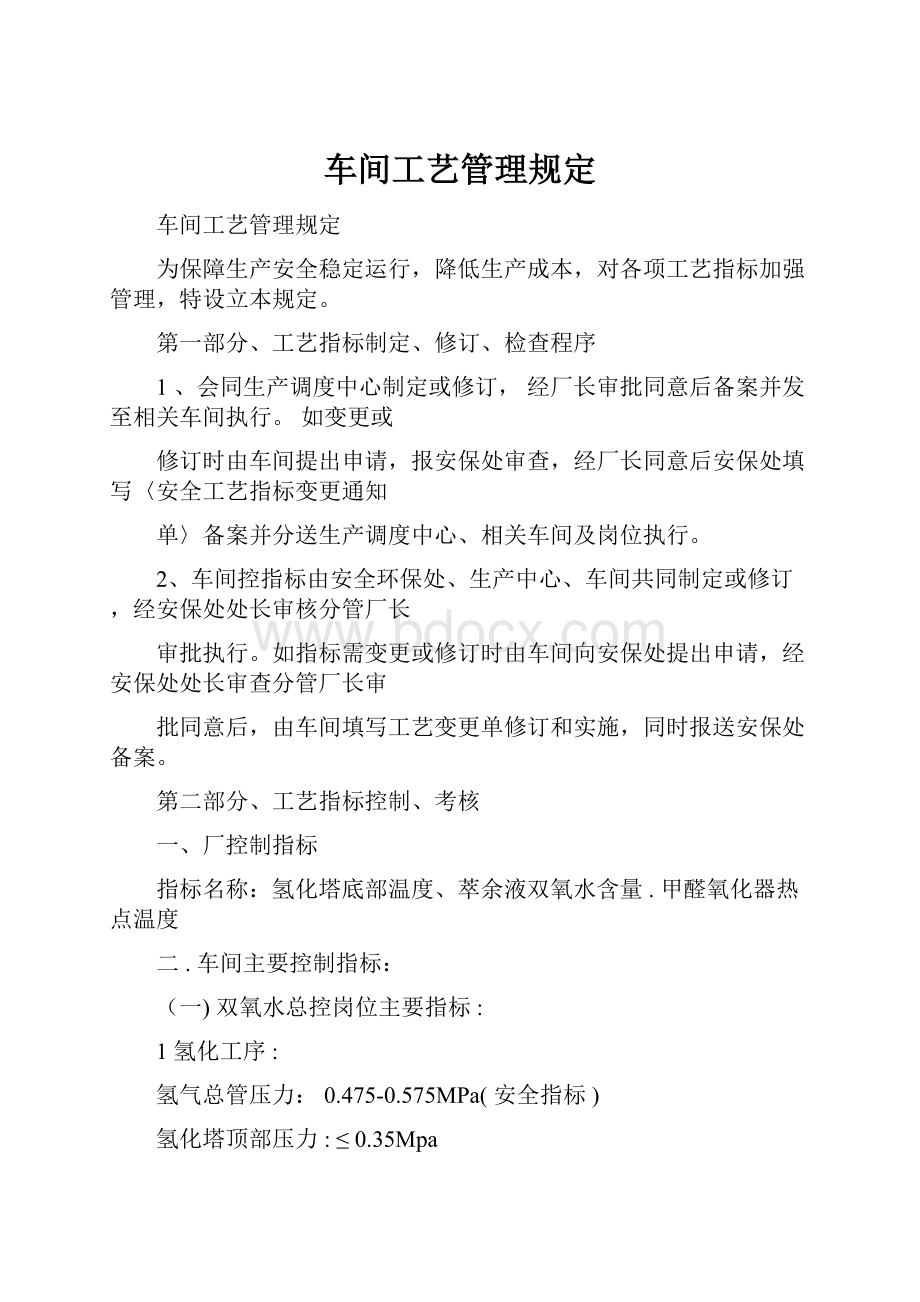
车间工艺管理规定
车间工艺管理规定
为保障生产安全稳定运行,降低生产成本,对各项工艺指标加强管理,特设立本规定。
第一部分、工艺指标制定、修订、检查程序
1、会同生产调度中心制定或修订,经厂长审批同意后备案并发至相关车间执行。
如变更或
修订时由车间提出申请,报安保处审查,经厂长同意后安保处填写〈安全工艺指标变更通知
单〉备案并分送生产调度中心、相关车间及岗位执行。
2、车间控指标由安全环保处、生产中心、车间共同制定或修订,经安保处处长审核分管厂长
审批执行。
如指标需变更或修订时由车间向安保处提出申请,经安保处处长审查分管厂长审
批同意后,由车间填写工艺变更单修订和实施,同时报送安保处备案。
第二部分、工艺指标控制、考核
一、厂控制指标
指标名称:
氢化塔底部温度、萃余液双氧水含量.甲醛氧化器热点温度
二.车间主要控制指标:
(一)双氧水总控岗位主要指标:
1氢化工序:
氢气总管压力:
0.475-0.575MPa(安全指标)
氢化塔顶部压力:
≤0.35Mpa
▲氢化塔底部温度:
45—55℃(初期)、55—65℃(中期)、65—70℃(后期)(关键控制点)
氢化效率:
6.8-7.5g/l
氢化液气液分离器液位:
25-45%
氢化尾气氧含量:
≤1%
氢化液流量:
185m3/h±3
2氧化工序:
氧化尾气压力:
≤0.25MPa
氧化尾气回收蒸气压力:
0.20-0.35MPa
氧化尾气回收缓冲器后压力:
≤0.025MPa
氧化尾气氧含量:
6-11%
氧化塔上节温度:
52-58c?
氧化塔下节温度:
52-58°c
氧化塔上节空气量:
3500-4300m3/h
氧化塔下节空气量:
1800-2400m3/h
氧化液酸度:
0.003-0.008g/l(安全指标)
氧化液气液分离器B:
