DCS JX300X系统在热电厂中的应用.docx
《DCS JX300X系统在热电厂中的应用.docx》由会员分享,可在线阅读,更多相关《DCS JX300X系统在热电厂中的应用.docx(15页珍藏版)》请在冰豆网上搜索。
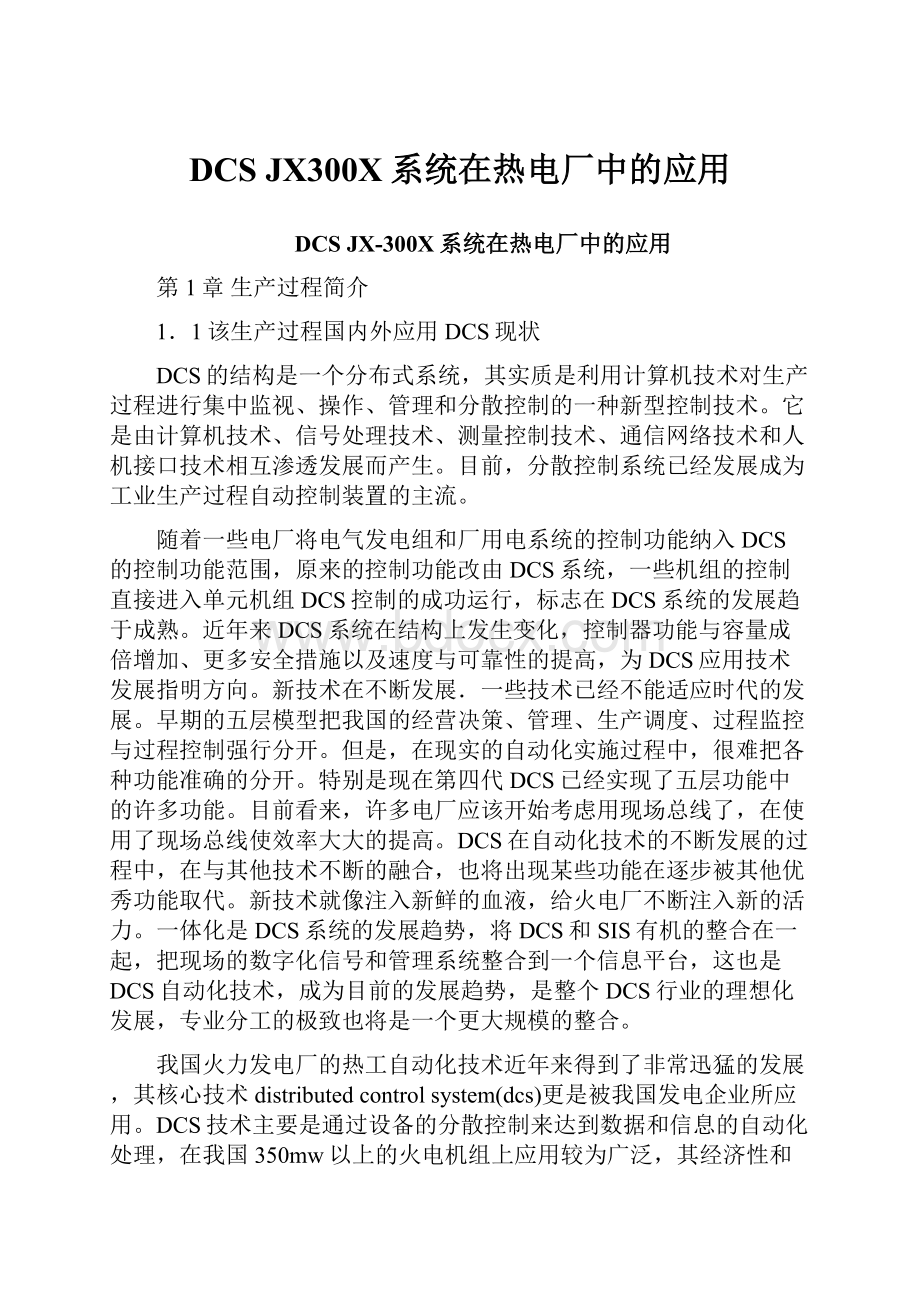
DCSJX300X系统在热电厂中的应用
DCSJX-300X系统在热电厂中的应用
第1章生产过程简介
1.1该生产过程国内外应用DCS现状
DCS的结构是一个分布式系统,其实质是利用计算机技术对生产过程进行集中监视、操作、管理和分散控制的一种新型控制技术。
它是由计算机技术、信号处理技术、测量控制技术、通信网络技术和人机接口技术相互渗透发展而产生。
目前,分散控制系统已经发展成为工业生产过程自动控制装置的主流。
随着一些电厂将电气发电组和厂用电系统的控制功能纳入DCS的控制功能范围,原来的控制功能改由DCS系统,一些机组的控制直接进入单元机组DCS控制的成功运行,标志在DCS系统的发展趋于成熟。
近年来DCS系统在结构上发生变化,控制器功能与容量成倍增加、更多安全措施以及速度与可靠性的提高,为DCS应用技术发展指明方向。
新技术在不断发展.一些技术已经不能适应时代的发展。
早期的五层模型把我国的经营决策、管理、生产调度、过程监控与过程控制强行分开。
但是,在现实的自动化实施过程中,很难把各种功能准确的分开。
特别是现在第四代DCS已经实现了五层功能中的许多功能。
目前看来,许多电厂应该开始考虑用现场总线了,在使用了现场总线使效率大大的提高。
DCS在自动化技术的不断发展的过程中,在与其他技术不断的融合,也将出现某些功能在逐步被其他优秀功能取代。
新技术就像注入新鲜的血液,给火电厂不断注入新的活力。
一体化是DCS系统的发展趋势,将DCS和SIS有机的整合在一起,把现场的数字化信号和管理系统整合到一个信息平台,这也是DCS自动化技术,成为目前的发展趋势,是整个DCS行业的理想化发展,专业分工的极致也将是一个更大规模的整合。
我国火力发电厂的热工自动化技术近年来得到了非常迅猛的发展,其核心技术distributedcontrolsystem(dcs)更是被我国发电企业所应用。
DCS技术主要是通过设备的分散控制来达到数据和信息的自动化处理,在我国350mw以上的火电机组上应用较为广泛,其经济性和安全性被我国发电企业所认同。
近年来随着计算机软件可视化效果的提高,DCS技术得到了极大的发展和应用,通讯接口的识别和管理系统数据的共享为火力发电厂的信息化处理提供了必要保障,同时DCS的分散控制也起到了非常好的效果。
1.2电厂DCS在应用中存在的问题
电厂DCS集散控制系统在应用时可能会出现的问题有很多,故障问题的出现不光是硬件问题的故障,还包括以下几个部分:
现场仪表设备故障、系统故障、软件故障、操作、使用不当造成故障等,下面就对这些故障问题进行简要的阐述:
(1)硬件故障问题。
硬件故障主要指的是过程控制层的故障,这主要是集散控制系统的模块发生故障,常见为YO模块损坏造成的故障。
这种故障的主要特点是发生故障的主要影响是
局部的,范围较小。
