毕业设计solidworks.docx
《毕业设计solidworks.docx》由会员分享,可在线阅读,更多相关《毕业设计solidworks.docx(34页珍藏版)》请在冰豆网上搜索。
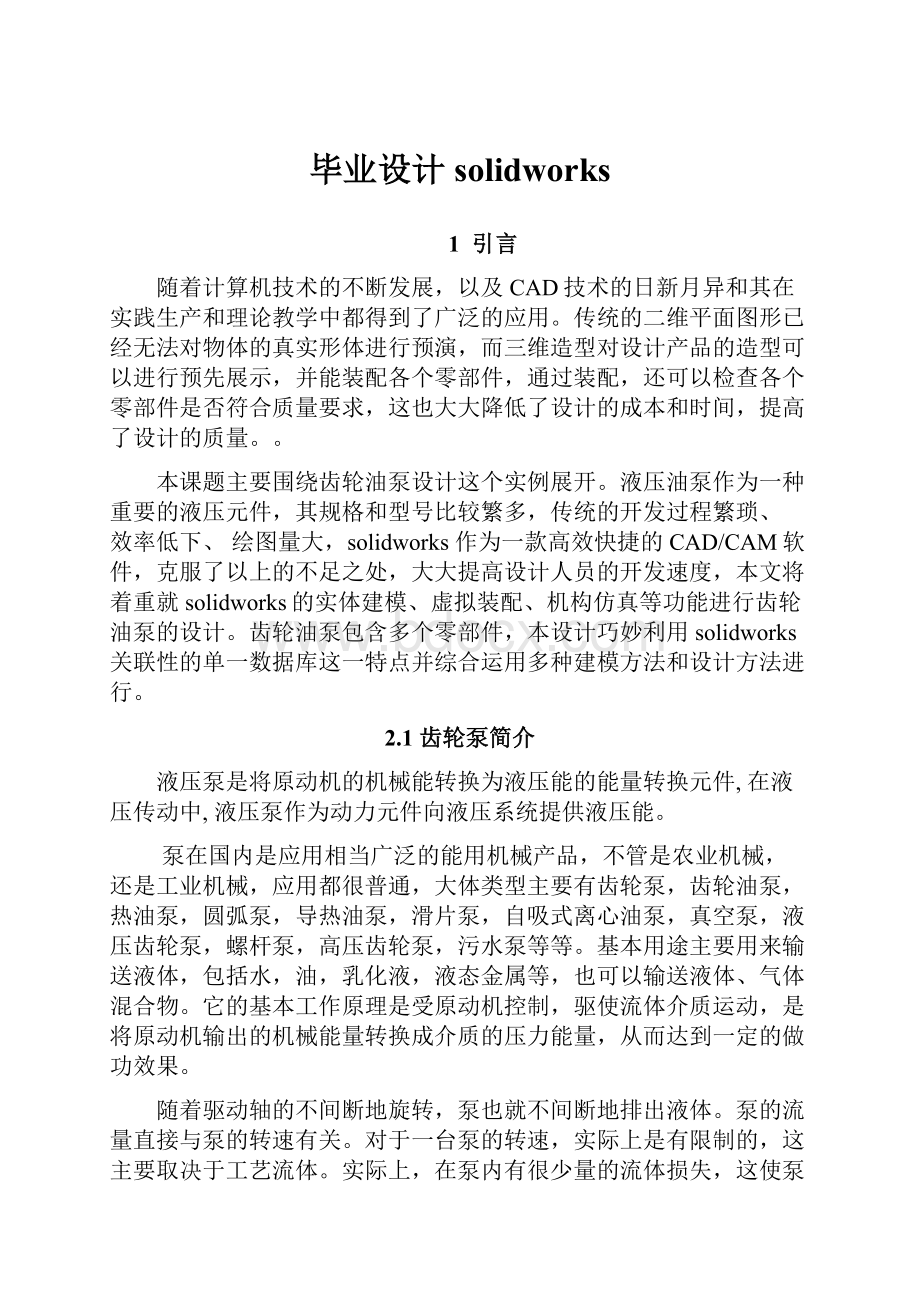
毕业设计solidworks
1引言
随着计算机技术的不断发展,以及CAD技术的日新月异和其在实践生产和理论教学中都得到了广泛的应用。
传统的二维平面图形已经无法对物体的真实形体进行预演,而三维造型对设计产品的造型可以进行预先展示,并能装配各个零部件,通过装配,还可以检查各个零部件是否符合质量要求,这也大大降低了设计的成本和时间,提高了设计的质量。
。
本课题主要围绕齿轮油泵设计这个实例展开。
液压油泵作为一种重要的液压元件,其规格和型号比较繁多,传统的开发过程繁琐、效率低下、绘图量大,solidworks作为一款高效快捷的CAD/CAM软件,克服了以上的不足之处,大大提高设计人员的开发速度,本文将着重就solidworks的实体建模、虚拟装配、机构仿真等功能进行齿轮油泵的设计。
齿轮油泵包含多个零部件,本设计巧妙利用solidworks关联性的单一数据库这一特点并综合运用多种建模方法和设计方法进行。
2.1齿轮泵简介
液压泵是将原动机的机械能转换为液压能的能量转换元件,在液压传动中,液压泵作为动力元件向液压系统提供液压能。
泵在国内是应用相当广泛的能用机械产品,不管是农业机械,还是工业机械,应用都很普通,大体类型主要有齿轮泵,齿轮油泵,热油泵,圆弧泵,导热油泵,滑片泵,自吸式离心油泵,真空泵,液压齿轮泵,螺杆泵,高压齿轮泵,污水泵等等。
基本用途主要用来输送液体,包括水,油,乳化液,液态金属等,也可以输送液体、气体混合物。
它的基本工作原理是受原动机控制,驱使流体介质运动,是将原动机输出的机械能量转换成介质的压力能量,从而达到一定的做功效果。
随着驱动轴的不间断地旋转,泵也就不间断地排出液体。
泵的流量直接与泵的转速有关。
对于一台泵的转速,实际上是有限制的,这主要取决于工艺流体。
实际上,在泵内有很少量的流体损失,这使泵的运行效率不能达到100%,因为这些流体被用来润滑轴承及齿轮两侧,而泵体也绝无可能无间隙配合,故不能使流体100%地从出口排出,所以少量的流体损失是必然的。
然而泵还是可以良好地运行,对大多数挤出物料来说,认可以达到85%~98%的效率。
如果传送的是油类,泵则能以很高的速度转动,但当流体是一种高粘度的聚合物溶体时,这种限制就会大幅度降低。
推动高粘度流体进入吸入口一侧的两齿空间是非常重要的,如果这一空间没有填充满,则泵就不能排出准确的流量,所以压力和流速的乘积也是另一个限制因素,而且是一个工艺变量。
由于这些限制,齿轮泵制造商将提供一系列产品,即不同的规格及排量(每转一周所排出的量)。
这些泵将与具体的应用工艺相配合,以使系统能力及价格达到最优,即产品的性价比达到最高。
2.2齿轮泵的工作原理
外啮合齿轮泵的工作原理如图所示,它由装在壳体内的一对齿轮所组成,齿轮两
侧有端盖(图中未示出),壳体、端盖和齿轮的各个齿槽组成了许多密封工作腔。
当齿轮泵主动齿轮转动,吸油腔齿轮脱开啮合,齿轮的轮齿退出齿间,使密封容积增大,形成局部真空,油箱中的油液在外界大气压的作用下,经吸油管路、吸油腔进入齿间。
