第78章集成电路设计与制造讲义.docx
《第78章集成电路设计与制造讲义.docx》由会员分享,可在线阅读,更多相关《第78章集成电路设计与制造讲义.docx(23页珍藏版)》请在冰豆网上搜索。
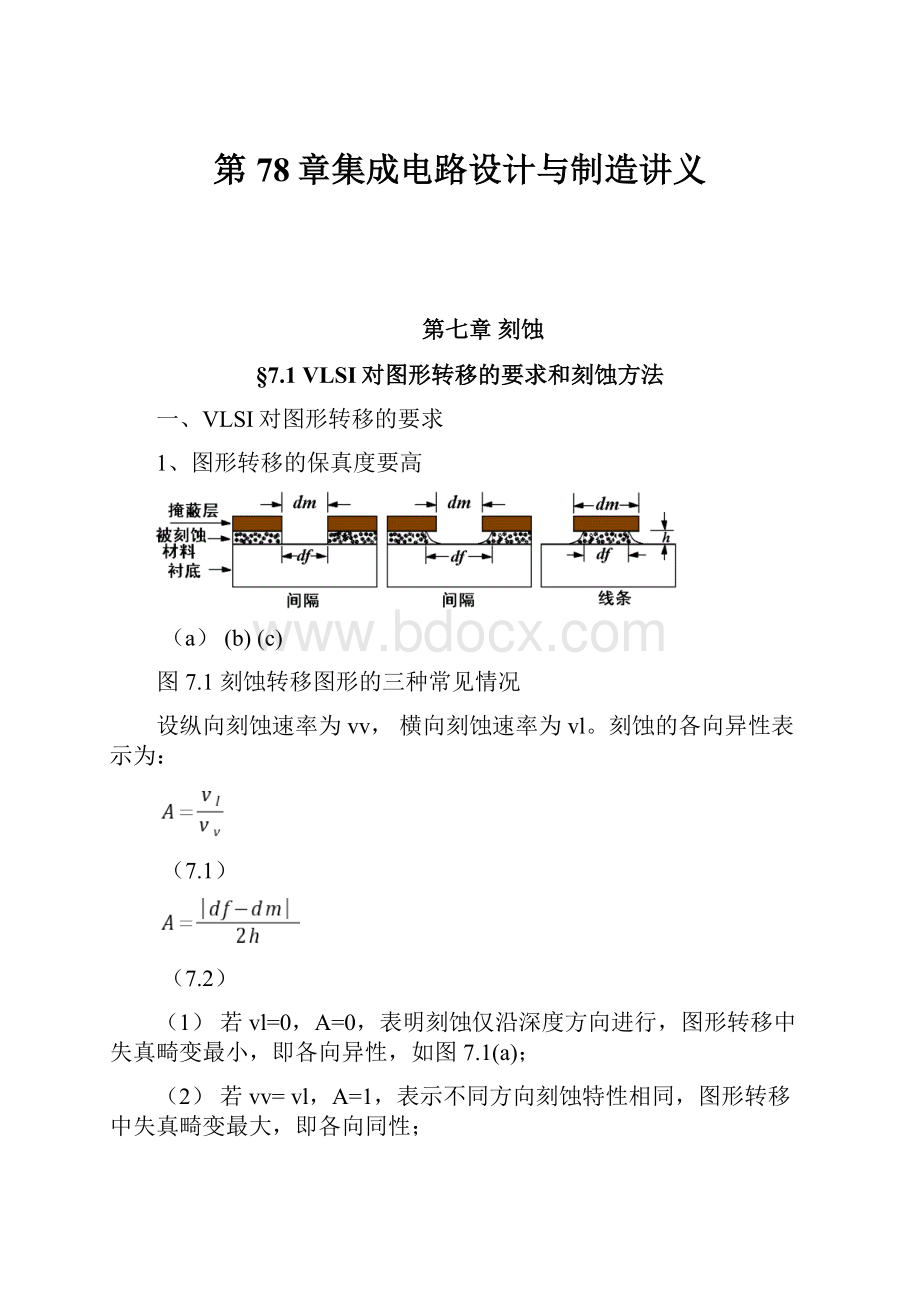
第78章集成电路设计与制造讲义
第七章刻蚀
§7.1VLSI对图形转移的要求和刻蚀方法
一、VLSI对图形转移的要求
1、图形转移的保真度要高
(a)(b)(c)
图7.1刻蚀转移图形的三种常见情况
设纵向刻蚀速率为vv,横向刻蚀速率为vl。
刻蚀的各向异性表示为:
(7.1)
(7.2)
(1)若vl=0,A=0,表明刻蚀仅沿深度方向进行,图形转移中失真畸变最小,即各向异性,如图7.1(a);
(2)若vv=vl,A=1,表示不同方向刻蚀特性相同,图形转移中失真畸变最大,即各向同性;
(3)通常vvvl,1>A>0,如图7.1(b)、(c),刻蚀同时在纵向、横向进行。
因此,各向异性是图形转移中保真程度的反映。
2、选择比大(即被刻蚀材料与掩蔽材料的刻蚀速率比尽可能大)
3、均匀性高
大面积硅片上生长的薄膜厚度的不均匀和各个部位刻蚀速率的不均匀将导致刻蚀图形转移的不均匀性。
4、防止沾污
二、刻蚀方法
1、湿法刻蚀
采用化学方法腐蚀硅片中无光刻胶覆盖的部分,要求光刻胶有较强的抗蚀能力。
腐蚀速率R表示为:
(7.3)
对于给定材料,激活能Ea一定,影响反应速率的主要因素是温度(T高,R大)。
湿法腐蚀的特点如下:
(1)湿法腐蚀的反应产物必须是气体或能溶于腐蚀液的物质;
(2)湿法腐蚀为各向同性,造成严重的侧向腐蚀,显著地限制了器件尺寸向微细化发展;
(3)湿化学腐蚀反应过程常伴有放热和放气。
放热导致腐蚀区局部温度升高,引起反应速率增加,刻蚀质量较差;放气造成腐蚀区的局部区域因气泡停留,使腐蚀停止进行,形成局部缺陷。
通常采用搅拌的方式减小上述效应;
(4)湿化学腐蚀耗费大量的酸碱溶液,污染大,成本高,还容易损伤芯片表面,影响器件的成品率。
2、干法刻蚀(干法腐蚀)
主要是指采用纯化学作用的等离子腐蚀、或纯物理作用的离子腐蚀、或兼有物理及化学作用的反应离子腐蚀等方法来腐蚀样品。
(1)干法刻蚀特点:
1)除等离子腐蚀一般是各向同性外,其它干法腐蚀都具有各向异性特点;
2)干法刻蚀大部分在低压反应系统中进行,其加工清洁度高,有利于提高器件的成品率;
3)干法刻蚀不需要大量的酸碱溶液,减小了环境污染,降低了成本;
4)干法刻蚀操作简便,有利于实现工艺自动化。
(2)干法刻蚀按机理分,有如下几种类型:
表7.1各种干法腐蚀一览表
腐蚀
方法
反应物
种类
反应
气体
腐蚀
材料
反应
机构
选择性
方向性
装置
等
离
子
腐
蚀
自由基
O2
CF4
CF4+O2
Si
SiO2
Si3N4
多晶硅
化学反应
大
各向同性
圆筒型
自由基+活性离子
O2
CF4
CF4+O2
Si
SiO2
Si3N4
多晶硅
物理/化学反应
大
各向异性
平行极板型
反应
离子
腐蚀
活性离子
CF4+H2
C3F8
CCl4
BCl3