(2)现场仪表设备故障问题。
整个DCS系统中的现场仪表设备主要包括各种与生产有直接联系的传感器、变送器、执行器和电动门等,这类故障主要是属于现场层的故障问题。
如果DCS现场的仪表设备出现故障问题,那么这就会直接影响整个DCS的操作与控制功能。
这类故障是存在于集散控制系统中最为常见于比例最大的一类,当显示系统出现的画面参数不正
确,或者执行机构调整不了,或者电机启动不了时,这一系列故障都可以优先考虑到现场仪表设备故障问题。
这类故障产生的主要原因是由于仪表本事具有质量和使用寿命等因素,同时,还应注意仪表使用时周围生产环境是否过于复杂而造成的故障等。
(3)系统故障问题。
系统故障问题显然是关于系统运行的问题,这类故障直接回导致系统运行时出现全局性的故障发生。
但是,这类系统故障问题一般情况下是很难发生的,一旦发生此类故障,也无需慌张,主要这是一种偶然性故障,一般情况下只要重新启动系统,既可回复正常使用。
还有另一种可能就是系统在使用之出就在设计时存在问题或者程序存在问题,那么我们只能另寻解决办法了。
(4)软件故障问题。
软件故障问题主要指的是软件本身出现错误而引发的故障。
这类故障一般会在DCS集散控制系统准备投运进行调试的阶段。
产生这类故障问题的主要原因是软件应用程序本身就是非常的复杂与庞大的,需要的工作量极大,所以在应用时出现软件故障是在所难免的。
因此,我们在调试DCS系统时就要参与的热工人员和运行人员认真对待,当发现问题时积极配合好DCS系统软件调试人员及时解决问题。
这类软件故障在调试完成计入正常运行阶段一般是很少出现的。
(5)操作和使用不当引起的故障问题。
在DCS系统实际运行中,有时会出现集散控制系统某一部分的功能不正常,无法使用,检查后发现整个DCS系统都不存在问题,那么此时就应该考虑到操作人员是否存在操作不熟练或者操作错误的问题,这种现象也是经常发生的。
因此,在DCS集散控制系统的安装调试时一定要注意让供货厂家安排操作人员的培训工作,一定要严格按照操作手册进行,对于上岗人员要进行培训考核,合格后才能正式进行DCS系统的操作工作。
1.3生产工艺流程
本设计为热电厂DCS控制组态设计和实现。
主要通过数据采集系统(DAS)采集模拟量和开关量信号,模拟量控制系统(Mcs)控制水位、汽温,汽压等参数、顺序控制系统(scS)控制辅机及其设备的启停和联锁控制、汽轮机保护跳闸系统(ETS)完成汽轮机保护功能、主燃料跳闸系统(MFT)完成锅炉保护功能。
达到有效监测和控制热电厂锅炉汽轮发电机组运行的目的。
该设计使用的是浙江中控SUPCONWebFieldJX一300XDCS控制系统,首先了解和学习其基本功能和主要技术;在掌握该系统的基本原理和功能的基础上,论文然后以同集热电厂机组为控制对象,应用浙江中控系统进行了硬件选型和系统组态;论文最后以汽包水位监控为重点进行McS控制组态的实现,以给水泵监控为重点进行SCS控制组态的实现,以汽轮机保护跳闸为重点进行ETS组态的实现。
最终全面实现了浙江中控系统在同集热电厂机组上的DcS控制功能。
1.4应用DCS需求背景