随着齿轮转动,吸入齿间的油液被带到另一侧,进入压油腔。
这是齿轮进入啮合,使密封性逐渐减小,齿轮间部分的油液被挤出,形成了齿轮的压油过程。
齿轮啮合时齿向接触线把吸油腔和压油腔分开,起配油作用。
当齿轮泵的主动齿轮有电机带动不断转动时,齿轮脱开啮合一侧,由于密封容积变大,则不断从油箱中吸油,轮齿进入啮合的一侧,由于密封容积减小则不断地排油,形成一个不断循环的过程。
图2.1齿轮泵工作原理示意图
2.3本课题设计的内容和意义
齿轮泵是液压传动系统中常见的液压元件,在结构上可分为外啮合齿轮泵和内啮合齿轮泵两大类。
外啮合齿轮泵的优点是结构简单、尺寸小、重量轻、制造维护方便、价格低廉、工作可靠、自吸能力强、对油液污染不敏感等。
外啮合齿轮泵是应用最广泛的一种齿轮泵(称为普通齿轮泵),其设计及生产技术水平也最成熟。
多采用三片式结构、浮动轴套轴向间隙自动补偿措施、铝合金壳体径向“扫膛”工艺,并采用平衡槽以减小齿轮(轴承)的径向不平衡力。
目前,这种齿轮泵的额定压力可达6.3MPa。
正因为其诸多的特点引起了多人对其进行研究,目前,其三维设计技术已经达到了一个很高的境界,它能为产品开发人员提供更先进的设计方法和设计手段,具有形象生动、直观明了、快速响应的设计特点,其开发过程很符合设计人员的设计思维。
三维开发平台的出现和完善,为增强企业的开发能力、提高设计效率和产品的质量,提供了强有力的技术支持。
三维开发技术的应用和推广,可谓是传统的机械设计的一次革命。
三维立体设计逐步代替传统的二维平面是必然的趋势。
目前,市面上可供选择的软件很多,主要包括高端的UG、Pro/E和中端的Solidworks等3D设计软件。
这些软件的一个共性就是它们都具备了尺寸参数驱动技术以及虚拟装配技术;这些技术一般都能满足用户设计的各项诸如设计、计算分析、制造、虚拟装配、干涉检查、有限元分析、运动分析等高级CAD技术的需求。
尤其是集设计、工程及制造系统于一体化的UG软件,Pro/E是一个典型的模块化集成软件,其功能非常强大,最显著的特征就是使用参数化的特征造型。
根据目前的市场来看,它在我国的CAD/CAM研究所和工厂中得到了广泛的应用,有着越来越广阔的市场。
同AutoCAD相比,它的技术特点就是参数化管理,所有的算法都是矢量化的,三维与二维图形元素具有关联性,是目前不可多得的计算机辅助设计软件。
在本次毕业设计中,对外啮合齿轮泵的三维造型进行设计计算,并用三维造型软件绘制出各个零件的实体造型,将各个零件进行精确的装配,并且生成爆炸试图等辅助更加清晰的看透各零件的装配过程的图素,从而全面了解齿轮泵的三维造型。
2.4外啮合齿轮泵的研究现状
国内外有关齿轮泵的研究主要集中在以下几方面:
1.困油冲击及卸荷措施
齿轮泵的困油现象对齿轮泵及整个液压系统都产生了很大的危害。
困油冲击与齿轮啮合的重叠系数及卸荷是否完全等有和大的关系。
2齿轮泵噪声的控制技术
液压系统噪声的根源是复杂的和很多方面的。
它涉及到液压技术,流体力学,
振动力学,声学极其他学科的渗透和影响,液压泵产生的噪声,一般与其种类,
结构,大小,转数及工作压力有关。
液压泵的噪声随液压功率的增加而增加,而