SiO2
PSG
Al
AlSi
物理/化学反应
中
各向异性
平行极板型
离子束腐蚀
非活性离子
Ar
SiO2
物理反应
大
各向异性
离子枪
§7.2等离子刻蚀
一、等离子体腐蚀原理
低压(13~1300Pa)环境中RF电场作用下,气体原子或分子产生电离,形成由离子、电子及自由基(中性原子和分子)构成的等离子体。
其中自由基占90%以上。
自由基是一种处于激发态的气体粒子,具有较强的化学活性,又称活性基,它与被刻蚀物质发生化学反应,产生挥发性物质,达到腐蚀的目的。
因等离子体中活性基自由程较小,可以认为到达被刻蚀材料上各处粒子的碰撞几率大致相同,因而等离子腐蚀是各向同性的。
如Si、多晶硅的等离子腐蚀,采用CF4气体作为腐蚀气体:
(7.4)
激发态氟基F*和上述材料分别反应如下:
(7.5)
反应后生成的SiF4有很高的挥发性,随即被抽走。
二、等离子腐蚀装置
1、圆筒形反应器
(1)可用于干法去胶,反应气体为氧等离子体。
(2)带孔的铝屏蔽罩把等离子体与反应室隔开,只有较长寿命的自由基达到硅片表面进行腐蚀,从而避免硅片直接受离子轰击的影响,显著提高腐蚀的均匀性,增加光刻胶的寿命;
(3)通过铝屏蔽罩的反应粒子以任意方向入射到硅片表面上,因而圆筒形刻蚀为各向同性。
图7.2圆筒形反应器
2、平行平板型反应器
图7.3平行平板型等离子反应器
该结构特点:
(1)上下电极彼此平行,间距2~5cm,电场均匀地分布在平行极板之间,电场中的离子垂直硅片表面作定向运动,使腐蚀具有各向异性的特点;
(2)具有腐蚀速率高,选择性好,设备简单,成本低等特点。
三、等离子腐蚀性能
1、腐蚀速率
(1)射频功率越高,腐蚀速率越快。
但较高的功率会降低光刻胶的抗蚀性,导致腐蚀的可控性变差;
(2)增加腐蚀气体流量,将增加活性离子浓度,腐蚀速率相应增大。
但流量过大会导致压力增高,使电子的自由程缩短,气体的离化率变低,腐蚀速率会下降;
(3)衬底温度升高,腐蚀速率增大。
为确保腐蚀的重复性,须精确控制反应室与衬底温度;
(4)腐蚀气体种类和气体成份对腐蚀速率影响较大。
1)各种氟里昂气体对Si(111)腐蚀速率:
CF4>CCl3F>CCl2F2>CHCl2F
2)CF4+(5~12%)O2刻蚀气体:
Si/SiO2刻蚀速率比为10:
1
3)CF4+H2刻蚀气体:
SiO2/Si刻蚀速率比10
2、腐蚀均匀性
采用平行平板反应器且反应室采用恒温控制可提高片内、片间及批次间腐蚀均匀性。
3、负载效应
在给定气体流量、气压和输入功率条件下,待刻蚀样品数量增加,刻蚀速率下降。
§7.3反应离子刻蚀(RIE)与离子腐蚀
一、反应离子刻蚀(RIE)
1、原理
在很低的气压下(1.3~13Pa)通过反应气体放电产生各种活性等离子体,射频溅射使活性离子作定向运动,产生各向异性腐蚀;活性离子在电场作用下又加速化学反应过程,加快了腐蚀的速度。
不仅能刻蚀用等离子体刻蚀法难以刻蚀的Al-Si-Cu、SiO2等材料,其刻蚀的方向性也优于等离子体腐蚀法,是目前VLSI广泛采用的干式腐蚀方法。
2、RIE刻蚀装置
图7.4RIE刻蚀结构
3、特点