20-45%
氧化液流量:
185m3/h±3
3、萃取工序:
萃取浓度:
303-312g/l
萃余液H202:
≤0.3g/l(安全指标)
萃取塔顶部界面:
60-90%
净化塔底部界面:
50%±5
4、后处理工序
工作液计量槽液位:
30-50%
干燥塔界面40-70%
氢化液氧化液工作液储槽液位:
25-50%
稀碱比重:
1.28-1.35g/l
工作液水分:
≤3ml/l
工作液流量:
185m3±3
工作液双氧水含量:
≤0.1g/l(安全指标)
(二)泵房岗位:
浓碱比重:
1.38-1.42g/l
氢化液过滤器进口压力:
≤0.12MPa
纯水加磷酸量:
1500ml/槽
纯水酸度:
0.4-0.5g/l
浓碱槽液位:
30-90%
稀碱槽液位:
30-90%
废工作液槽液位:
≤200cm
氢化液汽液分离器液位:
70-100cm
净化塔底界面:
50%
氢化液再生床流量:
10-25m3/h
后处理白土床排污:
1次/h
稀品槽稳定剂加入量:
50-150ml/每槽
蒸汽总管压力:
≤0.6MPa(安全指标)
碱蒸发器进口蒸汽压力:
0.1-0.25MPa
(三)配置岗位
1工作液配置加料:
芳烃3.36m3
磷酸三辛酯1027kg(5.7桶)
EAQ650kg(26袋)
2工作液清洗:
清洗后双氧水含量小于0.1g/l
3芳烃蒸馏条件:
蒸汽压力制0.4-0.5MPa
釜内真空度0.06-0.08MPa釜内液相温度125-135?
c
4工作液碱洗
氢氧化钠溶液配比30%NaOH75L
纯水25L
加热温度70-80C?
加热时间1小时
(四)空压机岗位
(3)空压机
一级出口压力≤0.2Mpa
二级出口压力≤0.75MPa
一级出口温度≤165c?
二级出口温度≤165c?
润滑油压力>0.3MPa
(4)冰机
出口压力≤1.6MPa
出口温度≤150c?