液压功率是由泵的输出功率P,每转排量q,及转速n这三个工作参数的增加而
增加。
对于齿轮泵,可以采取如下措施来降低噪声:
加大罩壳的厚度,提高零部
件的刚性,使油更容易吸进,改进困油卸荷槽,改进齿形,使齿轮的模数减小,
加大齿宽,提高零部件尺寸的精度及降低表面粗糙度等。
3.降低齿轮泵流量脉动的方法
由于齿轮泵流量脉动较大,在一些要求较高的液压系统中,很少采用齿轮泵,关于降低齿轮泵流量脉动的方法有很多,如合理选择齿轮的参数;采用剖式齿轮;采用多齿轮。
4.齿轮泵高压的研究
高压齿轮泵和低压齿轮泵的工作原理是相同的,但低压齿轮泵却不能在高压
下使用。
其原因有二:
(a)由于低压齿轮泵齿轮的端面间隙和径向间隙是定值,
当工作压力提高后,期间隙的泄漏量大大增加,使容积效率下降。
(b)随着工作压力的提高,不平衡的径向力也随之增大,以至于轴承承载能力不足而不能工作
2.5外啮合齿轮泵的结构特点和优缺点
2.5.1外啮合齿轮泵的三大问题
外啮合齿轮泵的泄漏、困油和径向力不平衡是影响齿轮泵性能指标和寿命的三大问题。
各种不同齿轮泵的结构特点之所以不同,都因采用了不同结构措施来解决这三大问题所致。
1)泄漏
齿轮泵存在着三个可能产生泄漏的部位:
齿轮端面与端盖间;齿轮外圆和壳体内孔间以及两个齿轮的齿面啮合处。
其中对泄漏影响最大的是齿轮端面与端盖间的周向间隙,通过轴向间隙的泄漏量可占总泄漏量的75%~85%,因为这里泄漏途径短,泄漏面积大。
轴向间隙过大,泄漏量多,会使容积效率降低;但间隙过小,齿轮端面与端盖之间的机械摩擦损失增加,会使泵的机械效率降低。
因此设计和制造时必须严格控制泵的轴向间隙。
2)困油
齿轮泵要平稳工作,齿轮泵啮合的重叠系数必须大于1,也就是说要求在一对轮齿间即将脱开啮合前,后面的一对轮齿就要开始啮合。
就在两对轮齿同时啮合的这一小段时间内,留在齿间的油也困在两对轮齿和上下盖所形成的一个密闭空间内,当轮齿继续旋转时,这个空间的容积逐渐减小,直到两个啮合点处于节点两侧的对称位置时,这时封闭容积减至最小。
由于油液的可压缩性很小,当封闭空间的容积减小时,被困的油液受挤压,压力急剧上升,油液从零件接合面的缝隙中强行挤出,使齿轮和轴承受到很大的径向力;当齿轮继续旋转,这个封闭容积又逐渐增大到最大位置,容积增大时又会造成局部真空,使油液中溶解的气体分离,产生气穴现象,这些都将使齿轮泵产生强烈的噪声,这就是齿轮泵的困油现象。
消除困油的方法,通常是在齿轮泵的两侧端盖上铣两条卸荷槽,当密闭容积减小时,使其与压油腔相通;而密闭容积增大时,使其与吸油腔相通。
一般的齿轮泵两卸荷槽是非对称开设的,往往向吸油腔偏移,但无论怎样,两槽间的距离必须保证在任何时候都不能使吸油腔和压油腔相互串通。
3)径向不平衡力
在齿轮泵中,作用在齿轮外圆上的压力是不相等的,在压油腔和吸油腔处齿轮外圆和齿廓表面承受着工作压力和吸油腔压力,在齿轮和壳体内孔的径向间隙中,可以认为压力由压油腔压力逐渐分级下降到吸油腔压力,这些液体压力综合作用的结果,相当于给齿轮一个径向的作用力使齿轮和轴承受载。
工作压力越大,径向不平衡力也越大。
径向不平衡力很大时能使轴弯曲,齿顶和轴套产生接触,同时加速轴承的磨损,降低轴承的寿命。