(1)化学反应与物理反应相结合,产生各向异性腐蚀,刻蚀效果好;
分辨率能达到1m,对大多数材料的选择比已超过10:
1。
(2)RIE的反应气压极低
反应气压低,气体的平均自由程大,导致离子被电场作用的距离、速度与动能增大,加速轰击样品表面,物理切削作用加强。
4、刻蚀气体与被刻蚀材料
Si、Poly-Si、Si3N4、Mo、W
CHF3
SiO2
CCl3
Al,Ti
O2
光刻胶
二、离子束腐蚀(离子铣)
1、原理
射频等离子体中产生的惰性气体离子Ar+在低压(0.13~13Pa)环境中被加速轰击样品表面,通过和样品材料原子间的动量交换达到腐蚀的目的。
2、特点
(1)纯物理性腐蚀法,各向异性腐蚀,腐蚀速率低;bb
(2)离子纯度高,定向性好,离子能量分布均匀,分辨率很高(0.01m);
(3)可腐蚀任何材料,刻蚀重复性、均匀性优良;
(4)缺点是腐蚀速率慢,刻蚀选择性较差,刻蚀时会产生再淀积现象。
3、被刻蚀材料
Si、SiO2、GaAs、Ag、Au、光刻胶等
第八章金属化
§8.1概述
一、金属化工艺的作用
金属化工艺是根据集成电路的设计要求,将各种晶体管、二极管、电阻、电容等元器件用金属薄膜线条(互连线)连接起来,形成一个完整的电路与系统,并提供与外电源相连接的接点。
金属化系统和金属化工艺的优劣将影响整个电路的电特性和可靠性。
为提高电路速度与集成度,应可能缩短互连线,采用多层金属化系统。
二、金属化系统的要求
1、电导率高,能提供低阻的互连引线;
2、与N+硅、P+硅或高掺杂多晶硅能形成低阻欧姆接触;
3、与硅、SiO2的粘附能力强;
4、抗电迁移能力强;
5、抗电化学腐蚀强;
6、易于淀积和刻蚀;
7、便于超声或热压键合,且键合点能经受长期工作;
8、多层互连中,层与层之间不互相渗透和扩散。
三、金属-半导体接触
1、肖特基接触
当金属的功函数M大于N型半导体的功函数SN或小于P型半导体的功函数SP时,两者接触为肖特基接触,即整流接触(具有单向导电性)。
2、欧姆接触
流过金属-半导体接触区的电流随电压成正比关系,近似服从欧姆定律。
其主要特点是:
引线孔处接触电阻上的电压降与硅体内的电压降相比可忽略。
形成欧姆接触的措施:
(1)半导体高掺杂;
(2)适当选取金属电极(如Pt、Ti等),使得与半导体接触的势垒较低。
§8.2金属化薄膜的制备
一、真空蒸发
1、概念及过程
真空蒸发技术是对淀积薄膜的源材料施加热能或动能,使之分解为原子或原子的集合体,并结合或凝聚在硅片表面而形成薄膜。
蒸发过程:
(1)被蒸发物质从凝聚相(固体或液体)转化为汽相;
(2)汽相原子或分子在真空系统中输运;(3)汽相原子或分子在衬底上淀积、成核和生长。
2、真空蒸发要求
(1)真空蒸发系统应具有加热源,将蒸发源材料加热到足够高温度,形成汽相原子或分子;
(2)蒸发必须在真空室内进行,真空度应在1.3310-3Pa~1.3310-7Pa;
图8.1电阻加热蒸发装置图
(3)金属蒸发原子在系统中输运的平均自由程远大于蒸发源与衬底间的距离。
3、电阻加热蒸发(2000℃以下材料)
(1)电阻加热器材料的性能要求