(5)循环水
循环水上水压力大于0.3MPa
循环水上水温度小于35c?
(6)制氮
空压机出口压力1.25MPa
空压机出口温度165c?
入膜温度45-50c?
入膜压力118-12.5bar
出膜温度35-40c?
出膜压力8.0bar
氧含量小于20000ppm
氮气储槽氧含量:
小于2%(安全指标)
氧分析仪取样参数:
压力86-105kpa
流量150-300ml/min
(五)甲醛总控主要工艺指标:
1、甲醛岗位
▲氧化炉温度:
620℃-670℃(关键控制点)
安全指标:
蒸发温度42-50℃
平衡浓度>90%
氧化汽包液位10-40%
尾锅汽包液位10-40%
过热温度103-130°c
蒸发器液位50%±5
氧醇比0.38-0.41
配料浓度56-60%
氧化汽包压力小于1.25MPa
尾锅汽包压力0.3-0.4MPa
一塔顶温度小于50c?
三塔顶温度小于35c?
甲醛含量36.5-37.4%
酸含量小于0.05%
一塔底液位50%±5
罗茨风机油位1/2
(六)托品岗位主要工艺指标:
▲反应温度50-75℃(关键控制点)
蒸发锅温度70-85℃
膜式蒸发器温度70±80°c
蒸发锅真空度-0.030―-0.007MPa
膜式蒸发器真空度-0.030―-0.007MPa
氨过量1.0-2.5%
蒸发锅液位1/2(以中视镜为准)
浓缩液浓度大于38%
三、工艺指标的考核:
各项工艺指标考核采用月底合格率累记汇总计算合格率,记录指标采取管理人员抽查
制度,月底合格率>95%统计。
考核办法及奖惩:
1、厂控指标(氢化温度.萃余.氧化器热点温度):
(1)、萃余考核按照合格率进行考核,以厂审核统计合格率为准,合格率95%每降低1%,扣
罚20元,落实到班组并加扣班组分1分。
(2)、氢化温度考核按照自动记录仪表记录数据进行统计,实行班组竞赛,以厂审核统计合
格率为准,排列名次,按照厂规定进行奖励
A、全部合格率均达到指标时,按照合格率高低进行奖励如下:
第一名奖励60元第二名奖励50元第三名奖励40元第四名奖励30元。
B、合格率低于95%时,扣罚班组20元,并每降低1%扣罚每班加扣4元。
第四名加扣30元。
(3)、甲醛氧化温度考核按照DCS记录数据进行考核,实行班组竞赛,以审核统计合格率为
准,排列名次,按照厂规定进行奖励
A、全部合格率均达到指标时,按照合格率高低进行奖励如下:
第一名奖励150元第二名奖励100元。
B、合格率低于95%时,扣罚班组20元,并每降低1%扣工艺分1分。
2、车间控制指标合格率每低于指标1%,加扣班组工艺分1分。
车间主要考核指标:
(1)双氧水:
氢化效率、氧化温度、萃取、氧化酸度
(2)甲醛:
甲醛浓度
(3)托品:
反应温度、过量氨
3、安全指标:
每超一次扣工艺分0.5分,并落实责任人50-100元/次。
造成减量或停车者按
事故处理,严重超标引起安全事故发生的,按总厂处理意见执行。
4、班组出现工艺指标超标严重或出现大幅波动时,当班下班前以书面形式写出反馈到车间,
不反馈或反馈不及时者按工艺事故处理。
5、工艺事故扣指标分2-10分(视情况轻重定),并扣罚当班人员50-200元
6、无纪录仪记录的工艺指标,车间管理人员每天抽查不少于2次,发现超标时扣工艺分0.5
分/次,厂检查出现工艺问题时,扣罚当班2分/次,并纳入合格率统计。
7、出现重大事故时按照车间及集团有关规定执行。
8、遇到停车情况,必需按规定进行处理,停车时出现异常情况纳入考核。
9、开车考核范围:
短停4小时后;长停16小时后开始纳入考核,出现特殊情况适当延长时
间。
10、萃取液双氧水含量交班后2小时内数据按交班者控制进行统计考核,交班数据不合格扣工
艺分0.5分,连续不合格加倍扣罚以下情况按质量事故处理:
萃取含量低于指标4g/l以上(含
4g/l),.或连续4小时以上不合格(含4小时,包含中间出现短期合格数据)达到合格率的班组
参加车间质量评比将.