为了减小径向不平衡力的影响,有的泵上采取了缩小压油口的办法,使压力油仅作用在一个齿到两个齿的范围内,同时适当增大径向间隙,是齿轮在压力作用下,齿顶不能和壳体相接触。
4)优缺点
外啮合齿轮泵的优点是结构简单,尺寸小,重量轻,制造方便,价格低廉,工作可靠,自吸能力强,对油液污染不敏感,维护容易。
它的缺点是一些机件承受不平衡径向力,磨损严重,泄漏大,工作压力的提高受到限制。
此外,他的流量脉动大,因而压力脉动和噪声都比较大。
2.5.2提高外啮合齿轮泵压力的措施
要提高齿轮泵的压力,必须要减小端面的泄露,一般采用齿轮端面间隙自动补偿的办法。
利用特制的通道把泵内压力油引到浮动轴套的外侧,产生液压作用力,使轴套压向齿轮端面,这个力必须大于齿轮端面作用在轴套内侧的作用力,才能保证在各种压力下,轴套始终自动贴紧齿轮端面,减小泵内通过端面的泄露,达到提高压力的目的。
2.6齿轮泵造型的相关基础技术
本课题的三维造型软件选择Solidworks,其是一套基于Windows的CAD/CAM/CAE桌面集成系统,是由美国Solidworks公司在总结和继承了大型机械CAD软件的基础上,在Windows环境下实现的第一个机械三维CAD软件,于1995年研制成功。
Solidworks是市场份额增长最快、技术发展最好、性能价格比最优的软件。
随着Solidworks版本的不断提高、其性能不断提高和完善,已从根本上改变了传统的设计、生产、组织模式,对推动现有企业的技术改造、带动整个产业结构的变革、发展新技术、促进经济增长都具有十分重要的作用。
该软件的动画演示形象、直观,能表达文字或者叙述不易讲解清楚的复杂产品的内部结构,模拟产品的工作情况,达到与非专业人士交流设计思想的目的。
建立运动机构模型,进行机构的干涉分析,跟踪零件的运动轨迹,分析机构中零件的速度、加速度、作用力、反作用力和转矩等,并用动画、图形等多种形式输出结果,其结果可指导修改零件的结构设计。
此外还可以将零部件在复杂运动情况下的复杂卸荷情况直接输出到主流有限元分析软件中以做出正确的强度和结构分析。
3齿轮泵的设计、校核及流量计算
3.1齿轮轴的设计
3.1.1各轴参数的确定
选取电机型号为YE112M-2,功率P=3.0kw转速n=1450r/min液压泵的容积效率为0.9。
各轴输入功率:
主动轴(长轴)P1=P·η1=P×0.99=2.97kw
η1---联轴器的效率值为0.99
从动轴(短轴)P2=P1·η2=P×0.97=2.88kw
η2---齿轮传动的效率值为0.97
各轴输出转矩
电机轴Td=9.55×106×P/n=19758.6N.mm
主动轴T1=9.55×106×P1/n=19561N.mm
从动轴T2=9.55×106×P2/n=18968.3N.mm
3.1.2齿轮的设计
齿轮分度圆直径的设计计算
d>=2.32×{(KT1/Ψd)×[(u+1)/u]×(ZE/[σH])}1/3
式中:
K=1.5
T1=2.064×104N.mm
Ψd=0.8
u=z2/z1=1
查表得材料系数ZE=189.8(MPa)1/2
两齿轮材料采用40Cr调质后表面淬火硬度为48~55HRC,
接触疲劳强度极限为σHlim1=σHlim2=1260MPa
设计齿轮泵的使用寿命为5年,每天工作16h,每年300天