●电阻丝熔点远高于蒸发源的熔点,且蒸汽压极低;
●蒸发过程中不软化,不与蒸发源生成合金;
●容易加工成所需要的各种形状。
常用的电阻加热丝材料:
钨、钼、钽丝。
(2)蒸发工艺流程(蒸铝膜)
1)挂铝丝(99.99%纯度)并放置硅在衬底加热器上,转动活动挡板,使之位于蒸发源与硅片之间,盖好钟罩;
2)抽真空:
开动机械泵,打开低真空阀,待真空度高于1.3Pa后,转到扩散泵抽高真空;
3)硅片加热:
真空度抽到6.710-3Pa,开始加温。
衬底温度升到400℃,恒温数分钟以除去硅片表面吸附的污物,然后降温;
4)蒸发:
衬底温度降至150℃且真空度达到6.710-3Pa以上,逐步加热蒸发源使之熔化后附在钨丝上,先使铝中高蒸汽压杂质挥发掉(提高铝的纯度),然后迅速增大加热电流到一定值,打开挡板,蒸发铝到硅片上。
蒸发完毕转回挡板,并停止蒸发源加热;
5)取片:
待硅片温度降至150℃以下,关闭高真空阀,关闭扩散泵电源,对真空室放气,打开钟罩,取出硅片。
(3)特点
●优点:
操作简单,不产生电离辐射;
●缺点:
可能受到来自加热器的污染(钨丝加热器会引进K、Na离子沾污,而钽丝则几乎没有);装载量小而限制了最终薄膜厚度。
4、电子束蒸发(2000℃以上或难熔金属)
(1)原理
电子束蒸发是利用阴极电子枪发射出电子,电子束在电场作用下穿过加速极阳极进入磁场空间,通过调节磁场强度控制电子束的偏转半径,准确地打到坩埚内的蒸发源上(Al或Ti等),将电子的动能转变为热能,使金属熔化并蒸发到硅片表面上,形成薄膜。
(2)特点
优点:
K、Na离子沾污轻;蒸发速率大;台阶
覆盖性好;膜厚控制好。
缺点:
导致辐射损伤。
(可用退火方法消除:
380℃~500℃,N2或N2+H2混合气氛中退火15~40min)
图8.2电子束蒸发装置
5、蒸发工艺中影响的薄膜质量的因素
(1)金属膜淀积前硅片的清洗
2号清洗剂煮(HCl:
H2O2:
H2O=1:
2:
8)
2.5%HF酸腐蚀90S
冷去离子水冲
甩干。
(1)蒸发速率
蒸发速率过低,金属膜不光亮,电阻大,键合困难;蒸发速率过大会在硅片表面形成金属原子团淀积小丘,影响光刻,且厚度也不易控制。
(2)蒸发源的合金成分
为防止合金化时Si向Al中溶解引起PN结穿通,采用Al-Si(1~2%)合金蒸发源;为提高Al膜的抗电迁移能力,采用Al-Cu(1~4%)或Al-Si-Cu(含Cu4%,含Si1%)合金源。
(3)衬底温度
较高的衬底温度可使蒸发薄膜与Si、SiO2粘附得更好,有利于降低接触电阻,膜的晶粒越大,台阶处的连续性好。
(4)蒸发后金属膜的合金化
将光刻好金属化布线的硅片在真空中或干N2或N2+H2(3:
1)混合气体的保护下加热到一定温度并保持足够时间的过程。
目的:
改进金属化薄膜与衬底(Si或SiO2)的粘附性,并与硅之间形成良好的欧姆接触或肖特基接触;消除电子束蒸发引起的辐射损伤;保证双层布线间的良好接触。
合金温度:
380℃~450℃;时间:
15~30min。
二、溅射
1、溅射的基本原理