随着电厂自动化水平的不断发展与提高,DCS集散控制系统已经发展进入一个相对成熟的阶段,成为了一种标准模式,不仅是应用于热力系统、发电机一变压器组、励磁等指标,同时集散控制系统还作用于发电机组,成为保护记住安全稳定运行的重要核心,对发电机组的安全可靠起到了至关重要的作用。
第二章DCS应用组成
2.1硬件组成
浙江中控SUPCONJX一300XDCS由工程师站、操作站、控制站、过程控制网络等组成。
过程控制网络实现工程师站、操作站、控制站的连接,完成信息、控制命令等传输,双重化冗余设计,使得信息传输安全、高速。
图2—1通讯网络
JX一300XDcS采用三层通信网络结构,如图2—1所示。
最上层为信息管理网,采用符合TCP/IP协议的以太网,连接了各个控制装置的网桥以及企业内各类管理计算机,用于工厂级的信息传送和管理,是实现全厂综合管理的信息通道。
中间层为过程控制网(名称为SCnetII),连接操作站、工程师站与控制站等,传输各种实时信息。
底层网络为控制站内部网络(名称为SBUS),采用主控制卡指挥式令牌网,存储转发通信协议,是控制站各卡件之间进行信息交换的通道.系统主要性能指标过程控制网络SCnetII连接系统的工程师站、操作站和控制站,完成站与站之间的数据交换。
SCnetII可以接多个SCnetII子网,形成一种组合结构。
2.1.1控制站
控制站是系统中直接与现场打交道的I/O处理单元,完成整个工业过程的实时监控功能。
通过软件设置和硬件的不同配置可构成不同功能的控制结构,如过程控制站、逻辑控制站、数据采集站。
控制站主要由机柜、机笼、供电单元和各类卡件(包括主控制卡、数据转发卡和各种信号输入/输出卡)组成,其核心是主控制卡。
主控制卡通常插在过程控制站最上部机笼内,通过系统内高速数据网络一SBUS扩充各种功能,实现现场信号的输入输出,同时完成过程控制中的数据采集、回路控制、顺序控制、以及包括优化控制等各种控制算法。
2.1.2工程师站
工程师站是为专业工程技术人员设计的,内装有相应的组态平台和系统维护工具。
通过系统组态平台生成适合于生产工艺要求的应用系统,具体功能包括:
系统生成、数据库结构定义、操作组态、流程图画面组态、报表程序编制等。
而使用系统的维护工具软件实现过程控制网络调试、故障诊断、信号调校等。
2.1.2冗余设置
控制站可冗余配置,灵活、合理。
在同一系统中,任何信号均可按冗余或不冗余连接。
对于系统中重要的公用部件,建议采用lOO%冗余,如主控制卡、数据转发卡和电源箱。
2.1.3I/O板卡及控制器
根据前期设计得到的系统信号点和控制要求,选择系统需要的硬件设备(机柜,机笼、卡件、操作站等)。
使硬件配置可以满足设计中的数据监控的要求,并为未来系统扩展升级留有一定的余量。
本工程共有I/O信号点813个,其中热电偶输入点58个,热电阻输入点54个,压力、水位,流量等4~20mA模拟量输入点186个,4~20mA模拟量输出点48个,开关量输入点326个,开关量输出点127个(如表2.1)。
工程师站一个,操作站三个。
能够满足热电厂监控的需要。
表2.1I/O点统计表
信号类型
信号点数
卡件
AI
热电偶
58
SP314
热电阻
54
SP316
4~20mA