16、出现质量事故扣罚主要责任班组班组考核分5分,工长考核分10分,主操100元.次要班
组班组分3分,工长考核分5分,主操50元.情节严重者,安车间或总厂意见处理.
17、各项工艺指标考核以上述规定指标进行考核,如有变动以《工艺指标变更单》为准进行
考核。
四分析项目管理规定:
1、各个分析项目得分析频率如下
1.1双氧水:
(1)氢化效率2小时/次,双点取样
(2)氧化效率2小时/次.单点取样
(3)工作液中双氧水含量,4小时/次
(4)氧化液酸度,1小时/次
(5)萃取液浓度,1小时/次
(6)萃余液H2O21小时/次
(7)工作液碱度2小时/次
(8)碱分离器后碱度每班一次
(8)萃取酸度8小时/次
(9)氧化尾气氧含量8小时/次
(10)氮气中氧含量每8小时一次
(11)纯水酸度2小时/次随机抽查
(12)双氧水稀品计量槽浓度每槽一次
1.2甲醛项目
(1)甲醛计量槽含量每班两次
(2)甲醛采出浓度每小时一次
(3)甲酸含量每小时一次
(4)甲醇含量每小时一次
(5)二塔.三塔甲醛含量每班一次
(6)蒸发器平衡浓度2小时一次
(7)尾气CO.CO2.O2含量8小时一次
1.3托品项目
(1)托品含量每班一次,水分每班一次
(2)过量氨每班一次
2保证分析频率,按时取样,发现不按时取样者扣20元/次.
3取样时间统一规定为整点取样.
4取样后要及时分析,半小时后应报告分析结果,要分析准确,发现异常情况要重新分析,两次
结果均应报主控室.
5分析数据无论高低,均应据实记录,严禁弄虚作假,发现更改原始数据或填写不真实或中途换
表纸重抄者,一次扣100元,情节严重因分析数据误导造成事故者,负主要责任.
6对总控提出加作项目要及时分析,及时报告结果.
7严格尊守约交接班制,因交接不严造成问题,由接班者负责.
五以上考核自下发之日起执行,原先车间制度仍有效,和本制度相抵触部分以本制度为准。
工艺指标如有变更以《工艺指标变更单》为准。
六工艺排污管理:
为加强操作人员的责任心,严格排污制度,以保障安全稳定运行各排污点排污严格按制度执
行.
1双氧水系统各点排污每小时一次,氧化塔排污每班2次,间隔4小时,必要是增加排污次数.
2双氧水各排污点按时排污,保持各视盅界面,排污时勿将工作液排出不及时排污者,发现一
次扣20元,排除工作液者,发现一次扣50元,情节严重者,按事故处理.
3因操作不当造成跑料或带水现象者一次扣50元-100元,情节严重者按事故处理.
4空压机出口空气缓冲罐排污每小时一次
5甲醛氧化汽包,尾锅汽包排污2小时一次,工长负责.
6蒸汽分配器排污每小时一次
7蒸汽过热器排污每小时一次
8空气缓冲罐排污每小时一次
9蒸汽总管排污每小时一次
10托品超滤,氨过滤器排污每班一次,蒸汽分配器排污每班两次.
11各处排污要按时,如发现不按时按规定排污者,一次扣20元.