用高能粒子(由电场加速的正离子)冲击固态靶的表面,靶原子与这些高能粒子交换能量后从表面飞出,淀积在硅片(阳极),形成薄膜。
每个正离子能从阴极上打出的平均原子数称为溅射系数S(溅射率),影响溅射率S的因素:
1)轰击粒子的质量增大,溅射率增加。
在惰性气体轰击离子中,氪和氙的溅射系数较大,氩次之。
因氩易获得,故常用。
2)轰击粒子的能量不同,溅射率不同。
在能量小于70eV的低压区,溅射率几乎为零;离子能量在70eV~104eV之间,溅射随电压升高而增大;离子能量高于3104eV,因大部分高能离子注入到靶材料内部损失掉能量,溅射率随电压升高反而下降;
3)气体压力增大,溅射率减小;
图8.3直流二极溅射台图8.4高频溅射台
4)靶材料不同,溅射率也不同。
2、溅射方法
表8.1几种溅射技术的比较
溅射技术
工艺参数
工作压力(Pa)
主要特点
直流二极
溅射
直流:
1~7kV
0.15~1.5mA/cm2
13.3~1.3
优点:
结构简单,适于在大面积衬底上淀积均匀的导电薄膜;调整压强和电压以控制放电电流。
缺点:
溅射速率低,衬底温升高;辐射损伤较重;薄膜纯度较差。
高频溅射
13.56MHz,
峰-峰电压:
0~2kV
1.3~0.13
优点:
适于制作绝缘介质膜(如SiO2、Al2O3等)和金属膜;
缺点:
溅射速率低。
磁控溅射
0.2~1kV
0.13
利用电场与磁场正交的磁控管模式,使离化率大大提高,溅射速率提高一个数量级;衬底上硅片温升降低,实现低温溅射;低压低能溅射,膜层质量好,辐射损伤最轻。
3、溅射特点
(1)由于淀积粒子的能量较高,膜与衬底的粘附性更好;
(2)溅射膜的合金成份与靶的合金成份比例基本相同;
(3)溅射膜对衬底的台阶覆盖更好;
(4)与普通钨丝蒸发相比,大大减小了K、Na离子沾污;
(5)溅射电压较低,尤其是磁控溅射,电压约300~700V,从而大大降低了硅片的辐射损伤。
三、其它淀积技术
1、离子束溅射
(1)优点:
离子不是辉光放电产生,而是直接由独立的离子源发射惰性气体的离子,经电场加速进入放置样品的真空室;离子束源与样品室的真空度均可高达1.3mPa~13Pa,因而膜的纯度很高。
(2)缺点:
溅射速率低,离子束源复杂。
2、CVD化学气相淀积技术
包括常压、低压、等离子增强CVD等技术。
优点:
(1)薄膜的成分精确可控、配比范围大;
(2)淀积速率一般高于PVD(物理气相淀积,如蒸发、溅射等);
(3)厚度范围广,由几百埃至数毫米,且能大量生产;
(4)淀积膜结构完整、致密,与衬底粘附性好,台阶覆盖性好。
§8.3金属化互连技术
一、金属化系统
金属化互连线分为两大类:
(1)铝为主的金属化系统,可以不加接触层、粘附层和阻挡层等,工艺简单,与铝丝键合,产品价格低廉而获广泛使用,但抗电迁移能力差;
(2)以金为主的金属化互连,抗电迁移能力强,特别是采用金丝球形热压键合,键合点特别牢固,适于特殊要求的高可靠集成电路。
图8.5硅集成电路的金属化系统图8.6互连线在接触孔处的纵向结构
表8.2常用金属的性质
金属
体电阻率
(.cm)
6000Å厚的
方块电阻(/)
与硅的接触电阻()
与SiO2的粘附性