186
SP313
AO
4~20mA
42
SP322
DI
开入
306
SP363
DO
开出
167
SP362
根据现场输入输出信号类型的不同,信号点可分为模拟量输入信号、模拟量输出信号、开关量输入信号、开关量输出信号等四种信号,文献[6]对此进行了介绍。
本设计涉及到的模拟量输入卡有:
1.SP313卡(四路电流信号输入卡),测量配电和不配电标准电流信号,如差压变送器输出信号(测量流量、水位、氧量、风量、位移量、调节阀门位置等)、压力变送器输出信号(测量压力信号)、电流变送器输出信号(测量电流信号)。
配电系指卡件对外供给24V电源。
2.SP314卡(四路电压信号输入卡),测量II型III型标准电压信号、毫伏信号、以及各种型号的热电偶信号,如K型热电偶、E型热电偶等。
3.SP316卡(两路热电阻信号输入卡),专用于测量热电阻信号,每一路可以分别接收Ptl00、
Cu50两种热电阻信号。
4.SP322卡(四路模拟量输出卡件),用于控制调节阀门的开度。
5.SP363卡(7/8路数字量信号输入卡),用于响应各种保护干簧触点和开关状态干簧触点的输入。
6.SP362卡(7/8路无源晶体管开关触点输出卡),主要用于报警信号控制和开关断合控制。
控制器采用PID控制器。
2.2软件组态
组态(Configuration)是用分散控制系统提供的功能模块或算法组成所需的系统结构,完成所需功能。
分散控制系统的组态包括系统组态、画面组态和控制组态。
系统组态完成系统的各设备间的连接。
画面组态完成操作站的各种画面、画面间连接。
控制组态完成各控制器、过程控制装置的控制结构连接、参数设置等。
趋势显示、历史数据压缩、数据报表打印及画面拷贝等组态常作为画面组态或控制组态的一部分来完成。
也可以分开进行,单独组态。
该设计采用的是SUPCONDCS系统的SCKey组态软件。
2.2.1组态流程
SUPCONDCS的组态工作通过组态软件SCKey来完成。
该软件用户界面友好,操作方便,充分支持各种控制方案。
SCKey组态软件将帮助工程师有序且系统地完成“系统组态”这一复杂的工作。
整个组态设计流程如下图2-2所示:
图2—2组态设计流程图
2.2.2监控软件
一.软件特点
实时监控软件(文件名为AdvanTr01)是基于Windows2000/NT4.0中文版开发的SUPCON系列控制系统的上位机监控软件,采用多任务、多线程以及实时数据库,用户界面友好,所有的命令都化为形象直观的功麓图标,只须用鼠标单击即可轻而易举地完成操作,再加上SP032操作员键盘的配合使用,生产过程实时监控操作更是得心应手,方便简洁。
二.技术参数
1.图形分辨率1024×768,16位真彩色
2.数据更新周期1秒,动态参数刷新周期1秒
3.按键响应时间<=0.2秒
4.流程图完整显示时间<=2秒,其余画面<=1秒
5.命令响应时间<=0.5秒
6.提供实时和历史数据读取、控制站参数修改的API,以便向用户开放
图2-3监控界面——主界面
2.2.3存档报表
SCForm报表制作软件是针对SUPEON集散控制系统所开发的全中文界面的制表工具软件,是SUPcON集散控制系统组态软件包的重要组成部分之一,具有全中文化、视窗化的图形用户操作界面。