七、本规定自下达之日起开始执行。
以前规定中凡与本规定有冲突时,以本规定中条例为准。
第三部分明泉车间记录规范化要求
记录表(本)是车间为生产调节提供数据的重要原始记录,记录表(本)的规范化也代表
了车间的部分形象。
针对目前记录表(本)的检查情况,特制定如下要求:
一、记录时间要求:
1、记录周期为一小时,接班后整点做第一次记录,以后每隔一小时记录一次,记录时间为
整点前后10分钟。
除因系统开停车及大幅度加减量等特殊情况外,都必须准时记录。
2、分析记录时间及报总控时间氢效一小时内报结果,其余数据为半小时以内,超过时间不
报或无记录视为超时记录
3、凡超时记录者发现一次,扣30元。
二、记录真实性:
1、填写数据必须真实,不漏项,如因仪表误差或仪表失灵等原因无法记录,必须在备注栏
注明,不注明者视为记录不真实。
2、凡记录数据与实际数据相差较大或记录数据无波动,检查时发现记录与实际不符视为记
录不真实。
3、岗位操作人员不得人为掩盖工艺指标超标现象,如超标不记或记录合格数据,干扰自动
仪记录等。
4、分析人员应严格执行厂有关化验规程要求,不得无故降低分析频率,如因人员不足时,
经车间同意,按车间要求减少分析频率。
5、分析人员应按分析结果真实记录,不得弄虚作假,编造数据,检查发现弄虚作假现象者
一次扣罚半月效益工资。
6、生产出现异常,根据需要加做时,分析结果要全部反映在记录表上,并及时通知有关岗
位。
否则视为记录不实。
7、岗位记录本是交接班重要依据,一定要详细记录本班生产情况,发现生产中异常情况及
现象要如实记录,尤其是减量或全停时要详细记录。
8、检查发现记录不详扣罚10元,出现问题无记录或记录不真实一次扣罚50元,掩盖工艺
指标超标现象扣罚100元。
三、记录规范化要求:
1、版面要求整洁、无污染,如记录错误,应按如下规定处理,不准在记录表上涂改,不准
损坏记录表(本),故意损坏者发现一次扣罚10元。
2、记录表本中书写文字、数字、必须做到“字体端正,笔画清楚,排列整齐,间隔均匀。
”
书写汉字用钢笔书写,颜色采用蓝黑色,字体均采用长仿宋字,数字与字母采用斜仿宋体,
例:
1234567890
字体端正,笔画清楚,排列整齐,间隔均匀
不按规定书写者,发现一次扣罚5元。
3、所有记录表(本)严禁以草表形式记录。
严禁在记录表(本)上乱写乱划。
发现有乱写
乱划者扣罚当班人员20元。
4、所有记录内容按规定位置书写,禁止随便填写。
四、记录表(本)评比:
1、评比岗位
双氧水总控、循环、分析、泵房、空压机记录表
双氧水总控、循环、分析、泵房、空压机、配制、工长记录本
甲醛总控,托品,离心机记录本
甲醛总控,托品,离心机记录表
2、评比标准:
1)、幅面整洁,无污,页面无损坏现象。
(10分)
页面有污物视情况扣1—5分/次,页面损坏按情况扣1—5分/次。
2)、书写颜色统一(蓝黑),字体标准,书写位置正确(30分)
书写颜色不统一,书写位置不正确扣2分/次,字体不标准,字迹潦草视情况扣1—10分/次,
有涂改情况时扣10—20分/次。
3)、记录按时,无滞后或超前现象。
(20分)
检查发现记录超时时,扣2分/次。
4)、书写内容真实,内容详细,无涂改,无漏记错记现象。
(40分)
记录内容不真实扣10分/次,内容不详,漏记错记扣2分/次,涂改一次扣5分。
5)、凡检查扣罚项目同时列入考核范围。
6):
评比时间及方法:
每月评比一次,按评分标准打分后评定等级。
3、评比等级及奖罚:
一等90分以上。
奖励20元/人
二等80—90分。
奖励10元/人
三等70—80分。
无奖
四等60—70分。
扣罚10元/人
五等60分以下。
扣罚20元/人
五、本规定自下达之日起开始执行。
以前规定中凡与本规定有冲突时,以本规定中条例为准。
六、工艺管理规定中与本规程无冲突项目继续执行。