使用寿命N1=N2=60njLh=60×1440×1×5×300×16=2.0448×109h
查表得
泵的接触疲劳寿命系数ZN1=ZN2=0.9
最小安全系数SHlim=1.05
许用应力[σH1]=[σH2]=ZN1·σHlim1/SHlim=1200MPa
分度圆直径d1>=2.32×{(KT1/Ψd)×[(u+1)/u]×(ZE/[σH])}
=27.78mm
圆周速度V=π·d1·n/(60×100)
=3.14×28.88×1440/(60×100)
=21.08m/s
查表得
使用系数KA=1
根据V=21.46m/s7级精度得动载系数KV=1.25
齿向载荷分布系数KHβ=1.25
载荷系数K=KA·KV·KHβ=1×1.25×1.25=1.56
校正分度圆直径d=d1·(K/Kt)1/3=29.28mm
模数m=d/z=29.28/10=2.928mm<3mm
即按标准模数取m=3mm
分度圆直径d1=d2=m·z=3×11=33mm
中心距a=m·(z1+z2)/2=33mm
齿宽b=Ψd·d=0.8×33=26mm
齿底圆df=(z1-2ha*-2c*)m=26mm
齿顶圆da=(z1+2ha*)m=39mm
基圆直径db=d·cosα=28.7mm(标准压力角α=200)
3.1.3轴的设计
1)短轴的设计
短轴的总长应稍小于泵体的厚度,泵体厚度为71mm,则短轴总长为L=71-3=68mm
由于短轴的齿轮两侧相互对称,齿宽b=26mm,所以两侧的轴的长度相等,且为:
L1=L2=(68-26)/2=21mm
2)长轴的设计
长轴是在短轴的基础上加上一段与联轴器相连的长度的阶梯轴,联轴器与泵体之间隔有一个上盖,其厚度为22mm,同时上盖于联轴器之间应有1~2mm的间隔,联轴器与长轴的接触部分约为20mm,故长轴的总长约为:
L=71+21+20+2=114mm,第三段轴长应为L3=20+2=22mm。
3.1.4泵体设计分析
作为齿轮泵的主要部件,齿轮泵泵体结构设计的合理性将直接关系到齿轮泵的性能指标及产品可靠性。
通过合理的规划,可以大大提高齿轮泵的结构强度,同时也可提高齿轮泵的寿命。
在齿轮泵的使用过程中,泵体出现的常见问题是泵体爆裂,这主要是由泵体的结构设计不合理所造成的。
根据实践经验,泵体爆裂主要出现在图3.1中所示的A处和B处。
由于A处钻有螺纹孔,使其截面积比其他剖面的截面积要小,在齿轮泵承受内部压力的情况下,此处受到的拉应力大于平均拉应力,形成危险的截面。
因此必须改善A截面处的承载能力。
在不改变螺孔尺寸的条件下,减小连接螺孔之间的距离,增加螺孔外部的尺厚,从而使危险截面的面积增大,提高了A截面的安全系数。
B处位于齿轮泵的压力油的出油口的横向剖面上,两个螺孔也在此横向剖面上。
在此结构下,出油口的横向剖面的实际承载面积比其他横向的剖面面积要小很多,大大削弱了承载能力,为了降低此种危险,我们可以把四个螺孔的位置旋转一个角度,如45度。
比较好的设计方案如图3.2所示。
图3.1泵体结构(改进前)
图3.2泵体结构(改进后)
3.1.5齿轮泵的闭死容积和卸荷槽
1)闭死容积