该软件功能强人、编辑方便,为用户实现自动报表提供了一条快捷、灵活的途径。
它用来记录重要的系统数据和现场数据。
以供工程技术人员进行系统状态检查或工艺分析。
软件的功能特点:
自动报表系统分为组态(即报表制作)和实时运行两部分。
其中,报表制作部分在SCForm报表制作软件中实现,实时运行部分与AdvanTrol监控软什集成在一起。
SCForm软件从功能上分为制表和报表数据组态部分。
报表制作功能的设计采用了与商用电子表格软件EXCEL类似的组织形式和功能分割。
该软件具有与EXCEL类似的表格界面,并提供了诸如单元格添加、删除、合并、拆分以及单元格编辑、自动填充等较为齐全的表格编辑器操作功能(功能定义均与EXCEL类似),使用户能够方便、快捷地制作出各种类型格式的表格。
另外.SCForm报表制作软件与EXCEL报表数据可以相互引用。
用EXCEL软件编辑过的报表文件可以通过剪切、复制,粘贴的方式在SCForm报表制作软件的编辑环境中进行再次编辑;而用SCForm报表制作软件编辑过的报表文件可以通过剪切、复制、粘贴的方式将报表内容在EXCEL软件的编辑环境中进行再次编辑。
当然,在这两种情况下,粘贴后的文件必须要做一些修改,才能得到原先编辑环境下的实际效果。
在报表数据组态功能的设计中,最主要的是事件的概念。
所谓事件。
实际就是一个进行条件判断的表达式。
用户可根据需要,将事件表达式定义成报表数据记录和报表输出的相关条件.依次来实现报表的条件记录与条件输出。
这样的形式极大增强了SCForm软件的灵活性和易用性,可很好地满足用户对工业报表的各种要求,实现现代化工业生产中的各类工业实时报表。
SCForm软件采用窗口式交互界面,所见即所得的数据显示方式,同时,它还提供了全中文的详细在线帮助,使用户在遇到疑难问题时,只要按下Fl键就能够迅速获取相关的帮助信息,进而有效地解决问题。
2.3主要控制模式
汽包水位反映了锅炉蒸汽流量与给水流量之间的平衡关系,保持汽包的正常水位是汽包锅炉和汽轮机安全运行的重要条件之一。
汽包水位过高,蒸汽空间将缩小.会引起蒸汽带水,使蒸汽品质恶化,还将导致在过热器管内产生盐垢沉积,使管子过热,金属强度降低而发生爆管。
严重满水时,将使蒸汽大量带水,引起管道与汽轮机内严重的水冲击,造成设备损坏。
水位过低,将破坏正常的水循环,造成水冷壁管超温过热。
当严重缺水时.还可能造成水冷壁管的爆破。
因此,汽包给水调节的任务是维持汽包水位在允许的范围,使锅炉的给水量适应于锅炉的蒸发量。
2.3.1三冲量前馈一串级汽包水位控制原理
汽包水位存在着虚假水位现象,在负荷扰动时,单一的PID调节很难克服虚假水位.一般来说,汽包水位的控制原则上采用三冲量串级前溃控制。
汽包水位是主(被控)参数,即主冲量;给水流量作为副(被控)参数,蒸汽流量是前馈补偿的主要扰动,给水流量与蒸汽流量作为辅助冲量。
形成一个以主蒸汽流量为前馈,根据汽包水位和给水流量的变化来确定给水量,再根据给水量确定调节阀门的开度,以达到控制汽包水位的目的。
图2-4汽包水位前馈一串级回路控制系统框图