0.001.cmN型硅
0.002.cmP型硅
Ag
1.61
2.710-2
Al
2.74
4.6
0.09
0.03
好
Au
2.44
4.1
不好
Cu
1.70
2.8
不好
Mo
5.3
8.8
0.08
0.06
好
W
5.3
8.8
较好
Ni
7.8
13.0
0.02
0.02
较好
Ti
0.01
0.01
很好
Cr
13
0.03
0.04
很好
Pt
9.8
16.4
0.02
0.02
二、常用金属化系统及其特点
1、纯铝系统
铝是三价元素,在硅中是强P型杂质,与P型硅能形成低欧姆接触;N型硅表面杂质浓度超过1019cm-3时,铝能与其形成低阻欧姆接触。
双极及MOS两类集成电路,无论是单层布线或多层布线,均广泛采用铝作互连材料。
(1)优点
●能单独作金属化布先,工艺简单;
●材料价格低廉;
●电阻率低;
●能用电阻丝加热蒸发,工艺简单;
●与SiO2粘附性强;
●容易光刻;
●腐蚀铝时对SiO2和Si不产生腐蚀;
●铝能够穿透引线孔内残余的氧化层,容易形成欧姆接触;
●铝与硅的接触处无空隙,粘附牢;
●铝与高浓度P型及N型硅均形成低欧姆接触;
●固溶在铝引线内的硅对铝引线的电阻率影响不大;
●铝互连线与外引线键合容易;
(2)缺点
●铝布线的电迁移现象比较严重;
●高于500℃下能与SiO2反应,导致铝膜变薄,电阻变大,SiO2受到侵蚀,甚至铝可穿透SiO2而与Si接触,引起短路;
●金丝与铝丝互连线键合会产生黄斑和紫斑,可靠性差;
●铝是软金属,容易擦伤;
●铝与硅在较高温度下热处理时,由于硅在铝中的溶解和扩散,导致浅PN结退化甚至穿通。
(3)克服铝系统的措施
●采用钝化层保护以免铝膜擦伤;
●在铝中掺入(2~4%)Cu或(1~2%)Si,以减缓电迁移;
●采用铝丝键合技术,以克服黄斑和紫斑;
●在铝中掺入(1~2%)Si,使Si在铝膜中达到饱和,以克服铝对硅的溶解。
2、铝-硅(1~2%)合金系统
(1)避免硅在铝中溶解,保护PN结;
(2)抗电迁移能力强;
3、铝-(2~4%)铜-(1~2%)硅合金系统
(1)抗电迁移能力强;
(2)热处理过程中能阻止铝、硅的再结晶,减小膜中小丘的产生,对多层布线有利。
4、Al-TiW-Pt-Si互连系统
优点:
(1)Pt与P型硅及高浓度N型硅均能形成阻值极低的欧姆接触;
图8.7硅栅MOS晶体管
(2)抗电迁移能力强,可靠性高;
(3)适于超浅结电路。
5、多晶硅和难熔金属硅化物复合栅结构和互连
(1)多晶硅栅优点
●自对准方式减小了晶体管的尺寸,并减小了栅电极与源、漏电极间的交叠电容,从而提高了器件的集成度与工作速度,如图8.7;
●多晶硅可以高温氧化,对多层布线非常有利;
●阈值电压低(取决于硅与硅的功函数差);
图8.8SiO2的击穿时间与
电容电极材料的关系
●有利于利用缩比原则,如图8.8。
随着集成电路的发展,器件和薄膜的纵向尺寸和横向尺寸都将按比例缩小,作为互连材料的多晶硅薄膜,其过高的电阻率成为限制集成电路速度的因素之一(重掺杂多晶硅R10/),延迟时间常数RC与电阻率和方块电阻的关系如下:
=
=R