为保证齿轮泵能连续输液,必须使齿轮的重叠系数ε>1,即要求在一对齿啮合行将脱开前,后面一对就进入啮合,因此在一段时间内同时啮合的就有两对齿,留在齿间的液体被困在两对啮合齿后形成一个封闭容积(称闭死容积)内,当齿轮继续转动时,闭死容积逐渐减小,直至两啮合点处于对称于节点P的位置时,闭死容积变至最小,随后这一容积又逐渐增大,至第一对齿开始脱开时增至最大。
当闭死容积由大变小时,被困在里面的液体受到挤压,压力急剧升高,远大于泵排出压力,可超过10倍以上的程度。
于是被困液体从一切可以泄露的缝隙里强行排出,这时齿轮和轴承受到很大的脉冲径向力,功率损失增大,当闭死容积由小变大时,剩余的被困液体压力降低,里面形成局部真空,使容解在液体中的气体析出,液体本身产生气化,泵随之产生噪声和振动,困油现象对齿轮的工作性能和寿命均造成很大的危害。
2)卸荷槽
为消除困油现象,可在与齿轮端面接触的两侧板上开两个用来引出困液的沟槽,即卸荷槽。
卸荷槽有相对于节点P对称布置和非对称布置两种。
它的位置应保证困液空间在容积达到最小位置以前与排出腔相连,过了最小位置后与吸引腔相连通。
本设计卸荷槽采用非对称布置。
表3.1卸荷槽深度
齿轮模数m
1
2
3
4
5
6
7
卸荷槽深度
1.0
1.5
2.5
4.0
5.5
7.5
10
用插值法取卸荷槽深度值为2mm。
(2)非对称布置卸荷槽尺寸
齿侧间隙很小(接近无齿侧间隙)时,采用非对称布置卸荷槽,其位置向吸入腔一方偏移一段距离,这样不仅可以解决困液问题,还可以回收一部分高压液体。
3.2齿轮泵的校核
3.2.1齿轮的校核
已知输入功率为P=3.0kw,主轴转速为n=1450r/min,转矩T=20848.6N.mm
齿轮1、2模数m=3齿数z=11齿宽b=26
两齿轮材料采用40Cr调质后表面淬火硬度为48~55HRC,
则齿宽系数Ψd=0.8
齿形系数YFa1=YFa2=2.60
应力修正系数Ysa1=Ysa2=1.64
查表得
弯曲疲劳极限σFlim1=σFlim2=2.346×HRC+605.628N/mm2
=2.346×48+605.628N/mm2
=718N/mm2
弯曲许用应力[σF3]=[σF4]=0.7σlim=0.7×718N/mm2
=502.6N/mm2
1)校核齿根弯曲疲劳强度
使用情况系数KA=1
圆周速度V=π·dn/(60×100)
=3.14×33×1440/(60×100)
=22.29m/s
查表得
动载系数KV=1.25
齿向载荷分布系数KHβ=1.25
KFβ=0.794×KHβ+0.207=1.20
Ft=2T1/d=2×2.065×104/33=1376.7N
KAFt1/b=1×1376.7/26=57.36N.m<100N.m
查表得
齿向载荷分布系数KHα=1.09KFα=1.18
重合度εα=[1.88-3.2×(1/z+1/z)]×cosβ
=[1.88-3.2×1/5]=1.24
式中β=00
重合度系数Yε=0.25+0.75/εα=0.25+0.75/1.24=0.85
KH=KA·KV·KHβ·KHα=1×1.25×1.25×1.09=1.7
KF=KA·KV·KFβ·KFα=1×1.25×1.20×1.18=1.77
查表得
弯曲最小安全系数SFmin=1.25
弯曲寿命系数YN1=YN2=1
尺寸系数Yx=1.1