2.3.2三冲量汽包水位调节控制方案
根据上述前馈—控制回路控制的系统框图(图2-4),DBF功能图软件的控制特点和同集热电DCS输入输出点的情况,形成下述汽包水位调节控制方案(图2-5)
图2-5前馈一串级控制回路控制的系统框图
2.3.3三冲量汽包水位调节图形化编程
通过该方案我们可以用DFB软件功能块中的BSCX单回路扩展模块为主进行编程。
图形化编程(图2-6)所示:
图2-6三冲量汽包水位调节图形化编程
第三章DCS配置及实施
3.1硬件选型
根据现场条件、系统规模以及投资需要,我们准备配备两个控制站(一个控制#l锅炉和公用系统,另一个控制#2锅炉和汽轮机)。
由此,该工程设备配置表(表3.1)形成如下:
表3.1设备配备表
软件配置
序号
名称
型号
数量
备注
1
AdvanTrol软件
1
2
DCS操作员站软件狗
3
3
DCS工程师站软件狗
1
4
操作系统
WIN2000
1
硬件配置
序号
名称
型号
数量
备注
1
机柜
SP202
4
2
I/O机笼
SP211
13
3
数据转发卡
SP233
26
4
主控制卡
SP243X
4
5
电源箱机笼
SP251
4
6
电源
SP251—1
13
7
电源指示卡
SP221
20
8
电流信号输入卡
SP313
51
9
电压信号输入卡
SP314
19
10
热电阻信号输入卡
SP316
35
11
模拟量信号输出卡
SP322
12
12
触点型开关输入卡
SP363
53
13
晶体管触点型开关量输出卡
SP362
30
14
空卡
SP000
16
5
工程师站
1
16
操作员站
3
17
集线器
SP071
2
18
Scnet网卡
SP023
8
根据硬件配置图和现场条件,我们形成如下图(图3-1)示DCS系统配置图
图3-1DCS系统配置图
3.2编译、下载和传送
通过上述汽包水位的图形化编程,大体介绍了本热电厂DCS控制组态设计的核心内容,其余设备和参数的模拟量控制、顺序控制和保护联锁功能同样可以通过图形化软件的编程来实现。
到这里我们所进行的控制组态工作基本上完成了,保存文件,对所进行的组态进行编译,我们所定义的组态文件必须经过系统编译,才能下载给控制站执行,或传送到操作站操作,组态编译包括对系统组态信息、流程图及报表等一系列组态信息文件的编译。
如果有错误,则双击编译中产生的错误信息,将弹出对应出错的信息窗口,在窗口中进行修改。
如果没有错误则进行组态下载,组态下载用于将上位机上的组态内容编译后下载到控制站。
在修改与控制站有关的组态信息(主控制卡配置、I/O卡件设置、信号点组态、常规控制方案组态、自定义控制组态等)后,需要重新下载组态信息;如果修改操作主机的组态(控制分组画面、状态分组画面)信息则不需要下载组态信息.当组态下载成功时,信息显示区本站信息与控制站信息相同。
最后我们进行组态传送,选择需传送的操作小组名称。
组态传送用于将编译后的.SCO操作信息文件、.IDX编译索引文件、.SCC控制信息文件等通过网络传送给操作站。
如果都没有错误,这个系统基本就可以运行了。
可以和操作组态一起完成对热电厂设备和运行参数的监视和控制。