式中R为方块电阻,l为互连引线长度,d和w分别为引线的厚度与宽度,ox、tox分别为多晶硅互连引线下面的绝缘层的介电常数和厚度。
图8.9多晶硅/硅化物复合栅结构
(2)难熔金属硅化物的优点
●难熔金属硅化物具有低的、类金属的电阻率(约为多晶硅的十分之一或更低);
●高温稳定性好,抗电迁移性能好;
●可直接淀积难熔金属在多晶硅上,加温处理形成硅化物,工艺与现有硅栅工艺兼容。
1)适用于制作栅和互连的硅化物材料
ⅣB族的 TiSi2(二硅化钛)、ⅤB族的TaSi2(二硅化钽)、ⅥB族的MoSi2(二硅化钼)和WSi2(二硅化钨)。
2)适用于制作欧姆接触的材料
ⅧB族的PtSi(硅化铂)和PdSi2(二硅化钯)。
(3)多晶硅和难熔金属硅化物复合栅和互连
图8.10Al/Si接触中的结穿刺现象
先淀积一层多晶硅(约500Å),离子注入或扩散掺入磷,再淀积一层硅化物(4000Å~5000Å),一般采用溅射工艺以确保硅化物组分。
复合栅结构如图8.9。
三、金属化互连系统中失效及改进措施
1、结穿刺现象(如图8.10)
改进措施:
(1)Al/重掺杂多晶硅双层金属化结构
(2)Al-阻挡层结构
如Al-PtSi或PdSi2(欧姆接触层)-TiN或TiW(阻挡层)-Si
2、电迁移现象
导电材料的质量输运现象,是由在外加电场影响下导体内运动的电子,将其动能传给正金属离子所引起的。
改进措施:
(1)Al-Cu(4%)合金和Al-Si(1~2%)-Cu(2~4%)合金
采用溅射工艺以确保金属膜合金成分与靶一致。
(2)Al-TiW-Pt-Si互连系统
3、台阶覆盖问题
图8.11引线孔台阶淀积金
属膜的覆盖问题
台阶覆盖问题容易导致金属化引线断路,对精细光刻工艺带来不良影响,严重影响集成电路的可靠性和成品率。
结构如图8.11。
改进措施:
(1)增加金属薄膜淀积时的衬底温度,以增加淀积材料分子(原子)的表面迁移率,改善其厚度的均匀性;
(2)用行星旋转式真空淀积装置;
通过蒸发源和衬底硅相对方向的连续改变,使蒸发原子或分子到达硅衬底的角度不断变化,有效地消除蒸发“死角”,增加淀积膜的均匀性。
(3)磷硅玻璃(PSG,含磷量为6~8%重量比)或硼磷硅玻璃(BPSG,硼含量约3%,磷含量约5%)回流技术;
原理:
高温下,PSG和BPSG软化并流动,使锐利的台阶形状改变为平滑的状况,从而改善台阶覆盖状况。
工艺条件:
850℃~950℃,15~30分钟。
(4)平面化技术
1)剥离工艺
在芯片表面涂布聚酰亚胺(粘性液体,加热老化后转变为介质膜)作为绝缘介质,其厚度与金属化引线厚度近似相同;在其上涂布一层剥离层(光刻胶),然后再低温淀积SiO2并光刻出布线图形,经腐蚀后,蒸发金属化引线铝,最后去掉剥离层及其上的SiO2膜和铝膜,得到平坦的金属化布线。
2)腐蚀工艺
在整个硅片表面涂布光刻胶或聚酰亚胺,得到比较平坦的表面,选择适当的等离子刻蚀工艺,使其队光刻胶或聚酰亚胺层的腐蚀速率与下面的绝缘介质的近似相等,涂布光刻胶薄的地方,绝缘介质层被腐蚀掉的厚度比较大,从而实现绝缘层表面的平坦化。
3)化学机械抛光工艺(CMP)