[σF1]]=δFlim1·YN1·Yx/SFmin=718×1×1.1/1.25=574.4N/mm2=[σF2]
σF1=2KF*T1·YFa1·Ysa1·Yε/b·d·m
=2×1.77×2.064×2.60×1.64×0.85/24×30×3
=122.61N/mm2<[σH]
σF2=σF1·YFa2·Ysa2/(YFa1·Ysa1)=σF1,
齿根弯曲疲劳强度满足要求。
2)校核齿面接触疲劳强度
重合度系数Zε=[(4-εα)/3]1/2
=[(4-1.24)/3]1/2
=0.96
查表得
材料系数ZE=189.8(MPa)1/2
节点区域系数ZH=2.5
接触最小安全系数SHmin=1.05
接触寿命系数ZN1=1.09,ZN2=1.07
接触疲劳极限σHlim1=σHlim2
=12HRC+550
=12×48+550
=1126N/mm2,
许用接触力[σH1]=σHlim1·ZN1/SHmin
=1126·1.09/1.05
=1244N/mm2
[σH2]=σHlim2·ZN2/SHmin
=1126×1.07/1.05
=1147.4N/mm2
σH=ZH·ZE·Zε·{[2KH·T1/(b·d2)]·[(u+1)/u]}1/2
=455.52×{[2×1.5×2.064×104/(24×302)]×[(1+1)/1]}1/2
=1090.7N/mm2<[σH2],
齿面接触疲劳强度满足要求。
(其三维实体造型见图3.3和3.4)
图3.3主动齿轮轴(长轴)
图3.4从动齿轮轴(短轴)
3.2.2齿轮轴的校核
1、主动齿轮轴的强度计算
1)、主动齿轮轴经的支反力RA和RB(其受力分析见图3.5)
由于主动齿轮轴在受力上对称,轴径的支反力为主动齿轮承受的径向力的一半,即,
Fr1=Ft1/tanα=(2T1/d)/tanα=3780.53N
RA=RB=F1/2=1890.27N
其中:
F1为作用在主动齿轮轴上的径向力,F1=q·b(N),q为均布载荷(N/mm2)
图3.5主动齿轮轴的受力分析
2)、危险截面S-S处的弯矩MWA
MWA=RA·L=1890.27×23=43476.11N.mm
3)、表面的抗弯断面模数WA
WA=π·d3/32=3.14×183/32=572.265mm3
其中,d为轴径直径
4)截面的弯曲应力σWA
σWA=MWA/WA=43476.11/572.265=75.972N/mm2<[σ]
所以抗弯强度满足要求。
5)、传动轴传递的扭矩Mn
Mn=p·q×103/(2×π×ηm)=28917.2N.mm
其中,p为泵的最大压力,q为泵的理论排量,ηm为泵的机械效率,一般为0.9
6)、截面的抗扭断面模数Wn
Wn=π·d3/16=286.13mm3
7)、截面的扭转剪应力τn
τn=Mn/Wn=101.07N/mm2=<[τ]
2、从动齿轮轴的强度计算
1)、从动齿轮轴经的支反力RA’和RB’(其受力分析见图3.6)
由于从动齿轮轴在受力上对称,轴径的支反力为从动齿轮承受的径向力的一半,即,
Fr2=Ft2/tanα=(2T2/d)/tanα=3667.11N
RA’=RB=F2/2=1833.56N
其中:
F2为作用在主动齿轮轴上的径向力,F2